2020年から2021年にかけて、製造業は新型コロナウイルス感染症の拡大や経済安全保障に関わる国際情勢の変化などの影響を受けました。その状況は、不確実性を増した現代の製造企業に対して、企業変革の必要性をあらわにしています。
企業が変革に向けて取り組むことを、経済産業省の「2022年版ものづくり白書」ではダイナミックケイパビリティ(企業変革力)と表現しています。ダイナミックケイパビリティの強化として求められるのがDX(デジタル・トランスフォーメーション)の推進となるデジタル技術の導入です。
製造企業は、デジタル技術の導入により工場のスマートファクトリー化や工場の在庫管理や製造の進捗率などさまざまなデータの見える化を実現できます。工場の見える化は、製造業の中長期的な課題を解決するキーワードになるでしょう。
今回は、製造企業が工場の見える化を目指す理由について解説します。工場の見える化によるメリットや見える化に取り組んだ事例も紹介するので、検討材料としてお役立てください。
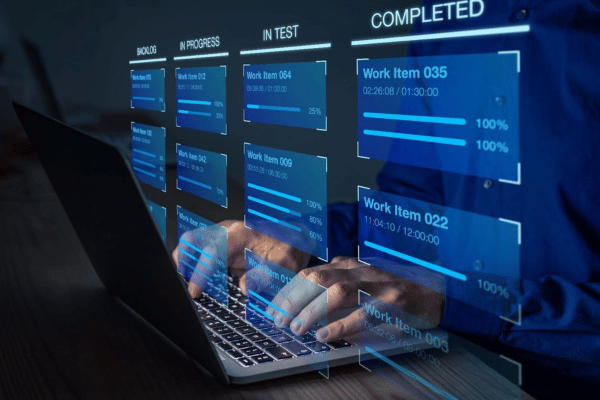
目次
工場の見える化とは
独立行政法人中小企業基盤整備機構の運営している「J-Net21|経営課題を解決する羅針盤」では、「工場の見える化」について次のように定義しています。
“工場の見える化は、近年使われ始めた言葉ではなく、製造業において「目で見る管理」の意味合いで使われてきた表現の1つです。工場の物理的な「モノ」や、その影響を受ける「コト」などの共通認識ともいえます。関係者が共通認識することで、判断や解決策につながる工場の詳細を把握できる状態ではないでしょうか。”
つまり工場の見える化は、さまざまな業務プロセスと工程が同時進行で行われる製造業において、各分野で発生する課題やエラーを迅速に察知して全体に共有できる状態であり、その課題を改善することで業務効率・生産性を上げていくことにつながります。
見える化の事例として、トヨタ自動車株式会社を紹介します。
トヨタ生産方式「アンドン」
トヨタ自動車株式会社では、独自の管理ツール「アンドン」が見える化の役割を果たしています。トヨタ生産方式の「アンドン」は、製造現場の関係者に作業や処置などの行動を促すための情報を表示するツール・仕組みです。次のような仕組みで活用されています。
- 機械に異常が表示された場合:担当者による異常処置・原因を調査し再発防止
- 機械が異常を原因として停止した場合:停止時に自動で赤ランプ点灯・機械を点検
アンドンは、異常検知を起きた場合、即時に工場全体に共有でき、生産ラインの効率的な管理ができます。アンドンはデジタルツールではないですが、工場の見える化に通じる要素を持っています。
