「7つのムダ」とはトヨタ生産方式から生まれた、製造現場を効率化し、より良くするための手法です。現場のムダを「か・ざ・つ・て・ど・う・ふ(飾って豆腐)」の頭文字から始まる要素7つに分類したうえで、現状の「ムダ」を洗い出して見直しを行い、排除することに役立ちます。この記事では7つのムダの由来と定義、内容とそれぞれのムダの例、企業における7つのムダの排除方法について解説します。
「7つのムダ」とは?
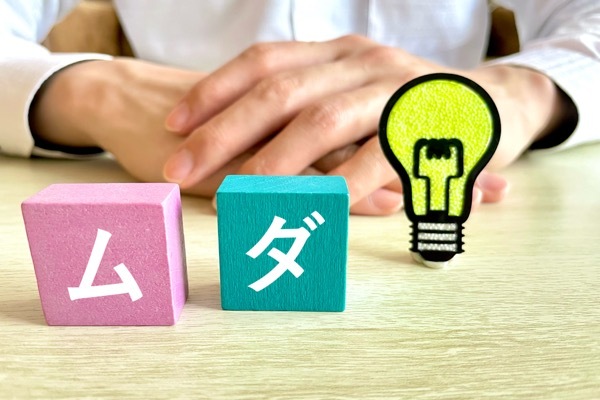
はじめに、7つのムダとは何か、概要を解説します。
「7つのムダ」とは
「7つのムダ」とは、トヨタ生産方式で定義された「製造現場におけるムダ」の7つのカテゴリーを指します。これらのムダを徹底的に排除することで、生産効率を大幅に向上させ、コスト削減を実現することができるという考え方です。
トヨタが唱える「ムダ」の定義とは|トヨタ生産方式における「ムダ」
ところで、そもそもトヨタが考える「ムダ」とは、何を指しているのでしょうか。一般的な用語としての「無駄」の意味は、「役に立たないこと、余計なこと、効果がないもの、不要にぜいたくなものや様子のこと」などがあります。しかしトヨタのいう「ムダ」はこの定義とは異なります。
「ムダとは、ある場合は在庫であり、ある場合は作業そのものであり、ある場合は不良であり、それぞれの要素が複雑にからみ合い、ムダがムダを生み、やがては企業経営そのものを圧迫します。」
(出典)TOYOTA「トヨタ生産方式」
もともとトヨタ生産方式におけるムダの概念は、「「異常が発生したら機械がただちに停止して、不良品を造らない」という考え方(トヨタではニンベンの付いた「自働化」といいます)と、各工程が必要なものだけを、流れるように停滞なく生産する考え方(「ジャスト・イン・タイム」)の2つの考え方\」から生まれたものといえます。
*(引用元)TOYOTA「トヨタ生産方式」
トヨタ生産方式とは
ここで、あらためて「トヨタ生産方式」について少し解説します。トヨタ自動車が長年の「カイゼン(改善)」を積み重ねて確立した効率的な生産方式ですが、その特徴は「2つの柱」にあります。2つの柱は「ジャストインタイム」と「自働化」です。
ジャストインタイム
必要に応じて、必要なものを、必要なタイミングで生産する方式。在庫の削減、リードタイムの短縮、コスト削減を実現する。
自働化(にんべんのついた働)
異常発生時に自動的に停止し、不良品の発生を防止する仕組み。品質向上、安定稼働、人件費削減に貢献できる。
トヨタ生産方式はこの2本の柱をもとに「ムダ、ムラ、ムリをなくす」ことを基本理念とした生産方式です。
お客様のために良いものを、より早く、より安くお届けする
働く人のために、より働きやすく楽にする
そのために、ムリ、ムラ、ムダをなくす
この「ムダ」をさらに突き詰めると、生産プロセスにおいて発生する「製品を作る上で付加価値を生み出さない作業」を指します。ムダを排除することで、効率性を向上させ、コスト削減や生産性の向上を図ろうとするこの考え方をトヨタでは推進しており、日々の業務や製造品の改善に役立てています。
