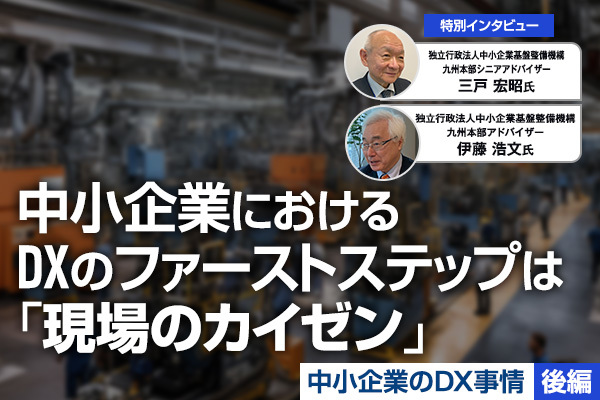
国際競争の激化や少子高齢化に伴う人材不足、日進月歩のデジタル技術の進歩により、製造業における業務効率化の必要性はこれまで以上に高まっています。
特に中小規模の製造業では、この問題が顕著です。大手とは異なり、人材確保の難易度は高く、1人あたりの生産性向上やこれまでの業務プロセスの改善が求められます。
独立行政法人中小企業基盤整備機構 九州本部の中小企業アドバイザーとして中小企業支援を行っている専門家のお二人に、中小企業におけるDXの現在地点を伺う本シリーズ。後編では、大企業との関わり方や、DXプロジェクトを推進するためのプロセスについての考えをお聞きします。
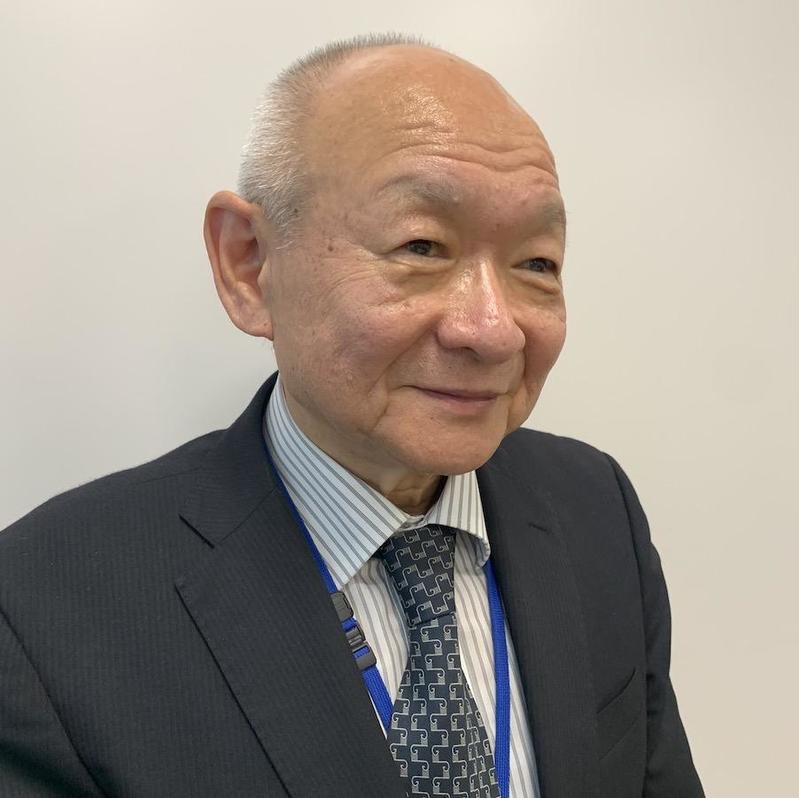

デバイスの商品開発、生産技術、製造を担当。2020年より中小機構九州本部の中小企業アドバイザーとして、生産性、品質、原価改善をベースにおいた中小企業支援に従事。
ーー前編では人材面における中小企業の課題を伺いましたが、事業面ではどのような課題がありますか。
三戸:自動化しやすい領域は大企業を中心にどんどん進んでいく一方、生産工程で人の判断を要する自動化の難易度が高い領域については、大企業は積極的には取り組みません。
その大企業が自動化に手をつけていない領域が、中小企業の負担の増加につながっていることは間違いないと思います。
伊藤:特に工数が多いわりに業績への大きな影響も見出しづらい多品種少量生産への対応で苦しんでいることが多いですね。
生産プロセスが複雑な多品種少量生産の領域は、システムで効率化させづらいため、人手をかけてコツコツと対応していく必要があります。
中小企業は発注者側に対してきちんと意見が言えるように強くなる必要があると感じます。
ーー発注者と受注者という関係上、受注者側が強く意見をするハードルは高いと思います。この課題を乗り越えるためには、どのようなアプローチが必要なのでしょうか。
伊藤:気合で話を進めないということです(笑)。製造物の価格の裏付けが、技術的にも品質的にも論理的に発注者に説明できることが重要です。
「このような理由でこの金額、品質になるんですよ」と論理的に説明するためには、自社の生産工程をデータドリブンでしっかり分析できる必要があります。
従来、紙で保管していた生産データをサーバに置いておくだけで、あっという間に平均数値や工程能力を出力できます。
データを活かすものづくりは、このような理論武装の観点でも重要な意味を持ちます。大企業との差を埋めやすい部分でもあるので、積極的に対応を進め、発注者と対等にコミュニケーションが取れるようになって欲しいと考えています。
ーー中小企業がDXプロジェクトを推進する際に障害となりやすいポイントはありますか。
