工場の生産性向上は、製造業の合言葉のようになっています。しかし、どうやったら生産性が向上するのか、はっきりわからないという企業が多いのも実情です。生産性とは何かを見直して、その方法について探っていきましょう。ここでは、工場の生産性向上に成功した事例を集めました。
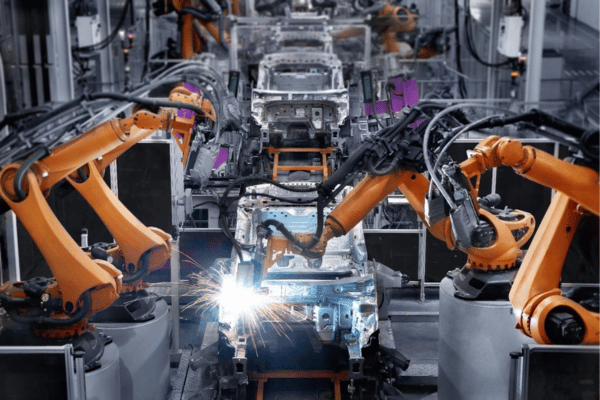
そもそも工場における「生産性」とは
恒常的な課題である「工場における生産性の向上」とは、どんなことを示しているのでしょうか。生産性とは、次のような公式であらわすことができます。
生産性=産出量÷資源投入量
産出量は生産数量、資源投入量は材料、労働、諸費用の投入量になります。すなわち、できるだけ少ない資源でたくさんの生産量を上げることが「生産性の向上」ということになります。
この式では、決まった資源投入量のなかで産出量を増加させれば、生産性は上がることになります。資源投入量を抑えながらたくさん生産すれば、生産性が上がっていく関係になることがよくあります。大量に生産することが生産性を上げる方法の1つになる関係です。
ここで気を付けなくてはならないのは、限りなく産出量を上げれば、限りなく生産性が上がるのではないということです。生産したものは実際に市場で売れなければ在庫となります。仕掛品も増えれば管理の手間が増えます。すなわち、在庫が増えていくことは在庫管理のための労働力や経費が増えていくことを意味します。必要ではない資源投入が発生し、結果的に生産性は落ちていくのです。
よって、生産性には最適な水準というものがあり、産出量・出来高だけでは判断できません。資源投入から生産数、市場における需要、在庫維持にかかる時間やコストなど幅広い観点から見極めて、判断する必要があるのです。
工場の生産性向上が求められる背景
日本における工場の生産性向上が求められる背景には、主に2つのポイントがあります。労働力不足の時代が来ることと海外に比べて生産性が低いことの2つです。1つずつ見ていきましょう。
労働力不足の時代が来ること
下のグラフで、オレンジ色の部分に注目してください。日本の労働力人口(15歳~64歳)は2010年頃がピークで、それ以降は増えません。
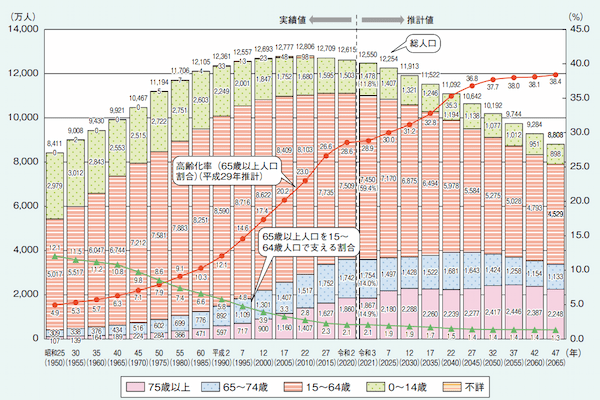
https://www8.cao.go.jp/kourei/whitepaper/w-2022/zenbun/pdf/1s1s_01.pdf
今後約40年間で、人口の中で65歳以上の高齢者の占める割合だけが大きくなり、実際に働く年齢層の人(15歳~64歳)は減り続けていくことが予想されています。下のグラフの通り、子供が生まれる数が減り続けてきたので、人口増加の実績は低く、人口構成に関してはこれから将来を変えることはできません。
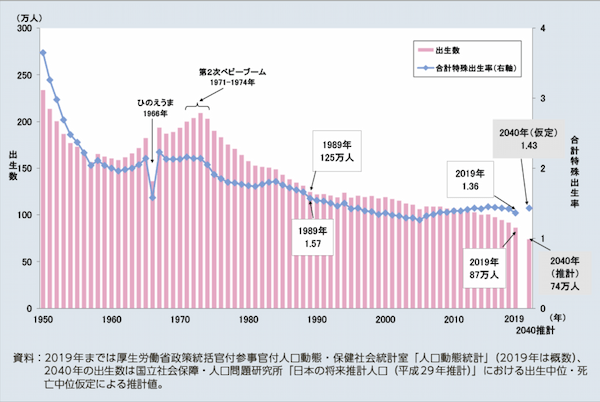
https://www.mhlw.go.jp/stf/wp/hakusyo/kousei/19/backdata/01-01-01-07.html
