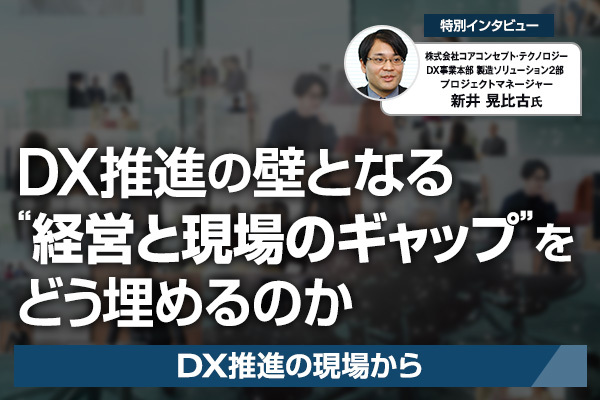
DX事業本部 製造ソリューション2部 プロジェクトマネージャー
大学卒業後、大手電気部品メーカーに入社。入社2年目で放電加工の自動化プロジェクトを推進し、大幅な生産性向上を実現。その後も社内でDX推進や業務の平準化を実行し、●●年に株式会社コアコンセプト・テクノロジーに入社。より多くの製造業の課題を解決することをモットーに、経営と現場の繋ぎ込み、ユーザー視点を重視した成果に直結するDX推進を手がける。写真撮影が趣味。
DXの情報や知識、事例はインターネット上・書籍などさまざまなコンテンツを通して情報が届けられています。しかし、DX推進の答えは企業の数ほどあると表現しても過言ではなく、さまざまな要因によってアプローチ方法は異なります。
多くの企業のDX推進を現場から支援してきたプロフェッショナルからヒントを得る企画「DX推進の現場から」の第1弾は、株式会社コアコンセプト・テクノロジーの新井 晃比古氏に話を伺います。
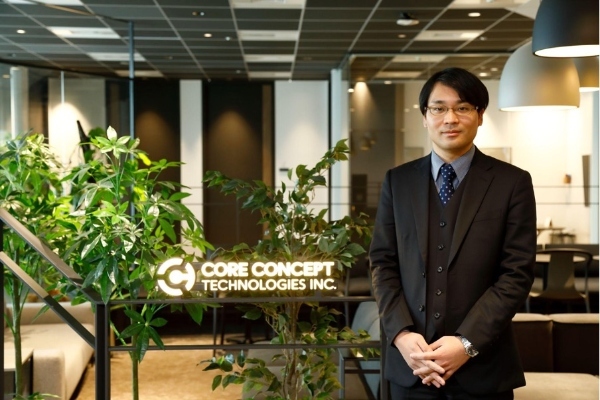
ーー新井さんはメーカー企業での技術者としてキャリアをスタートしています。まずはこれまでのご経歴からお伺いしてもよろしいですか。
新井:前職では長野県の大手電気部品メーカーで内製の金型を作る部門に勤めておりました。
大学時代に工業系の物理学、量子力学を専攻していて、かなり微細なものを扱う研究をしていました。そのため学生時代から微細加工が必要となるメーカーに勤めたいと思っており、ご縁があったのが、製造に当たってプラスマイナス1ミクロンの世界での微細加工を必要とする前職の金型部門でした。
ーー前職ではどのような業務をご経験されたのでしょうか。
製造工程をすべて実務ベースで経験しました。
具体的には切削や研磨、放電加工など金型部品を作るための様々な工程や、3次元測定器や表面粗さ測定器などを使って実際のものを測る品質検査業務、金型自体のパーツを組み上げる作業などですね。
このような業務を経験する中で、例えば放電加工の工程で手作業が多すぎて効率が悪かった点に課題を感じました。そこで入社2年目のときにソフトウェアパッケージを活用して工程の自動化を実現するためのプロジェクトを提案し、実行することになりました。
そのプロジェクトでは、まずは3D CADのモデルを組み合わせつつシステムの使い方のマニュアルを作成。その後、放電加工の現場作業員の方を教育して、 無事運用軌道に乗せることができました。
出来合いのパッケージソフトを活用しただけだったので、私が何か開発したわけではないのですが、1つの工程の自動化を実現した実績を買われ、所属部署の部長から MES(製造実行システム)の導入プロジェクトを打診され、プロジェクトリーダーとしてMESの導入を担当しました。
ーーいわばDX推進担当者の立ち位置ですね。入社2年目の時点で、なぜそこまで自動化の必要性を感じたのでしょうか。
新井:今思うとかなり生意気でしたね(笑)。
各現場の実務を回っている際に、工程の作業手順や、加工機のオペレーション方法など、先輩技術者にくっついて作業を覚える必要がありました。体質的に「見て覚える」文化がまだ残っており、作業の平準化・効率化の点からマニュアルがないとまずいな、と身に染みて感じましたね。
高齢化が進んでいる製造の現場では、職人さんがどんどん定年退職で辞めていく一方で、同じクオリティ、生産高を維持することが求められます。そのような中で、マニュアルの有無は若い層にとって死活問題となります。
そこから着想を得て、自動化もマニュアルさえ整備すればもしかしたら軌道に乗るんじゃないかと、2年目で提案しました。
ーーDXや自動化のプロジェクトでは現場の反対にあってしまい、頓挫してしまうケースも多いです。プロジェクトを推進するにあたって現場との連携に課題はありましたか?
