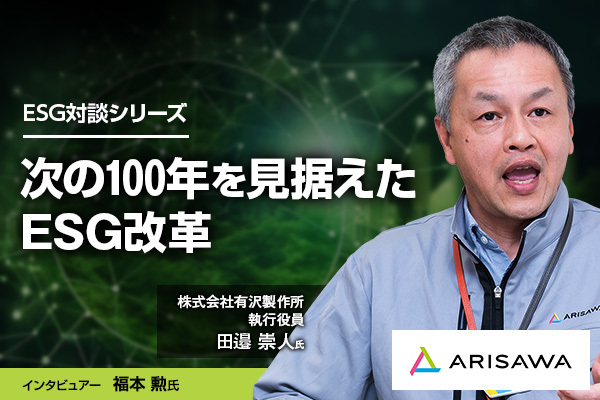
ESGやDXの最前線について、東芝 デジタルイノベーションテクノロジーセンター チーフエバンジェリストの福本勲氏が各企業にインタビューする本シリーズ。第11回となる今回は、新潟県上越市に本社を構える有沢製作所のESGやDXに関する取り組みを紹介します。
同社は電子材料や産業用構造材料、電気絶縁材料、ディスプレイ材料などの製造・販売を手がけるメーカーです。ESGやDXにも積極的に取り組んでいます。
今回は有沢製作所の執行役員で生産本部副本部長の田邉崇人氏をゲストにお招きし、同社の戦略について、福本氏とKoto Online編集長でコアコンセプト・テクノロジー(CCT)CTOの田口紀成氏がお話を伺いました。
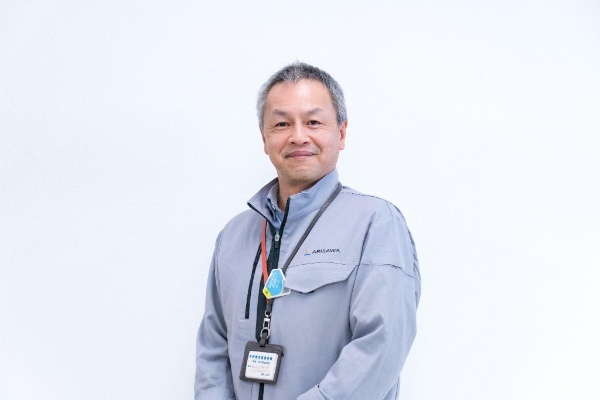
1996年、有沢製作所に入社後は光学材料分野の開発部署に配属。2015年からは電子材料分野の製造管理者を務める。
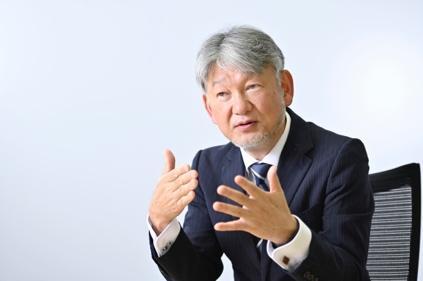
アルファコンパス代表
1990年3月、早稲田大学大学院修士課程(機械工学)修了。1990年に東芝に入社後、製造業向けSCM、ERP、CRMなどのソリューション事業立ち上げやマーケティングに携わり、現在はインダストリアルIoT、デジタル事業の企画・マーケティング・エバンジェリスト活動などを担うとともに、オウンドメディア「DiGiTAL CONVENTiON」の編集長を務める。また、企業のデジタル化(DX)の支援と推進を行う株式会社コアコンセプト・テクノロジーのアドバイザーも務めている。主な著書に「デジタル・プラットフォーム解体新書」、「デジタルファースト・ソサエティ」(いずれも共著)がある。主なWebコラム連載に、ビジネス+IT/SeizoTrendの「第4次産業革命のビジネス実務論」がある。その他Webコラムなどの執筆や講演など多数。
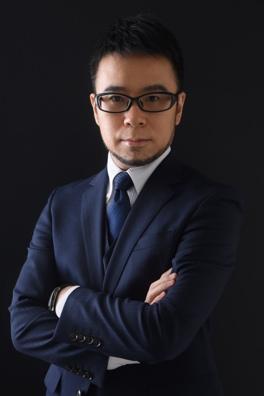
2002年、明治大学大学院理工学研究科修了後、株式会社インクス入社。自動車部品製造、金属加工業向けの3D CAD/CAMシステム、自律型エージェントシステムの開発などに従事。2009年にコアコンセプト・テクノロジーの設立メンバーとして参画し、3D CAD/CAM/CAEシステム開発、IoT/AIプラットフォーム「Orizuru(オリヅル)」の企画・開発などDXに関する幅広い開発業務を牽引。2014年より理化学研究所客員研究員を兼務し、有機ELデバイスの製造システムの開発及び金属加工のIoTを研究。2015年に取締役CTOに就任後はモノづくり系ITエンジニアとして先端システムの企画・開発に従事しながら、データでマーケティング&営業活動する組織・環境構築を推進。
目次
「織る」「塗る」「形づくる」のコア技術で事業を拡大
福本氏(以下、敬称略) 最初に、御社の事業概要ついてお聞かせください。
田邉氏(以下、敬称略) 弊社は1909年に創業し、来年に115周年を迎えます。かつて応接間のテーブルなどで使われていたレース模様のテーブルクロス「バテンレース」の製造が原点です。テープ状に編んだ糸を型紙に貼り縫っていく伝統工芸品として知られています。
