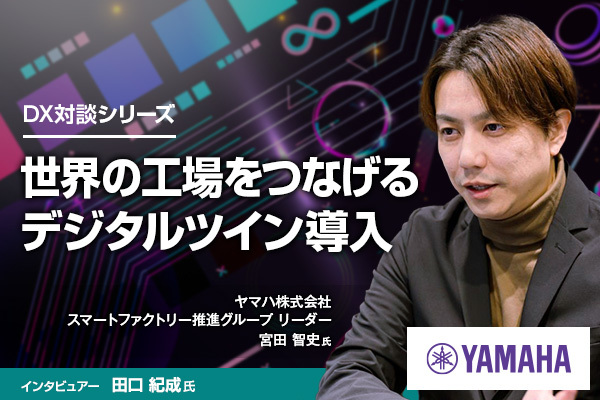
製造業のDXに対する取り組みについて、コアコンセプト・テクノロジー(CCT)CTOでKoto Online編集長の田口紀成氏が対談する本企画。第17回のお相手は、ヤマハ株式会社で楽器・音響生産本部 生産企画統括部 企画推進部 スマートファクトリー推進グループ リーダーを務める宮田智史氏です。
世界的な楽器・音響メーカーとして知られるヤマハは「感動を・ともに・創る」という企業理念のもと、アコースティックからデジタルまで多種多様な楽器をはじめ、業務用音響機器やホームオーディオ機器などさまざまな楽器・機器を提供しています。
また、2022年度から3ヵ年の中期経営計画「Make Wave 2.0」においては、「柔軟さと強靭さを備え持つ」を重点テーマの1つとし、生産・技術開発の高度化を目指すためのスマートファクトリー化や製造のデジタルツイン化を進めてきました。今回の対談では、これらの取り組みについてお話を伺います。
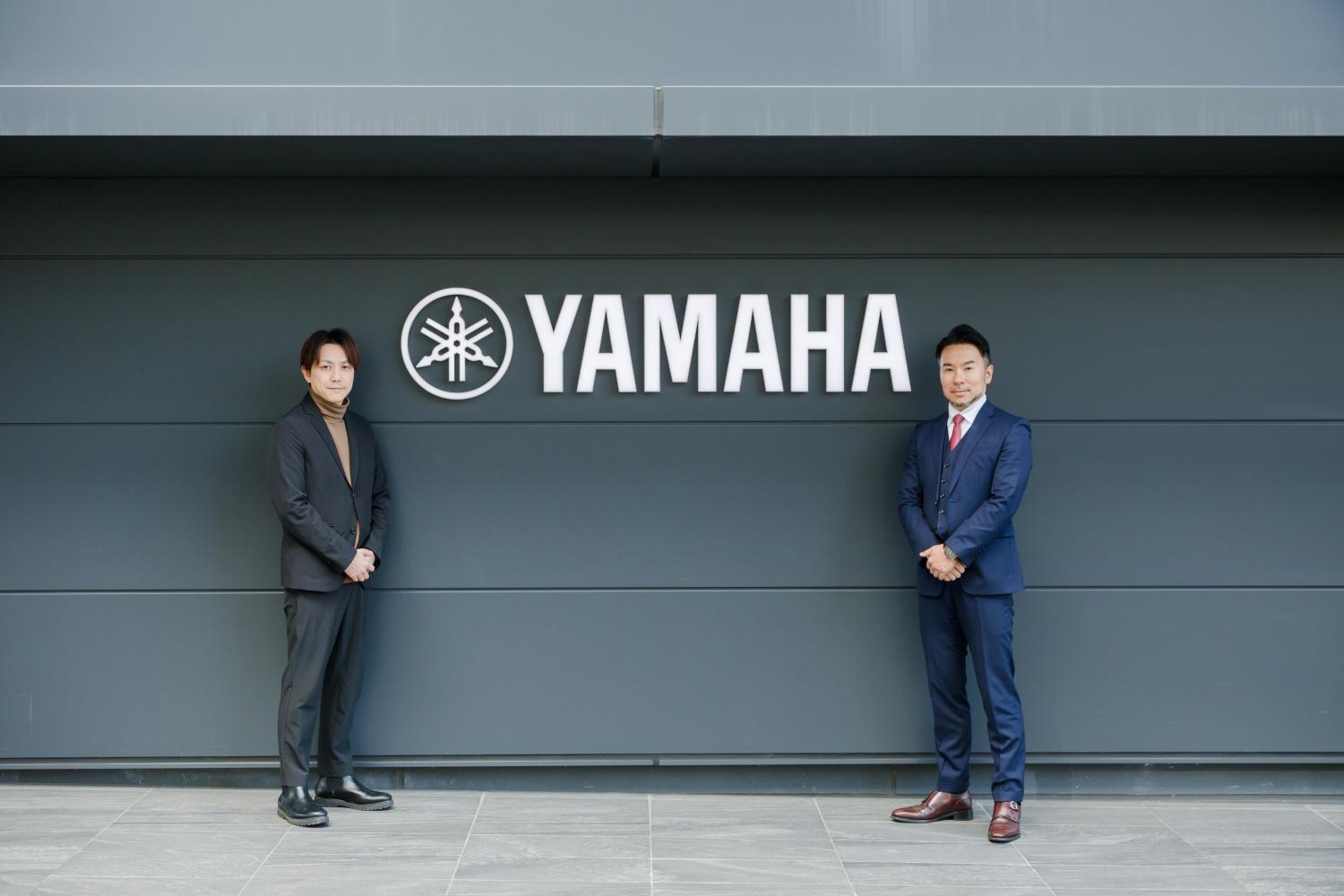
1999年 ヤマハ株式会社に入社。工場で品質保証・生産技術業務に従事し、ITシステム導入による生産現場の業務改善が主業務となる。2013年 本社企画管理部IT推進グループに異動、海外拠点の生産管理システム導入に携わる。2018年企画推進部にスマートファクトリー推進グループが創設され、初期メンバーとして異動。ヤマハ全工場をスマートファクトリー化するための企画・導入を推進、現在に至る。
