近年は物流の2024年問題といったサプライチェーンに関わるニュースを聞く機会が多くなっています。特に製造業においては、業務効率化や在庫管理の観点でデカップリング・ポイントという考え方が非常に重要となるでしょう。デカップリング・ポイントは、簡潔に表現すると見込み生産と受注生産を切り替える基準となる在庫数です。
本記事では、ビジネスでサプライチェーンに関わる方に向けて、デカップリング・ポイントの概要を始め、その決め方や改善事例を含めて解説します。
目次
デカップリング・ポイントとは
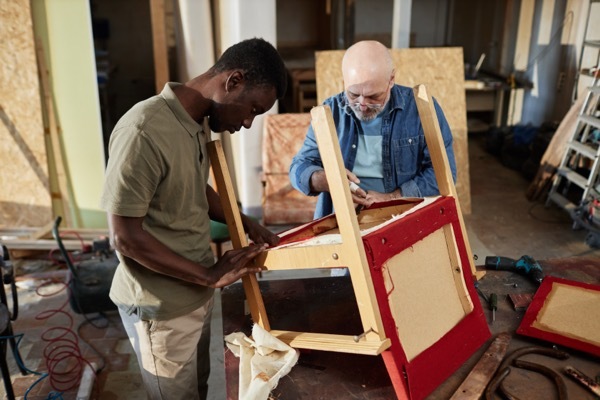
デカップリング・ポイントは、製造プロセスにおいて、見込み生産と受注生産の切り替えを判断する基準点です。デカップリングは日本語で「分ける」「分岐する」という意味を持ちます。具体的には、見込み生産から受注生産に切り替えるタイミングで在庫が発生する時点がデカップリング・ポイントです。
例えば、ある製品の製造工程において部品調達までは計画に基づいた見込みで行い、組み立て工程以降は受注生産に切り替える場合、部品調達と組み立て工程の間にデカップリング・ポイントを置いているといえます。そして、部品調達までは見込みで行われるため組み立て前の部品については注文が来るまで在庫となります。
デカップリング・ポイントの考え方は、物流の効率化や在庫管理の観点で非常に重要な概念といえるでしょう。
デカップリング・ポイントとストック・ポイントの違い
デカップリング・ポイントの類似概念として、ストック・ポイントがあります。デカップリング・ポイントが「工程のどの時点で在庫を持つか」に着目するのに対し、ストック・ポイントは「どこに在庫を置くか」に焦点を置いた考え方です。ストック・ポイントの具体例としては、原材料の倉庫や最終製品の保管場所が挙げられます。
ストック・ポイントは業界や扱う製品によって、物流センターや店舗などさまざまです。サプライチェーンの検討においては、ストック・ポイントをどこに設けるかという点に加えて、どれだけの数を設置するかも重要なテーマです。
受注生産と見込み生産の違い
受注生産 | 見込み生産 | |
---|---|---|
生産タイミング | 顧客から注文が入ってから | 顧客からの注文の前 |
在庫 | 持たない | 持つ |
コスト | 高コストになりやすい | 低コスト |
納期 | 長くなりやすい | 短い |
需要予想や販売計画 | しない | する |
リスク | 不測の事態に対処しづらい | ニーズの変化に対応しにくい |
デカップリング・ポイントを理解するためには、受注生産と見込み生産についても知っておく必要があります。
受注生産は顧客からの注文があった時点で生産が開始される生産方式です。身近な具体例としてはオーダーメイドの家具が挙げられます。例えば、顧客が特定の寸法やデザインの家具を注文した場合、メーカーは注文に基づいて生産を開始します。受注生産であれば特定の素材、色、デザインのソファやテーブルなどが注文された場合、その商品を作る前に注文を受けることが一般的です。
一方で、見込み生産は予測や市場の需要予測に基づいて事前に生産を計画する生産方式です。ここでも見込み生産の具体例を見てみましょう。家電業界では、季節や新製品の発売時期によって需要の変動が大きいことがあります。例えば、エアコンや暖房器具は季節ごとに需要が変動するため、需要の予測に基づいて一定数量を見込んで生産することが一般的です。
受注生産の特徴
