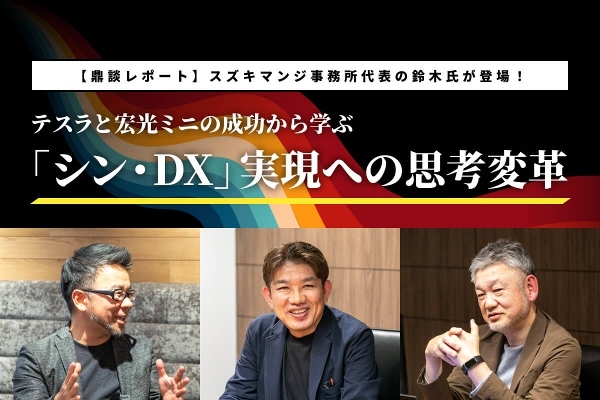
欧州では、ドイツを中心にデータ基盤構築の動きが進んでいます。グローバルに広がるサプライチェーンを持つ日本企業も、将来的にはこの種の取り組みに関与する必要があると考えられます。ただ、要素技術開発主導で産業・事業を考えると言われてきた日本企業にとっては、この新しい取り組みに積極的に関与していくことが難しいと感じるかもしれません。しかし、企業活動をより効率的に行い、顧客の体験価値を高めるためには、この変化への適応が必須です。では、具体的にどういったアプローチが必要なのでしょうか。
今回は「次世代自動車における価値づくりのあり方」をテーマに、コアコンセプト・テクノロジー(CCT)CTOの田口紀成氏と、CCTのアドバイザーで東芝 デジタルイノベーションテクノロジーセンターのチーフエバンジェリストである福本勲氏が、スズキマンジ事務所代表でデンソー技術企画部キャリアエキスパートの鈴木万治氏を迎え、2023年6月21日にウェビナーを開催したものについて、その内容を再構成したダイジェストをお届けします。
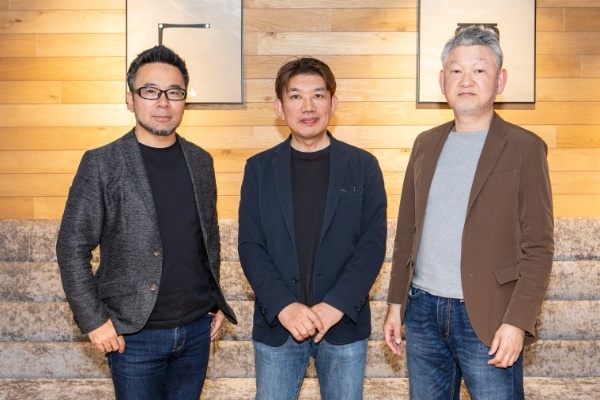
株式会社デンソー 技術企画部 キャリアエキスパート
1986年(昭和61年)名大院工修了、日本電装(現デンソー)入社。宇宙機器開発やモデルベース開発など全社プロジェクトを担当。2017年から20年まで米シリコンバレーに駐在し、18年からは中国子会社のイノベーション部門トップも兼務。数週間ごとに米中を行き来する生活を送った。21年にスズキマンジ事務所(manji@manji3.com)を開業。
*本対談において、鈴木氏は個人の経験・見解からお話いただく形となります。所属する会社・組織とは関係するものではございません。
アルファコンパス代表
1990年3月、早稲田大学大学院修士課程(機械工学)修了。1990年に東芝に入社後、製造業向けSCM、ERP、CRMなどのソリューション事業立ち上げやマーケティングに携わり、現在はインダストリアルIoT、デジタル事業の企画・マーケティング・エバンジェリスト活動などを担うとともに、オウンドメディア「DiGiTAL CONVENTiON」の編集長を務める。また、企業のデジタル化(DX)の支援と推進を行う株式会社コアコンセプト・テクノロジーのアドバイザーも務めている。主な著書に「デジタル・プラットフォーム解体新書」「デジタルファースト・ソサエティ」(いずれも共著)がある。主なWebコラム連載に、ビジネス+IT/SeizoTrendの「第4次産業革命のビジネス実務論」がある。その他Webコラムなどの執筆や講演など多数。
2002年、明治大学大学院 理工学研究科修了後、株式会社インクス入社。2009年にコアコンセプト・テクノロジーの設立メンバーとして参画し、3D CAD/CAM/CAEシステム開発、IoT/AIプラットフォーム「Orizuru」の企画・開発などDXに関する幅広い開発業務を牽引。2015年に取締役CTOに就任後は、ものづくり系ITエンジニアとして先端システムの企画/開発に従事しながら、データでマーケティング&営業活動する組織/環境構築を推進。
目次
「Gaia-X」を基盤に「Catena-X」が発足 ヨーロッパの自動車産業で進むデジタル化