なお、トヨタ生産方式は世界中の製造業に大きな影響を与えたと言われています。例えば「リーン生産方式」は、米国の大学教授がトヨタ生産方式などを参考に研究して一般化した生産方式です。トヨタ生産方式は単なる生産方式ではなく、経営哲学と言えるでしょう。
トヨタの「自”働”化」とムダの関係
上記のとおり、トヨタのいう「自働化」とは、異常が起きたときに機械が止まることを実現させるシステムを指します。自働化を実現するには、徹底して、まずは人がこだわって手作業でものや仕組みを作り込み、誰がやっても同じようにできる作業までシンプルにわかりやすく洗練させ、機械が実際に行う作業レベルに落とし込まなければなりません。これをトヨタでは「ムダ・ムラ・ムリを徹底的になくす」と表現しています。
このこだわりと作り込みを繰り返すことで、よりよい製品をより早く顧客に届けられるとしています。そして、この「ムダ・ムラ・ムリ」の中の「ムダ」を、さらに細分化したものが「7つのムダ」ということになります。
「7つのムダ」の考え方は、現在は製造業だけでなくあらゆる分野で活用できる考え方として広まっています。ムダを減らすことで効率化、コスト削減、顧客満足度向上など事業に良い影響を与え、成果を期待できるとして注目を集めています。
トヨタ生産方式が唱える7つのムダ
ここでは、トヨタ生産方式において重要視されている「ムダ」のうち、トヨタが唱える7つのムダについて解説します。
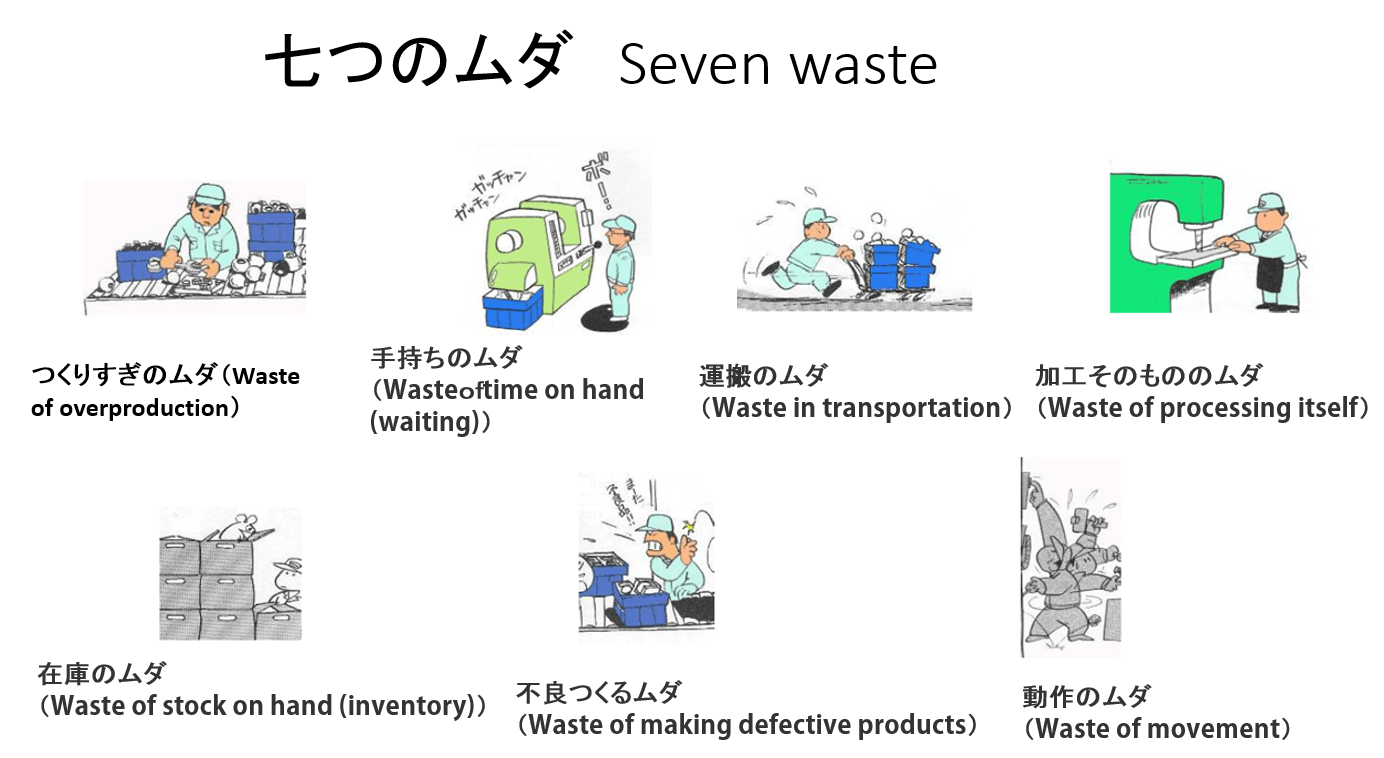
トヨタグループでは「か・ざ・つ・て・と・う・ふ(飾って豆腐)」というふうに、7つのムダの先頭の文字をとって覚えやすく紹介しているそうです。以下で、それぞれについて説明します。
(1)「か」加工のムダ(本来の仕事の完成度に直接関係しないのにリソースを使うこと)
(2)「ざ」在庫のムダ(不要な在庫や備品を保有すること)
(3)「つ」作りすぎのムダ(計画性なく必要以上に多く生産したりタイミング早く製造したりすること)
(4)「て」手待ちのムダ(不要な時間・やることがない状態が発生すること)
(5)「と」動作のムダ(付加価値を生まない動きのこと)
(6)「う」運搬のムダ(付加価値を生まないモノや情報の流れのこと)
(7)「ふ」不良・手直しのムダ(不良品や手直しが必要な仕事をすること)
(1)「か」加工のムダ(本来の仕事の完成度に直接関係しないのにリソースを使うこと)
製品に付加価値をもたらさない過剰な加工を行うことや、加工時間のムダを指します。これは、良品を必要な仕様どおりにスムーズに作り出していることが理想と考えると、それ以外の加工作業はすべてムダとなります。
例えば、過去からの慣例で特に意味はないけれど続けている加工や作業なども、ムダと考えられます。なぜその加工を行うのか、本当に必要なのかを考えなければなりません。必要以上に検査を行うことも同じく加工のムダです。
また開発部署での仕様変更が場管理者まで伝わっておらず、無駄な加工をずっと続けていたということも起こり得ます。これも加工のムダといえるでしょう。
(2)「ざ」在庫のムダ(不要な在庫や備品を保有すること)
この場合の「在庫」とは、「原材料」「部品」「仕掛品(しかかりひん)」「完成品」を指します。どうしてその物品がそこに在るのか、それが説明できない場合は全て「ムダ」になります。