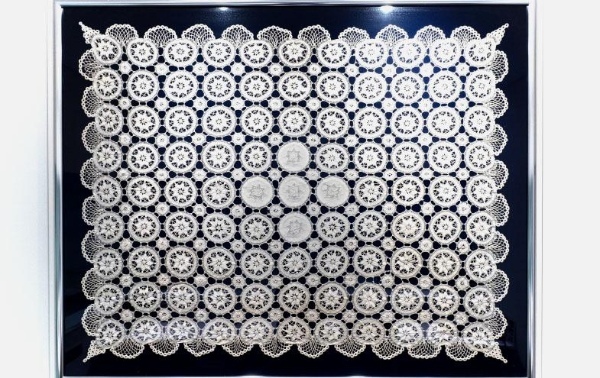
雪国である上越市では冬場の内職として発展しました。弊社は量産化を通じて「織る」「塗る」「形づくる」といったコア技術を磨き上げ、さまざまな分野へ製品展開しています。
福本 具体的に、どういった製品を扱っているのですか。
田邉 電子材料を筆頭に機能構造材料や光学材料の3分野を手がけています。モバイルや航空機、アミューズメント、エネルギー分野、近年はヘルスケア、半導体関係などで自社製品が使われています。「織る」「塗る」「形づくる」の技術があれば何でもできる自負があり、幅広く事業を行っている状況です。元々はニッチ分野を狙っていますが、ヒットするとグレートニッチに成長します。今では売り上げの約6割を電子材料関係が占めるようになりました。
福本 田邉様のご経歴をお聞かせください。
田邉 私は1996年に入社し、光学材料分野の開発部署に配属されました。2015年から5年間は電子材料分野の製造管理者を務め、以降は生産技術部で製品の量産化に必要な製造設備や工場建屋、インフラの整備に関わっています。加えて、カーボンニュートラルやIoT・DXを絡めたスマートファクトリーも担当しています。
福本 日本のものづくりは、一方通行型で物事を考えてきたと思います。対して、カーボンニュートラルやESGはサーキュラー型で考えないといけませんが、従来の業務と比べてギャップは感じますか。
田邉 生産技術部サイドでは改善活動が一番の仕事ですが、省エネ活動も重要です。2015年のパリ協定を機に世界が本気でカーボンニュートラルに動き出したので、弊社も一企業として何をすべきか考えました。ただ、環境対策が事業の足かせにならないか懸念していたのも事実です。
ところが、2020年に入ると状況は一気に加速し、主要顧客であるグローバル企業がRE100(✳︎1)について明言し始めます。その情報をいち早くキャッチした弊社は、サプライチェーンを巻き込んだグローバルな動きになると認識しました。
2016年には政府が2030年度に温室効果ガスを2013年度比46%減、2050年にはカーボンニュートラルを達成する目標を立てました。弊社もエンドユーザー様の意向に沿い、2030年度にCO₂の排出区分を示すScope1(*2)とScope2(*3)については、カーボンニュートラルを達成すると2021年に宣言しました。現在はロードマップを掲げて動いているところです。
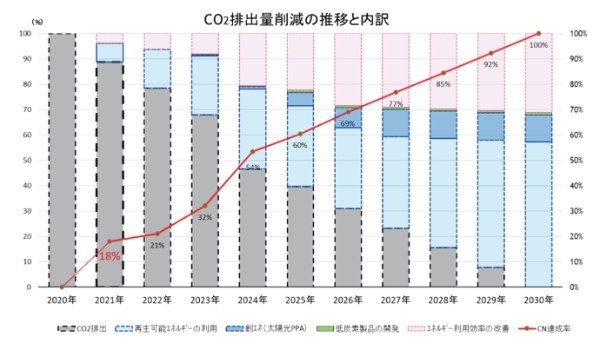
*2:事業者自らによる温室効果ガスの直接排出
*3:他社から供給された電気・熱・蒸気の使用に伴う間接排出
福本 グローバルサプライチェーンの中では、サプライヤーに対して2030年の期限を求めている企業もあり、それに対応されているのだと思います。御社は産業廃棄物のリサイクル率も約97%と高水準です。カーボンニュートラルのみならず、サーキュラーエコノミーも含めて先進的な取り組みをなさっていると理解しています。