田口氏(以下、敬称略) 今回は、次世代自動車における価値づくりのあり方について、鈴木万治さんをお招きして福本勲さんと共にお話しを伺ってまいります。まず、現在の自動車業界で起こっている世界的なトレンドについてお聞きしてみたいと思います。福本さんは4月に開催された「ハノーバーメッセ2023」を訪問されたそうですが、そこで見つけた注目すべきドイツの動向について教えていただけますか。
福本氏(以下、敬称略) 欧州では、「Gaia-X」という統合データ基盤プロジェクトが2020年6月に発足しました。ドイツが主導し、フランスと共に準備が進められてきたこのプロジェクトの目的は、欧州域内外のさまざまな企業のクラウドサービスを単一のシステム上で統合し、業界をまたがるデータ交換を容易に行える標準的な認証の仕組みを通じて、インターオペラビリティ(相互運用性)を実現することにある、とされます。
BMWグループとメルセデス・ベンツは、自動車業界において安全な企業間データ交換を目指すためのアライアンス、「Catena-X Automotive Network(以下、Catena-X)」を2021年3月に設立しました。Catena-XはGaia-X上のユースケースであり、ドイツの自動車メーカーだけでなく、他の関連企業も参加可能な実践志向のネットワークです。参加企業・団体の中には、自動車関連メーカー以外にプラットフォームとアプリケーションのベンダーも目立ち、SAPなどのドイツ勢やマイクロソフトなどの米国勢も含まれています。また、ドイツでは日本と同じように中小企業(SME)の割合が95%以上を占めているという背景から、SMEの積極的な参画が重要であるとの考えに基づき、SME向けのソリューションを備えたオープンネットワークが構想されています。
Catena-Xが目指すのは、自動車産業のサプライチェーンとエンジニアリングチェーンにおいて拡張性の高いエコシステムを作り、オープンかつ中立的な環境を確保しつつ、標準化されたデータにアクセスできるようにすることです。バリューチェーン全体の効率化と最適化を図ると同時に、従来は自動車の製造に関わってこなかった企業や業界との連携なども進めていくことを視野に入れています。
ハノーバーメッセ2023では、BASF、ヘンケル、メルセデス・ベンツ、SAP、シェフラー、SIEMENS、T-Systems、フォルクスワーゲン、ZFの10社が、Catena-Xのユースケースの運用や採用を目的に、Cofinity-Xを設立したことを発表しました。Cofinity-Xは、まず欧州市場を対象に、エコシステムの全参加者間での効率的かつセキュアなデータ交換を可能にする製品・サービスの供給を目指し、2023年9月に正式に市場投入していくとのことです。
田口 これまでとの違いは何でしょうか。
福本 Catena-Xではベースとなるオープンソース(OSS)の基盤が間もなくリリースされます。これにより、さまざまなプレイヤーがアプリケーションを構築・提供することが可能になるため、そのためのマーケットプレイスの具体的な運用を行う役割を担うのだと思います。
田口 現実に即した、利用の観点で実装が先に進められるということですね。
