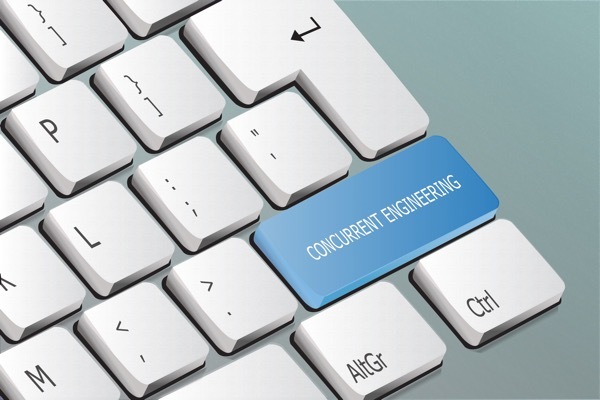
激しい競争にさらされている昨今の製造業では、製品開発力の強化が急務となっています。そこで改めて注目されているのが、コンカレントエンジニアリングと呼ばれる開発手法です。コンカレントエンジニアリングは開発期間の短縮や効率化を図る手法であり、企業の競争力を高めていくと考えられています。本コラムでは、コンカレントエンジニアリングの概要やメリット・デメリット、実現するための方法などを解説します。
目次
コンカレントエンジニアリングとは
まずコンカレントエンジニアリングの概要と、従来の手法との違いについて解説します。
コンカレントエンジニアリングの概要
コンカレントエンジニアリング(Concurrent Engineering:コンカレントは「同時並行」を意味する。CEとも表記)は製品開発の手法の一つであり、複数のプロセスを同時並行で進めることを指します。たとえば、設計部門が設計を終える前に製造方法を検討する、生産技術部門の持つノウハウをフィードバックしながら設計を行う、といったイメージです。
コンカレントエンジニアリングは、1980年代にアメリカで生まれた後に日本にも広まり、自動車業界や電機業界などが取り入れていきました。規模の大きな製品開発で特に効果を発揮するため、従来は大手企業しか導入していませんでしたが、昨今では製品開発の進化を図ろうとする中小企業でも導入が進んでおり、改めて注目が集まっています。
従来の開発手法との違い|CEは設計と生産を同時並行で進める手法
一般的な製品開発の手法は「ウォーターフォール型」と言われ、上流から下流に向けて順番に開発を進めていきます。上流のプロセスが完了するのを待ってから下流のプロセスが動き出すため、確実に製品開発を進められますが、設計が完了してから生産工程が開始されるため、製品の設計変更や修正が生産段階で発生すると、時間やコストがかかります。また、開発期間はどうしても長くなってしまいます。
一方、コンカレントエンジニアリングでは設計と生産を同時に進めるため、生産に関連する要件や制約を早期に考慮し、設計段階での変更や修正を最小限に抑えることができます。上流と下流のプロセスが同時並行で進んでいくので、開発期間を大幅に短縮することも可能です。
このような同時並行のプロセスにより、製品の開発期間が短縮され、設計の品質や製品の信頼性が向上します。また、設計と生産の連携により、生産コストの削減や製品の競争力強化が可能となります。さらに、コンカレントエンジニアリングを実現することで、顧客の要求や市場の変化に迅速に対応する柔軟性も得ることができます。
コンカレントエンジニアリングの特徴|メリットとデメリット
コンカレントエンジニアリングには、メリットとデメリットの両方があります。それぞれどのような内容なのかをご紹介します。
コンカレントエンジニアリングのメリット
コンカレントエンジニアリングを導入するメリットは、おもにQCD(納期・コスト・品質)の向上です。
開発期間の短縮による納期の適正化が可能
設計と生産を同時に進めることで開発期間が短縮されることに加えて、設計変更・修正など生産段階で発生するリスクを低減も可能になります。結果として迅速な製品の市場投入が可能となります。
また製品開発をスピーディに進めることで、顧客のニーズに合った製品を素早くリリースできるようになり、先駆者利益を得られます。
コスト削減
設計と生産の同時進行によって、開発コストを削減できるとともに、無駄な設計変更などにかかわる生産リソースの無駄遣いを削減できます。また、製品開発の効率化によって、設計段階から製造方法や品質管理を意識することで品質を向上させる、といった効果も得られます。
品質の向上
コンカレントエンジニアリングでは、設計者と生産者が連携して製品開発を進めるため、設計段階でニーズに基づいた生産性や製造性を考慮することができます。スピーディに市場のニーズを反映できるため、製品の品質や信頼性が向上にも期待できます。
