タクトタイムを求めれば、一つの製品にかけられる時間を示すだけでなく、人員配置の最適化やボトルネック工程の改善に役立てられます。本記事では、タクトタイム・サイクルタイム・リードタイムの関係性や、タクトタイムの計算方法などについて解説します。
目次
タクトタイムとは
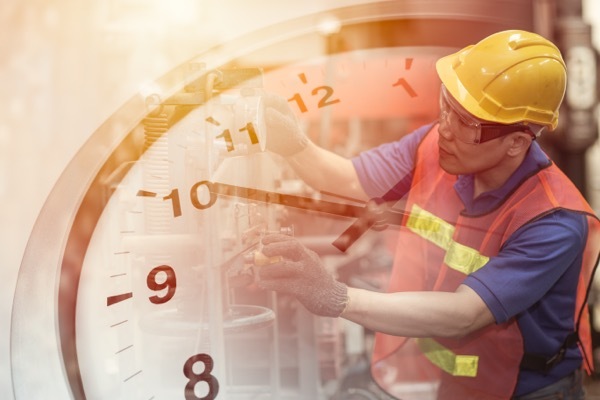
タクトタイムとは、一つの製品の製造にかけられる時間のことです。製品をつくる間隔を表すことから、ピッチタイムと呼ばれることもあります。タクトタイムは、稼働時間を必要生産数で割ることで求められます。
タクトタイム=1日の稼働時間/1日の必要生産数
必要生産数は、納品数を納期の稼働日数で割ることで求められます。必要生産数は時期や需要によって変動するため、それに応じてタクトタイムも変動します。タクトタイムが短くなれば、その分製品を素早く製造する体制を取らなければなりません。
タクトタイムの計算方法
具体的な例をもとに、タクトタイムの計算方法を解説します。稼働時間や納期は以下の通りです。
1日の稼働時間:10時間(36,000秒)
納期までの稼働日数:30日
納品数:3万個
まず、1日の必要生産数を求めるために、納品数を納期までの稼働日数で割ります。
必要生産数
=納品数/納期までの稼働日数
=30,000個/30日
=1,000個/日
1日の必要生産数は1,000個だとわかりました。次に、1日の稼働時間を1日の必要生産数で割り、タクトタイムを求めます。
タクトタイム
=1日の稼働時間/1日の必要生産数
=36,000秒/1,000個
=36秒/個
タクトタイムは36秒とわかりました。ただし、納期に製品が完成しても、すぐ取引先に届けられない場合もあります。輸送に時間がかかる場合は、納期までの稼働日数から輸送にかかる日数を引くなど、状況に応じて計算しなければなりません。
タクトタイムの重要性
タクトタイムは、特に製造業の現場で重要視されています。世界トップの自動車メーカーであるトヨタもタクトタイムを活用しています。
同社の生産管理システム「トヨタ生産方式」の考え方の大きな柱は、「ジャスト・イン・タイム」と「ニンベンの付いた自働化」の2つです。その中の「ジャスト・イン・タイム」は「必要なものを必要な時に必要なだけ作ること」と定義されています。
これは、需要に応じて製造する=売れるペースで製造する、ということです。同社では、売れるペースで製造するための指標として、タクトタイムを活用しています。変動するタクトタイムに応じて、人員配置や作業の組み合わせ方を変えれば、業務効率化が図れます。
実際にトヨタの生産現場では、タクトタイムと従業員の能力を数値化することにより、人員配置を最適化しています。数値化すれば、タクトタイムに対して余裕のある工程やボトルネック工程がわかるため、作業の再分配や効果的な業務改善が可能になります。
タクトタイムとサイクルタイムの違い
タクトタイムと関連性の高い言葉に「サイクルタイム」があります。タクトタイムと大きく異なる点は、視点となる立場です。タクトタイムは生産設備の能力を考慮しない顧客視点の時間であり、サイクルタイムは自社の生産設備の能力を考慮した生産者視点の時間といえます。
サイクルタイムとは
サイクルタイムとは、自社の生産設備で一つの製品を製造するのにかかる時間です。サイクルタイムは、実際の稼働時間を生産数で割ることで求められます。
独立した作業工程が複数ある場合、サイクルタイムは製品を製造するために踏む工程の中で最も時間のかかる工程(=ボトルネック工程)の時間と等しいという特徴があります。
サイクルタイムは生産設備の能力や従業員の技術力によって変動するため、製品が同じでも企業や工場によって異なります。サイクルタイムはボトルネック工程にかかる時間と等しいため、サイクルタイムの短縮にはボトルネック工程の改善が効果的です。
サイクルタイムの計算方法
サイクルタイムは、過去の稼働実績をもとに計算します。例として、下記の過去1ヵ月の稼働実績をもとにサイクルタイムを求めます。
1日の稼働時間:10時間(36,000秒)
稼働日数:30日
生産数:4.5万個
ここでは、1日当たりの数値にして計算します。まず、1日当たりの生産数を求めるために、生産数を稼働日数で割ります。
1日当たりの実際の生産数
=生産数/稼働日数
=45,000個/30日
=1,500個/日
1日当たり1,500個の製品を製造していることが分かりました。次に、生産数を稼働時間で割り、サイクルタイムを求めます。
サイクルタイム
=1日当たりの稼働時間/1日当たりの生産数