福本 また、Manufacturing-Xというイニシアチブも立ち上がっています。自動車業界には先ほどお話ししたCatena-Xがありますが、Manufacturing-Xは自動車を含む製造業全体を対象としています。Catena-XをBluePrint(土台)としつつも、製造業のセクター横断で進めていくイニシアチブという位置付けです。欧州ではデジタルプロダクトパスポート(DPP:Digital Product Passport)(*)の取り組みも進み始めており、Manufacturing-Xがその推進を主導していくとのことでした。
自動車産業の観点ではおそらく、Catena-Xに準拠していくことがManufacturing-Xに対応することにつながると思います。自動車以外の製造業においては、同じような形でGaia-X、Catena-Xの標準に準拠し、データ基盤を活用していくことになるのではないでしょうか。
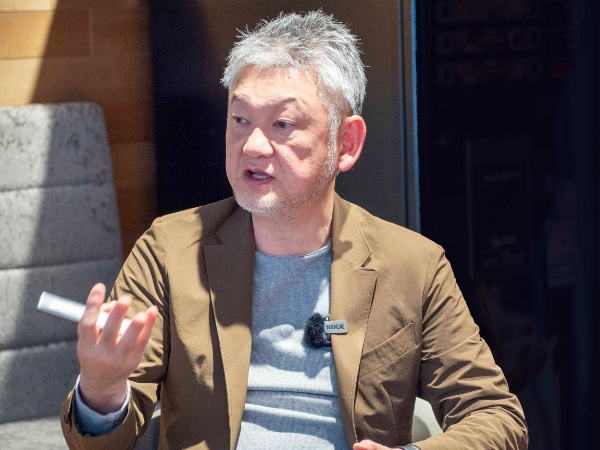
欧州で進むデジタルプロダクトパスポート法制化の動き
田口 これからさまざまな実装が具体的に見えてくるということでしょうか。
福本 おっしゃる通りです。特に注目されているのが、先ほどお話ししたDPPの取り組みです。DPPは、欧州委員会がEU全域にサーキュラーエコノミーを加速させるための計画「サーキュラーエコノミーアクションプラン(循環型経済行動計画)」の要として、2022年3月に「持続可能な製品イニシアチブ(SPI: Sustainable Products Initiative)」の一環として提案され、導入が促進されているものです。
通常、パスポートと言えば、個人の属性や国境を越えた移動の履歴などを書き込む公的な証明書を思い浮かべますが、DPPはプロダクトにパスポートが適用される初のケースとなります。
初めてDPPが適用される製品としては、EVのリチウムイオン電池が挙げられ、電池規則はすでに法制化が進められています。この規則のもとで、EVのリチウムイオン電池が管理されることになります。その際、自動車に使用された後に他の目的でリユース可能な場合は、リサイクルよりも優先してリユースすることが法的に要求されます。
田口 なるほど。国の境界を越えると同様に、企業の枠を越えて情報を適切に伝えるというイメージなのですね。
福本 まさにその通りです。法制化が進むDPPなど、トレーサビリティ情報のデジタル化が求められる中で、設計情報もデジタル化を進めることが必要になると考えています。EVのリチウムイオン電池が最初の対象となるため、自動車産業がまず影響を受けることになります。日本企業にとって、関係のない遠い国の取り組みではなくなってきています。
鈴木氏(以下、敬称略) 実は自動車業界はこれまでも欧州市場を狙って仕事をする場合は、欧州の標準のフレームワークなどに対応していました。ただ、今の話を伺っていて大きな変化だと思ったのは、従来は各企業が個別に対応していたのに対し、今回のプラットフォームは企業間での情報共有を必要としているという点です。そう考えると、巨大なサプライチェーンを持つ自動車業界にとっては大きなチャレンジになるでしょう。
欧州のように競争領域と非競争領域の定義が参画企業間で、きちんと共有されている場合は、非競争領域に関しては皆が一丸となります。極端なことを言えば、ライバル同士でも協力します。日本の場合、競争領域と非競争領域の境界線とそれに対する意識が曖昧ではないかと感じています。福本さんのお話を伺って、「自動車業界もこれまでとは違う取り組みが必要になる」と感じました。
