デジタル化の動きは、物流の世界にも及んでいます。その1つとして注目されているのが、商品を出荷する際のアソート(詰め合わせ)を効率化するためのシステム「デジタルアソートシステム(DAS)」です。EC時代の複雑な物流を支えるDASとは何か、どれほどの効果があるのか、その耐用年数やメリット、デメリットについて調べてみました。
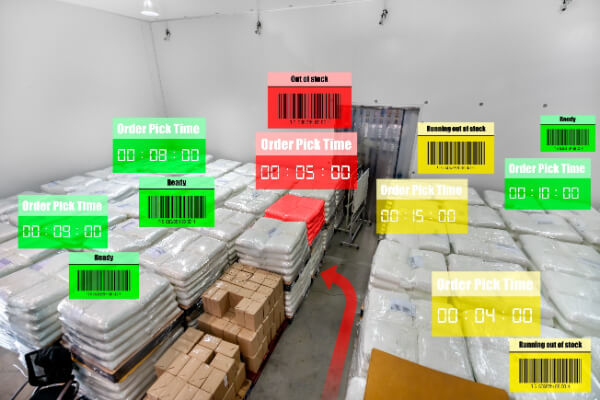
目次
デジタルアソートシステム(DAS)とは?
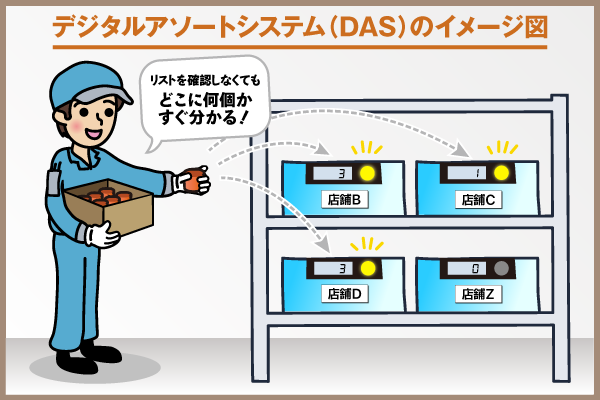
デジタルアソートシステム(以下、DAS)は、倉庫から商品を出荷する際、その業務を効率化するシステムです。DASは“Digital Assort System”の頭文字をとった略語で、Assortは「仕分ける」「詰め合わせる」「えり分ける」「分類する」といった意味です。つまり、デジタル化した「より分け、詰め合わせ」システムといえます。
従来、受注品のリストは紙に印刷されて、発送商品をそろえる作業員に手渡されていました。作業員はそのリストを確認しながら商品をピッキング(摘み取り)し、箱に詰めていましたが、DASではこのリストは不要となり、担当者がリストを確認しながら選ぶ作業はなくなります。
商品を詰め合わせる棚の間口にデジタル表示器が設置され、商品の種類と数量が指示される仕組みです。作業員は、デジタル表示を確認しながら1回につき1種類の商品を指示された数量だけ収集していくシンプルな作業になります。
これにより、商品を探すために要していた時間が短縮もしくはゼロとなり、ミスもなくなって著しく効率化されます。とくに在庫をストックすることなく、直ちに出荷するタイプの流通拠点にはうってつけのシステムであり、その需要は拡大しています。
リストを確認しながら商品をピッキングするスタイルは、作物を収穫するのに似ていることから「摘み取り式」といいますが、これに対してDASは種まきに似ているので「種まき式」といわれます。
ゲートアソートシステム(GAS)・デジタルピッキングシステム(DPS)との違い
DASと混同されやすい言葉に、ゲートアソートシステム(以下GAS)と、デジタルピッキングシステム(以下DPS)があります。どれも倉庫内の作業効率化に役立つシステムですが、以下のような違いがあります。
DAS | 種まき式。 商品を認識すると、ボックス上の表示器に同商品の投入数を表示するシステム。 |
GAS | 種まき式。 全てのボックスにゲートが付いており、投入するボックスのゲートが一つずつ開き、商品の投入数を表示するシステム。ゲートを閉じると次のゲートが開く。 |
DPS | 摘み取り式。 仕入れ先を指定すると、摘み取るべき商品が入っているボックスの表示器が光り、ボタンを押すと摘み取り数を表示するシステム。 |
GASはDASのボックスにゲートが付いたシステムです。GASに商品を読み取らせると、投入すべきボックスのゲートが一つ開き、表示器に投入数が表示されます。投入し終わり、作業員がスイッチを押すとそのゲートは閉じ、次に投入すべきゲートが開くようになっています。
DPSは、作業員が仕入れ先に納める集品箱を持ち、商品をピッキングしていく摘み取り式のシステムです。DASやGASとは異なり、自ら商品を摘み取っていくスタイルを取ります。集品箱を移動しなければなりませんが、経路を最適化することで振り返りやかがみ動作を最小限に抑えられるシステムも出てきています。
DASによる生産性向上はどれくらいか
