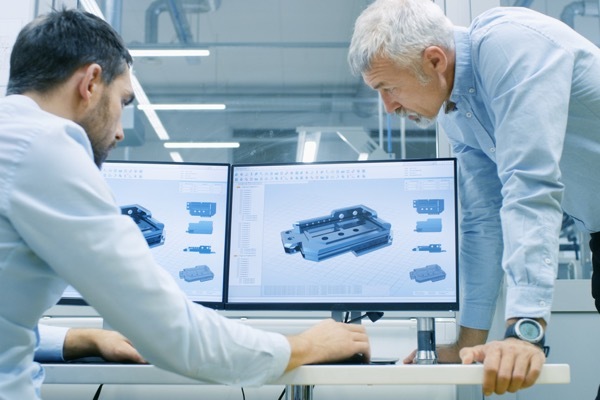
機械製品などを開発する製造業企業では、試作品にかかるコストや時間を低減させることが競争力の源泉となっています。そこで着目されるのがコンピューターで耐久性能などをシミュレーションする「CAE解析」という技術です。CAEは現在、自動車関連やエレクトロニクス分野にとどまらず、医療やエネルギーなどの分野でも活用されています。
CAEとは何か?
CAEはComputer Aided Engineeringの略語で、工学的問題を解決するためにコンピューター上でシミュレーションを行う技術およびソフトウェア製品のことです。構造力学や精密工学、流体工学などの理論を駆使して物理的な現象を計算します。それにより開発しようとしている製品のさまざまな環境下における耐久力などを把握します。また、実際に市場に出回っている製品で起きた物理的な不具合についてその原因を究明したりすることもできます。
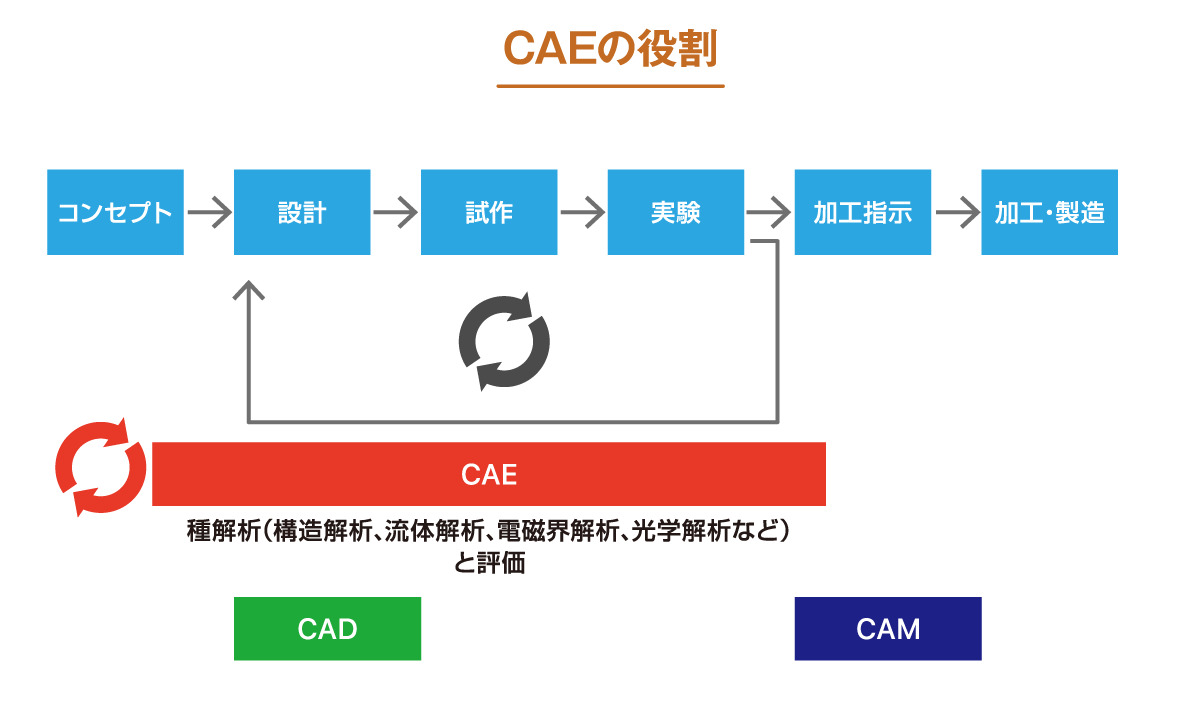
コンピューターで精密なシミュレーションができなかった時代は、自動車、医療用機械、電子部品などの開発には具体的に試作品を作り、それらにさまざまな条件を与えて耐久性や問題点を調べていました。そうした作業には時間もコストもかかり、また完成段階に近づいた状態になっても構造的な問題が発見され、開発工程で手戻りが何度も生じることがありました。しかしCAEを活用するようになって、そうした問題が大幅に軽減されるようになっています。
CAEが登場し、高度化していくことによって、さまざまなモノづくりの現場では、製造段階に進む前にその製品にまつわる多種多様な問題を解決できるようになりました。このことで、多くの企業は開発コストを低減させるとともに、最適なタイミングで製品を市場に投入できるようになり、競争力を向上させることができます。CAEは、製造業企業にとってなくてはならない技術といえるでしょう。
CAD、CAM、MBDとの違い
CAEとともに現代の製造業企業にとって欠かせない技術が「CAD」(Computer Aided Design)です。CADはコンピューター上で設計図面を作成するツールです。CADとCAEは開発において関係が深いものですが、同じ役割を担うわけではありません。
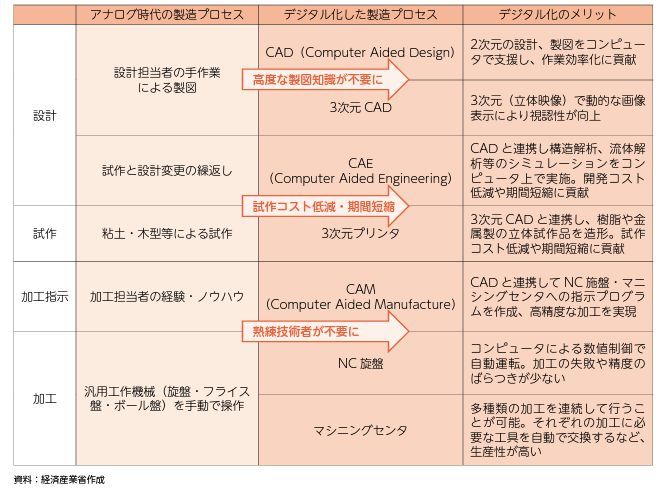
両者の決定的な違いは、CAEがシミュレーションを行い、さまざまな検証を行うツールだという点です。CADはデジタル化によって高度な製図知識や技能を不要にします。一方CAEは試作と設計変更の繰り返しを減らし、試作コスト低減・期間短縮を実現します。CAEはCADからのデータを活用してシミュレーションを行うこともあり、CAE機能を搭載したCAD製品もあります。
CAM(Computer Aided Manufacturing)は、工作機械などに用いるプログラムの作成に使用されるツールです。製品や部品の製造・加工を行う際、CADで作成した図面を基に、工作機械での高精度な加工に必要なNC(数値制御)や、工作機械専用のプログラムなどを作成します。また、CAEのシミュレーション・検証結果を考慮に入れてCAMの工程に進むことで、デジタルによる検証を経た、より精度の高い製造が可能となります。
