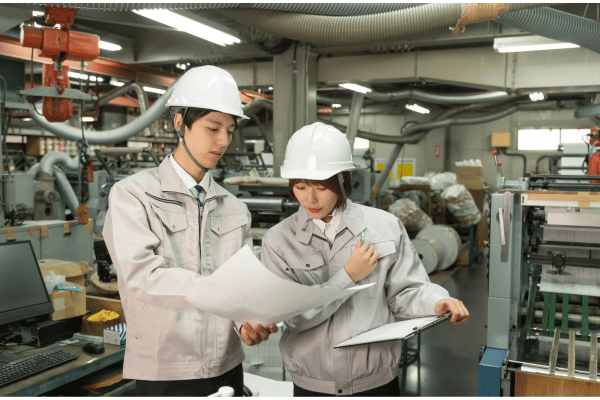
製造業における業務の改善ネタや事例を知ることは、職場環境を良くするためにも、優れた人材と認められるためにも役立ちます。ネタ出しに使えるフレームワークや用語、成功事例における共通点も意識することで、地に足の着いた改革を生み出せるでしょう。
目次
製造業の小さな改善ネタ・アイデア事例15選
数ある業界の中でも特に日々の改善が重要となるのが製造業です。製造業者は、以下の3点の理由から日進月歩で業務を効率化していくことが求められています。
- 競合他社に負けない生産スピード&クオリティの確保
→改善を進める他社との競争力を保つためには自社も改善をしていくことが必須 - 深刻化する人手不足への対策
→作業効率の上昇によりスタッフ一人あたりの生産力を無理なく上昇できる - SDGsやCSRなどの社会ニーズへの対応
→労災を防ぐ安全面の確保など、商品の質だけでなく労働環境まで注目される時代
しかし、改善提案を繰り返す中でネタやアイデアが枯渇してしまうこともあるでしょう。そこで、すぐにでも現場で実践できる製造業の小さな改善ネタ・アイデア15選をご紹介します。
工具・資材の置き場所を明確にする
業務効率を大きく左右するのが、工具・資材置き場の明確化です。「あの工具はどこにあるか」と毎回探すことから作業を始めていては非効率です。レンチはここ、梱包(こんぽう)資材はここ、代車はここなどと、使い終わった道具の置き場所をスタッフ間で取り決めましょう。
ボックスの中身を一目で確認できるようにする
ボックスに何かを収納する際、外から中身が確認できる工夫も大切です。例えば、収納されているアイテムの写真を外側に貼ると、何度も開け閉めする手間から解放されます。また、ボルトのような使用頻度も見間違いも多いアイテムは、サイズ・規格ごとに入れる場所を分けた上でラベリングをしましょう。
充電状態を一目で確認できるようにする
各種工具のバッテリーについては、充電状態により収納場所を分けることも重要です。充電済みと未充電のバッテリーを同じ場所に置くと、交換して試してまた交換して、と時間がかかってしまいます。充電済みは青いカゴ、充電されていないものは赤いカゴなどと色分けをするのもおすすめです。
多機能な治具(ジグ)や工具を使用する
一つの作業過程でいくつもの治具や工具を持ち替えている場合、マルチに対応しやすい多機能なものと交換することで作業の負担が減少します。また、使用感を損なわない範囲で軽量なグッズを選ぶと体への負担が和らぎます。
作業台や作業スペースの配置を見直す
作業中にいつも体が痛くなるような場合は、作業台や作業スペースに問題がないか再確認することも大切です。例えば、両腕を常に肩よりも高く上げなければいけない、無理な前傾姿勢になってしまう、などといった場合は、作業スペースの設置場所を見直すだけで負担を激減できる可能性があります。
照明の高さと明るさを再検討する
見落としがちなポイントとして、照明の高さや明るさの確認が挙げられます。手元に十分な光が届かない状況では、作業スピードが落ちる上にミスも生まれやすくなります。作業台の真上に小型のLEDライトを設置するなどの工夫を施しましょう。
空調設備の温度設定を見直す
空調設備の温度設定も再検討したいポイントです。取り扱う商品にもよるものの、過度に冷房が効いている、あるいは効いていない状況では作業の能率も落ちます。また、ドアを開けっ放しにしないなど、少しの意識改革を行うだけでも大きな改善となります。
ゴミ箱や不要資材入れを大型のものに変える
作業中、ゴミ箱を空にするために何度も移動していませんか? ゴミ箱や不要資材入れを大型のものに変えるだけで、このような非効率を防げる場合があります。ラベリングにより何のゴミ箱なのか瞬間的に把握しやすくすることも重要です。
安全カバーや防護柵を活用する
機材の内部がむき出しになっている部分に安全カバーを付ける、階段や2階スペースに転落防止用の防護柵を付けるなど、安全のための提案も重要な改善につながります。日々の業務の中で危ないと感じたら、その瞬間から改善のアイデアを生み出すことができます。
衛生環境を保つための清掃ルールを設ける
製造業の現場で作業効率を上げるためには、衛生環境も大切です。ゴミが散らばっていたり濡れていたりする場所では、作業のミスも重大インシデントも起こりやすくなってしまいます。休憩前に周囲を3分掃除するなど、全員が参加しやすい清掃ルールを検討してみましょう。