2002年、明治大学大学院理工学研究科修了後、株式会社インクス入社。自動車部品製造、金属加工業向けの3D CAD/CAMシステム、自律型エージェントシステムの開発などに従事。2009年にコアコンセプト・テクノロジーの設立メンバーとして参画し、3D CAD/CAM/CAEシステム開発、IoT/AIプラットフォーム「Orizuru(オリヅル)」の企画・開発などDXに関する幅広い開発業務を牽引。2014年より理化学研究所客員研究員を兼務し、有機ELデバイスの製造システムの開発及び金属加工のIoTを研究。2015年に取締役CTOに就任後はモノづくり系ITエンジニアとして先端システムの企画・開発に従事しながら、データでマーケティング&営業活動する組織・環境構築を推進。
目次
現場の課題を解決するシステムが生き残る
田口氏(以下、敬称略) 御社はサックスなどを生産する豊岡工場、ピアノやギターなどを生産する掛川工場のほか、国内外で13の工場を稼働しています。まず、宮田さんがスマートファクトリーの推進に関わるようになった経緯からお聞きかせください。
宮田氏(以下、敬称略) 2010年前後だと思いますが、私は豊岡工場で生産技術の業務を担当していました。当時は新しく立ち上げた電子基板実装工程のQCD改善に取り組んでおり、IT技術が使いやすくなり始めた頃でもあったので作業改善のためのシステムを構想企画・開発し、タブレット等のIT機器を生産現場へ導入し、生産の合理化を進めていました。