福本 標準が決まってから対応しようとすると、その標準に準拠したソリューションを利用しなければならなくなり、投資が必要です。企業から見るとコストになってしまいます。
鈴木 その通りだと思います。ルール作りに参画しないと自分たちに不利なものができてしまうので、決める前の段階できちんと標準化のコミュニティにジョインし、発言力を持つことが自動車業界には求められるでしょう。
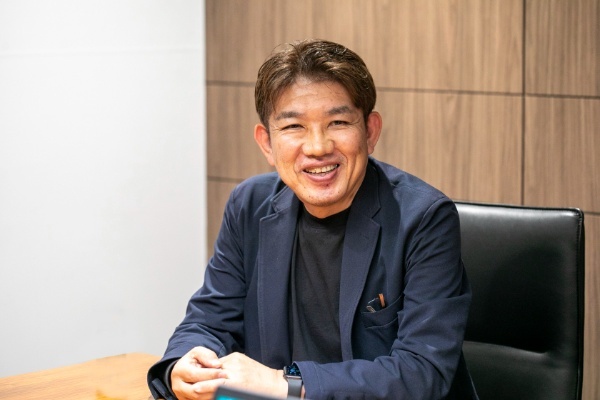
DXは手段、目的は価値創生である カイゼンの達人ほどDXが苦手?
田口 多くの制約があるとはいえ、ものづくりの本質は「どのように価値を作っていくか」という点かと思います。DXなどについて数多く講演されている鈴木さんのご見解をお聞かせください。
鈴木 価値作りは全てのビジネスの根幹です。お客さまから対価をいただくためには、お客様に価値を提供しなければなりません。近年、自動車業界では「CASE(Connected、Autonomous、Shared&Service、Electrification)」の推進が叫ばれていますが、本日ここで議論したいのは、「果たしてCASEは自動車業界のDXなのか?」ということです。DXはあくまで手段であり、目的は「価値創生」ですよね。この点について詳しくお話ししたいと思います。
まず、日本の製造業といえば、多くの人の頭に浮かぶのはやはりカイゼンでしょう。ただ、カイゼンの達人になればなるほどDXの取り組みが難しく感じる、という意見もよく耳にします。なぜかというと、カイゼンは複雑で大きな問題を分割し、それらを個別に緻密な計画に基づいて継続的に改善するという方法をとります。現状を漸進的に改善する上では非常に効果的ですが、反面、一時的なマイナスや失敗を許容することが難しく、部分的な改善を積み重ねても全体的な改善にはつながらない、という側面もありますよね。
福本 確かに、要素技術の開発を一つ一つ積み上げても、アーキテクチャはできませんからね。
鈴木 その通りです。また、現場では計画の完璧さを追求するあまり、「PDCA」ではなくて「PPP…」のように、計画(Plan)が繰り返されてしまうこともよく見られます。しかし、最近は変化の速度がどんどん速くなっているため、計画に時間をかけすぎると前提が大きく変化してしまうリスクが高まります。そこで、小さなPDCAサイクルを高速で回すことをおすすめします。
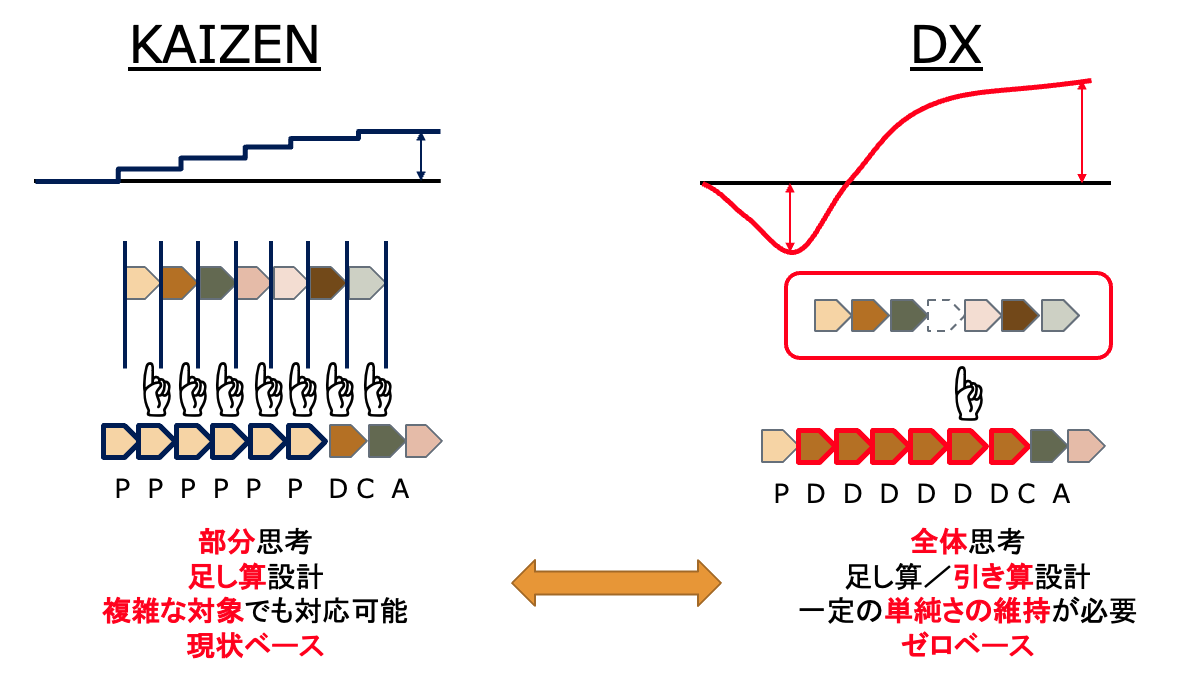
この図は、カイゼンとDXの違いを僕なりに簡単にまとめたものです。あくまでも、僕のイメージです。このような図を示すと、多くの方が「どちらが優れているのか、正しいのか」と問いかけてきます。ただ、私が強調したいのは、「どちらが優れているのか、正しいのか」ではなく、「それぞれ違います」ということです。
カイゼンがよい場合もあるし、DXがよい場合もあります。ただし、この図に示すように、部分思考と全体思考、足し算の設計と引き算の設計といった違いがあり、それらを上手に使い分け、組み合わせることが重要なのです。
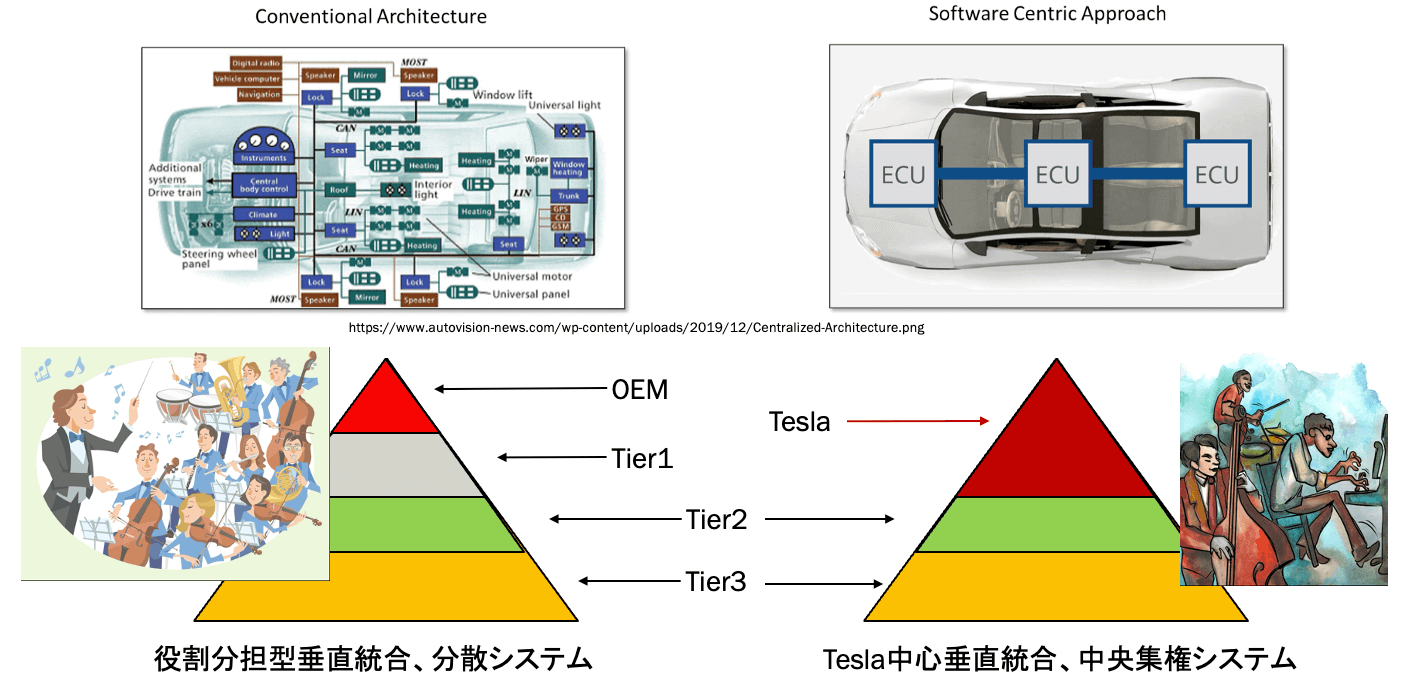