DASによって商品の仕分け作業が効率化されることで、どれほど生産性の向上が図れるのでしょうか。ある食品流通会社では、出荷する商品の仕分け作業に昼間と夜間併せて一日で延べ180時間かかっていました。DAS導入後はこれが145時間にまで短縮されたといいますので、所要時間は導入前より延べ35時間も短縮できたことになります。
このほか、出荷ミスがなくなりそのリカバリーに要していた時間もなくなったことで、全体の生産性は相当上がったことが想定できます。
この食品流通会社の仕分け作業は、出荷先ごとに用意された“かご車”に商品を収集していく作業ですが、 DASによってかご車の配置を自由に換えられることができるようになったことも、効率アップに大きく貢献できたといいます。
このように、DASによる生産性向上の効果は明確です。直接的な時間短縮のほか、同時にほかの利点も生じるシナジー効果が発揮されており、理想的なシステム導入状況であるといえます。
DASの耐用年数はどれくらいか
DASの導入において気になるのが“どれくらいもつか”ということです。一般的に「耐用年数」といわれますが、この耐用年数には2種類の見方があります。1つは、国税庁が決める「法定耐用年数」です。もう1つは部品の消耗や生産体制、技術の進歩による陳腐化などにより、実際に使えなくなるまで何年かかるのかという点です。
前者において、DASは一般的に「機械および装置」に該当し、8〜12年と考えられます。年数にやや幅があるのは、コンピューターなど情報通信機器の部分と、各種デバイスのついた台車など「倉庫業用設備」あるいは「運輸に付帯するサービス業用設備」などに分けられ、それぞれ対応年数が異なるためです。
国税庁の示す法定耐用年数はほとんどの場合、実際に経年劣化・陳腐化して使えなくなる年数と大差ないため、ビジネス上では法定耐用年数をもって実際の耐用年数と考えることが多いようです。
ただし、今日のような変化が著しいデジタル革命の時代は、新しい手法が発見、開発されて、導入したばかりのシステムが想定より早く陳腐化してしまう可能性がないとは言えません。
したがって、「耐用年数を見越した導入」というより、外部環境が変わっても対応できるようなフレキシブルに変化できる導入方法を考えたほうが良いかもしれません。
DASメーカーの紹介
ここからは、国内の主要なDASメーカーを紹介しましょう。
・富士電機
富士電機は、一般的に広く知られている歴史の古い電機メーカーです。1923年古河電機とドイツのシーメンス社が技術提携で設立して以来、発電機をはじめとする社会インフラを構成する電気機器を製造してきました。コンピューターで知られる富士通は1935年に富士電機の電話部が独立したのが始まりです。
富士電機の事業の柱は現在でも発電機などパワープラント周りになりますが、物流ソリューションも大規模に営業しており、多くの実績があります。DAS/DPSなどのデジタルピッキングシステム、倉庫運用管理システム、スマート仕分けシステムなど従来の在庫管理やマテハン(マテリアルハンドリング)で解決できなかったものに取り組んでいます。
・寺岡精工
寺岡精工は、計量器のメーカーです。肉などの重さを計って金額を表示する機器をスーパーマーケットなどで見かけたことはないでしょうか。近年、普及が進んだセルフレジの製造も手掛けています。
物流ソリューションとして、DPSやDASも作っています。DPSでは得意の計量器の技術を応用したものもあります。これらは、計量器の製造から始まった流通と小売りのソリューションの発展形であり、日本の流通をよく知ったメーカーとして広く知られています。
・DAIFUKU(ダイフク)