田口 一般的な消費者が日常でITに触れるのは当たり前でしたが、製造現場ではそこまで普及していなかった頃ですね。
宮田 企業がIT技術を導入するにはセキュリティ面などでハードルが高く、豊岡工場でもようやく10~20台のタブレットを入れるようになったタイミングだったと思います。私は生産計画を立てるスケジューラーやバーコードを使った部材のピッキングなど、システム関連の企画を立てて外部に開発を依頼し、現場へ導入することを担当していました。
こういった現場に即したシステム企画が評価され、2013年からは本社の生産企画部門に異動し、マレーシアや中国など海外工場における標準の生産管理システムの導入も担当しました。そして、2018年10月のスマートファクトリー推進グループ創設に伴い同グループに異動し、DX推進担当としてスマートファクトリー化などの取り組みに参画しています。
田口 ちなみに、宮田さんが手がけたシステムは、現在も工場で使われているのですか。
宮田 そうですね。
田口 製造現場では、新しいシステムが登場しても、定着しないことは多々あります。何が違ったのでしょうか。
宮田 現場の困りごとを発端に開発したからです。誰かの都合で作ったものは浸透しづらく、今までのやり方を変えろと言うと反発も起きます。そもそも求めていない仕組みを一方的に押し付けられても、誰も使いたがりません。
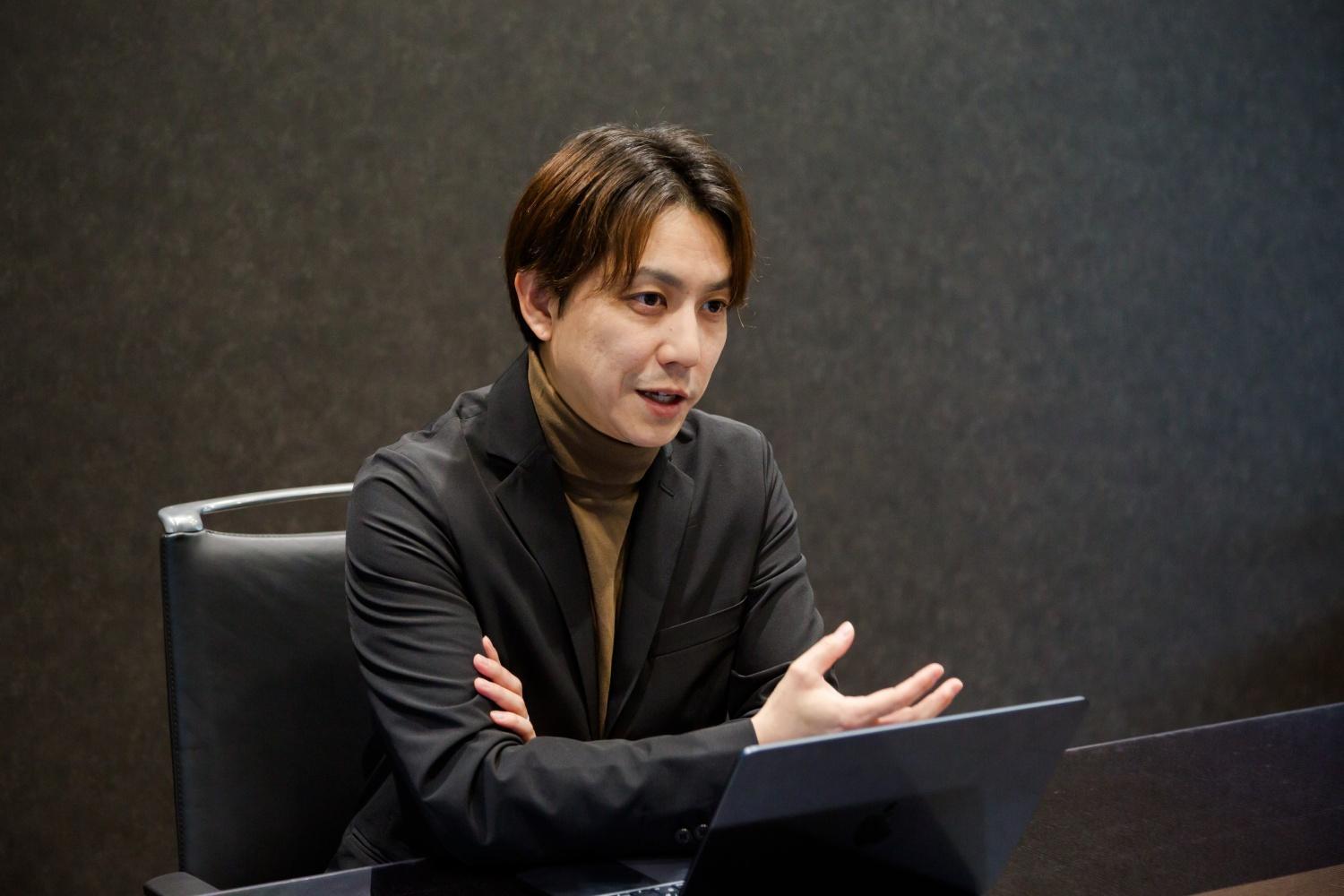
田口 課題はどのように特定するのでしょうか。集める仕掛けがあるとか?