田邉 産業廃棄物についてはおっしゃる通りですが、大半はサーマルリサイクルであるのは課題です。廃棄物の量を減らす、もしくは他のリサイクルを採用するなど、世の中の動きと照らし合わせながら次善策を考えないといけません。
リブランディングでは「人」を深く意識
田口氏(以下、敬称略) 私からも失礼いたします。御社は2023年4月にコーポレート・ロゴを一新しました。これは、ESGと何かしら関係があったのでしょうか。
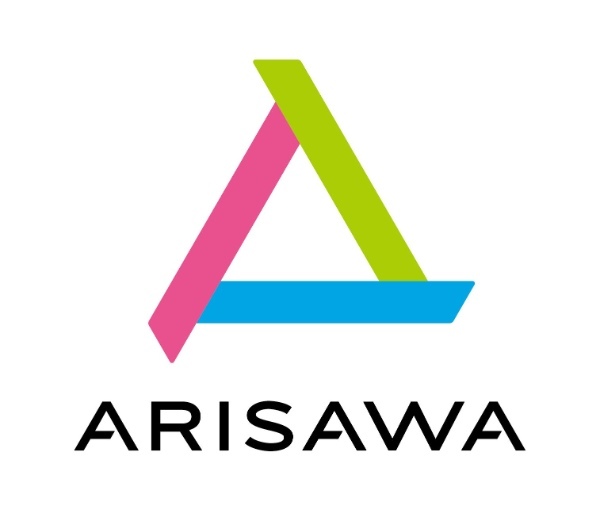
田邉 弊社は次の100年に向け、企業としての責任と誇りを胸に、よりしなやかに果敢に前進していきます。世界中のものづくりをより良く変える決意表明として、ロゴとコーポレート・メッセージを一新するリブランディングを実施しました。
私の感覚では、新しいロゴの意味合いとESGの共通点は「人」だと思います。次の100年を見据えた時に人や環境、人的資本への関わり方など、人を重要視した製造活動が求められるはずです。今回のロゴには、そういった思いが込められていると捉えています。
これからの100年は変化のスピードがさらに速く、生き延びるには人が変わらなければなりません。ロゴだけではなく、社員のマインドも変えようとの想いから、リブランディングを実施しました。ロゴを含めて目に見えるところを大きく変えたのは社員にとってインパクトがあり、お堅いイメージのある有沢製作所がポップな方向に舵を切ったと地域の方々も驚いています。
上越市は四季がはっきりした土地柄です。我々は、自然の変化や表情を感じながら生産活動を行い、100年間事業を継続してきました。だからこそ人が環境のこともよく考えないといけません。ESGにも積極的に取り組みたい意識が根強くあります。
福本 インナーブランディングが高まるので、地域内外に関係なく人への影響は大きく、ESGのG(ガバナンス)に関する効果も大きいのだと思います。
田邉 目まぐるしく世界情勢が変わる中、我々は100年の歴史で良いDNAを引き継ぎつつ、次の100年のパイオニアとなるべく新しい有沢製作所を築いていこうと一致団結しているところです。
田口 100年残ること自体が企業としてサステナブルであり、このタイミングでリブランディングをすることは、今後100年続く企業にとって必要なことだと思います。
2030年度までにScope1・2でカーボンニュートラル達成
福本 ESGのE(環境)に関する具体的な取り組みについて伺ってもよろしいでしょうか。
田邉 はい。全社的なESG委員会で、カーボンニュートラルや調達、廃棄物、人的資本など、さまざまな分科会を展開しています。私が担当するのはカーボンニュートラルプロジェクトで、先ほど申し上げた通り2030年度までにScope1・2を達成すると宣言しました。今年で3年目になりますが、Scope2はクレジットの活用を通じて目途はつき始めています。
その一方で、Scope1については困っています。弊社は金額ベースで電気とほぼ同等の都市ガスを使っているからです。電化する手もありますが、都市ガスくらいの高カロリーな熱を使わないと作ることができない製品がありまして、そこをどう解消するか悩んでいます。