ダイフクは1937年の創業の物流システムメーカーです。物流の業界ではモノを動かすマテハンの最大手として、同業界では広く知られている企業です。
物を動かす仕事から派生するソリューションとして、物流ソリューションが業務として発達してきました。DASも開発しておりホストコンピューターから無線で表示器に送信される指示に従って商品を種まき方式でそろえていくシステムを開発しています。通過型や食品加工センターなど、在庫を持たないセンターの荷揃えに適したシステムです。
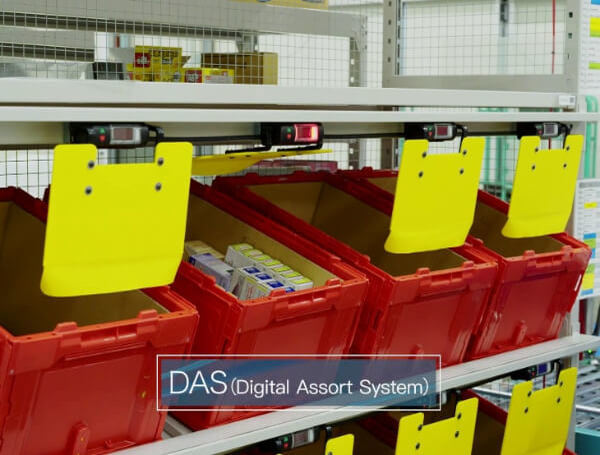
DASのメリットとデメリット
冒頭で述べた通り、DASの導入には効率化や生産性の向上などが期待できますが、懸念点も考えられます。DASのメリットとデメリットについて整理してみましょう。
DASのメリット
仕分け時の作業工程を標準化できる
DASを導入することで、システムの運用方法として手順が決まることから、おのずと仕分け作業工程は決められた手順をこなすようになります。こうして標準化されれば、熟練した従業員でなくても同じような速度で作業が可能になるでしょう。アルバイトや新入社員のような不慣れな社員であっても同じように作業ができれば、全体の生産性は上がっていくと考えられます。人件費率を下げられる
作業工程が標準化され、仕分け作業の所要時間が短縮されれば、同じ量の仕分け作業の実働人員数は少なくなるはずです。8人の作業員が1日1時間を短縮できれば8時間の短縮となり、1人分を削減できます。計算上、売り上げに対する人件費率が下がるでしょう。 人員配置を見直すことで、さらなる生産性の向上が見込めるかもしれません。- 仕分けミスが減少する
作業工程が標準化され、作業内容がシンプルになることでミスは必然的に少なくなるでしょう。標準化を進め、熟練者でなくても同じように作業ができるようになることの効果は、ミスの減少という良い結果を生むことにつながります。 仕分けミスのない物流は、リカバリーに要する時間を削減できるため、作業はさらにはかどることが期待できます。
- 仕分けミスが減少する
DASのデメリット
導入コストの負担
DASはデジタル表示器など、専用の機器が必要となります。人件費率の向上が見込める一方で、導入コストを回収できるかどうかの検討が必要です。ただし、コスト対効果は、経済的な効率だけでは測れない部分もあります。 作業の標準化にコストをかけなければ、将来的な労働力の確保が難しくなるという見方もあるでしょう。稼働後のロケーション変更が難しい
無線で信号を飛ばす方式のデジタル表示器もありますが、そうでない場合は作業手順や効率を考慮したレイアウトを検討し、ケーブルを張り巡らす必要があります。このように電気工事が必要な場合、その後のレイアウト変更は困難になります。
またDASのシステム上、一度に行う仕分けは1商品ずつとなります。工程を踏まえて計画しないと、次の商品は「仕分け待ち」という状態が発生しかねません。かご車、棚、人の導線の設計はとても重要な作業となるでしょう。システム停止時のリスク
DASを実行するシステムは機械である以上、故障の可能性は排除できません。完全に停止した場合の備えがなければ、極端に作業効率が落ちる、あるいは仕分け作業が全くできないリスクがあります。万が一のケースに、どのように業務を継続するのか、DASで効率化するのであれば対策を講じておく必要があるでしょう。
DASのケーススタディー-①
神奈川県に本部のある外食チェーンでは、毎日100店舗に食材を配送しています。以前は各店舗から寄せられた発注データを紙に印刷して作業員に手渡され、荷箱を床に並べ、リストに書かれた内容通りに収集していく、種まき方式の仕分け作業がとられていました。