こうした事実をみると、工場の生産を維持するのに必要な労働力を維持するのは困難になっていくことがわかります。この事実は、製造業においては限られた人員で生産量を落とさないようにすることが求められていることを意味します。すなわち生産性向上は社会的な課題となっているのです。
海外に比べて生産性が低いこと
日本の生産性は諸外国と比べて低いということが問題になっています。
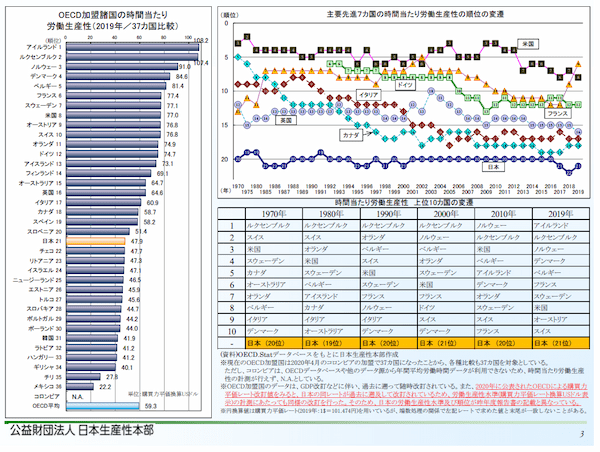
https://www.jpc-net.jp/research/assets/pdf/press_2020_new.pdf
このグラフはOECD(経済協力開発機構)36か国の時間当たり労働生産性を表示しています。日本は36か国中21位です。G7(主要7か国)では、フランス、米国、ドイツ、英国、イタリア、カナダ、日本の順になっているのが分かります。主要7か国中、生産性が最下位なのです。
これはあくまでもOECD加盟国中の順位であって、加盟していない国との比較は分かりません。めざましい経済発展を遂げている新興国もある中、このままでは日本の存在感が薄くなっていく一方です。
国際間の競争力低下は、日本の抱える大きな課題です。このことからも生産性向上が必要になっています。
日本の生産性が低い理由とは何か
日本の生産性が低い原因とは何なのでしょうか。いろいろな原因が唱えられていますが、かなり根の深い問題のようです。ここでは一般によく言われているうちからいくつかを取り上げます。
労働時間の長さ
前段で掲出したOECD諸国の中の順位は「時間当たりの労働生産性」を比較しての順位となっています。すなわち、同じ量を生産していたとしても、労働時間が長い国は生産性が低くなってきます。日本の労働者は有給休暇をあまり取得しなかったり、残業時間が多かったりすることが、以前から問題になっていました。風潮として長時間働く人が、高く評価される傾向があったことは否めません。
また賃金制度自体、基本給が安く設定され、残業代で稼ぐことが常態となっている職場も多く見受けられ、一人当たりの労働時間を長いものにしています。この傾向があると、統計として見た場合に、一人当たりの労働生産性が低くなる計算となります。
この点に関して、厚生労働省でも残業時間の上限の設定や有給休暇の取得義務日数などを設定した、労働法の改正を行い、全国の労働時間短縮を推し進めようとしています。
価格競争に陥った結果のデフレスパイラル
前述したように、日本の労働者は懸命に働いているにもかかわらず、生産性が低いなどと言われています。決して生産する力が低いわけではなく、労働時間が長いことに加え、価格競争に陥った日本経済では生産したものの価格が上がらずに、売上総利益が低い状態で推移してきたという事情があります。
生産物の価格が低ければ、もとより生産が低いことと同義になり、生産性を計算した場合に低くなる結果になります。
- デジタル化の遅れ