ガスの利用については動きもあり、CO₂が発生しないとみなされるカーボンニュートラルガスをINPEX社(エネルギー関連企業)や行政からご提案いただき、2年前に県内初で導入しました。さらに燃料転換として、非化石燃料として認められているRPF(廃プラ固形燃料)の導入も検討中です。ガス会社や国の動向も見ていますが、LNG(液化天然ガス)の代わりにアンモニアや水素、合成メタンなどの活用も自治体と会話をしながら進めていこうと考えています。
田口 再生可能エネルギーの活用として太陽光発電は行いますか。
田邉 はい。我々は再生可能エネルギーを「創エネ」と呼んでいます。上越市は冬場に雪が降りますが、それを除く季節の日照時間は関東地方とあまり変わらないので、ピークカットに寄与します。今年中にオンサイトPPA(✳︎)の導入を始める方針です。
田口 どのくらいの発電量を目指していますか。
田邉 スモールスタートなので、発電量は全体の2%程度を考えています。大手事業者に相談したところすべて断られ、唯一手を挙げてくれた地元で実績のある事業者にお願いしました。蓄電や水素への変換なども考えていますが、イニシャルコストもかかりそうです。コストが下がった時に一気に進めたいと思います。
スマートファクトリーへの転換に挑戦
田口 エネルギー使用効率の改善は簡単でないと思いますが、IoTも活用されていますか。
田邉 IoTは電気とガス、蒸気に関するインプット・アウトプットの管理に活用しています。全社のエネルギーの利用状況をリアルタイムで監視し、運転の効率化に向けて分析にかけています。
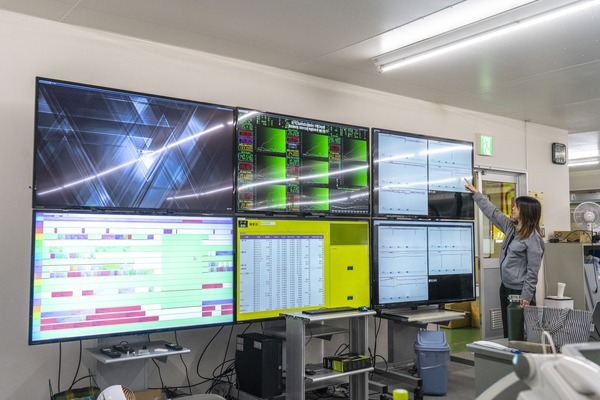
いわゆる、スマートファクトリー構築への取り組みです。製造現場では「余計な空調は止める」「高効率な設備に更新する」「間接部門でも就業時間を過ぎると空調を止める」「残業は大きなフロアでなく小さな会議室でする」といった地道な活動もしています。
福本 エネルギー転換をすると、コスト的な問題は生じないでしょうか。ロシアのウクライナ侵攻により、グローバルなLNG価格は欧州で10倍、日本でも2倍以上に上昇し、エネルギーのインフレリスクが顕在化しています。
田邉 今だけを考えると何かしらの策を打てるかもしれません。しかし、今後10~20年を見据えると、エネルギー価格の変化を予想しないと手が打てず、現状は使えるカードを増やしています。
福本 スマートファクトリーで、エネルギーの見える化以外の取り組みはありますか。
田邉 スマートファクトリー推進室を立ち上げたのは2020年のことです。当時は各メーカーで品質管理の不祥事が報道され、弊社でもお客様からの要求が厳しくなり始めました。今までも管理値を設けて品質管理していましたが、現在はリアルタイムトレンドまで見る必要があるので、工場の生産設備データを集約・分析する取り組みが始まり、品質・生産管理に役立てています。
福本 何か事が起きた時、速やかに手が打てるように対応されているわけですね。廃棄物の管理についてもお聞かせください。
田邉 弊社では、廃プラスチックや廃油、木くず、廃酸、ガラスくずなどの産業廃棄物が発生します。積極的なサーマルリサイクルにより、2021年度のリサイクル率は96.8%にのぼりました。