MBD(Model Based Development)とは、「モデルベース開発」を意味し、従来の紙の仕様書を確認しながら設計と検証を行う開発方法とは異なり、ソフトウェアを用いてコンピューター上に「動く仕様書」と呼ばれるモデルを作り、開発と検証を同時に進められます。製品を作らずに検証できるため、テストや分析を納得するまで繰り返して品質向上につなげられると同時に、検証にかかる手間やコストが削減できます。
CAE解析とMBDは似たものとして認識されがちですが、MBDが製品の妥当性を検証する一方、CAE解析はコンピューター上で振動や温度などの条件をさまざまに変えながら、効率的にシミュレーションを行うためのツールと言えます。MBDは主に自動車業界で利用されてきましたが、他分野の製造現場でも今後ますます重宝されることでしょう。
CAE解析の種類
CAEはシミュレーションを行います。言い換えると、ある条件を数値化して解析するということになります。代表的なCAEの解析分野としては、構造解析、流体解析、電磁界解析、光学解析の4つが挙げられます。
構造解析
構造解析は固体力学に基づいた解析手法で、構造物に対する荷重や応力による変化(挙動や状態、安全性)を分析します。構造物にかかった負荷による破壊や倒壊、変形の状態を可視化して最適な部材や形状の選定に活用するわけです。CAEがない時代には、難しい構造計算や実際の実験によって検討していたのですが、CAEがあればそうした手間も必要ありません。
構造解析では、荷重によって生じる応力や変形の値をプログラムが計算します。そしてCG によって3次元形状や色で可視化します。こうしてわかりやすく可視化されているので、構造的な弱さや補強の必要な部位などを把握し、対応策を具体的に考えられるようになるのです。
構造解析の代表例は、自動車が何かに衝突したときの破損状況についてのシミュレーションでしょう。このほか地震が発生した時の建物の変形をシミュレーションして、耐震構造を検討するときなどにも利用します。
流体解析
流体解析は、気体および液体の流れや構造物に対する圧力の影響などを分析するときに利用します。流体力学を応用し、空気の流れによって変動する熱の移動などを解析し、こうした変動をCAEによって可視化します。
流体にはいろいろな種類があり、動きも極めて複雑になるため、流体解析で利用されるプログラムの種類は構造解析より多岐にわたります。
流体解析の活用事例としては、自動車のボディ周辺で発生する空気抵抗などの解析、電子基板上で熱源となっている部品からの空気の流れを解析して効率的な冷却方法を検討するなどが挙げられます。他に医療、環境、発電所といった幅広い分野で導入されている解析手法です。
電磁界解析
電磁界解析は、製造業の現場では電気や磁気に関するシミュレーションをする方法です。磁力や電気信号、電磁波を使用する製品や部品が対象となり、それらがどのように影響しあうのかを解析します。
電磁界とは、「電気のある空間」(電界)と「磁気のある空間」(磁界)が組み合わさった空間のことです。磁力や電気信号、電磁波は人体への影響も考えられるので、設計・開発段階での検討には欠かせない解析手法です。
電磁界解析は、膨大な時間や手間、コストがかかる試作品の代わりに、コンピューター上の仮想モデルを使ってシミュレーションできるので、試作品よりも簡単に、いろいろな試行錯誤ができます。具体的には自動車や飛行機のアンテナを設計するときや、医療機器や電子機器などを人が使用することを想定したときに使われます。
光学解析
光学解析では、高精度光学解析ソフトや光線追跡ソフトなどを利用し、光の反射や屈折、分散などの動きが対象物に与える影響など、あらゆる光のデータを解析します。CAEを活用することで光の明るさや色、照射範囲などを可視化でき、ライトなどの光源の配置や殺菌の効果を検討できるようになります。