しかし人的作業においては、どうしてもミスが発生してしまいます。外食チェーンにおいて発注した品物が届かなければ、売り上げの機会喪失を招いてしまいます。この現象がどうしても発生してしまうことが、この企業にとっての課題となっていました。合計した数でチェックをしても、数は合っているので気付くことができません。
さらに、物流と加工を担当する従業員のほとんどは不慣れなパートの従業員で、日本語が得意ではない外国人労働者もいます。受注品のリストを読めなければ仕分け作業に従事させることができないという問題もありました。
これらの課題を解決すべく、仕分け方式を摘み取り方式にしてみたり、2人で行っていた作業を1人で行ってみたりしたものの、解決には至りませんでした。リストをもとに行う以上、この課題は解決しなかったのです。
そこでDASの導入を検討することにしました。デジタル表示器に指定色のランプが点灯し、その色の商品を表示されている個数だけ収集する方式です。この方式であれば、日本語を読む必要はなく、リストを印刷する必要もありません。他にも全自動の大規模なマテハン設備やスマートフォンを利用したピッキングシステムも候補にありましたが、現在の業務事情に最も適合したのがDASでした。
倉庫内のスペースなども考慮に入れ、全工程を2回実施する方式をメーカー担当者と相談してつくり出しました。店舗ごとに設置されたコンテナには、デジタル表示器がつけられています。デジタル表示器には点灯する5種類の色のボタンと上部に数量の表示器があります。
仕分け担当者が自分の商品の色のボタンを押すと、表示器の該当する色のボタンが点灯します。仕分け担当者は担当の商品をもってコンテナの前に来ると、その色のボタンを押します。すると表示器に数量が表示されるので、その個数をコンテナに入れます。入れたらもう1回ボタンを押せばボタンが消えます。これを繰り返して商品が仕分けされていきます。
表示器は専用のキャスター付き架台に設置されており、移動することができます。仕分け作業が終われば片づけられるので、限られたスペースで無駄を省くことが可能です。
このシステムを導入してから、受注品のリストを印刷する必要がなくなりました。仕分けのミスも減り、作業員は両手を使えるようになりました。もしミスが発生しても「再点灯モード」で数量の確認ができるので、足りない、あるいは多すぎる場合に、該当のコンテナを全員で確認することができ、リカバリーも時間がかかりません。
このDASシステムの導入によって、作業にあたる従業員を抑えることができ、少人数で以前より多くの店舗を担当できるようになったといいます。また、空いた時間で翌日の準備や、仕分け以外の作業(加工など)まで取り組めることから、センター全体の効率化にも貢献できています。
DASのケーススタディー-②
「七輪焼肉安安」や「Mr.チャーハン」を展開する株式会社富士達はDASを導入し、倉庫内の速やかな仕分けを実現しました。これにより、仕分けにかかる時間の削減や、作業の簡易化を実現しました。
従来同社は、紙のリストに書かれた商品をピッキングしていく手法を採用していました。しかし紙ベースだと、入れた商品をペンで塗りつぶしたり、仕入れ先のボックスを探したりする必要があるため、ピッキング作業に多くの時間がかかっていました。
また、紙のリストを見て商品を入れる必要があるため、日本語が読めない外国人労働者にはピッキング作業を頼めないという問題もありました。これらを解決するため、同社は紙のリストを廃止し、誰でも簡単に仕分けできるDASを導入しました。