受注生産の大きな特徴は、顧客からの注文を確認して初めて生産が開始されることです。注文を受けてから生産を開始するため、余分な在庫を最小限に抑えて顧客の注文内容に細かく対応できることが受注生産の大きなメリットです。また、受注生産は顧客のニーズに合致した製品やサービスを提供できることから顧客満足度の向上につながる可能性も高いでしょう。
一方で、注文があるまでは生産に着手しないことから、短期間で多数の注文が来る、部品が一時的に枯渇しているといった不測の事態に対処しづらく、納期が長くなる可能性があります。また、注文内容によって生産プロセスを変更する必要が出た場合は、その調整コストが大きくなる可能性にも注意が必要です。
製品や顧客の性質によって受注生産が適する場合とそうではない場合があるため、慎重な検討が必要になるでしょう。
見込み生産の特徴
見込み生産は、一定期間内の需要予測に基づいて生産される方式です。特に同じ仕様や規格を持つ製品を大量生産する際に、見込み生産方式が採用されることが多いでしょう。見込み生産方式を採用すると、需要予測に基づいて生産しますのでニーズの変化にでき、在庫数を安定させることが可能です。また、同じ仕様を持つ製品を大量生産することから、一貫した品質と低コストでの生産が可能になります。
一方で、事前の需要予測に狂いが生じると過剰在庫や供給不足に陥るリスクがあることに注意が必要です。また、見込み生産は仕様や規格が標準化された製品の生産を前提としているため、市場や顧客のニーズが変わった際に迅速な対応ができず、結果的にチャンスを逃してしまう可能性があります。
見込み生産も、受注生産と同じく一長一短があることから生産方式の検討は慎重に進める必要があるでしょう。
デカップリング・ポイントで変わるサプライチェーンモデルの分類
デカップリング・ポイントは先述の通り、生産工程の中で受注生産と見込み生産が切り替わるタイミングを指します。以下の表にある「設計」から「配送据付」までの生産プロセスにおいて、どこにデカップリング・ポイントを置くかで、それぞれ異なる生産方式が定義されています。
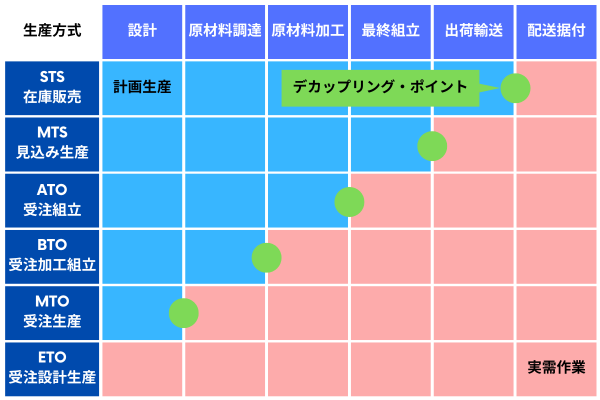
ETO:受注設計生産
ETO(Engineering to Order)は、製品が注文される度に設計工程から生産が行われる方式です。ETOの場合、注文と設計開始が同時であるためデカップリング・ポイントはありません。
ETOでは注文を受け手から設計を開始するため、顧客の要望に合わせて製品の仕様を変えることができ、在庫を最小限に抑えることが可能です。また、顧客の要望に対して柔軟な設計が可能なことから細やかなニーズに対応でき、顧客満足度の向上にもつながるでしょう。
一方で、顧客要望に幅広く対応するためには製造工程で人手が介在することになり、製造ラインの標準化や自動化は難しくなります。また、短期間で多くの注文が集中した場合や事前の需要予測が外れた場合には最終製品の供給までに時間を要する可能性があるでしょう。
MTO:受注生産
MTO(Make to Order)は、顧客からの注文があった際に原材料の手配から生産を開始する手法です。MTOのデカップリング・ポイントは「設計」と「原材料調達」の間にあります。
MTOは製品の種類が多く、かつ散発的に注文が入る場合に適した手法です。また、顧客から細かく仕様が指定される製品についてもMTOが向いているでしょう。在庫管理の面でも注文を受けてから原材料を手配するため、基本的に注文数以上の在庫を持たないことから過剰在庫のリスクは低いといえます。