日本の企業のうち97%は中小企業です。企業の規模によってITに対する投資力に差異が見られており、全体としてIT化が遅れていることによるという見方もあります。スイスにある国際経営開発研究所(IMD)の統計を基にした「デジタル競争力ランキング2020」の結果によれば、デジタル競争力ランキングにおいて日本は63カ国中27位にとどまっています。
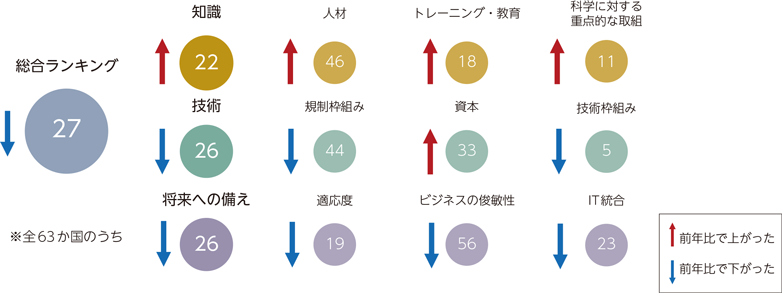
https://www.soumu.go.jp/johotsusintokei/whitepaper/ja/r03/image/n0103030.png
IT投資に積極的な企業が一部にあったとしても、サプライチェーンのどこかでIT化されておらず、手間がかかるようなことが発生すれば時間がかかってしまい、全体としての生産性は落ちます。小さな非効率が積み重なって、全体としての生産性の低さにつながっているとも言えます。
この点では、国も税制面などで支援を行い、IT投資を促進しようとしています。
工場の生産性を向上させるためのステップ
では、工場の生産性を上げるにはどのようにしていけばよいのでしょうか。次のようなステップで進めていくことが考えられます。
業務プロセスの改善
整理・整頓・清掃・清潔といういわゆる4Sに課題があるのなら、まずはここから取り組むことが必要です。工場内の整理整頓が正しく行われているだけで生産効率はだいぶ違います。4Sは現場で働く人にしかできないことであり、意識改革のようなことがベースとして必要になるかもしれません。
次に、無駄な作業、手待ちの発生などがないかどうかのチェックです。工程ごとにかかる時間が違いすぎるため、どこかで詰まってしまっているのであれば、ボトルネックとなる工程を2つに分けるなどの措置を行います。
また、工具やチェック表、参照すべき図面やマニュアル、部品表などを探したり見たりする時間をなるべく短くできるよう工夫する改善も必要です。無理な姿勢での作業が強いられていたり、伝統的にやる必要・重要性のない作業があったり、乾燥待ちなどの手待ちが発生する工程は、極力改善していきます。
データによる可視化
設備に取り付けたIoT機器の活用で生産性の向上を図ることが重要です。今やIoT機器から出るデータを活用することが新しいイノベーションを生み出す源泉になっています。IoT機器から出るデータを集めて、機械が故障するのを事前に察知したり、稼働状況を把握することによって適切な指示を出せたりします。IoT機器とそこから生成されるデータをうまく活用することがこれからの生産性向上には有効になってきます。
デジタルツール・システムの導入
IoT機器からのデータを活用する方法の中には、データ活用基盤の構築をして、機械学習・AIを用いた取り組みも見られ始めています。在庫や出荷に合わせて、車両や機械を適正に稼働させたり、遠隔地からの工場管理などを可能にしたり、あるいはデジタルツインといって、工場内をそっくりコンピュータの中に再現してさまざまなシミュレーションをしてみたりと、これまでできなかったような方法で生産性を上げる試みが始まっています。
設備の再配置・最適化