手順書(マニュアル書)を作成する
業務に関する手順書(マニュアル書)の作成により、誰でも同じように作業できるようにすることも重要です。新人や短期雇用のアルバイトなど、ベテラン以外でも一定の業務を行えるようになれば、安定した生産ペースを確保できます。
日報や点検報告書をデジタル化する
日報や点検報告書が紙の場合、デジタル化を進めることで業務効率を改善できます。一度紙で作り、後からまとめてエクセルやワードに入力するようでは非効率です。デジタル化には必ずしも高額な費用が求められるわけではありません。タブレットのメモアプリやクラウドファイル共有サービスを使うなどの方法もあります。
連絡事項を誰でもいつでも確認できるようにする
直近の不具合報告や臨時の作業変更、治具や工具の新規導入など、連絡事項を朝礼時に口頭で伝えている現場も多いと思います。重要事項は誰でもいつでも確認できるよう、文章に残しましょう。タブレットなどのデジタル共有が便利ですが、専用のノートを設置するだけでもすぐに解消できます。
カメラ映像により設備を遠隔監視する
一人が複数の機材やラインを担当する場合、稼働状況を確かめるために何度も持ち場を離れるケースが目立ちます。このような場合は、ホームセンターなどで数千円~数万円程度のカメラとモニターを購入し、離れた場所から様子を確認できるようにするだけで作業を効率化できます。
●仕入れ先とのやり取りをデジタル化する
見積書、注文書、納品書、請求書など、製造業では仕入れ先との間でさまざまな文書が交わされます。手書き書類の手渡しやFAXでのやり取りもまだまだ多いですが、パソコンでの作業に切り替えることで業務のスピード感を向上させられます。月末の経理作業の負担も減り、やり取りをいつでも再確認できるなど、副次的なメリットも生まれるでしょう。
大きな改善まで成功した製造業の企業事例5選
製造業の業務改善は小さな一工夫からでも行えます。しかし、中にはデジタル・ITツールの活用により劇的な改善に成功した企業もあります。その事例をご紹介しましょう。
発注業務の電子化で月400時間の工数を削減:株式会社フジワラテクノアート
株式会社フジワラテクノアートは、日本酒やみそなどの醸造食品を作るための製造機械と大型醸造プラントを提供する企業です。同分野で国内シェア80%以上を誇っています。
同社では、発注業務の電子化により効率改善を行いました。従来の発注作業では、設計部門が図面を作り、その図面を元に発注書を作成し、1社ずつ印刷してFAXで送るという手順を取っていましたが、ITシステムの導入により一連の作業をパソコン上で完結できるようになり、1ヵ月当たり400時間もの工数の削減に成功しています。
また、生産計画もパソコン上で管理できるようになり、スケジュール管理に割く時間も月に120時間削減されています。合計で月520時間と圧倒的な時短に成功した同社は、日本DX大賞2022の「中小規模法人部門」で大賞に輝きました。
IT導入補助金で新たな販路を獲得:有限会社千葉恵製菓
2020年度のIT導入補助金を活用し、自社の専用ECサイトを構築した有限会社千葉恵製菓。岩手県で和菓子と洋菓子を製造する同社では、スーパーやコンビニ、お土産店での販売が売り上げの大部分を占めていました。しかし、コロナ禍により観光需要が冷え込む中で窮地に追い込まれます。
そこで、ターゲットに応じた複数のECサイトを構築し、東北以外の地方への販売に挑戦しました。結果、中部地方や四国地方などこれまでは手の届かなかった場所からも注文が入るようになったそうです。運営に関わる社員のモチベーション向上につながるなど、副次的な効果も生まれています。
RPAによる業務の自動化・無人化を達成:理化工業株式会社
理化工業株式会社もIT導入補助金を活用した企業の一つで、こちらは人件費の削減に成功しました。金属製品の熱処理や塗装加工を手がける同社では、現場での情報の記録(材料調整の履歴や加工数量、作業時間など)を紙で行い、パソコンに入力し直す二度手間が課題となっていました。
そこで、iPadを活用した電子入力システムを採用し、現場担当者が直接デジタル入力できるように工程を整えました。あわせてRPAツールを導入し、夜間に自動稼働させることで、事務作業に必要な人手を削減しています。現在は製品の不良率の検出にもITツールを活用しようとするなど、改善の取り組みは進んでいます。