宮田 私が意識していたのは、現場にいることです。用事がある時もない時も関係なく足を運び、たわいもない話をしたりしていると、困った時に呼ばれるようになります。日常的なコミュニケーションに気を使い、声をかけてもらえる関係性を作るようにしていました。
田口 一方、工場にいる時は、どのように本社と対話を進めていましたか。
宮田 本社や他部門の方たちは、その場にいないので現場の課題を正確に把握できません。そのため、課題と解決する仕組み、現実的な効果を説明し、投資してもらえるよう説明してきました。
ビーコンを活用した実績管理システムを構築
田口 2018年にスマートファクトリー推進グループが立ち上がったのは、なぜですか。
宮田 ヤマハには国内外に13ヵ所の工場があり、2010年代から各工場でDXを進めてきました。豊岡工場における私の取り組みも、その1つです。当時の状況として、 各工場が独自で取り組んでいたためシステムがサイロ化し、取得するデータや取得方法そのものも異なり、全社的なデータ活用ができませんでした。
全工場にデジタル技術を活用した標準的な仕組みを作り、工場QCDを継続的に向上させることを目的にスマートファクトリー推進グループを発足し、スマートファクトリー化に着手したのです。各工場が独自の仕組み・システムを作るのは否定しませんが、根幹となる生産管理や工場管理に必要なデータは標準で取りたいというのが、基本的な考えです。
田口 これまでの具体的な取り組みを、お聞かせください。
宮田 1つ目は、サックスの組み立て工程におけるビーコンを活用した実績管理システムの構築です。サックスの組み立ては約30工程に約50人が関わっています。品番も100種類ほどあり、部材が完成品になり梱包されるまで、とにかく人とモノの動きが不規則で、現状どうなっているのか把握できないという課題がありました。
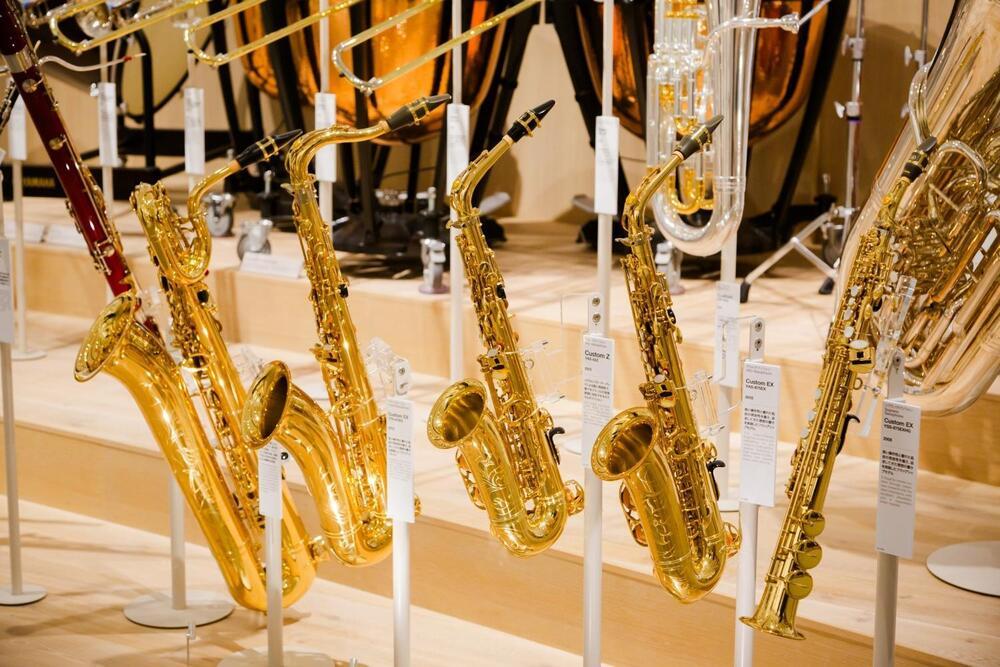
当時の生産管理システムでは、工程の要所で中間ポイントを定め、どのモデルがいくつできたかを手間がかかっても手書きで記録していましたが、全体的な流れは把握できません。途中で修正が生じると工程を遡ることもあるので、製品が重複カウントされることもあります。
そこで、製品にビーコンを付けて作業の軌跡を追えるようにして、作業の様子はIPカメラで録画し、さらに独自で開発した統合基盤に情報が送信されるようにして可視化することで、どの作業にどれだけ時間がかかっているか、滞留エリアや作業が遅い工程などはないかを現場の管理者がダッシュボードで把握、分析、改善できるようにしました。