4Sなどの基本的な対応や、業務の見直しとデジタル化など抜本的改革のなかで、工場内の設備は、設置場所そのものを変更し、最適化したほうが良いという結論も導き出されるかもしれません。最初から設備の再配置や最適化を考えるのではなく、4S、業務プロセスの改善、データ活用と考えた結果の設備再配置の結論になるのが自然な流れでしょう。
工場の生産性が向上した事例
こうしたステップを経て、工場の生産性を向上させた事例を紹介しましょう。
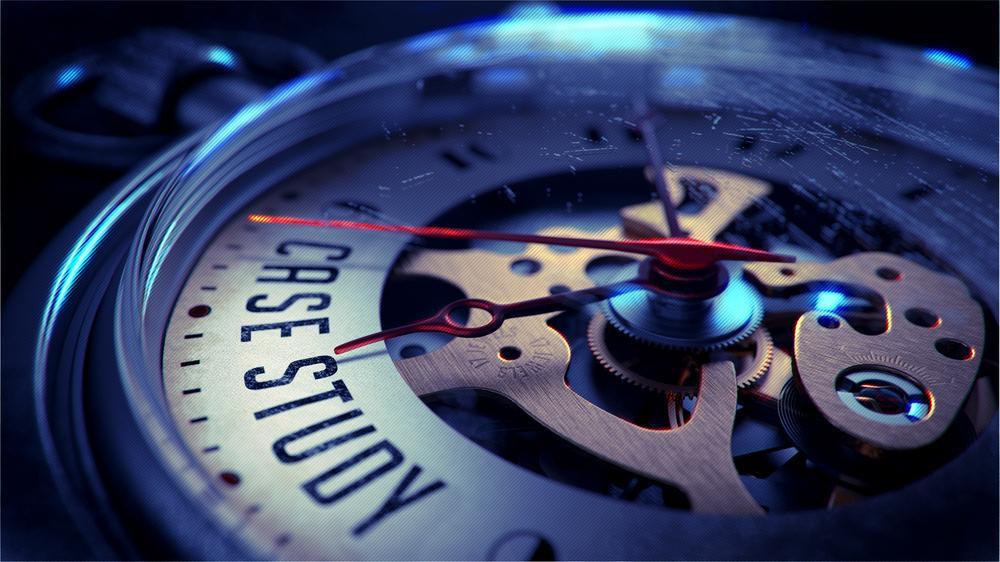
総合食品会社(東京都)
東京都に拠点を持つ総合食品会社は、物や情報の流れを整理して生産性を向上させたいと考えていました。そこで専門家を招いて取り組んだところ、その専門家が最初に着手したのはバックヤードの商品を整理整頓することだったといいます。
ストック棚の追加を行い、カゴ台車の数の最適化を行ったところ、従業員の動きに無駄が無くなり、生産性が5%向上しました。さらに野菜の加工ラインを変更し、導線に無駄がないよう変更したところ生産性は22%向上したといいます。
総菜の製造ラインでも、調理ルールを統一して誰でも同じ品質ができるよう環境整備をした結果、生産効率は39%向上しました。
基本的な見直しだけで、生産性が上がった良い事例です。
食品製造販売業(新潟県)
この企業は、仕出し弁当の製造を行っていました。テーブルの上にパッケージを並べ従業員がその周りを移動しながら盛り付けを行う方法でこれまでやってきましたが、他の方法でもっと効率化できるのではないかと考えました。
そこで、弁当の種類を1種類に集約したうえで、ベルトコンベアを導入し、流れ作業で盛り付けを行ったところ、これまで2時間かかっていた盛り付け作業が、1時間30分でできるようになったということです。
この事例では、従業員の時給を上げることにつながっています。この事例も基本的な見直しを行った例であり、確実に実績が上がっています。
醸造食品製造販売業(岡山県)
この企業では麹を使った食品である味噌や甘酒などを製造販売しています。麹づくりは生物の力を利用した製造業で、どうしても職人の長年の勘に頼らざるを得ないところがありました。また麹づくりには『寝ずの番』などの長時間労働で温度管理を行う必要もありました。
今後は、高齢化に伴い人材も不足してくることが予想されたため、職人の勘の世界をデータに置き換え、可視化することに取り組みました。温度センサーと空調設備を連動させるなどし、自動化に努めたのです。
結果、従業員の長時間労働など労力は大きく軽減させることができ、品質も安定したといいます。さらにそれだけではなく、通販のシステムもIT化し、ファンとなる顧客一人一人を的確に把握できるようにしたため、売り上げは3年間で25%伸びたそうです。
自動車部品製造業(群馬県)
自動車のステアリングに使用する部品を製造するこの企業は、各作業者の徒歩数歩圏内に必要な全ての設備を配置して効率化と省力化を実現、90%の稼働率、60%のファンクションタイム、そして手扱い1工程につき4秒、1個流し、さらに自前設備で高難度の加工にも対応可能な生産体制を構築しています。