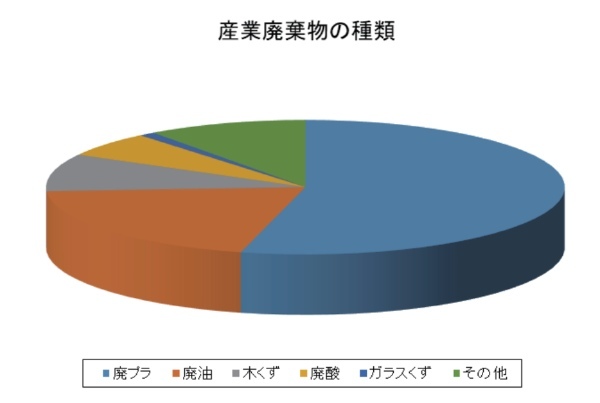
ただ、残り数%のハードルが高いです。コア技術と絡むフィラメントワインディングは、ガラスと有機化合物の樹脂が混ざっていて、現状では埋め立てしか処理方法がありません。ガラスと樹脂を切り分けてそれぞれをリサイクルすべく、いま研究を進めているところです。
福本 複合材はリサイクル難度が圧倒的に高いです。だからといってバージン材や単素材にするという簡単な話でもないのですね。
田邉 リサイクルしやすい材料へのシフトや、粉々に砕いてセメントに混ぜる処理方法なども検討しています。
福本 御社は「塗る」ことに関する事業もありますが、原材料の環境負荷への対応はどうなさっていますか。
田邉 フィルムなどにコーティングする時に使うレジンは有機溶剤で希釈します。VOC(揮発性有機化合物)処理装置を使い、法令に則る形で大気に放出する流れです。レジンそのものも有機溶剤を含むので、特別な産廃業者に廃棄をお願いしています。「量を作らない」「材料ロスを出さない」のも我々の使命です。
女性の採用比率・管理職比率が向上
福本 ESGのS(社会)やG(ガバナンス)への取り組みはいかがですか。
田邉 女性の活躍や管理職比率の向上は、直近で最も話題になっています。
田口 製造業は女性比率を上げるのが難しい業界であり、どの会社も同じ課題を抱えています。
田邉 弊社の近況では、新卒採用における女性比率が上がりました。弊社は開発業務を中心に理系の大卒・大学院卒が多いのですが、化学は女性が多いことも関係しているのでしょう。樹脂を扱うので汚い・臭いというイメージを持たれがちですが、作業環境もかなり改善されて今では女性が現場に入るようになっています。
人事部主導で女性管理職を目指すセミナーも開催したこともあり、実際に女性管理職が増えました。女性管理職の比率は、目標の2割に対して13%弱まで引き上げています。海外関連会社は、購買系がほぼ女性であることからすでに目標を達成しているところもあります。ソフト・ハードの両面から課題が多いのは、国内だと認識しています。
田口 私も海外法人のある東南アジアによく行きますが、多くの女性が働いているのを目の当たりにします。元々の環境があるので改善は難しい面もありますが、日本においては意識的に進めざるを得ないと思います。弊社はITなので女性比率が高いと思われがちですが、製造や建築に近く、同じ苦労をしています。
「15%カルチャー」で新事業を創出
田邉 「15%カルチャー」も非常に大事な活動文化です。研究開発の社員は勤務時間の15%を自分の好きな研究に充てられます。組織の垣根を取り払い、ワーキンググループも作りました。成果がアイデアという形で出始め、先日の発表会で「有機溶剤を水系に変えられないか」など8件ほどのテーマが上がり、どれも興味を誘う内容でした。
田口 有機溶剤に関しては私もかつて研究していました。生産性の観点で難しいことを理解していますが、そういった取り組みをしているのは心強いですね。