カメラや眼鏡、顕微鏡などの開発では光学設計が欠かせません。光学設計は、光の性能を最大化、最適化するために行われます。レンズやミラーなど光学部品の形状を設計したり、照明やレンズなどの最適なレイアウトや機構を検討したりします。この光学設計を効率的に行うためにCAEが活用されるのです。
この解析手法は、水滴や霧、赤外光を考慮したシミュレーションも可能です。カメラのレンズ機構、自動車の車内照明やバックモニターの解像度や歪みの最適化などにも活用されます。
CAEの導入メリット
では、ここでCAEを導入することのメリットについて解説します。主たる導入メリットは、製品を設計・開発していく際のコスト削減と開発・製造段階での時間短縮です。
そのほかに資源の節約・環境への配慮を効率的に実施できることや、リアルでは再現できない環境でのシミュレーションができること、DXの推進に貢献することなどが挙げられます。
試作品関連のコストを削減
CAEを活用することでコンピューター上でのシミュレーションが可能になり、試作品を大量に作る必要がなくなります。試作品の制作コストだけでなく実験環境の構築にもコストがかかりますので、これらの節約効果は大きいものになります。
自動車1台には、3万個程度の部品が必要です。新車を開発するたびにすべての部品を設計するわけではないにしても、試作品の作成、実験にはかなりのコストがかかることは想像できます。また一般に自動車の試作には1車種につき10億円以上のコストがかかるとされています。そのことからも、CAEの導入効果は極めて大きいと考えてよいでしょう。
また、設計・開発段階でのコストは設計段階で8割が決まるとされています。例えば設計段階で発生したミスやエラーが、その後の試作段階の表面化すると、設計のやり直しなど、手戻りが発生して大きな損失につながります。こうしたことを可能な限り防ぐためにも、設計・開発の初期段階でのエラーを回避することが効率化につながります。そうした目的にもCAEは大きく貢献します。
開発および製造段階での時間短縮
自動車メーカーなどでは、設計・開発段階から保守点検まで一連の過程でCAEを活用することも珍しくありません。
まず、計者自身がCAEでシミュレーションすることで素早く技術的な問題の洗い出しを繰り返し実施できます。これにより1つの設計案件にかかる設計作業の時間を減らせるはずです。技術的な問題の洗い出しには、熟練技術者とのコミュニケーションが欠かせないとされていますが、CAEを使えば、検証できる項目を素早く増やし、問題解決のスピードも上げられます。
さらにCAE の結果を用いて課題の説明をすることで、関係者たちとの課題共有も迅速かつ正確に進みます。こうした設計者自身が行う CAE シミュレーションを「設計者 CAE」と呼ぶこともあります。
設計・開発段階で効率よく課題を見つけ、解決していくだけでなく、いざ製造段階に入ったときにどのような問題が生じる可能性があるのかをあらかじめシミュレーションで把握します。
設計・開発では視野に入っていなかった問題として、製造段階で材料の扱い方によって変形や劣化が生じるといった可能性も消すことはできません。そうした課題をあらかじめシミュレーションしておくことで、効率的な対策を打てます。
また同様に保守点検の段階で留意すべき点も同様にシミュレーションしておけば、製品のライフサイクル全体で、迅速で適切な対応を進めることが可能となり、すべてのプロセスで時間短縮が可能となります。