田口 経験や勘、コツによる管理から、データによる管理に変わったわけですね。
宮田 それまでは、手書きやヒアリング、ストップウォッチを使った計測で記録していましたが、すべて自動化しました。これにより、一人ひとりの作業時間が収集されるので、管理者はどの作業が速いか遅いかがわかりボトルネックの改善がしやすくなったうえ、一定の時間でバランスよく製品を組み立てられるようになりました。2020年5月に稼働してから半年で、サックスの組み立て工程の生産性は16%向上しています。
田口 ビーコンの活用はどうやって思いついたのですか。
宮村 技術自体は世の中にあったので活用方法を探っていて、スマートファクトリー推進グループのメンバーと議論を重ねる中で、モノに付けて作業台に受信機を置けば動きがわかるという発想にたどり着きました。産業用なのでメンテナンスや保守に関してあまり心配はありません。ただ、タグは約1年単位に電池交換が必要なのですが、電池残量は遠隔でモニタリングできるので、ランプがついたら現場サイドで交換してもらっています。導入後も、思ったより保守に手はかかっていません。
ギターの組み立て工程でデジタルツインの概念実証
宮田 コロナ禍以降は、ギターの組み立て工程におけるデジタルツインの概念実証を始めています。
田口 こちらの取り組みは、どういった経緯で始まったのですか。
宮田 ビーコンの活用を水平展開する予定でしたが、コロナ禍により導入を見送ることになったのです。そこで、需要が戻るまでの間にヤマハ工場のデジタルツイン化を構想企画し、工場から得られる情報をデジタル空間上に再現するデジタルツインは本当に効果があるのか、何を使ってどのように実現するか、製造現場でどのように活かされるのか確かめたいと考えました。
田口 どういった効果を期待していますか。
宮田 多くの企業はシミュレーションなどに活用しますが、私たちはもっと現実的で、遠隔で生産管理を行えるようにするのが目標です。要するに、リモートで生産管理を実現したいと考えています。通常は人が3現主義(現場・現物・現実)でコントロールしなければなりませんが、それをデジタル上でできるようにするのが狙いです。そうすれば、その工場だけでなく遠隔で多くの人の手と知恵が借りられます。また、生産現場の情報をデジタル化すれば、誰かが紙でメモを取り、そのメモを誰かがExcelに転記し、それを誰かが報告するといったプロセスも一気にデータ化ができると考えています。