トヨタ生産方式「かんばん」(ジャスト・イン・タイム)
効率的な生産を目的に活用されるトヨタ生産方式の「かんばん」は、無駄を撤廃するための手法で、ジャスト・イン・タイムとも呼ばれています。トヨタのかんばんは、「必要なものを必要なときに必要なだけ作る」というコンセプトで生産体制を構築しています。その仕組みは、部品ごとにかんばんというカードを付けることがポイントです。
部品に付いているカードは、組立工場で使う際に外し、外したカードを部品工場の担当者へ届けます。部品工場の担当者は、届けられたカードの数だけ部品を作るため、余計な部品を作ることのない生産管理を実現できます。このカンバンが現在では、電子化されデータで管理されています。
工場の見える化は、トヨタ生産方式のメリットとなる他部署に分かれている生産現場の効率性と正確性を自社工場に反映できます。要するに、工場の状態を全社で把握できる仕組みです。
===
見える化は見せるための手段ではない
工場の見える化は、見せるための手段ではありません。工場の見える化を目的にさまざまな取り組みをした企業が、結果として「見せる化」になってしまっている例も少なくありません。この違いを理解するには、見える化と見せる化を明確にする必要があります。見える化と見せる化の違いは、次のとおりです。
目的 | メリット | |
見える化 |
|
|
見せる化 |
|
|
見える化と見せる化の違いは、ビジネスへの貢献度ではないでしょうか。見せる化は、あくまで現場の状態を見せる(可視化)までを目的とします。見える化は、可視化したデータから課題を洗い出し、課題解決となる施策を実行するまでが対象となるでしょう。
工場を見える化する理由
工場を見える化する目的は、あくまでも製造現場の状態を正確にあらゆる角度から必要とする関係者に伝達することです。工場の見える化を実現することで、部門横断的なシステムによって現場状況を逐次伝達可能になるため、スピーディな経営判断に役立ちます。その結果、製造現場における人手不足の課題や技能の属人化を解消でき、業務環境や生産性の向上まで期待できるでしょう。
工場における見える化の目的は現場の状況を素早く把握して、状況の改善や経営判断に活かすものです。そのため見える化を実現する手段にはデジタル技術の導入が欠かせないのです。
経済産業省が公開している「2022年版ものづくり白書」では、ものづくりの工程・活動におけるデジタル技術の活用状況を公開しています。デジタル技術を活用している企業は、調査に参加した製造企業全体の67.2%という結果です。一方のデジタル技術を活用していない製造業は、31.1%という数字になっています。
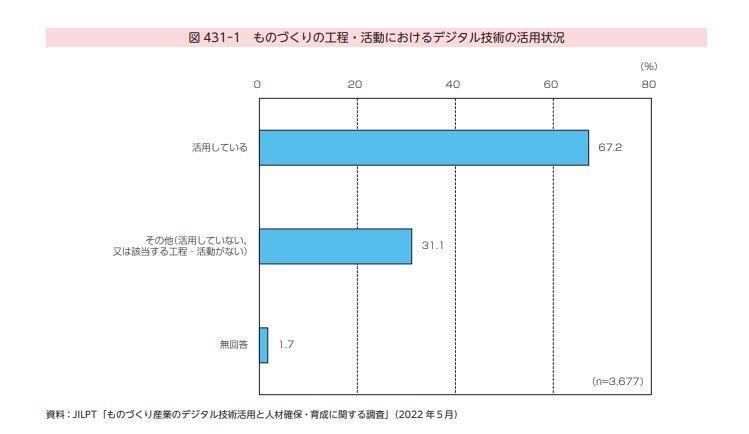