次に、自動車の電気電子システムのアーキテクチャを例に説明します。この図は「カイゼン的アプローチとDX的アプローチ、そしてそこから生まれる製品」を表現したものです。左側は伝統的な車のアーキテクチャで、大小さまざまなコンピューターが数十から100個ほど搭載されています。対照的に、右側のテスラは大きなコンピューターがわずか3つほどしか搭載されていません。
ここで、分かりやすくするために喩えを用います。左側のアーキテクチャは60人の団員がいるオーケストラだと思ってみてください。たくさんの団員がいるので、作曲家がどんなに良い曲を作っても、指揮者がいないと全体としてうまく演奏できません。その指揮者の役割を果たすのが、Tier1サプライヤーです。Tier1の人が、各演奏者(Tier2以降のサプライヤー)をうまく指揮することで全体をまとめています。
一方、テスラはどうでしょうか。テスラはシンプルなアーキテクチャなのでTier1を必要とせず、全て自社で手がけています。左側のオーケストラに対して、こちらはジャズトリオですね。私はジャズが大好きで、ジャズライブを聴きに行かれている方ならお分かりになると思うのですが、ジャズトリオは演奏しながら「次、あなたね」みたいにお互いに目配せをして、アドリブをどんどん回します。このような演奏がまさにテスラのスタイルなのです。
ここでも再度強調したいのは、これらは「どちらが優れているか」ではなく、オーケストラもジャズトリオも、どちらも素晴らしいということです。左側はとても複雑なものを管理できる良さがあり、一方、右側はとてもフレキシブルにいろいろなものに対応できる良さがあります。このそれぞれの特徴が、カイゼンとDXの性質につながると考えます。
テスラに対しては、「イメージ先行では?」「企業価値は高いが実力はどうなの?」などと、さまざまな印象を持つ方がいることでしょう。しかし、近年のテスラの成功は、(イメージではなく)ものづくりにおいてもすごいということを少しだけお話しします。
テスラは他の自動車メーカーと比べ、ダントツに高い収益率を実現しています。その理由は非常にシンプルなのです。「安く作って高く売る」ということです。「高く売る」は、イーロン・マスクとテスラのブランド力があれば比較的容易に達成できます。「安く作る」という部分については、イーロン・マスクがツイートすると、下手な広告より宣伝効果があるため、宣伝費用がほとんど必要ないということもありますが、それ以上に、「安く」作るというテスラのものづくりがすごいのです。
テスラと「45万円EV」に見る、「シン・DX」のヒント
鈴木 イーロン・マスク自身がツアーコンダクターとなり、スペースXを案内しているYouTube動画があります。その様子を、「イーロン・マスクのロケット製造5つのステップがサイコーだった」という記事にまとめた方がおられ、その方の許可のもと引用します。ものづくりのDXに取り組む方にとって、これ、むちゃくちゃ重要だと思います。
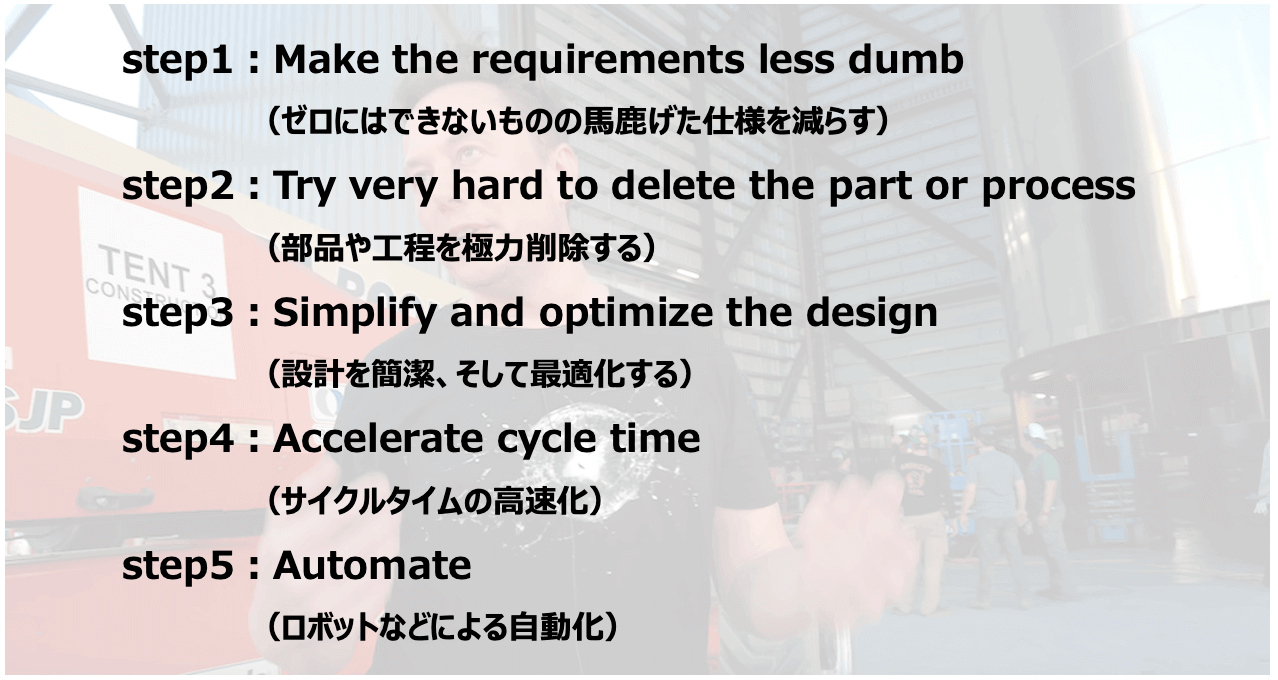
ステップ1は、「ゼロにはできないものの馬鹿げた仕様を減らす」。要は、仕様を可能な限りシンプルにするということです。製品全体の品質は、その源流である仕様の断捨離ぶりに左右されますから。
田口 確かに、カイゼンの延長にはなさそうです。