一方で、注文がない場合は生産ラインの稼働が止まり組織全体の生産性が落ちる可能性があります。また、注文を受けて初めて原材料の手配を行うことから短納期の注文には対応できないこともあるでしょう。
BTO:受注加工組立
BTO(Build to Order)は、顧客からの注文があってから完成品の生産を行うという点では、後述のATOと類似した生産方式ですが、注文前に在庫として保持するものが部品やモジュールなどの原材料であることが特徴です。そのため、BTOのデカップリング・ポイントは「原材料調達」と「原材料加工」の間になります。
BTOを採用することにより、原材料のみを在庫として持つため、中間部品の在庫が不要となります。一方で、原材料は事前に確保しているものの、受注があってから生産に着手するため他の生産方式に比べる納期がやや長くなるというデメリットがあります。
ATO:受注組立
ATO(Assemble to Order)は、主に製造業で採用される生産手法の一つで、製品が顧客からの注文に基づいて組み立てられる生産方式です。この方式では、事前に完成品として在庫を保持するのではなく、受注があった時点で事前に調達した共通部品やモジュールを組み立てて、完成品として出荷します。ATOのデカップリング・ポイントは「原材料加工」と「最終組立」の間です。
ATOでは受注があったらすぐに組立工程から生産を始めるため、製品出荷までのリードタイムを短縮できます。一方で、完成品として出荷できるまでの組立に時間を要する可能性があり、組立工程の効率化が必須となるでしょう。
MTS:見込み生産
MTS(Make to Stock)は、製造業における生産方式の一つで、需要予測に基づいて事前に製品を生産し、在庫として保管する方式です。この方式では、デカップリング・ポイントが「最終組立」と「出荷輸送」の間に置かれています。MTSでは、顧客からの注文が入る前に製品が完成しているため、比較的短い納期で注文に対応することが特徴です。
MTSは仕様や規格が標準化された製品に適しており、需要の予測がしやすい場合に有効な手法です。一方で、需要予測の誤差による過剰在庫や供給不足のリスクが懸念されます。MTSを採用するにあたっては、市場のニーズが安定していることと、個別要件が少なく仕様が標準化された製品を扱うことが前提となるでしょう。
STS:在庫販売
STS(Sell Through Stock)は、小売業で使用される在庫管理手法の一つです。STSでは、商品が店舗に入荷された際に、直ちに販売可能な状態で陳列され、比較的短期間で完売することを目指します。この方式では、デカップリング・ポイントが「出荷輸送」と「配送据付」の間に置かれています。
例えば日用品や食品を販売するスーパーでは、新しい商品や季節限定商品が店頭に並べ、食品の賞味期限などを考慮して販促を行うことが一般的です。また、書店においてもベストセラーの書籍や話題の漫画などを目立つ場所に陳列して、購買意欲を促進するといった施策が行われます。
STSにおいては、短期間での売上アップを目指すため、リアルタイムでの需給データ分析や迅速な商品補充が重要になります。
デカップリング・ポイントの決め方
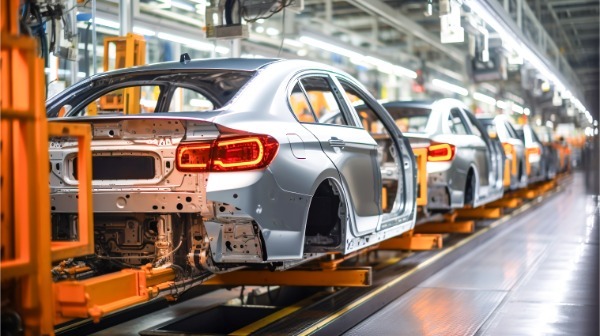
デカップリング・ポイントをどこに置くかでサプライチェーンの在り方が変わります。ここでは、デカップリング・ポイントを決める具体的な方法について解説します。