地理的制限を超えた近未来の製造現場:株式会社ダイセル
株式会社ダイセルは1919年創業。100年以上の歴史を誇る製造業者です。メディカル・ヘルスケア製品の提供から自動車用のエンジニアリングプラスチックの製造まで、幅広く手がけています。
同社の特徴は、遠隔地にある二つの工場(兵庫県の網干工場と広島県の大竹工場)を隣接施設のように一体化して稼働させている点です。ガス・石炭を主な燃料とする網干工場と石炭・タイヤチップを用いる大竹工場では、同一製品の製造に関しても必要とされるエネルギーコストが異なります。そこで、オンラインで両工場の生産計画や運転状況を一括監視し、その時々に応じて最適な稼働指示を出すことで生産コストを最小限に抑制。全体のエネルギー効率向上という大きな改善に成功しています。
24時間365日停まらない工場:株式会社土屋合成
24時間365日稼働し続けるスマートファクトリーを実現したのが、株式会社土屋合成です。文具や雑貨から家電の製造までを手がける同社では、自社開発のITシステムの活用により、昨今の人手不足の流れの中でも安定した製造を続けています。
同工場では、倉庫への材料の入出庫は場所・残量ともに自動管理され、製品の取り出しや加工といった繰り返し作業はロボットが担います。生産状況はすべてオンラインで把握でき、工場外からリアルタイムで確認することも可能です。このような取り組みは、長時間労働や休日・深夜労働をなくすなど、社員の働き方の改善にも役立っています。
事例から見る製造業改善のポイント
では、製造業の改善ではどのようなポイントが成否を分けるのでしょうか。大きく以下の4つのポイントを意識することが大切です。
「不便・不満の声」から問題を洗い出す
まず意識すべきは、不便・不満の声から改善点を洗い出すことです。「紙で用意してパソコンに入力し直す二度手間が発生している」「いつか誰かがケガをしてしまいそうな作業工程がある」など、業務中に感じる問題が改善案を生み出すキッカケとなります。作業工程をフローチャートなどの図で表し、問題はないか順番に検討してみることもおすすめです。
ITツールで大規模な変革を生み出す
企業事例でご紹介した通り、ITツールは大規模な変革を生み出します。受発注業務のデジタル化、単純作業の自動化、AIを使ったリアルタイム品質チェックなど、適切なシステムの導入によって業務効率を飛躍的に高めることが可能です。
ITツールにより業務効率を改善し、ビジネスモデルまで変革していく取り組みは、近年必要性が叫ばれている「DX(デジタル・トランスフォーメーション)」そのものです。取り組みを進めれば、先進的な企業であるとして社員からも喜ばれやすくなるでしょう。
補助金や助成金も有効に活用する
ITツールの導入を視野に入れている場合は、補助金や助成金の活用も検討しましょう。国は民間企業のDX化を推進しており、必要なシステムや設備の導入に際して金銭的支援を行っています。以下は製造業者の業務改善で利用しやすい補助金・助成金の一例です。
- IT導入補助金(サービス等生産性向上IT導入支援事業)
→ソフトウエアの購入、セキュリティーサービスの利用、パソコンの導入などを幅広く支援。補助率は1/2以内~3/4以内が基本。 - ものづくり補助金
→主に中小企業・小規模事業者向けの支援。試作品開発や生産プロセスの改善、生産性向上を目的とする設備投資などが支援対象。補助率は申請枠ごとに2/3など。数千万円の支援を受けられることも。 - 令和5年度「中小企業地域経済政策推進事業費補助金(地域DX促進環境整備事業)」
→地域特性とデジタル技術の掛け合わせで新ビジネスを生み出す際に利用可能(※詳細は調整中。2023年3月時点で執行団体の公募が終了済み)
このような支援策の利用により、金銭的に負担の少ない形で改善を進めていけます。
小さな改善も積み重ねていく
最後にあらためて意識しておきたいのが、小さな改善の重要性です。製造業の改善の取り組みでは、必ずしも高額な費用や多大な労力はかかりません。前述の「工具や材料の保管箱に中身が一目でわかる画像を貼り付ける」といったアクションも立派な改善の一つです。
ITツールを用いる大規模な改善とすぐにでも挑戦できる小さな改善、2つの視点から取り組みを進めることで、働きやすく生産効率の良い現場を実現できます。