さらに同資料では、無形固定資産の投資目的を2015年と2020年で比較しており、「工場のIoT化等」が9.4%から19.1%へと増加しており、IT投資の目的は「業務の効率化やコスト削減」が52.0%、「工場のIoT化等」が46.5%と高い割合となっています。
さらに具体的なIT投資の項目では、「生産管理を目的にしている」企業が最も多く、全体の65.4%となっています。さらに、工場の見える化がもたらす部分でもある「全社的・部門横断的なシステムへの投資」が59.3%と同じく高い数字です。
多くの企業が、部門間で遮断されがちな情報を見える化するため、全社的・部門横断的システムを導入することで、素早く課題解決をして生産性の向上を図ろうとしていることがわかります。
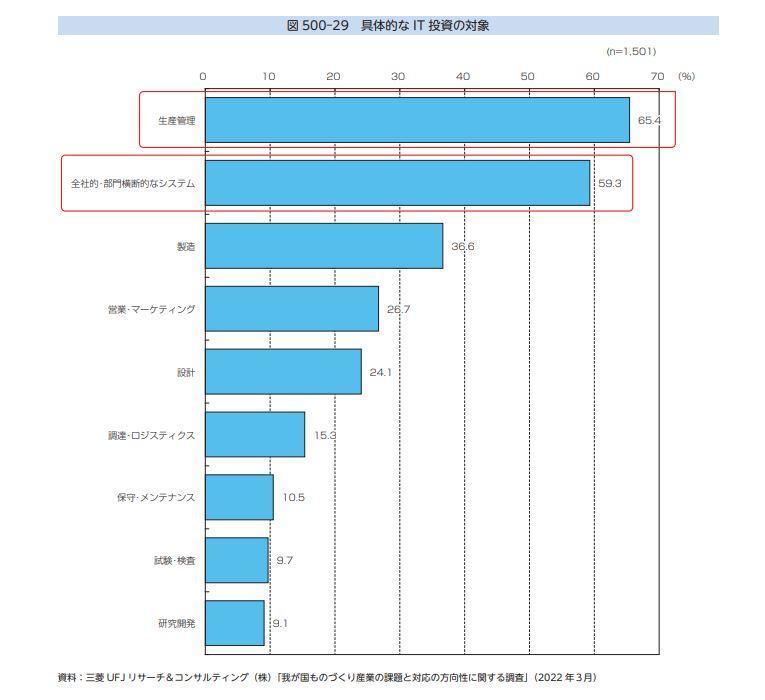
工場の見える化による4つのメリット
工場の見える化は、製造現場にIoT(Internet of Things:モノのインターネット)を導入して設備や人などの情報をデータ化および連携が必要です。前述した全社的で部門横断的なシステムとは、IoTシステムの導入による取り組みともいえます。IoTを導入することで、工場の見える化が製造現場にもたらす代表的なメリットを4つ紹介します。
- 課題を正確に把握できる
- 業務プロセスの社内共有が実現する
- 属人化を阻止できる
- ブラックボックス化を防げる
課題を正確に把握できる
工場の見える化は、製造現場の現状をインターネット経由で情報データに変換して伝達します。その情報は、適切なデータに変換されて物理的に処理されるため、現場の正確な情報の把握が可能です。現場の情報を正確に伝達できることは、課題の早期発見にもつながります。
現場の生産プロセスと資源データなどを連携できれば、「ムリ・ムダ・ムラ」も定量的に判断できるようになり、課題の早期発見から迅速な改善への取り組みまでのサイクルを構築することが可能です。
業務プロセスの社内共有が実現する
工場の見える化で伝達する情報は、客観的なデータとなるため、全社での目標達成や進捗率など部門間で課題を共有することが可能です。作業スピードや品質などのデータは、業務プロセスとして標準化することも可能です。標準化された業務プロセスが社内共通のプロセスとして浸透できれば、安定した品質で生産性の向上を目指せるでしょう。
属人化を阻止できる
製造業においては、デジタル技術の真逆となる属人化が課題のひとつです。属人化は、生産ラインの各工程において定量的なマニュアルがなく、人の裁量的な判断で作り出されます。各工程で独自の得意な作業を生み出してしまうと、その部分だけ特定の人に依存してしまう状況になるでしょう。この状況を放置してしまうと、持ち場ごとの属人化が進みます。