=36,000秒/1,500個
=24秒/個
サイクルタイムは24秒とわかりました。
サイクルタイムは、タクトタイムとよく比較されます。詳しくは後述しますが、もしタクトタイムがサイクルタイムより短ければ、生産能力を上げなければならないからです。サイクルタイムは過去の実績をもとに算出するため、実際の生産能力を測るのに役立ちます。
タクトタイムとリードタイムの違い
タクトタイムと同様に、製造現場でよく用いられる言葉に「リードタイム」があります。タクトタイムは一つの製品の製造にかかる平均の時間を表しますが、リードタイムは工程や作業が開始してから終了するまでの時間を指します。
リードタイムとは
製造業においてリードタイムは、生産リードタイムと顧客リードタイムの2つに分けられます。生産リードタイムは、材料が生産プロセスに投入されてから製品になるまでの時間です。一方、顧客リードタイムは発注してから納品されるまでの時間を指します。つまり、生産リードタイムは顧客リードタイムの構成要素といえるでしょう。
それぞれの特徴から、生産リードタイムは生産者目線のリードタイムであり、顧客リードタイムは顧客目線のリードタイムといえます。どちらも重要なリードタイムですが、顧客の評価に直接影響するのは顧客リードタイムです。そのため、従来は生産リードタイムの短縮に注視していたトヨタも、近年は顧客リードタイムに主眼を置くようになったそうです。
リードタイムの計算方法
リードタイムは、受発注してから納品するまでに経由する構成要素を足し合わせることで求めることができます。それぞれに含まれる構成要素は後述しますが、リードタイムを「開発・調達・生産・納品」に分けると、生産リードタイムと顧客リードタイムは以下のように求められます。
生産リードタイム=生産
顧客リードタイム=開発+調達+生産+納品
ここからは、それぞれの具体的な構成要素を解説します。
開発リードタイム
開発リードタイムとは、製品の開発にかかる時間です。製品の開発がすでに完了している場合は、開発リードタイムは発生しません。製造業の場合、製品を生産できる体制の構築まで完了している必要があります。
調達リードタイム
調達リードタイムは、製品をつくるために必要な材料や資材を調達する時間です。調達リードタイムは、主に以下の要素で構成されています。
- 顧客からの受注
- 必要な材料の手配
- 作業の準備
- 製造機器の準備
調達リードタイムは、受発注システムや在庫の有無によって変動します。材料を海外から輸入する場合や、調達元を新たに選定する場合は、調達リードタイムが長くなる傾向にあります。
生産リードタイム
生産リードタイムは、材料をもとに製品を製造する時間です。生産リードタイムは、主に以下の要素から構成されています。
- 製造(加工・成形)
- 包装
- 工程間の運搬
- 品質検査
先述の通り、現在は生産リードタイムよりも顧客リードタイムのほうが重視される傾向にあります。しかし、生産リードタイムは顧客リードタイムの一部であるため、生産リードタイムの短縮は、顧客リードタイムの改善に直接的に役立ちます。
納品リードタイム
納品リードタイムは、製造の完了から納品までにかかる時間です。納品先が遠かったり、輸送手段がフェリーや陸送だったりすると、納品リードタイムは長くなる傾向にあります。納品リードタイムの構成要素には、以下のようなものがあります。
- 入庫
- ピッキング・積み込み
- 各拠点への輸送
- 顧客への配送
運送会社や天候が関与するため、納品リードタイムは計算通りにいかないことがあります。悪天候などで遅延が予測される際は、納品が遅れることを事前に伝えておくとよいでしょう。
タクトタイム・サイクルタイム・リードタイムの関係性
ここまでに解説した3つの時間について、それぞれの定義をおさらいしましょう。
タクトタイム | 一つの製品の製造にかけられる時間 =「必要な生産能力」を示す |
サイクルタイム | 一つの製品の製造にかかる実際の時間 =「実際の生産能力」を示す |
リードタイム | 受発注から納品までにかかる時間 |
タクトタイムは、納期と納品数から机上の計算で求める時間です。この時間と、自社の生産能力を示すサイクルタイムを比べることで、必要な稼働時間や追加人員数が分かります。
例えば、タクトタイム=サイクルタイムであれば、必要な生産能力と実際の生産能力が等しいため、運用方法を変えることなく納期までに納品できることが分かります。
しかし、タクトタイム<サイクルタイムの場合、実際の生産能力が必要な生産能力に達していないため、納期までに必要量を生産できません。この場合、稼働時間や人員を増やすなどの対策を打たなければなりません。