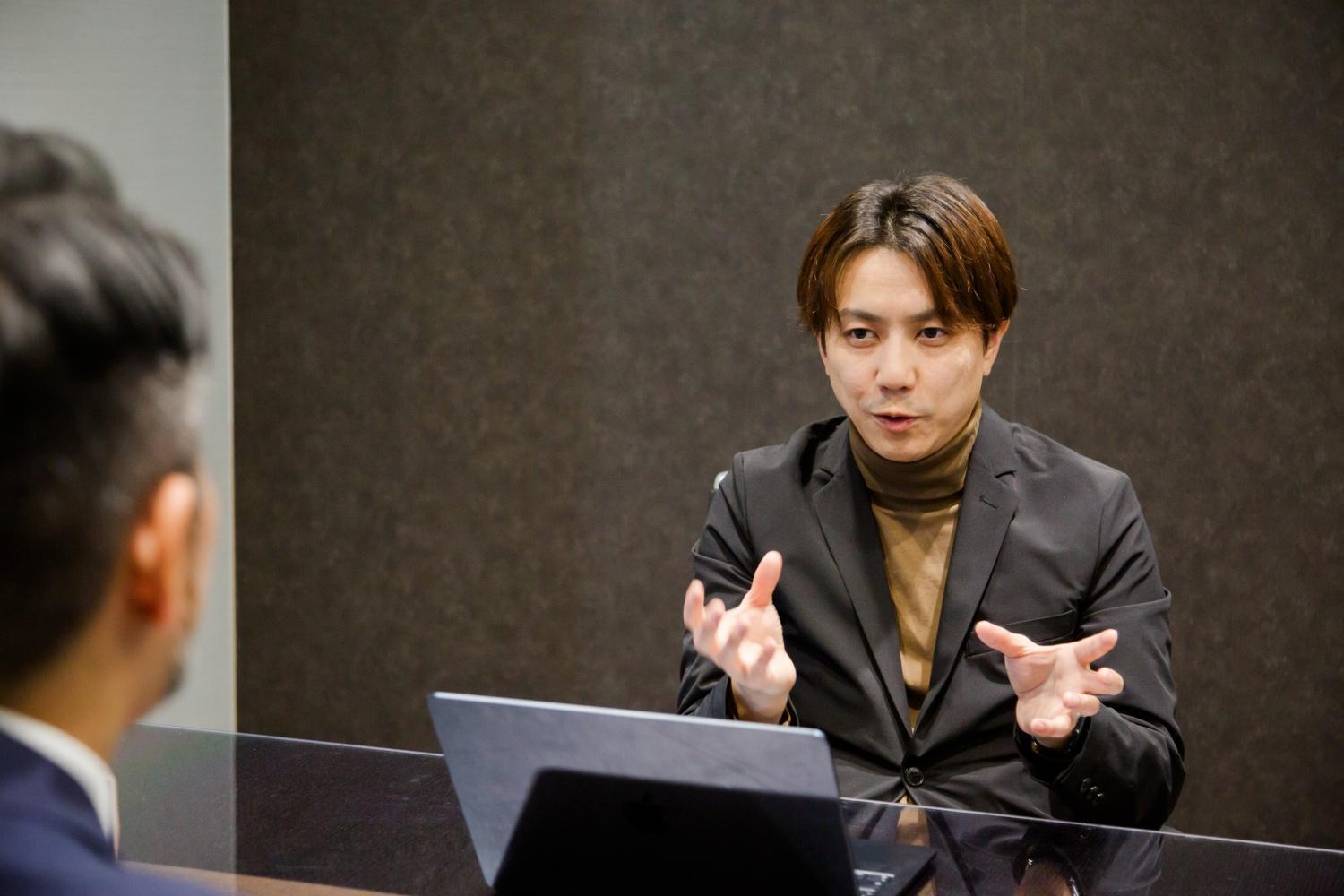
田口 現実感があり、地に足のついた活用法です。先ほどおっしゃっていた、課題があり、それを解決しようというアプローチも感じました。
宮田 デジタルツインを導入するとあんなことも、こんなこともできるといった夢物語ではなく、現場の課題感を盛り込む必要があります。今回も今までに我々が現場で経験した課題を仕様にすでに詰め込んでいますので、現場ですぐに使ってもらえることを目指しています。
田口 概念実証中とのことですが、肌感としてうまくいきそうですか。
宮田 ギターの製造は飯田工場と掛川工場の2ヵ所で行っており、移動には車で30分ほどかかります。工場が分断されると情報も分断されるので、そこをデジタルツインでつなげば、遠隔で製造にかかわる情報を把握することができます。遠隔で情報を見て活用するニーズはどの工場にもあるので、うまくいくという実感はすでにあります。
とりわけ海外の工場は日本の比でなく、インドネシアであれば広大な敷地にいくつも建屋があり、4000人の従業員が務める工場があります。製造工程や人の動きは複雑でわかりづらいのですが、情報をつなぎタブレットやパソコンで見られるようにすることで意思決定が速くなり、人手が足りないなら応援を出すなど、リソースのやりくりもスムーズになるでしょう。そういった効果を期待しています。
今後、国内外13工場に導入するスケジュールは決まっていて、中国とインドネシアではそれぞれ1工場への導入準備を始めており、来期から稼働する予定です。
工場からのたたき上げをデジタル人材に育てたい
田口 各工場でデジタルツインを導入するには、多くの人材も必要なはずです。
宮田 現状、スマートファクトリー推進グループには11名しかおらず、人手が足りません。そこで、デジタル人材の育成・活用戦略を立て始めており、中国とインドネシアは工場が多いので現地で育成・展開する体制の構築を進めています。
田口 デジタル人材の補完に関しては、社内から人材を募る、採用する、あるいは専門家を頼るなど、どのような方針を考えていますか。
宮田 工場からのたたき上げが良いと思っています。現場に精通しビジネス課題がわかる人はITがわかる人より少なく、前者にITを学んでもらった方が人材育成のスピードは速いからです。ただし、優秀な人材はすでに多くの仕事を抱えていて、なかなかI獲得できません。技能や匠の技の継承に関しては手を打っていますが、デジタル人材に関してはなかなか進まず、今後の課題の1つです。