工場の見える化は、機械の動作や作業担当者の手の動きなど、製造現場のあらゆる状況をデータ化します。そのデータは、定量的なマニュアル作成のもととなり、属人化の阻止に役立つでしょう。
ブラックボックス化を防げる
製造業では、熟練技能者の匠(たくみ)の技を引き継ぐまで5年や10年など相応の経験を求められます。ただし熟練技能者の技術は、専門性が高く、データ化されていないため正しい作業コストを判断できなくなっています。納期がある業務においてアウトプットを優先することで、作業のプロセスや詳細が不透明になり、ブラックボックス化していきます。
工場の見える化は、作業工程に不透明な部分を作らないため、ブラックボックス化を防げます。見える化により透明性のある生産工程で作業の効率性を高められるでしょう。
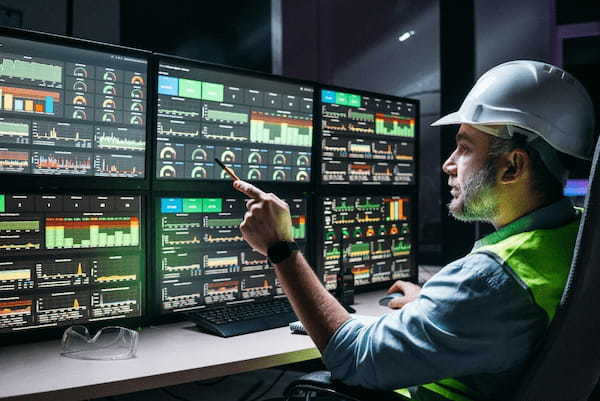
工場の見える化に向けた具体的な取り組み
製造企業は、工場の見える化に向けてどのように取り組んでいるのでしょうか。具体的な取り組みについて紹介します。
人の動きを見える化する具体的な取り組み
人の動きを見える化する具体的な取り組みとは、作業時間や作業内容のばらつきを可視化することです。人による作業は、基本的にばらつきが生じます。ばらつきを明確にすることが、見える化への取り組みになるでしょう。具体的には、作業時間や作業内容を製造日報で管理する場合も工夫が必要ですし、熟練者の動作をカメラやセンシング技術で分析して若手に継承するなどが挙げられます。
製造日報の入力を紙ベースで行っている場合は、デバイス端末を活用した電子入力への移行が求められます。また、入力に個人差を生み出さなくする工夫では、音声入力なども効果的です。
モノを見える化する具体的な取り組み
モノ(設備)を見える化する取り組みは、製造現場に設置された機械から数値データを取得しデータの連携および活用することです。具体的には、製造現場の設備がセンサやカメラで稼働状況をデータ化できる状態にします。センサやカメラにより入手した情報は、IoTで伝達され遠隔で管理することが可能です。
センサによる予測感知ができれば、異常検知に役立ちます。迅速に異常検知できれば、大きな故障トラブルを未然に防げるでしょう。また生産現場でくり返される作業工程をデータ化できれば、機械設備の遠隔管理も行えます。
工場の見える化を妨げるもの
経済産業省の公開している「製造基盤白書(ものづくり白書)2020年版」では、製造現場のライン・製造工程全般の稼働状況について見える化を実施している企業は、2019年の時点で全体の17.9%です。また全体の41.5%の企業が「可能であれば実施したい」と考えています。