フロントローディング・多品種少量生産に対応・顧客満足度の向上に貢献
変化の激しいこれからの時代においては、他社に先駆けて顧客のニーズに合った製品を提供していかなくてはなりません。そのためには、開発期間の長いウォーターフォール型の製品開発ではなく、コンカレントエンジニアリングの方が適していると考えられています。
コンカレントエンジニアリングは市場の変化や顧客の要求に「迅速に」対応することが可能です。製品を早期に市場に投入し、顧客のニーズに対応した製品提供や製品の改善を継続することで、顧客満足度を向上させることができます。
コンカレントエンジニアリングのデメリット
コンカレントエンジニアリングのデメリットは、かえってQCDが悪くなってしまう恐れがあることです。
リスクの増加
設計と生産を同時に進めていった結果、設計の変更や誤りが生産に波及するリスクがあります。計画の不備や予測不能な問題が発生した場合、開発プロセス全体に影響を及ぼす可能性があるということです。
たとえば、設計途中の情報をもとに調達部門や製造部門が動いていた場合に、大きな設計変更があるとそれまでの業務が無駄になってしまうリスクがあります。
コミュニケーションと調整の困難さ
複数のプロセスを同時並行でミスなく進めるためには、異なる部門間での情報共有やコミュニケーションを密接に行う必要があります。これを怠ると、情報共有や意思決定の遅延などが起こる可能性があります。
体制や環境が整っていない状態でコンカレントエンジニアリングを導入すると、失敗する可能性が高いことを覚えておきましょう。
コンカレントエンジニアリングに必要なITツール
複数のプロセスを同時並行で進めるコンカレントエンジニアリングは、情報共有を密接に行わなければ成り立ちません。そこで不可欠になってくるのが、次のような各種ITツールの活用です。これらのITツールを活用すれば製品開発のデジタル化が可能になり、情報共有や共同作業がしやすくなります。
- CAD(Computer Aided Design)
- CAM(Computer Aided Manufacturing)
- CAE(Computer Aided Engineering)
- PDM(Product Data Management)
- PLM(Product Lifecycle Management)
CAD(Computer Aided Design:コンピューター支援設計)
読み方は「キャド」です。製品の設計や図面作成を、コンピューターを活用して行う技術です。CADソフトウェアを使用することで、3Dデータのモデリングや2D図面の作成、設計の詳細化、デザインの変更や改善などが容易に行えます。
またCADには、さまざまな用途に対応できる「汎用CAD」のほかに、製造業向け・建築業向け等、機能に合わせた「専用CAD」があります。
CAM(Computer Aided Manufacturing:コンピューター支援生産)
読み方は「キャム」です。製造工程の計画や制御をコンピューターを用いて行う技術です。CADで作成された設計データをもとに、機械加工や切削加工、3Dプリンティングなどの製造工程を自動化・最適化したプログラムなどを作成します。
CAE(Computer Aided Engineering:コンピューター支援解析システム)
製品の開発や設計の段階において、解析やシミュレーションをコンピューター上で行う技術です。CAEソフトウェアを使用することで、物理的な特性や目には見えない物体内で起きる現象(応力・温度・電磁場・振動など)のシミュレーションを行ってデータを可視化。製品の性能や安全性を予測・評価することができます。CAEは製品の改良や最適化、品質向上に役立ちます。
PDM(Product Data Management:製品情報管理システム)