例えば「多めに在庫をもっておいた方がミスや不確定な要素に対してすぐ対応でき、安心できる」という理由で原材料や部品を多く調達しているケースがあります。しかし「ミスが起きたら予備の在庫を使えばいい」という考え方は、ミス自体を起こしやすい企業風土をつくります。
そもそも、必要以上の在庫を持つと資金やスペースを占有します。さらに他のムダを誘発して製造工程全体に影響を及ぼすおそれがあります。
(3)「つ」作(造)りすぎのムダ(計画性なく必要以上に多く生産したりタイミング早く製造したりすること)
需要以上に生産された製品や部品が存在する場合、その分は無駄な生産として過剰在庫につながります。作り過ぎた製造品に使われた原材料、製造の過程で使う燃料や時間、人と手間、それらに消費されたコストなどがムダになります。さらには作り過ぎた在庫を置く場所や場所代、その場所を使うことで他の製品が置けなくなる不都合、多く作り過ぎたために他の製造に移れず発生する手待ち時間など、その無駄な製造品一つのために多くの「ムダ」が発生することになります。
顧客の需要に合わせて生産量を調整する、生産計画を精緻化するなどの方法が考えられます。なお需要に合わせて生産量を最適化するには、製造工程を一貫して管理できるよう、IT化が必須となります。
(4)「て」手待ちのムダ(不要な時間・やることがない状態が発生すること)
機械が稼働しない時間や、作業者が次の作業までやることがない待ち時間を手待ちと呼びます。手待ちのムダは作業効率や生産性を下げる原因となります。
例えば原材料の配送が予定より遅れてしまったり、前工程に遅れが出て後の工程にしわ寄せが出てしまったり、機械の呼称や不具合で生産計画通りに進められていなかったり、というケースが考えられます。
手待ち時間のムダを減らすには、作業手順の現状把握と改善、作業の並行化と最適化、作業工程の可視化を進めるなどの方法があります。
(5)「と」動作のムダ(付加価値を生まない動きのこと)
生産ライン・製品や部品の運搬・その他において、不必要な動作や操作が発生する場合、動作のムダと呼ばれます。作業動線や運搬動線が効率化されていないケースのほか、作業員の数と工具の数が見合っていなかったり、保管場所が適正に管理されていなかったりして必要なときにその工具が探し出せず時間と手間がかかってしまうことも動作のムダといえます。
作業者の動作を効率化するためには、作業動線の改善・作業工具や機器の保管・管理の効率化が必要です。
(6)「う」運搬のムダ(付加価値を生まないモノや情報の流れのこと)
製品や部品の移動や運搬において、不必要な移動や輸送が行われる場合、運搬のムダが発生します。
そもそも、製造工程において「運搬」は付加価値を生まないプロセスです。運搬することで人や燃料、手間や時間、運搬機器を消費(劣化含む)しますが、その工程自体で何かを生み出すことはありません。そのため「可能な限りスムーズに流れが良くなる」「時間を短くする」「回数を減らす」「空っぽで運搬せず稼働率を上げる」ことを考えなければなりません。もっといえば、「可能なら、運搬しなくてもよい仕組みを考える」ことが必要といえます。
しかし運搬は製造と販売においては必須といえるため、理想としては「必要数量をそのつど運搬する」「可能な限り運搬距離を短縮する」となります。ただし理想どおりにはいかないことの方が多いため、その現場(職場)に合った運搬の方法を使い分けられるよう、改善とフィードバックの繰り返しが重要になります。また自動搬送システムなどの導入でコストやリソースのムダを省く方法もあります。