また、タクトタイム>サイクルタイムの場合、実際の生産能力が必要な生産能力を上回っているため、余裕をもって納品可能です。しかし、タクトタイムのほうが過剰に大きい場合、作りすぎや無駄な手待ちを引き起こす可能性が高くなります。
よって、タクトタイム<サイクルタイムとならないよう気を付けつつも、可能な限り等しくなるように生産能力を調整する必要があります。
サイクルタイムを短縮するための施策
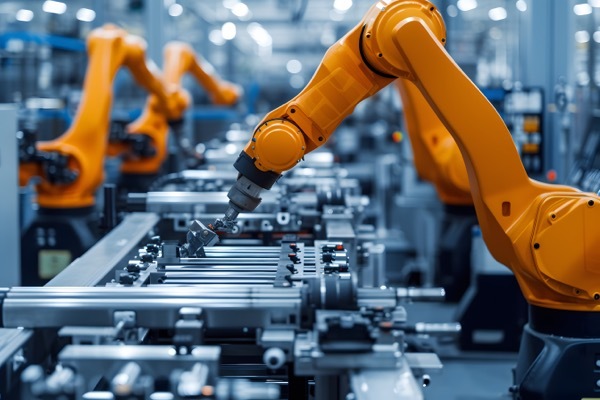
サイクルタイムを短縮すれば、リードタイムも短くなり、顧客により早く商品を届けられるようになります。サイクルタイムは、以下のような施策を講じることで短縮可能です。
- 予知保全
- 生産のボトルネックを解消する
- 品質検査を自動化する
予知保全
予知保全により設備の故障リスクを最小限に抑えることができれば、生産ラインが停止するリスクを低減でき、結果的にサイクルタイムを短縮できます。近年、飛躍的に進化しているAI技術も予知保全に活用されており、故障リスクの低下に寄与しています。
基本的に予知保全には、赤外線サーモグラフィーやマイクなどのセンサを用います。例えば、赤外線サーモグラフィーで石油プラント内の温度を確認したり、音波で配管のつまりや機械の故障を予知したりします。
特に、工場内で一つしかない設備や機器がある場合は要注意です。替えがない設備の故障は生産ラインの停止を招くため、予知保全により故障リスクを最小限に抑える必要があります。
ボトルネック工程の解消
先述の通り、サイクルタイムはボトルネック工程にかかる時間と等しいという特徴を持っています。すなわち、生産のボトルネック工程を短くできれば、サイクルタイムも短縮できます。
ボトルネック工程の有効な解消方法は、TOC理論(Theory Of Constraints)です。TOC理論では、ボトルネック工程を集中的に改善することで、全体の最適化を図ります。すなわち、ボトルネック工程を改善してサイクルタイムを短縮することと同義です。
TOC理論の改善プロセス(5 Focusing Step)は、以下の5段階です。
- ボトルネック工程を見つける
- ボトルネック工程の最適化に注力する
- 他の工程の生産性をボトルネック工程に合わせる
- ボトルネック工程の能力を向上させる
- ボトルネック工程が解消できたら1つ目の段階に戻る
TOC理論を繰り返せば、ボトルネック工程を短縮し続けられるため、結果的にサイクルタイムも短縮します。
品質検査の自動化
センサなどを使って品質検査を自動化すれば、サイクルタイムを短縮できます。例えば、X線や超音波を利用すれば、異物検出が可能です。また、赤外線を用いれば、野菜や果物などの内部を破壊せずに検査できます。
近年では、AIを活用した品質検査も実用化され始めています。
リードタイムを短縮するための施策
サイクルタイムが短くなればリードタイムも短くなります。そのため、先述の品質検査の自動化や予知保全をすれば、リードタイムも短縮できます。しかし、サイクルタイムの短縮だけでは、生産リードタイムしか短縮できません。リードタイム全体を短縮するには「開発・調達・生産・納品」それぞれを改善する必要があります。
開発リードタイムの短縮施策としては、CAEの活用が考えられます。CAEとは、コンピューター上でシミュレーションを行う技術を指します。これを活用すれば、仮想空間で試作を素早く繰り返すことができるため、開発時間の大幅な短縮が可能です。
調達・納品リードタイムの短縮施策としては、SCM(サプライチェーンマネジメント)の実施や受発注システムの導入が挙げられます。モノやデータのやりとりを円滑にすることで、調達や納品にかかる時間を短縮できます。
とはいえ、リードタイム短縮のための有効な施策は、企業や工場によって異なります。自社のボトルネック工程がどこかを見つけ出し、地道な改善を図ることがリードタイム短縮の最適解といえるでしょう。
タクトタイムを計算すれば適切な製造体制を構築できる
タクトタイムとサイクルタイムの関係性を最適化することで、無駄な人員を割くことなく、適切な製造体制のもとで生産を進められます。特に、サイクルタイムとのバランスに気をつけることで、過剰な生産体制や労力不足を防げます。
ただし、厳しいタクトタイムに対応するには、サイクルタイムを短縮する必要があります。生産性を向上するためにも、AI・IoTなどの先端技術や、業務改善システムなどの導入を考えてみてはいかがでしょうか。
(提供:Koto Online)