1個流しなので中間在庫はゼロとなり、不良品も発見が早くなり、大量に発生しません。設備は最小限で面積も取らず、複数工程を一人でこなすシステムなので技術の育成にも役立ちます。
工程の脱着が可能なので、製品や生産量によってラインの編成が可能、主婦や高齢者の雇用につなげることもできます。また海外展開も容易です。整理整頓と設備の配置による究極の生産性向上の例です。
食品製造業(茨城県)
パンなどを製造している茨木県のこの工場では、消費期限のシールを張り付ける作業を、5名で、56製品・1日当たり約2万3000個、9時間かけてハンドラベラーの手作業で処理していました。納品時間の関係でこの作業を夜中に行う必要があり、作業者の確保もなかなか困難になってきました。
そこで、パラレルリンクロボットと協働ロボットを導入し、正確で素早いラベル張りができるようになったといいます。協働ロボットは箱の用意、パラレルリンクロボットはラベルを張る役割をするそうです。
このロボットの導入によって5人で行っていた作業は2人で済むようになり、労働生産性は2.5倍に向上しました。また、不良品の流出が防止できる副次的効果もあったといいます。
これからの工場における生産性の向上
ここまで、工場の生産性について背景や方法、事例についてみてみました。現在は経済産業省などが中心に、国を挙げてデジタルトランスフォーメーション(DX)への取り組みが盛んですが、実態としては、意外にもDXありきで進んではいないことに気が付きます。生産性向上の第一歩は、現在の業務の見直しから始めるのがよいでしょう。その上で、コスト効率を高めたり、新たな顧客を獲得したりといった取り組みがビジネスとして必要であれば、DXを検討するということになります。
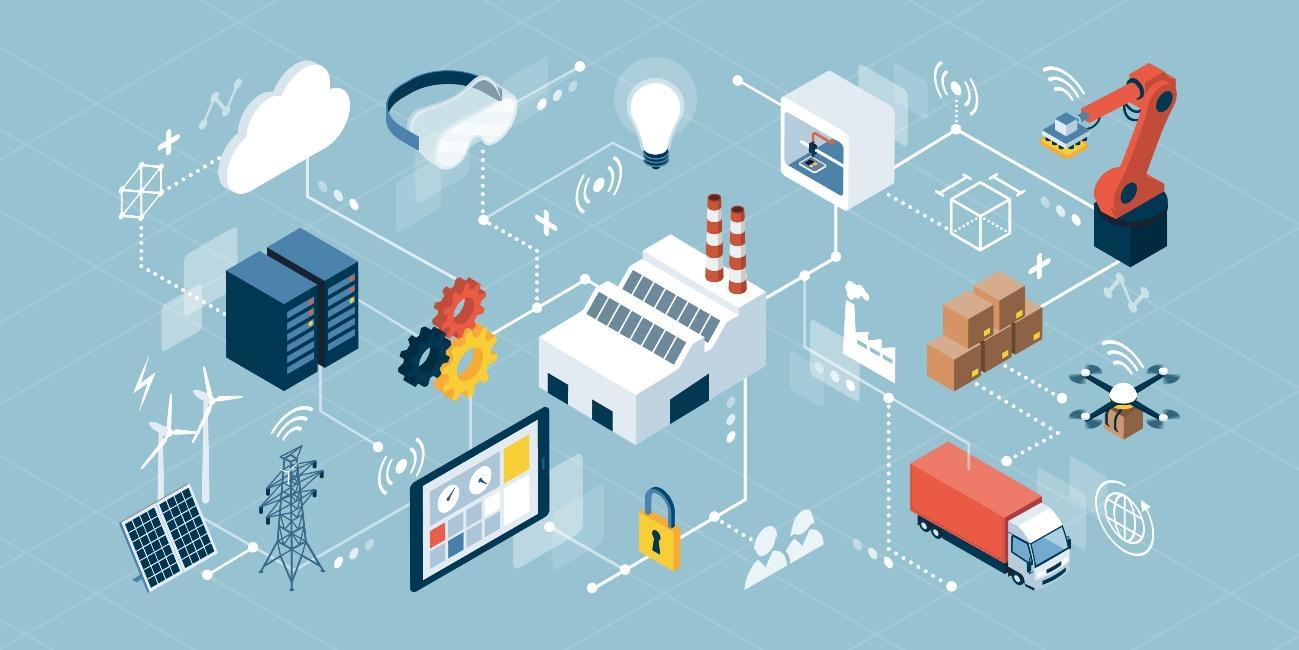
日本の製造業は、かつては世界の模範となった時期もあり、今も大きく遅れているわけではありません。ただし、必要以上に完成度を求めるなど、消費者ニーズを正確に把握しない方法を続けることによって、時代の推移に応じた変化ができていない側面があるのは否定できません。また、不景気などの影響で設備投資が抑えられてきたことで、生産性を思うように向上できなかったことも事実となってきます。
日本経済が「失われた30年」と指摘される時間を過ごしている間に、中国が製造業国家として大きく台頭しました。さらに、人工知能(AI)をはじめとした知的財産の領域でも、中国は米国と並んで世界のトップに上り詰めようとしています。
後れを取ってしまった原因を究明して、日本企業はDXの時代を迎える中で、これまでできなかったことをできるようにし、改めて国際競争力を持つ必要が出てきます。
一方で、人材不足の波は待ったなしの状況であり、経営者には対応が迫られます。新しい時代の工場づくりは始まったばかりですが、まずはどこをどのように変えれば自社の工場の生産性は上がるのか考えるべき時が来たようです。DXとともに変化し、飛躍するべき時が来たと言えるでしょう。