製造業改善に役立つフレームワーク・用語
最後に、これから製造業改善のアイデアを出す際に役立つフレームワークや用語を見ていきましょう。
5S活動
5S活動とは「整理(Seiri)」「整頓(Seiton)」「清掃(Seisou)」「清潔(Seiketsu)」「しつけ(Shitsuke)」の5つの活動を指す言葉です。経済産業省によれば、以下の通り定義されています。
- 整理(Seiri):不要な機械や資材を廃棄するなど、必要と不要を区別すること
- 整頓(Seiton):工具や材料、書類などの置き場所を明確にすること
- 清掃(Seisou):ゴミや汚れを取り除きつつ、道具や設備の異常を点検すること
- 清潔(Seiketsu):整理・整頓・清掃によるきれいな状態を維持すること
- しつけ(Shitsuke):ここまでの四つのSを社員に浸透させ、習慣化すること
(出典:経済産業省中小企業庁「ミラサポplus 中小企業向け補助金・総合支援サイト」を参考に作成 https://mirasapo-plus.go.jp/hint/19763/ )
製造業では頻繁に耳にする用語ですが、それゆえに形骸化してしまっていることもあります。あらためて5S活動を徹底するだけでも、多くの改善点が見つかるはずです。
QCD
QCDとは、製品・サービスにおける「品質(Quality)」「価格(Cost)」「納期(Delivery)」の3要素を表すフレームワークです。近年では、「Safety(安全)」「Environment(環境)」などを足して「QCDS」や「QCDE」などと呼ばれることもあります。
製品やサービスが消費者に受け入れられるためには、品質が優れている必要があります。しかし一方で、価格や納期に無理があれば継続的な提供は困難です。また最近では、CSRやESG、SDGsの観点から、製造現場の安全や環境負荷への配慮も重要視されています。
十分な品質の確保を前提としつつ、「コストで削減できる部分はないか」「納期短縮(生産効率の上昇)の余地はないか」と順番に要素を検討していくことで改善案を生み出せます。
ヒヤリハット
ヒヤリハットとは、「勤務中に危険なこと(ヒヤリとしたりハッとしたりすること)があったが、事故やケガにまでは至らなかった出来事」を指します。製造業ではメジャーな言葉ですが、このヒヤリハット体験も現場の安全面の改善に向けたヒントとなります。
1件の重大な事故が起こるまでには、29件の軽少な事故と300件のヒヤリハットがあるとされています。これは「ハインリッヒの法則(1:29:300の法則)」と呼ばれる有名な経験則です。ヒヤリハットの段階で改善を進めることで、深刻な労災を予防できます。
4M(6M)
4Mとは「人(Man)」「機械(Machine)」「材料(Material)」「方法(Method)」の4要素を指す用語です。主に品質管理に使われる言葉で、「計測(Measurement)」「管理(Management)」を加えて6Mと呼ばれることもあります。
- 人(Man):作業を担当する人(例:担当者のスキル・勤務状況・モチベーションなど)
- 機械(Machine):治具や工具までを含めた現場で使われている機械
- 材料(Material):製品に使われる材料(例:仕入れ先の状況や仕入れ価格、個数など)
- 方法(Method):製造の作業工程(例:生産形態、作業手順のマニュアル化など)
- 計測(Measurement):製造された製品の品質測定
- 管理(Management):生産工程全般の管理(例:製造計画のマネジメント、リソースの分配など)
5SやQCDと同様、4M(6M)の各要素を順番に確認していくことで、改善の余地を見出せます。いきなり製造過程全体を見るのではなく、一つひとつの事項を確認していくことが、製造業改善のカギです。
事例を参考に小さなことから製造業の現場改善を
この記事では、製造業の改善について、小さなアイデア・ネタの事例と大規模な改善に成功した企業事例、事例から見る改善のポイント、活用したい用語・フレームワークなどをご紹介しました。
製造業者にとって日々の改善は必須の取り組みです。競合他社に勝る競争力を確保し、CSRなどの社会ニーズを満たすことにもつながります。ご紹介したフレームワークや事例を参考に、採り入れやすいものから改善を進めてみてください。