伊藤:ものづくりに忙しく、新しい施策を考える時間がないという声はよくお聞きします。
そのような場合、背景にある従来の“業務の無駄”に気づいていないケースが多いです。
まずは足元の業務の無駄をなくし、新しいことにチャレンジする余白を生み出すための地道な改善から始める必要があります。
一方で、3年後はこのような技術を取り入れてデータドリブンなものづくりに持っていきましょうというビジョンも我々はあわせて提案します。
目先の改善をすすめながら、技術を取り込んでいく新しい考え方を持てるようになることが理想です。
三戸:システム導入を効率的に進めるという観点でも、従来の業務の無駄を改善させる意義は大きいです。
業務効率が悪い状態で大きいシステムを入れてしまうと、効率の悪い工程がそのままシステム化されてしまいます。結果として使いづらいうえに個別管理を必要とするシステムとなり、システム修正にも大きなコストがかかってしまいます。
既存の業務プロセスをきちんと改善したうえで、DXに至るプロセスを進めるようアドバイスしています。
ーー大企業であっても、DXの運用フェーズでうまくいかないという話もよく聞きます。地道な既存業務の改善に取り組みつつ、徐々にDXの知識を浸透させるアプローチが重要なのですね。
三戸:前職で、MES(製造実行システム)の導入プロジェクトを推進した際に、 現場との多大なコミュニケーションが発生し、導入に至るまで1年近くかかりました。
MESの導入後、集めたデータをもとに業務の標準化に取り組んだのですが、標準化するためには、作業者の技術水準にかかわらず、標準化した治具や工具を使用してもらう必要があります。
特級技能を持っている熟練者の方からすると「なぜ自分が他の人物と同じ工具を使って同じ作業をしないといけないんだ。」と反発され、標準化の実現にさらに数年を要しました。
このように熟練者の理解を醸成しつつ、業務の標準化を行っていくプロセスを、大企業は多かれ少なかれ繰り返しており、同様のプロセスが、今の中小企業にも求められると思います。
中小企業のDXが進み、サプライチェーンの一部の企業だけが損してしまう世界にならないようになるといいと思います。
中小企業はコストの問題から専門企業やコンサルタントに依頼するハードルが高い現状もあると思います。
弊機構では、現状の工場視察後、課題をヒアリングして改善方針を提案する「生産工程スマート化診断」という無料のサービスも提供しています。お悩みの企業はぜひお申し込み頂きたいです。
ーーDX推進でも格差が進んでおり、この遅れが中小企業にとって死活問題になり得ますね。中小企業のリアルな課題感と進むべき道筋がよく理解できるお話でした。今回はありがとうございました。
(提供:Koto Online)