鈴木 ステップ2は、「部品や工程を極力削減する」。ここでも、大胆な断捨離です。そして、まだまだDXでよく耳にする自動化には行きません。ステップ3に「設計を簡潔、そして最適化する」。ここまでとても重要です、そしてようやく、ここから先が皆さんにとてもなじみ深いものになります。ステップ4の「サイクルタイムの高速化」です。
田口 カイゼンですね。
鈴木 ステップ5は「ロボットなどによる自動化」です。ステップ4と5は、DXに取り組んでいる方々にはなじみ深い工程でしょう。
福本 従来の日本の製造業では、「このモノはどうやって作るのか」といったことがその検討の中心であったような気がしています。こういった発想だけでは、イーロン・マスクのステップ1〜3のような発想はなかなか湧いてこないのかもしれません。価値とは、顧客から見た経験価値ですよね。イーロン・マスクの発想は恐らく、「顧客が車を購入した後も仕様や性能などが顧客の利用環境や利用方法に応じて最適化されることで、顧客の経験価値が高まる」ということなのでしょうね。
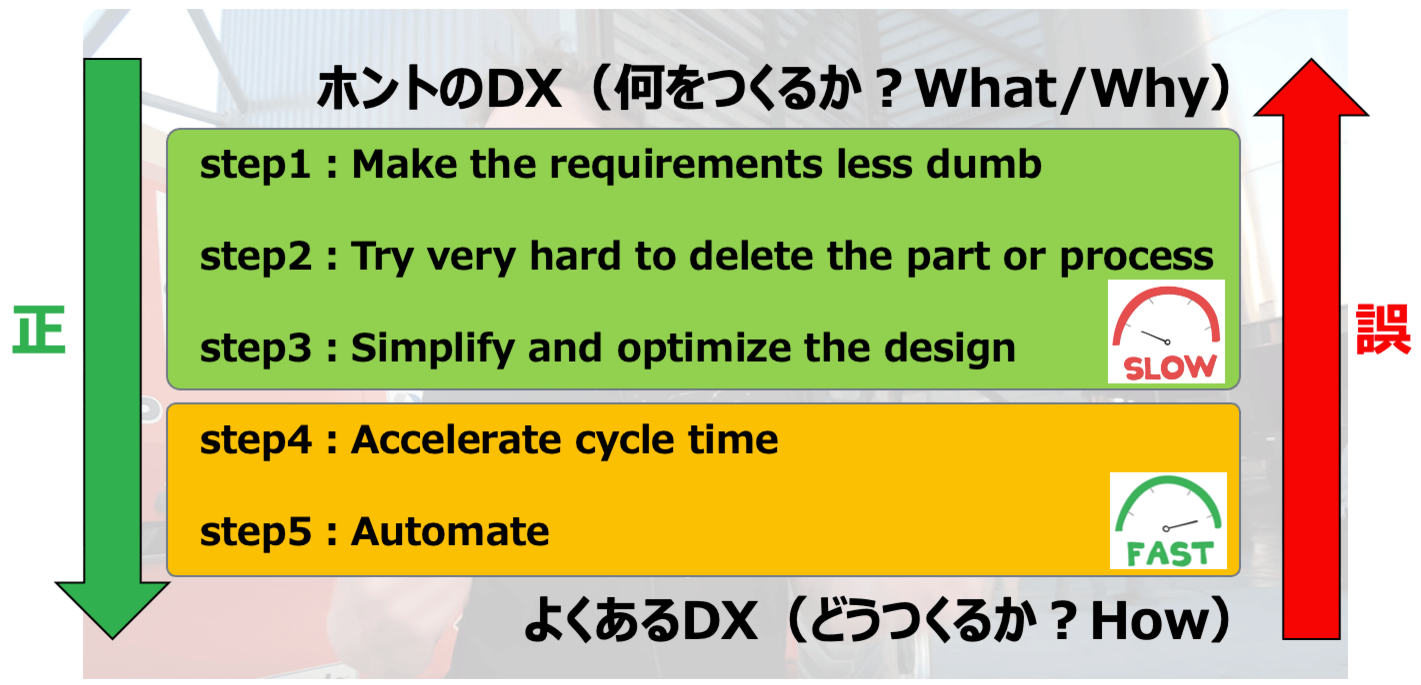
鈴木 本来のDX、今ふうに言えば「シン・DX」で何をすべきか。この図で言うと、ステップ1からステップ3までのWhatとWhyがシン・DXの具体的な内容です。あのイーロン・マスクでも、ステップ1から3はゆっくりやればいいと言っているくらい重要なステップです。逆に、ステップ4とステップ5はスピード感をもって進める必要があります。加えて重要なのは、実施する順番を間違えないことです。もしステップ4やステップ5から取り組むと、本来不要な工程をそのまま高速化や自動化してしまうことになりますので、注意が必要です。
ここで、「テスラは高価だから、高い顧客価値を提供して当たり前だ」という人のために、少し前の話なのですが、上汽通用五菱汽車の「宏光MINI EV」(以下、宏光ミニ)にも触れたいと思います。
販売台数のデータを見てみると、世界でダントツに売れているEVは、宏光ミニとテスラのModel Y、Model 3だけです。宏光ミニは俗に言う「45万円EV」、つまり、iPhone3台とほぼ同じ価格で手に入るEVです。一言で言えば「ゲタEV」のようなもので、子どもの送り迎えができるように、とりあえず雨風をしのげるEVであればいい程度の仕様です。フル充電すると一応は100km程度走行可能ですが、エアコンを使用するとおそらく60km程度に減少すると思います。急速充電には対応しておらず、通勤・通学や買い物など日常の移動後に自宅のコンセントで充電する、スマホと同じような使い方をします。
例えば、僕の地元の愛知県では、多くの人の走行距離は1日にせいぜい30〜40kmかと思います。出かける時にコンセントを抜いて、帰宅したらコンセントに再び差す。このような使い方のEVを定義し、顧客に提供しているのが宏光ミニなのです。
先ほどお話しした「ステップ1〜3」に当てはめると、ステップ1では走行距離100km、システム電圧100Vという究極の割り切りを行っています。ステップ2は、エアコン以外の装備や専用部品を一切排除し、もちろん回生ブレーキのような機能もありません。ステップ3ではシンプルな駆動系を採用しています。後輪の車軸に普通は前からドライブシャフトが来ているところに、モーターを直付けした感じです。従来からある部品をしっかり使っているのです。
