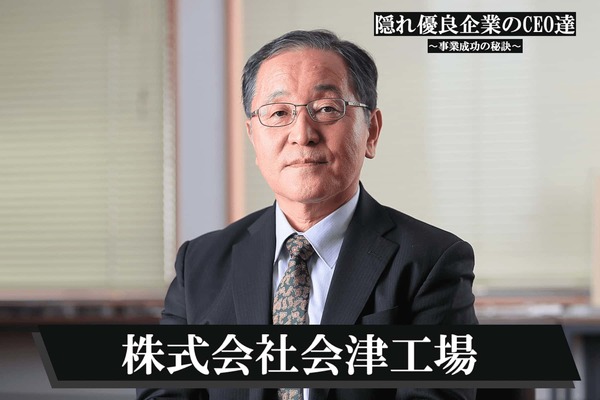
また、遠藤工業有限会社の代表取締役、ナイガイキャスティングス株式会社の取締役副社長、株式会社季の郷湯ら里の代表取締役を務めるほか、会津産業ネットワークフォーラムの副代表として地域産業の発展に寄与している。
これまでの事業変遷
—— 事業の変遷についてお聞かせいただければと思います。
株式会社会津工業 代表取締役・鈴木直記氏(以下社名、氏名略) 弊社は1975年に千葉で設立されました。内外マリアブルという鋳造メーカーの会津工場として創業しました。その後、1977年に独立分社化し、社名が株式会社会津工場となりました。事業内容としては、主に自動車関係の部品を生産する鋳物屋です。
新しい技術の開発にも力を入れており、1983年からHプロセスという工法の開発を始めました。これにより、新しい価値を持つ鋳物を作り上げ、事業を続けています。現在、会津工場は独立して48期目を迎え、社員数は鋳造工場で約160名、子会社を含めると約200名です。
—— 内外マリアブルさんの関連会社としての位置付けはどうなっていますか?
鈴木 当初は内外マリアブルのオーナーが会津工場の株式を持っていましたが、現在は私が株式の約70%を取得し、実質的に経営を行っています。もともとのオーナーは亡くなり、その家族が一部の株を保有していますが、経営は私が握っています。
—— 鋳物業界の収益性についてはいかがですか?
鈴木 鋳物業界全体で見ると、1980年頃がピークで、当時は日本国内に約3000社の事業所がありました。しかし、現在は約600社にまで減少しています。国内の鋳物生産量は減少していますが、グローバルでは増加しています。特にインドや中国などの新興国で自動車の保有台数が増えているため、鋳物の生産トン数も増加しています。ただ、インドと中国が主たる生産国として突出していますね。
自社事業の強みやケイパビリティ
—— 続いて、御社の事業の強みや競争力について教えていただけますか?
鈴木 弊社の一番の強みは、Hプロセス工法という技術にあります。高精度の鋳物を比較的安価に製造できる点が特徴です。鋳物は通常、寸法に1ミリから2ミリのばらつきがあるのが常識ですし、薄い鋳物を作るのも難しく、一般的には5ミリから6ミリが限界とされています。しかし、弊社では寸法のばらつきを0.1ミリから0.2ミリに抑え、肉厚も2ミリ程度まで薄くすることが可能です。これを実現するのがHプロセス工法です。
一般的な鋳物は大まかな形を作り、そこから切削加工で精度を出します。特に自動車部品では高品質と高精度が求められますので、削って加工するのが普通です。しかし、弊社の技術では高い寸法精度と薄肉を実現することで、切削加工を減らし、軽量化を提案することができます。これが私たちの最大の強みです。
—— 自動車関係に特化しているわけではないのですか?
鈴木 そうですね。特に自動車に特化して営業しているわけではありませんが、弊社の技術が自動車部品に最もマッチしていると考えています。月に数万個といった量産も可能ですので、自動車関係に最適な技術だと思います。
これまでぶつかってきた課題や変革秘話
—— これまでに直面した課題をどう乗り越えたかお話しいただけますか?