もちろん、キャリア採用も考えないといけないでしょう。外部を頼らないわけではありませんが、現場を知らないとコンサルティングができない状態なので、それなら自分たちで何とかしたいという考えがあります。
日本にいながら海外工場を管理できるように
田口 ビーコンもそうですが、御社はBIツールに『Motion Board』を使うなど、外部のツール・システムを採用しています。どうやって見つけているのですか。
宮田 ビーコンは展示会で見つけましたし、『Motion Board』は情報システム部がもともとライセンスを持っていたのですが使用していなかったので、譲り受けました。誰かに導入するよう指示されたりするのではなく、使いやすいものを自分達の手と足で見つけるというきわめて自然な流れで使い始めています。
ただし、ベンダーを選ぶ際はコンペを実施し、コストパフォーマンスだけではなく、過去の実績や誠実さなど、企業価値だけでは測れない人間性も含めて判断しています。ビーコンの導入時も5社ほどコンペに参加いただき、そのように決めさせていただきました。デジタルツインもこれからコンペを実施する予定ですが、選定基準は同様です。
田口 今後、目指すべき姿をどう思い描いていますか。
宮田 デジタルツインに関しては、中央監視室のような部屋のモニターに全工場の状況が表示され、ライブビューイングなどで現地の様子もわかるようにしたいです。加えて、相手の視線がわかりストレスなく会話などができる、遠隔用のコミュニケーションツールがあると良いですね。5年後、10年後には日本にいながら海外工場のマネジメントやコントロールができる状態になることを目指します。
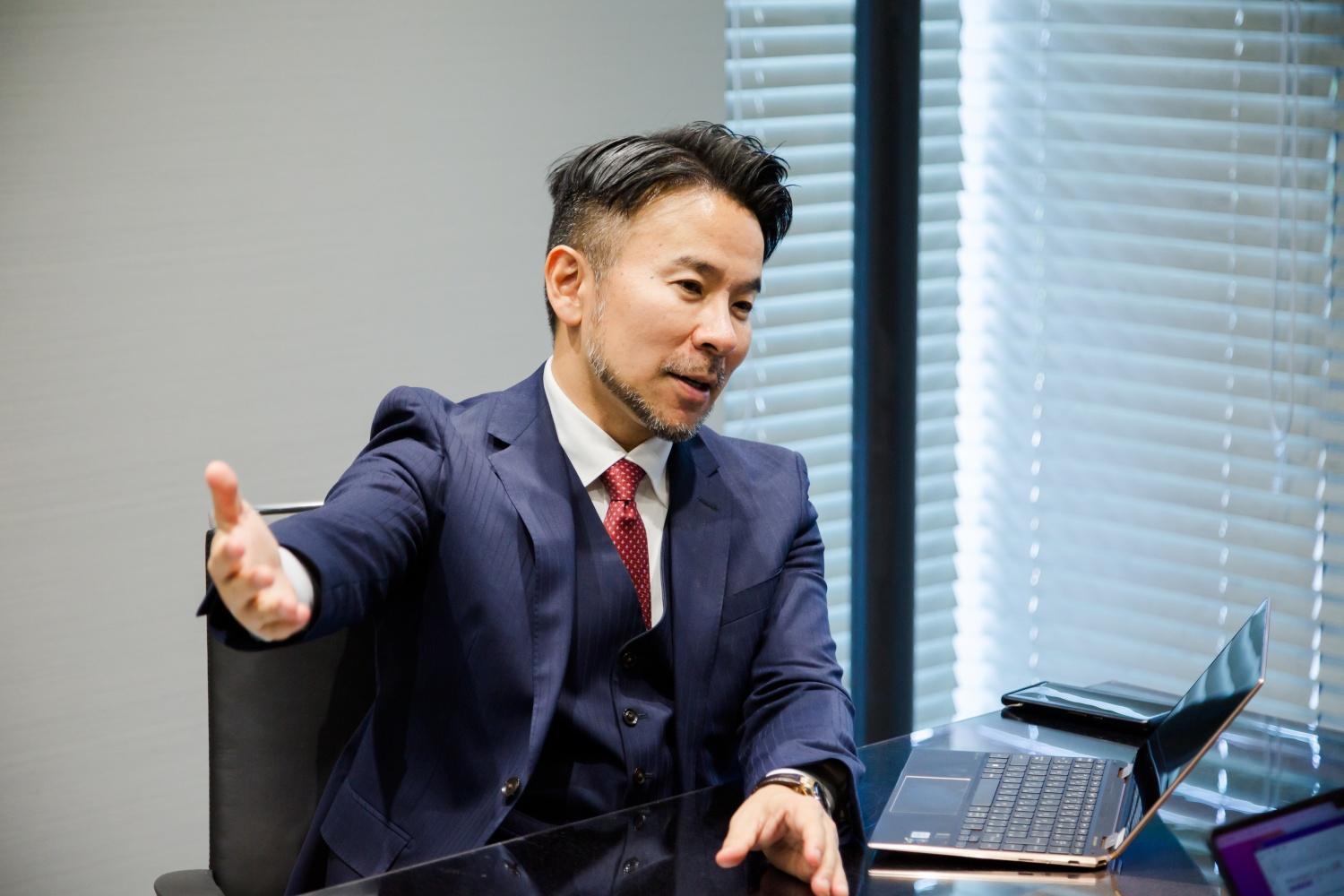
宮田 鹿島建設さんなどのデジタルツイン事例を拝見すると流石だなと感じますが、我々は誰でも・どこでも・必要な情報を・必要な鮮度と精度で情報活用できるデジタルツインを目指しています。導入を進めれば、そのデジタルツインを使って、遠隔地からでも相互コミュニケーションが取りたいなどの要望も出てくると想像しています。そのためにアンテナを高くしてデジタル技術や先進技術、最新ツールもリサーチしていきたいと思います。
田口 他にも何か課題はありますか。