田邉 釣り好きの社員は、市販の釣り竿では満足できず、フルカーボン製を自作しました。昔からスポーツ・レジャー系の材料も扱っていて、卓球で使うラケットの材料も好評です。農学部出身の研究者は、水や養分を与えなくても光だけで育つインビトロフラワーを開発・販売したこともあります。材料・設備は会社持ちなので、3Dプリンタを購入してもらった若手社員は、いつの間にかCADの達人になっていました。
狙っていたのと違う効果もあり、楽しんでいる若手開発者は多いようです。上司は横から口を出さないのが決まりで、各自の研究を優しく見守っています。やりたいことができる環境が功を奏しているのでしょう。
田口 新事業が生まれる期待もあるのでしょうか。
田邉 もちろんです。イノベーションを起こして、事業・会社に貢献できる製品ができればと思います。利益に対して新製品開発賞を授与したり、事業化したりすることもあります。2年前からは環境価値のある開発も表彰対象とされ、同分野の開発・取り組みが評価されるようになりました。
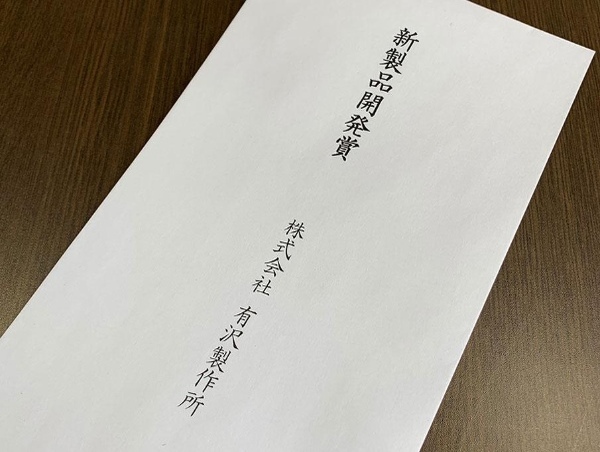
直近では、生産効率を上げたり熱を下げたりする条件変更関連の開発も始まり、エネルギーコスト削減に寄与させたい考えです。将来の目玉としては、先ほどお伝えした水系の何かが出てきてほしいと思います。
田口 若い方たちは環境や働く目的を重視するので、15%カルチャーはフィットする仕組みだと思います。
田邉 ここ4~5年で入社した若手社員はうまく利用しています。気分転換になるだけでなく、大学院時代の研究を15%カルチャーに充てる人もいます。論文も書きますし、権利化できるようなら特許も自ら取得しています。特許に関しては拒絶されても報奨金が出る仕組みで、積極的に取り組むよう勧めています。
田口 良い人材が集まる素晴らしい仕組みですね。
改善とインセンティブはセットで考える
福本 ESGの取り組みをどのように周知していますか。
田邉 次に目標を掲げないといけないのは、Scope3(*3)の部分です。サプライヤーの皆さまに理解して実行していただく必要があります。そのために、資材部がメインとなるESG委員会の調達分科会が、ヒアリングを実施して賛同を求めています。
カーボンニュートラルに関するお願いもしていますが、弊社のサプライヤー様は大手がほとんどなので、自ら進めていることが多いようです。スタートアップやベンチャー系の材料メーカーから購入する際は少し気を遣わないといけません。
福本 それは具体的にカーボンフットプリント(CFP)の価値を含めて一緒に提供してほしいということですね。
田邉 「将来的にカーボンフットプリントにしてもらわないと困る」とおっしゃるユーザー様もいるほどです。私たちも冗談めかして、「製品にゼロカロリーと書けたら良い」と話しています。
福本 そういったことに対して社内外からの反応はありましたか。
田邉 スタート時点で社内では「環境活動は利益を生み出すのか?」という意見も出ましたが、努力をすればインセンティブを与えるようルール化して理解を得ました。前向きに取り組むと評価されるという認識が浸透しています。