同社が導入したDASは、商品ごとに色が指定されています。これにより、日本語の読めない外国人労働者も色で判断することができ、どこに何を入れるかが直感的に分かるようになりました。
また、紙のリストを持たなくて済むようになったため、両手での作業が可能になりました。さらに、個数があわなかった時には、表示器の「再点灯モード」で間違いを大人数で一気に探せます。
これらの効率化により、従来は最大10人で対応していた作業が、今は多くて6人の人員で作業が進められています。また、非常に簡単な作業のため、軽度の知的障害者や日本語の読めない外国人も採用できるようになったと言います。
このようにDASの導入は、業務効率化だけでなく、人件費削減や人材募集の拡大にも繋がっています。同社は、初期投資が相殺できるほどの人件費削減効果を感じていると聞きます。
DASを選ぶ際のポイント
DASを選ぶ際には、以下の2つのポイントに注意すると、効率化の恩恵を最大限得られるでしょう。
- 既存システムとの連携
- 操作性
既存システムとの連携
DASを選ぶ際には、既存システムと連携が取れるかを確認しておきましょう。どれだけ良いシステムを選んでも、既存システムと連携できなければデータを共有できず、かえって非効率になる場合もあります。
データ共有が自動化できない場合、データの変換作業や手打ちでの入力作業が必要になります。そのような事態を避けるためにも、自社で利用しているWMSなどの上位システムと連携できるかを事前に確認しましょう。
操作性
導入したDASは自社の従業員が利用することになるため、操作性が高いものを選ぶようにしましょう。操作性が低いDASを選んでしまうと、業務効率化の効果が小さくなってしまうかもしれません。
操作がシンプルで覚えやすければ、教育やマニュアル作成にかかる時間は少なくなります。人の入れ替わりが激しい現場では、研修時間を少なくすることで、管理者の負担を軽減できます。できるだけ、直感的な作業が可能なシンプルなシステムを選ぶようにしましょう。
DASの今後は
国土交通省のホームページによれば、現在、日本の物流政策は、令和3年6月に閣議決定された「総合物流施策大綱(2021年度~2025年度)」に沿って行われています。国土交通省においても日本の物流が抱える課題は、より先鋭化・鮮明化していると捉えられています。
「総合物流施策大綱(2021年度~2025年度)」の内容をまとめると、要点は次の3つです。
[1]物流DXや物流標準化の推進によるサプライチェーン全体の徹底した最適化(簡素で滑らかな物流の実現)
[2]労働力不足対策と物流構造改革の推進(担い手にやさしい物流の実現)
[3]強靱で持続可能な物流ネットワークの構築(強くてしなやかな物流の実現)
▽総合物流施策大綱(2021年度~2025年度)
DASは、まさにこれらの命題に資するものであるといえるでしょう。DASの導入によって、出荷業務は直接的に人件費削減などの効果を得られることが分かってきました。また、文字(日本語)を用いないことで外国人労働者も雇うことができます。
導入に費用がかかる一方で、削減した人件費や効率性の向上により、売り上げが増え、導入のための投資を回収する速度も上がると計算できます。種まき方式では、コンテナをまとめておくことができるためスペースの削減にもなります。
物流のIT化が加速するなか、今後はDASだけではなく他のシステムと連携して、物流全体がさらに効率化していくような動きもあるかもしれません。経済産業省など国が進めるデジタルトランスフォーメーション(DX)の取り組みとも同じ方向性であるため、今後の発展が期待できます。
(提供:Koto Online)