宮田 日本ではデジタル関連どころか、人材そのものが不足しています。採用活動に力を入れるのはもちろん、私が所属するグループに現場スタッフを1~2年間異動させ、エバンジェリストになってもらい現場に戻すといった、人の育て方も個人的にはやっていきたいと考えています。
また、工場には私が生まれる前から使っている古い設備がたくさんありますが、図面がないので再発注は不可能です。設備の更新時は昔の機構は再現できず品質が変わるリスクもあるので、設備を導入するセクションは慎重に物事を進めていますが、その時に単に作り替え・置き換えるのではなく、IT化するようお願いしています。うまく他の部署の業務のなかにIoT化のための標準仕様エッセンスを入れてもらい接続性を確保しておくことで、今後のDXの導入推進に弾みをつけたい考えです。
田口 御社はDXで一定の成果を収めましたが、成功のポイントは?
宮田 DXは今始まったことではなく、デジタルを活用した施策は昔からありますし、新しいツールができるとプロセスは勝手に変わります。本来は業務プロセスを描いてからシステムを作るのが理想ですから、まずは課題を特定すること。次に、現場サイドが実行できるオペレーションを設計することがポイントだと思います。きちんと仕組みを作り相手に提供することが、使ってもらうための仕掛けです。
そして、できたものを渡しっぱなしにするのではなく、サポートも含めて伴走することも忘れてはなりません。安定するまで面倒を見るのも、DXを成功させるコツだと思います。
田口 最後に、Koto Onlineの読者にメッセージをお願いします。
宮田 欧州ではインダストリー4.0、今は5.0かもしれませんが、機械が相手なので情報が取りやすい環境だと思います。一方、我々は人に主眼を置き、技能伝承などにデジタルを活用したいとも考えています。こういった取り組みを面白いと思う方とは、ぜひ一緒に仕事をしたいと思います。同じ課題を持つ仲間と情報を交換し、協業しながら新しいことにチャレンジしたいので、興味がある方はお声がけください。
田口 宮田さんがおっしゃる通り、DXに対する課題を持つ企業はたくさんあります。連携することで、大きなイノベーションに発展するかもしれません。本日はありがとうございました。
【関連リンク】
ヤマハ株式会社 https://www.yamaha.com/ja/
株式会社コアコンセプト・テクノロジー https://www.cct-inc.co.jp/
(提供:Koto Online)