社外に関して、大企業はすでに取り組み、我々より進んでいる会社もあるので安心しています。中小企業への働きかけやフォロー体制については今後の課題です。Scope3のうち物流に関しては、EV(電気自動車)やFCV(燃料電池車)などに替えるのかなど、関連会社に働きかけながら進める方針です。
田口 物流を担うのがグループ会社ならコントロールできそうですね。
田邉 オンサイトPPAがうまくいけば、蓄積した電気や水素でフォークリフトやトラックに充電できます。
田口 サーキュラーエコノミーまで行くかはともかく、コントロール可能な範囲では実行できると感じました。カーボンニュートラルの目標達成も現実味を帯びているようですね。
田邉 現状の取り組みだけでは、2030年の目標達成は厳しいと思います。取り組みをより加速させないといけません。
DXはデータの収集・可視化から始める
福本 今後ESGやDXを加速させる上での課題や展望をお聞かせください。
田邉 DXに関しては色々なツールを試し、フィットするものを大きく取り入れたいと考えています。生産工場なら設備のセンシングやスキャナーは、すでに試しています。今後はさらに上層と連携させたく、今は主力事業の電子材料系の工場で経営層のシステムを更新しているところです。
福本 最後に、Koto Onlineの読者に向けて、今後の意気込みやメッセージをお願いします。
田邉 経営層はDXやAI、IoTを進めなさいと言いますが、具体的な実践は意外と難しいのではないでしょうか。工場や現場にデータが散らばっているので、まずはそれらを集約して見える化することが基本です。データを可視化するとデジタルに詳しくない人でも解決手法を思い浮かべられるので、DXのスタートはデータ収集と見える化だと実感しています。
弊社でも主力工場の電気の利用状況を完全に見える化することで、現場はデータを見ながら動くようになり、今年の猛暑を乗り切ることができました。指示なしで動けるようになったのは大きな成果です。今後は本業である製造に関しても生産の効率化や品質の安定化に寄与することに期待しています。
田口 御社の場合、インセンティブの機能がセットになっている気がします。データの見える化とともに、社員が自ら評価される取り組みについて考える機会が生まれたのが成果の要因なのでしょうか。
田邉 おっしゃる通りです。改善案を上げて評価されると報奨金が出るので、各現場も積極的になったと思います。
田口 データの見える化をしてもうまくいかないという方たちにとって、御社の取り組みは現実感のあるソリューションです。
田邉 施策の目的を理解してもらった上でインセンティブを与えると、積極的に社員自ら取り組むようになりました。
福本 環境問題は地球のためでもありますが、企業からすると戦略的にエネルギーコストを削減する手段となります。その分を社員に還元するとモチベーションにつながるでしょう。本日は有益なお話をたくさんしていただきました。ありがとうございます。
【関連リンク】
株式会社有沢製作所 https://www.arisawa.co.jp/
株式会社東芝 https://www.global.toshiba/
株式会社コアコンセプト・テクノロジー https://www.cct-inc.co.jp/
(提供:Koto Online)