こうして各プロセスでかかる時間を短縮することで、より高度な作業に取り組むことも可能となり、品質を向上させることにもつながります。
資源節約など環境への配慮ができる
試作品や実験環境の構築には、時間やコストだけでなく、さまざまな資源を使い、CO2も発生することになります。これらの作業をCAE に置き換えれば、試作・実験工程をコンピューター上で行えるので、環境負荷を最小限にとどめることも可能となるはずです。
昨今、企業を取り巻く環境はGX(グリーントランスフォーメーション)など、環境に配慮することが重視されるようになってきました。もはや企業ごとのCO2削減は、単なる努力目標ではなくなりつつあります。設計から市場投入、廃棄までの製品にまつわるプロセス全体で環境負荷低減を経営方針として掲げる必要がでています。そうしたなか、CAE などデジタルでの設計開発、製造の試みは欠かせないものとなっています。
現実では再現しにくい条件でのシミュレーションが可能
CAEを使えば、リアルでは再現しにくい、極高温下や極低温下での耐久実験、真空状態や無重力状態下を想定した実験などもバーチャル空間で実施することが可能です。
極高温下や極低温下、真空状態などの環境は、リアルに再現しようとすると、特殊な施設を利用する必要があり、コストも時間も大幅に消費せざるをえません。
こうした設定でのシミュレーションは、解析担当者の高い技術力も必要となりますが、従来の検証では把握しにくかったアイデアを得ることも期待できます。
DX推進の効率化
CAE はデジタルツールの 1 つであり、デジタルトランスフォーメーション (DX) においても重要な役割を担うことが期待できます。
シミュレーション結果を可視化することで、技術系分野以外の部署の人たちや顧客・ステークホルダーに対しても分かりやすくこれから開発しようとしている製品を説明できます。またパンデミックなどが起きた際にも、CAEによる設計開発の取り組みによって、ビジネスを止めない施策を打つことが可能です。
昨今注目されている「スマートファクトリー」「デジタルツイン」といった試みを進めていく際にも、CAEの技術は欠かせません。
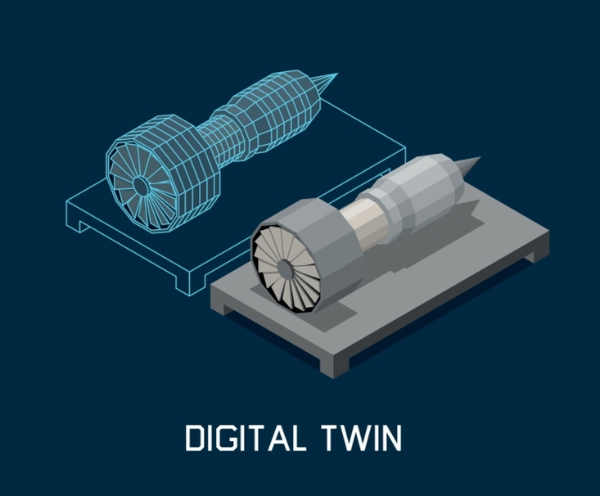
デジタルツインは、現実世界と仮想空間双方の情報を相互に反映させる技術です。これを活用すれば、自動化された「スマートファクトリー」を稼働させることも可能になります。こうした仕組みには、あらゆる環境を数値化してシミュレーションするCAEの力が欠かせないのです。
さらに企業のDXの取り組みの1つに「環境経営」があります。この取り組みでも、さまざまなシミュレーションによって想定される環境負荷をデータ化、可視化できるCAEは重要なツールとなるでしょう。環境負荷軽減は、業務負担をできるだけ少なくする自動化の管理手法が求められます。CAEの解析機能は、こうした自動化の実現にも大きな役割を果たすでしょう。
CAEの活用事例
次に、CAEが活用されている代表的な業界について解説してきます。
自動車業界
CAE解析を最も活用している業界の1つが自動車業界です。
自動車業界は試作・実験にかかる負荷が大きく、設計段階からコンピューター上でシミュレーションを実施すればさまざまなコストを大幅に削減できます。
例えば本田技研工業では、設計案を作成する段階でのシミュレーションにCAE解析を活用しています。これにより実験リソースの削減、開発スピード向上といった効果をあげています。