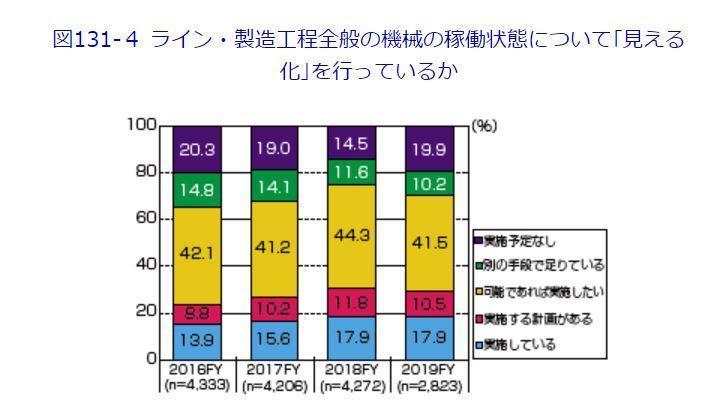
工場の見える化は、2019年の段階で全体の2割にも満たない実施状況です。見える化の実施が進まない要因は、先述した製造現場作業の属人化やブラックボックス化以外にも考えられます。それは、冒頭で触れたダイナミックケイパビリティを低下させる古い基幹系システムの存在です。
レガシーシステムからのデータ移行
経済産業省が公開している「DXレポート〜ITシステム『2025年の崖』克服とDXの本格的な展開〜」では、国内企業の8割が老朽化した複雑な基幹システムを使っていると伝えています。実際には、50%の国内企業がレガシーシステムの存在に対して、DXの妨げとなっていると判断しています。
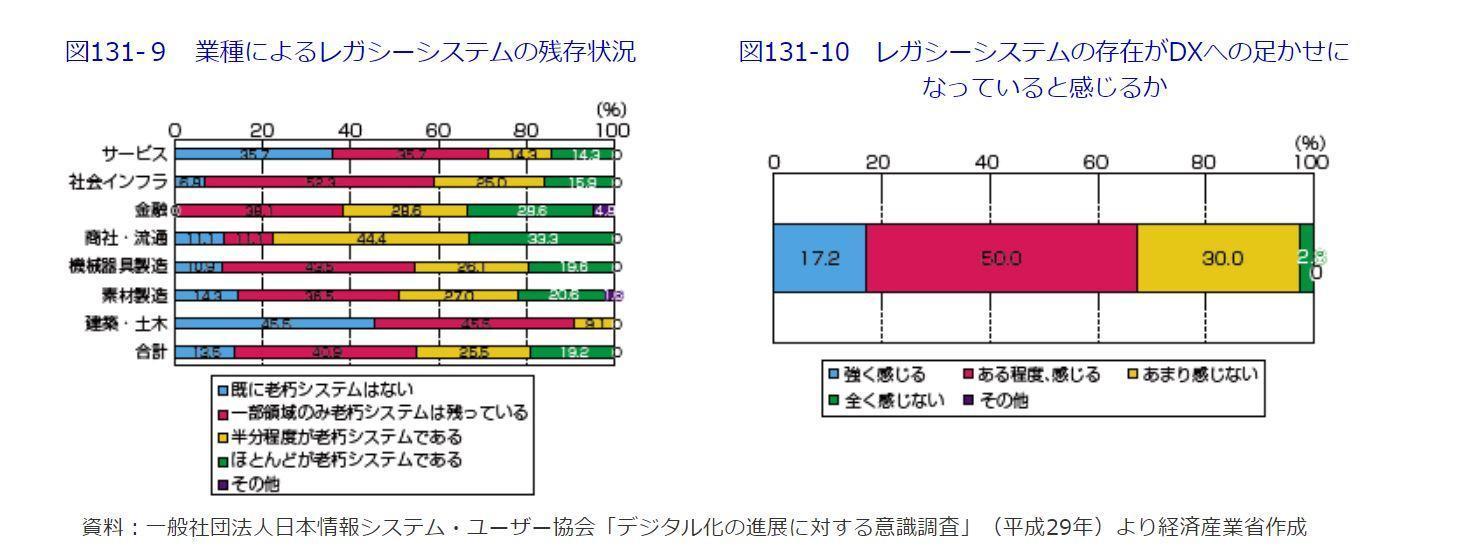
つまり、ブラックボックス化したレガシーシステムからのデータ移行を課題に抱えている状況も考えなければなりません。経済産業省による同資料では、この問題を「2025年の崖」の問題と掲げています。ダイナミックケイパビリティの強化には、「2025年の崖」問題を乗り越えなければ、膨大なデータへの対応ができず、結果的に古い基幹システムも活用できなくなるわけです。
つまり、製造業のDXは時間の猶予がない状況まで来ているといっても過言ではないでしょう。工場の見える化は、現状のレガシーシステムに妨げられているのかもしれません。
工場の見える化に成功している企業事例
工場の見える化は、それぞれの企業でどのように実施しているのでしょうか。ここでは、見える化に成功している企業事例を紹介します。
エネルギーの見える化事例:矢橋大理石株式会社
建築用の石材加工や鉄道車両部品、バルブ部品製造販売の「矢橋大理石株式会社」は、工場エネルギー使用量を見える化し、省エネ活動に貢献しています。同社は、石材加工および電子プリント基板、鉄道車両部品製造と3つの事業展開で成長を目指している企業です。
同社は、エネルギー管理において2017年2月に「中部地方電気使用合理化委員会委員⾧表彰」や2020年2月の「中部経済産業局⾧表彰受賞」などを受けています。その評価の取り組みとなる電子生産部の省エネ活動では、エネルギー管理組織による改善があげられます。
同社の省エネ活動は、ABM(Activity Based Management:活動基準管理・コストマネジメント)設備で未使用時のエアー停止による電力削減です。エアーが停止している状態は、システム入力上で確認できるように見える化されており、IoTの導入によりコンプレッサーの稼働状況をリアルタイムに監視し、アラートメールで迅速な対応を実現しています。