生産工程、商品特性によって決める方法
デカップリング・ポイントは生産工程や製品の特性によって決めることができます。具体的には、注文から製品出荷までのリードタイム、製品の共通性、保管期限の3つがデカップリング・ポイントを決める際の重要な要素となります。ここでは、それぞれの要素におけるデカップリング・ポイントの決め方を紹介しましょう。
製品出荷までのリードタイム:部品サプライヤーからの供給に時間がかかるなど、製品出荷までのリードタイムが長い場合は、できる限りデカップリング・ポイントを工程の前半に置くことで過剰在庫や供給不足のリスクを低減できます。
製品の共通性:製品の仕様や部品の共通要素が多い場合、デカップリング・ポイントを工程の後半に置くことで、急な注文にも迅速に対応できるでしょう。
保管期限:食品など保管期限が短いものは、デカップリング・ポイントを工程の後半に置いて可能な限り在庫として滞留する時間を短くすることが重要です。
成り行きで決める方法
生産工程や商品特性でデカップリング・ポイントを決めにくい場合は成り行きで決めるという方法もあります。具体的には、中長期での販売計画に基づいた部品の調達や生産を行い、在庫が発生しやすい工程をデカップリング・ポイントとしては特定する方法です。
一見、デカップリング・ポイントを適当に決めているようにも見えますが、在庫が発生するタイミングを探るという意味では理にかなった方法であるといえるでしょう。
デカップリング・ポイントを活用するコツ
デカップリング・ポイントを活用するためには、製品ではなく仕掛品で在庫を持つことがおすすめです。仕掛品とは最終製品として完成する前の製品を指します。
生産される品目によりますが、1つの仕掛品は複数の最終製品に組み立てられるケースがあります。そのため、最終製品を在庫で持つよりも仕掛品の在庫を持つ方が、事前の需要見込みが外れた場合でも他の最終製品に流用できることから、過剰在庫や供給不足のリスクを下げることが可能です。
デカップリング・ポイントの改善事例
大手PCメーカーのデルでは、「デル・モデル」と呼ばれる生産方式で製造工程の大幅な改善に成功しています。「デル・モデル」はBTOの考え方を採用した生産方式であり、「原材料調達」と「原材料加工」の間がデカップリング・ポイントとなっています。「デル・モデル」は現在では多くのPCメーカーが採用していますが、始まった当初は画期的な手法として注目されました。
「デル・モデル」においては、PCを構成するハードディスク、メモリ、CPUといった部品を注文の段階で顧客自身が選択し、その選択結果に基づいて組立を開始します。そのため、最終製品の在庫リスクを抑える一方で、ハードディスクを始めとするPCの構成部品は原材料として事前に確保しているため、出荷までのリードタイムも短縮することが可能です。
また、「デル・モデル」における顧客からの注文は1990年代では珍しくポータルサイトを通じて行われる方式でした。このように、IT技術が社会に浸透し始めていたことも「デル・モデル」が大きく普及した一因といえるでしょう。
まとめ
デカップリング・ポイントは、生産工程の中でどの部分で在庫を持つかを決めるための考え方です。サプライチェーンの効率化を検討する上で、デカップリング・ポイントをどこに置くかは非常に重要なテーマといえます。最適なデカップリング・ポイントは、扱う製品、製造ラインの特徴、顧客ニーズによって常に変わることから、継続的な改善と検討が求められるでしょう。
(提供:Koto Online)