新井:前職は手挙げて取り組む人を尊重する社風でしたので、かなり自由に現場とのコミュニケーションが取れました。
マニュアルの浸透では、まず従来の工程の業務を全く知らない同期にマニュアルを見てもらいました。初めての方が先入観なく理解できるかどうかを確かめるためです。その水準になるまで推敲を繰り返し、ある程度の段階で、今度はライン長レイヤーの方々に時間を割いてもらい、マンツーマンでマニュアルを1ページずつ理解してもらうステップを設けました。その時点で、ライン長の方々はマニュアルを完全に理解していますので、そのライン長の方々から現場作業員に展開してもらいました。
ーー社内浸透の設計を練られて実行されたんですね。プロジェクトはどのような成果がありましたか?
新井:放電加工の工程はとても加工時間が長く、長いものだと数十時間かかってしまいまうのですが、休日に人がいない時間であっても自動で稼働する状態になり、キャパシティが劇的に上がりました。
放電加工の自動化プロジェクトを担当した後、MES(製造実行システム)や基幹に近いシステムの導入の他、お付き合いのあったITベンダーの方から、スキルトランスファーという形で、ウェブアプリ開発におけるフロントエンドやバックエンド、サーバーサイドについても一通り全部教わり、社内のシステム担当のような立場となり、さまざまな業務改革に携わりました。
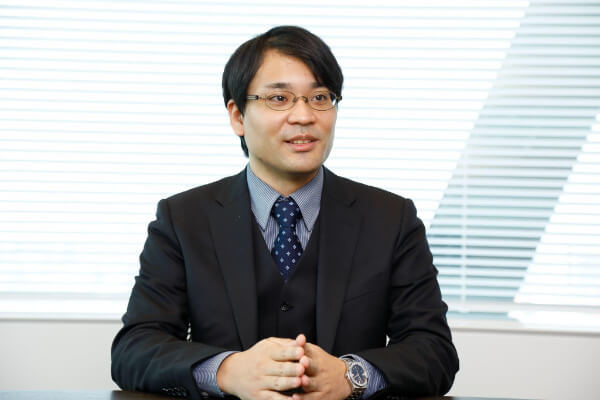
ーー現在はCCT社でどのような業務をされているのでしょうか?
新井:これまでの経験から、技能承継や業務効率化などで悩んでいるより多くの企業の手助けをしたいと考えるようになり、そのときに製造業に強いIT企業としてCCTの存在を知ったのがきっかけです。
現在は、製造業でも特に、ハードウェアとの連携が絡む案件に関わることが多いです。まだプロジェクトが始まっていない段階で企業の工場を訪問し、実際の工程を拝見した上で、 課題点やシステムへのニーズを聞かせていただき、AS-ISの調査やTO-BEを描いた上で、どのくらい費用対効果が見込めるかという試算や改善提案を行わせていただいてます。
ーー製造工程とシステム、双方のご知見がある新井さんにぴったりの業務ですね。
新井:自分で言うのも恥ずかしいのですが、私の強みとしてはディスクリート系の製造であれば、各加工機を実際に扱った経験があり、品質管理領域においても資格を持っており検査器具も使えるため、顧客の課題を解像度高く理解できる部分にあるのかなと考えています。
ーーDX推進にあたっては、現場サイドと経営サイド双方の視点を持つことが重要です。クライアントとコミュニケーションを取るなかで、気をつけているポイントはなんでしょうか?