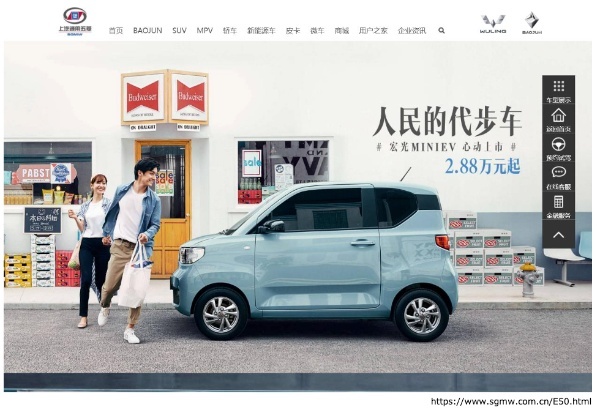
福本 まるで家電製品みたいですね。
鈴木 宏光ミニのことを「安かろう悪かろうのバッタものだ」とおっしゃる人もいますが、可能であれば「一度乗ってみてください」と僕は言いたいですね。実際に乗ってみる機会を得ることは困難ですが、ステップ1〜3を見事に実現しているこの車を体験することで、どれほど顧客を理解し、限られたリソースでどのように価値を作り込んでいるかを実感できるはずです。シン・DXのとても優れた事例と言えるでしょう。
田口 このステップ1〜3は、法律上の問題も含め、日本企業ではやりにくそうな感じがします。
鈴木 そうですね。私たちが「カイゼン魂」と呼ぶ手法は、巨大な問題をそのまま全体で考えることを避け、分割しようとします。そうすると、全体の仕様が考えづらくなります。分割すると良いこともあるのですが、「ゼロにはできないものの馬鹿げた仕様を減らす=ステップ1」を達成するためには、まず全体的に考え、「ここはいらないよね」などと必要ない部分を削減することが必要です。そのためには、分割し、各部分に担当者をアサインしてからでは遅いですよね。
田口 カイゼンが良かった時代はありました。だから全てを否定する訳ではないのですが、今の時代はシン・DXのアプローチを取れないと置いていかれてしまう部分は、多分にあると思うのですよ。
鈴木 現在でもカイゼンが有効な領域は数多くあります。けれども、価値にフォーカスしたシン・DXが必要な領域も増えてきています。成功の鍵はステップ1〜3です。これらを実行しなければ、少しヤバいなと最近感じることが多いです。
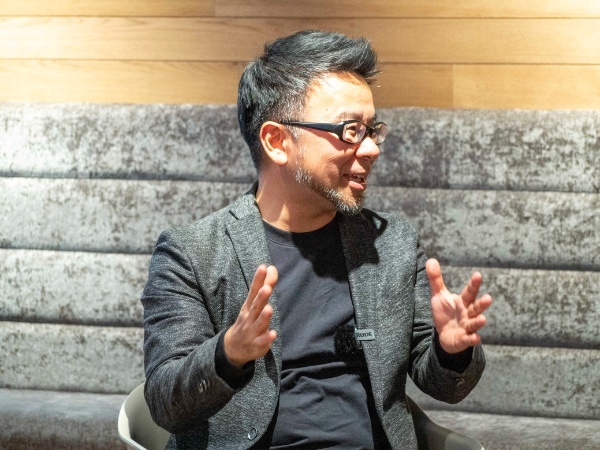
「つながる社会」への道は「守破離」にあり
田口 ここまでお話いただいたことを実際に進めていくとすれば、トップダウンで意志を持って進めることが必要になってくると思います。次世代のリーダーへのメッセージとして、実際にどうしていくべきなのかをお話しいただけますか。
福本 先ほど鈴木さんも触れていましたが、CASEの概念は数年前から自動車産業に起こっている変化の潮流として取り上げられてきました。この潮流は、単に自動車を新しい姿へと変化させるにとどまらず、自動車産業の構造をも大きく変えようとしています。
燃料から走行まで、トータルで自動車の環境負荷を低減するためには、電動化(EV化)による走行時のCO2排出の削減だけでなく、供給電力の発電時におけるCO2の削減、自動化やシェアリング、信号機などの都市交通インフラとの連携による自動車自体の運行効率の向上など、産業界が一体となった取り組みが必要となります。
これを実現していくためには、さまざまな産業界のプレイヤーが連携してエコシステムを作り、構造変革を実現していかなければなりません。従来付き合いのなかったプレイヤーとのつながりも必要となります。これがCASEの本質だと考えています。
このような取り組みは、ボトムアップでは実現できないと思います。経営層が強い意志を持ち、積極的に関与していくことが求められます。新たなつながりを作り、顧客や市場の立ち位置から見た顧客経験価値を高める取り組みを進めていくべきです。