製品に関連する設計校庭で発生するデータ(設計図面、仕様書など)の、一元管理を行うシステムやプロセスを指します。PDMはデータのバージョン管理や共有などを通じて、チーム内の協力や情報共有を強化し、製品ライフサイクル全体の最適化に貢献します。
PLM(Product Lifecycle Management:製品ライフサイクル管理システム)
製品のライフサイクル全体を統合的に管理する手法やシステムを指します。PLMは製品の計画、設計、製造、販売、保守、廃棄などの各段階でのデータやプロセスを相互に関連付け、製品情報や関連情報の一元管理を実現します。これらの製品開発と製品ライフサイクルの効率化、業務効率の向上など、体制の強化を図る取り組み自体を指します。
特に、PDMやPLMは設計データやBOM(部品表)といった製品に関するデータを一元管理し、情報共有することを目的としているシステムです。これらを導入することで、コンカレントエンジニアリングの実現が近づくといえます。
コンカレントエンジニアリングを実現するために必要な2つの要素
コンカレントエンジニアリングは高度な開発手法であり、簡単に実現できるものではありません。ここでは、コンカレントエンジニアリングを実現するための3つの方法をご紹介します。
担当者の知識レベルやスキルの向上
コンカレントエンジニアリングでは、製品開発の初期段階からあらゆることを想定していく必要があります。
たとえば、設計者は製造方法や原材料の調達方法を考慮した上で、量産化しやすい設計を行わなくてはなりません。そのため、設計者にはこれまで以上に幅広い知識が求められることになります。また、他部門の担当者への説明や調整が格段に増えるため、コミュニケーションスキルも高めていかなくてはならないでしょう。この実現には、全体統括できるDXプロデューサーや、デジタル人材の育成や獲得が必要となります。
コンカレントエンジニアリングを実現するためには各担当者の知識レベルやスキルの向上が不可欠です。製品開発の手法を切り替えていくためには、それなりの時間がかかることを覚えておきましょう。
開発体制の再構築
コンカレントエンジニアリングは、従来のウォーターフォール型の開発手法とは大きく異なります。そのため、部門間の連携やコミュニケーションがしやすい開発体制を再構築しなければなりません。
上述したITツールを活用しつつ、製品開発の手順を整備して設計レビューや進捗確認の場を設けるようにしましょう。その際に、最終的な意思決定を誰がどのように行うかといったルール化も重要です。また、イレギュラーチェックリストで事前に問題点を洗い出しておき、手戻りを防ぐといった工夫も求められます。
コンカレントエンジニアリングの先にあるもの
コンカレントエンジニアリングは、単なる業務効率化や期間短縮だけではなく、更に高度な業務プロセスの構築につながっていきます。コンカレントエンジニアリングの推進により部門間の連携や、担当者のレベルを上がっていくと、手戻りの減少をはじめとして業務効率化は勿論、より高い目標設定を設定でき、より大きなプロジェクト、複雑で技術レベルの高い案件の推進にもつながります。
また、その推進をさらに強固に、効率的に行うために業務プロセス自体の改善、革新が実現していきます。1部門、1製品のラインだけではなく、企業としての生産性、ものづくりとしてのパフォーマンスが進歩していくことにつながります。
まとめ|コンカレントエンジニアリングの導入を検討している企業様へ
今回は、製品開発の手法の一つであるコンカレントエンジニアリングについて解説しました。コンカレントエンジニアリングの実現によって、製造業の競争力は格段に高まっていくと考えられています。一方、コンカレントエンジニアリングにもメリットとデメリットがあり、組織の特性やプロジェクトの要件に応じて、利点と課題を適切に見極め、導入を検討する必要があります。自社の製品開発に課題を感じておられる方は、本コラムを参考にしつつ、コンカレントエンジニアリングの導入を検討してみてください。