(7)「ふ」不良・手直しのムダ(不良品や手直しが必要な仕事をすること)
製品や部品に不具合や欠陥が見つかり、手直しが必要となる場合、不良・手直しのムダが発生します。不良品が発生すると、その製品に関係するすべての部署が連携しつつ、顧客対応や製造ラインの見直し、不良原因の特定などを行います。また回収の必要がある場合はそのためのコストがかかります。改修した製品の廃棄にもコストと人件費がかかるでしょう。営業担当者は本来の営業活動はできず、顧客への説明にリソースを割かなければなりません。収束までに多くの時間がかかるため、本来の事業の生産性や製造物の品質が低下する可能性もあります。
このような大きな影響を与える不良のムダをなくすためには、品質管理の徹底が必要です。各工程が独立し連携が取れていない場合、意思疎通ができないため不良品や手直しが発生しやすくなります。何が原因で、どの課程で不良が発生したのか原因を究明し、フィードバックを各ラインに適用させたうえで、品質管理の仕組みの改善なども必要となります。
7つのムダを排除する5つのステップ
7つのムダを排除するには、どうすればよいのでしょうか。ここでは7つのムダとして考えられる具体例(製造業に限らず)と、その改善方法についての進め方を考えます。おおまかな流れは以下のとおりです。
- 現場を徹底的に観察し、ムダを見つける
- ムダの原因を見つける
- 改善策を検討する
- 改善策を実行する
- 改善効果を測定し、継続的に改善を行う
【ステップ1】現場を徹底的に観察し、ムダを見つける
まず、ムダが発生している現状について具体的に把握することが重要です。以下の項目を観察し、見つけます。
7つのムダの種類
どのムダがどの程度発生しているのかを把握する。
ムダが発生している場所
どの部門、どの工程でムダが発生しているのかを把握する。
ムダが発生している原因
そもそも、なぜそのムダが発生しているのかを把握する。
【ステップ2】ムダの原因を見つける
ステップ1で把握したムダについて、原因を調べます。ムダの発生原因が何かわかったら、さらに、その原因を引きおこしているものまで徹底的に調べます。最も重要ですが、難しい作業です。
各「ムダ」の原因を見つけるためのポイントは以下を参考にしてください。
ムダの種類 | ムダの原因を見つけるポイント |
---|---|
加工のムダ | ・最新の図面と作業工程、仕掛品、完成品が一致しているか ・従業員が勝手に加工作業を増やしていないか、製造品にバラつきが出ていないか |
在庫のムダ | ・原材料・部品・仕掛品・完成品の在庫数は適正か ・現場判断で勝手に在庫を増やしていないか |
作りすぎのムダ | ・工程ごとの1日当たりの生産量は適正か |
手待ちのムダ | ・工程ごとの工数や必要な時間を調査 |
動作のムダ | ・工程ごとに作業者の一連の動作にムダはないか ・作業者にムダな動作がないかヒアリングを行う ・機器、作業ライン、従業員の配置は適正か |
運搬のムダ | ・原材料・部品・仕掛品・完成品の保管場所と移動にかかる時間や距離を確認する |