鈴木 福本さんが今おっしゃったCASEの概念にとてもインスパイアされました。CASEの「C」「A」「S」「E」それぞれは部分的な要素ですよね。CASEを単なる部分として捉える限り、それらは集めても部分であり、全体ではない。もう一段上の、周囲の業界との関係性まで加えて考えることで、初めて、CASE全体としての意味が出てくると気づきました。
次の僕からのメッセージは、「変化の大きい時代においては、強みと弱みが反転する」ことです。これはシリコンバレーで勤務していた時に、インド出身の連続起業家の方から教えていただいたことです。具体的には、「30年の経験は、30年のタコツボになる」ということです。変化が少ない時代には、積み上げた知識や経験が強みになりましたが、変化が大きくなると、持っているアセットがむしろ足かせになってしまう面があるということです。
ではどうすればいいのでしょうか。今、多くの方が唱えている「リラーン(Relearning)」すればいいのです。ただ、実際に「リラーン」しようとしても、がなかなかうまくいかないことが多いのではないでしょうか。その原因の一つが「アンラーン(Unlearning)」の未実施です。いきなり「リラーン」しようとしても、既存のアセットの上に新たなものを積むことになってしまいます。そうならないために、まずアンラーンを行い、過去の強みを取り払い、その上でリラーンを行うことが必要なのです。焦ってリラーンしようとすると、大変なことになります。
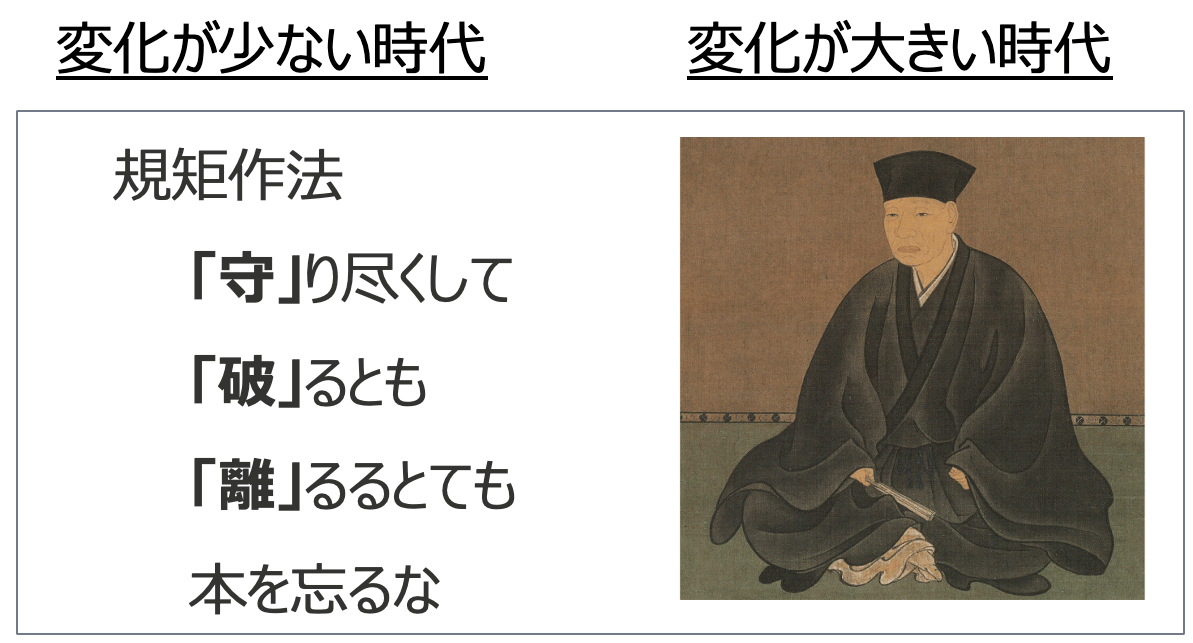
横文字がなんだか嫌だなあと思う人は、日本古来の規矩作法の「守破離」で考えてみてはいかがでしょうか。「アンラーン/リラーン」は、もう本当に「守破離」そのものです。カイゼンとDXを分けて苦手なことを無理矢理にやるのではなくて、カイゼンでできていることをうまく生かす。そして、できないことを責めるのではなくて、できていないところを埋めてあげることで、できるようにしていく。これこそが、今の製造業に必要なことなのではないかと思います。カイゼンをインクリメンタル(徐々)に、DXに近づけることができると思うのです。
田口 なるほど。カイゼンはある意味、インクリメンタルな行為です。例えばその中に、アンラーンとかリラーンみたいな行為を生み出しながら、ひょっとしたら日本的なステップ1、2、3ができる可能性があるかもしれませんよね。
鈴木 田口さん、とてもいいことを言われています。実はステップ1〜3は、本当は、日本企業や日本の組織が非常に得意なところではないかと思うのです。「外国製DX」として4、5に惑わされることなく、1〜3をきちんと理解して本当に実行できれば、僕は日本が大きく飛躍すると信じています。
福本 従来、日本企業の現場は、現場・現物・現実という三現主義で成り立ってきており、これが強い現場を支えてきました。これは強みですので決して否定すべきものではないと思います。今後は、現場の強みと新しい時代の世界観を共存させていく取り組みが重要になっていくということではないでしょうか。
田口 本日はお二方からの貴重なお話、ありがとうございました。
【関連リンク】
スズキマンジ事務所 https://linkedin.com/in/manji-suzuki-7500781/
株式会社東芝 https://www.global.toshiba/jp/top.html
株式会社コアコンセプト・テクノロジー https://www.cct-inc.co.jp/