経営者の方も現場の作業員の方も、それぞれの視点で課題やアイデアを持っている一方で、視点の違いからそれがうまく噛み合ってない状態が多いと感じます。
経営サイドが、削減目標とか、売上やキャパシティを伸ばすという目標を立てるが、現場としては具体的にどのようなことをやればいいのか、までは落とし込めていないケースが多いです。
逆に現場では経営者の考える全体方針を理解しきれていない中で、自分が担当しているラインがきちんと納期を守り、売上やキャパシティを上げて生産する部分に責任を持っています。その視点自体は決して間違っていないのですが結果的に個別最適に終始してしまっていることがあります。
そこに我々のようなIT企業が入って、経営者の目的を実現する手段と現場作業員が持っているものをうまく繋いであげて全体最適への道筋を描いてあげることが求められるのかなと思います。
ーーDX推進する中でこだわりや特に重視されているポイントをお伺いできますか。
新井:適切なツールやソリューション・システムを導入する際に、ユーザーの目線に立って考えることが1番重要だと思っています。
こうすれば開発コストを抑えられますと言っても、ユーザーが使いづらかったら意味がないし、 現場の作業員の方は入力の工数が多いとどうしても煩わしく感じて、結局システムを使わなくなってしまいます。
社内でも基本設計フェーズの画面設計では、このUIではタップ回数が多いから現場作業員の方は使えないよ、とダメ出ししたりすることはよくやっています。どこまでユーザーフレンドリーを追求できるかという部分はこだわってます。
ーー現在の業務で特にご自身がやりがいを感じてることはありますか。
TO-BEの提案をして、クライアントの社長さんから提案内容に非常に満足してますと言っていただけたのがすごく嬉しかったですね。
そういった時はやっぱりちゃんと役に立ってるんだと思ってやりがいを感じますね。
どうせ仕事するなら、人に喜ばれることをやりたいなとは常々思っています。
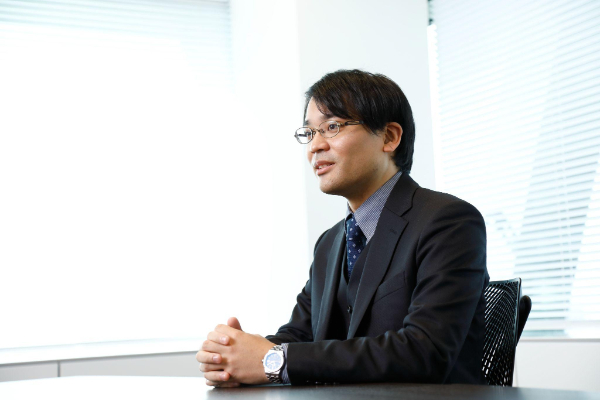
ーー今後チャレンジしていきたい課題や目標はなんでしょうか。。
新井:よりハードウェアとの連携を絡めた案件に携わっていきたいと思っています。 最近、直近担当した案件で、AGV(個人搬送車)の背中にロボットアームを置き、従来人が行っていた「物をピッキングして運ぶ」という作業を全て自動化して、運んだ先の加工機もMESでコントロールして、 スマートファクトリーの一歩目のような取組を行いました。
今後はもっといろんな設備を連携してMESで集中管理し、全く人がいなくてもずっと材料を供給して動き続けるような完全なスマートファクトリーを実現したいです。
ーー様々な設備をMESで集中管理するのはかなり難易度が高いことなのでしょうか
どこまでがハードウェアメーカーが責任を担保し、どこまでがソフトウェアメーカー側が担保するのか。この所掌範囲が明確でなくなるという点は1つの課題だと思っています。
ハードウェアメーカーはERPやMESなどの大きなソフトウェアパッケージまでは扱えない一方、SIerはソフトウェアの部分だけを担保したい考えがあり、どうしても責任の押し付け合いみたいな部分が出て、分断されてしまいます。
また、装置メーカーだと自社の装置間でしか連携できない課題もあります。
もっとメーカーをまたいで繋げられると考えているので、ERPの受注情報から製造の情報をMESに与え、その情報に従ってMESが加工機にものを作る指示を出す、といったところまで実現できるのが理想ですね。
ーーまさにスマートファクトリーの実現という感じですね。この思いは新井さんの原体験である自動化のお話にも繋がってきますね。
新井:納期に間に合わせるために無理やり土日に稼働するといったことが製造業ではどうしても起きてしまいます。
このようなことを削減できると、残業代の抑制にも直結し、経営的に重要なのはもちろん、従業員の働き方改革にもつながります。自身がメーカー勤務時代も定時でちゃんと家庭に戻れるというのはすごく嬉しかったので、そのような幸せが実現できる存在でありたいなと思いますし、ものづくりが魅力的な業界であり続けて欲しいと願っています。
(提供:Koto Online)