不良のムダ | ・製品ごとの不良品の発生率や工程戻りの率を調べる ・検査体制を調べる |
【ステップ3】改善策を検討する
作業手順の改善
作業手順を改善することで、動作のムダや運搬のムダなどを削減することができます。
設備の改善、更新などを行う
設備を改善することで、加工のムダや手待ちのムダなどを削減することができます。 ただしこれについては、設備投資費用や現在のシステムの改修費用などがかかる場合は、すぐ着手できない可能性が高いかもしれません。長期的な計画を立てて、「いずれ対応する」ではなく、具体的な日程まで決めて進めたほうが良いでしょう。
DXを取り入れ、工程を可視化し一元管理する
DXを取り入れ、製造工程に関わるすべてを一元管理できる仕組みに改善していくことも求められます。一元管理にすると部品調達から在庫管理までがシームレスに連携でき可視化されるため、「在庫のムダ」「作りすぎのムダ」も削減できます。
レイアウトの改善を行う
設備や従業員の配置(レイアウト)を改善することで、動作のムダや運搬のムダなどを削減することができます。このときのレイアウト変更についても、データをもとに論理的に改善することが大切です。また実際に現場で動く立場の従業員の意見も集め、フィードバックします。
【ステップ4】改善策を実行する
検討した改善策を実行します。
小さな改善から始める
最初から大きな改善をしようとすると、失敗する可能性が高いです。まずは小さな改善から始めて、徐々に改善を積み重ねていくことが重要です。
なお、トヨタ生産方式はトヨタという企業風土があって稼働している面もあり、トヨタ以外の企業がそのまま取り入れた場合はうまく馴染まないおそれがあります。このギャップを埋めるためにも「小さく始める」意識づけは大切です。
現場の意見を取り入れる
現場の意見を取り入れることで、より効果的な改善策を実行することができます。
【ステップ5】改善効果を測定し、継続的に改善を行う
改善策を実行した後に、時期を決めて定期的に効果を測定します。
目標を設定しておく
改善策を実行する前に、目標を設定しておきます。
データを収集する
改善策を実行した後、各データを収集し、目標達成度を測定します。
改善策の見直し
データをフィードバックし、目標達成度が十分でない場合は、改善策を見直しさらに改善を行います。
7つのムダを排除することは、簡単なことではありません。しかし、継続的に改善を積み重ねることで、大きな成果を上げることができるでしょう。
まとめ
この記事では、「7つのムダ」について解説しました。7つのムダとは、トヨタ生産方式において重要視される、生産プロセスにおける無駄や非効率な要素(ムダ)を7つに分類したものを指します。
7つのムダは、製造業に限らずあらゆる企業が抱えている問題です。また7つのムダの考え方は、業種によってさまざまに応用させることができます。7つのムダを徹底的に削減し最終的にはなくすことで生産効率を大幅に向上させ、コスト削減を実現することができます。簡単ではありませんが、現場の意識改革と継続的な改善活動を繰り返し取り組みましょう。
(参考)『すぐに使えるトヨタ生産方式 導入・実践ノウハウ集』竹内 鉦造(著),日本能率協会マネジメントセンター,2011年1月25日発行
(提供:Koto Online)