鈴木 Hプロセス工法は私たちが考案したものではなく、もともとは1982年頃にイギリスのWHブースという会社が考案した技術です。当時の社長がこの技術に将来性を感じ、イギリスから技術を導入しました。特許を取得し、日本国内に持ち込んだのが始まりです。しかし、当初は技術が確立されておらず、非常に難しいものでした。製品の80%が不良品で、技術的にも新しく、教えてくれる人もいませんでした。
その状況で、私は入社3年目の20代でしたが、数名のメンバーとともに立ち上げるよう指示されました。作っても作っても不良ばかりで、正直商売として成り立たないのではと思っていました。しかし、当時の社長はこの技術を諦めることを許してくれませんでした。進捗状況を確認しに来るたびに、何も進んでいないと怒られました。
技術的に行き詰まり、金型から自社で作らなければ成り立たないと提案しました。すると社長も乗り気になり、設備や予算の立案を指示されました。総額2億円ほどの見積もりを出し、さすがに諦めるだろうと思ったのですが、社長は「お金は俺がなんとかするから計画を進めよう」と言われ、逃げられなくなりました。それで金型工場ができたのが1986年です。
金型を自社で作ることで、設計、制作、テスト、改造を繰り返し、PDCAサイクルを回すことができました。1990年頃には商売として成り立つ品質を確立し、Hプロセス工法を主な技術として展開することができました。
—— Hプロセス工法が商売として成り立つまでにどのくらいの時間がかかりましたか?
鈴木 結局、7年ほどかかりました。ただ、その間も一般的な鋳物を生産し、かろうじて商売を続けていました。1990年頃に一般的な鋳物のラインを撤去し、Hプロセス工法専用の工場にリニューアルしました。
—— その間、業績的にはどうだったのでしょうか?
鈴木 業績的には大変でしたが、オーナーが同じ内外マリアブルが助けてくれたので、赤字分を補填してもらいながら進めました。大変な時期でしたが、それがあったからこそ今があるのだと思います。
今後の事業展開や投資領域
—— 今後の事業展開について、どのような方向性で進めていくのか教えていただけますか。
鈴木 現在、会津を拠点に事業を展開しておりまして、会津地区には鋳物の生産拠点が2か所、切削加工の工場が1か所、計3拠点で生産を行っています。社員数も増え、現在は200人ほどになりました。これまでの努力が実を結び、各事業が拡大しています。自動車メーカーであるトヨタ、日産、ホンダからも我々のHプロセス工法が高く評価され、認知され始めています。この技術を鋳物作りのグローバルスタンダードにまで高めたいと考えています。
現在、インドでの生産を計画しており、コロナの影響で一時的に足止めされましたが、インド市場の可能性を探るために現地の鋳物屋や自動車部品メーカーを訪問しています。インドでこの技術を提供できれば、大きな市場が開けると期待しています。
—— インド市場への進出にはどのような課題がありますか。
鈴木 インド市場に進出するには時間と資金が必要です。また、現地の風土や文化、常識が日本とは異なるため、簡単にはいかないと感じています。インドを訪れるたびに、現地の食事で体調を崩すこともありますが、これも現地の人々との交流の一環と捉えています。
—— 日本の自動車部品業界は海外でも強いと聞きますが、どのようにお考えですか?
鈴木 日本の自動車部品は、特にアジア市場で強みを発揮できると考えています。伝統的な技術や日本人の緻密な作業が生かせる場面が多いです。
—— 若いメンバーの活躍にも期待しているとのことですが、具体的にはどのような取り組みをされていますか?
鈴木 昨年、役員を一新し、私以外の取締役を全員30代~40代にしました。彼らが次の世代を担い、インド市場をはじめとする国際市場に飛び出していくことを期待しています。息子もその中にいますが、次期社長を決めるのはまだ先の話です。若い役員たちがタッグを組んで事業を展開していくことを願っています。
メディアユーザーへ一言
—— 最後に、我々のメディアの読者の皆さんに向けて、一言お願いできますか?
鈴木 このメディアをご覧になっているのは、きっと投資家や経営者の方々が多いと思います。そうした皆様に何かを申し上げるのは恐縮ですが、私自身の経験からお伝えしたいことがあります。
若いメンバーにはいつも「失敗は成功の元」だと話しています。ただ、私はそれをさらに前向きに捉えています。チャレンジすれば、結果は成功か失敗のどちらかですが、たとえ失敗しても“失敗という結果を出すことには成功している”。つまり、挑戦すればすべてが成功なんです。何もやらないことこそが、唯一の“失敗”だと考えています。
私自身も若い頃、当時の社長から厳しいプレッシャーを受けながら成長してきました。その経験があるからこそ、今の自分があると感じています。社員にも常に「まずは挑戦してみよう」と伝えています。失敗してもいい、それをしっかり分析して次に活かせばいいんです。大谷選手だって打率3割。それくらいの感覚で十分なんです。
10回挑戦して1〜2回成功すれば、それは大きな成果です。そんな前向きなマインドで、これからも事業を進めていきたいと考えています。
- 氏名
- 鈴木 直記(すずき なおき)
- 社名
- 株式会社会津工場
- 役職
- 代表取締役