その効果は、リアルタイムな判断による圧力の調整で無駄な起動や停止を撤廃しました。同社は、測定機器の活用による見える化(工場使用電力の監視強化)でさらなる削減を今後の取り組みとして掲げています。
生産計画の見える化事例:ダイニチ工業株式会社
石油風呂釜メーカーのダイニチ工業株式会社は、全自動の業務用石油ストーブや家庭用石油ファンヒーターなど約140種の石油暖房機器の製造販売を手掛けています。同社の課題は、季節商品である石油暖房機器の生産管理です。気候状況の影響を受ける製品に対して、迅速な商品化がビジネスのカギとなっています。
その対策として、自社製造現場にIoTやロボットを導入し、生産ラインの業務効率化を図りました。同社のこの取り組みは、ハイドーゾ生産方式といわれ受注から4時間で製品の工場出荷を実現しています。
同社が実施した工場の見える化は、全社的および部門横断的なデータ連携を可能にしています。見える化された工程は、次のとおりです。
- 受注後の資材供給調達
- プレス加工
- 塗装
- 組み立て
- 出荷情報
IoT技術により、リアルタイムな状況把握を実現したこの仕組みは、随時画面上で情報やデータを確認できることに加え、活用することで受注から4時間で製品出荷が可能になっています。
着座センサで製造過程の見える化に貢献する事例:株式会社メトロール
高精度工業用センサの製造販売をおこなう株式会社メトロールは、主力製品の「着座センサ」で製造現場の生産管理の見える化を実現しています。同社の着座センサは、工業機械の切削作業で発生する切削粉の混入などを検知して不良品を防止するものです。これまで切削粉の混入は熟練の職人に頼らざるをえず属人化するリスクがありましたが、このセンサにより自動化することが可能となりました。1,000分の1ミリメートルの反復作業を実現する精密さが特徴です。
同社は、生産管理システムで自動発注も可能にしています。センサによる生産管理システムが生産現場のリードタイムの短縮を実現し、生産現場の進捗(しんちょく)状況を見える化しました。
工場の見える化でベテラン業務を自動化し属人性を低減させよう
工場の見える化は、製造現場のデジタル化なくしては語れません。製造現場の抱える課題となる属人化やブラックボックス化は、IoT技術により浮き彫りとなってきます。その課題は、客観的に判断できるデータ化できれば、事例で紹介した企業のように受注から出荷までの工程を効率よく進められるでしょう。
工場の見える化は、属人化したベテラン技術者の業務を自動化します。自動化により製造事業の横展開が可能となるでしょう。これら設備や業務フローの最適化は、専門家の知識と経験が不可欠です。伴走型の業務コンサルティングと運用時の体制支援を活用することで計画的にDXを実現できます。