またトヨタ自動車は、グループ全体でCAEの解析システムを共同利用できる体制を構築しています。これにより大規模開発の解析や複数解析の同時処理などを実現しています。
自動車業界の新車開発というと、工業用粘土を使った「クレイモデル」が有名ですが、CAE活用の初期段階でこのモデルの作成をCAEで行うようになりました。最近ではさらに上流の工程である設計段階からCAEを使い、後工程の手戻りを削減ししようとしています。
また、同業界では昨今、自動運転技術などの導入が求められるようになり、機械、電気、ソフトウェアのそれぞれのカテゴリーでのシミュレーションを別々に行うのではなく、連携させて実施するようになっています。こうした個別シミュレーションの連係機能を持ったCAEが開発され、最終製品メーカーでの複雑な製品開発にも活用されるようになっています。
エレクトロニクス業界
半導体や電子部品、電化製品を設計、製造するエレクトロニクス業界でも、さかんにCAEが活用されています。自動車業界同様に試作や実験を繰り返し行う必要があり、熱・光の移動、電磁波など実験が難しい事象を扱うためシミュレーションが欠かせません。
例えば最近普及しはじめた「ワイヤレス充電」の多くは電磁誘導方式を採用しているため、電力効率を確認する目的でCAE解析が活用されています。電磁誘導方式は安定した電力供給が可能ですが、一方で伝送距離が短くコイル間の位置がずれると効率が著しく落ちてしまうからです。
また事務機器や家電製品の分野でもCAEは多く使われてきました。設計がほぼ完成した段階で解析担当者が製品の強度などを解析したり、3D CADのデータを活用して強度計算を行ったりといった取り組みです。
ヘルスケア業界
先進医療機器開発のシミュレーションの分野にもCAEが活用されています。これらの製品は人命にかかわるため安全性・耐久性・衛生面などが重視させるため、正確な解析が求められます。例えば、個別のサイズの設計が求められる酸素吸入器やカテーテルの解析などではCAEは欠かせないツールです。
このほか人体で使用するインプラントの開発でもCAE が活用されています。医療分野の製品規格は極めて厳しく、市場投入に必要な認証にも時間がかります。そうしたこともあり、医療用機器の開発は設計の初期段階から精密さとスピードが求められます。こうしたニーズを満たすため、CAEはどうしても必要なのです。
また医療現場でCAEは手術の前のシミュレーションにも活用されています。正確な解析結果を示すことで、患者一人ひとりの病状に即した医療が可能になります。
主要なCAEソフト
こちらでは、幅広い業種で導入されている4つのCAEソフトの機能や特長をご紹介します。自社に適したソフトはどれか、検討にお役立てください。
HyperWorks
アルテアエンジニアリング株式会社の「HyperWorks」は、製品開発に必要な構造、衝撃、機構、流体、電磁場(波)、最適化に加え、プレス、鋳造、押出成形用の各種ソルバー(解析エンジン)や、それらを使用するためのプリ・ポストプロセッサを装備した統合CAEプラットフォームです。
汎用性が高く、多くのCAD、CAEと連携できる点が特長と言えます。多様な3Dシミュレーションの実施や複雑な条件下での解析が可能で、自動車OEM、重工メーカー、電機メーカーのみならず、その他の業種でも幅広く利用されています。
SOLIDWORKS Simulation
新明和ソフトテクノロジ株式会社が提供する「SOLIDWORKS Simulation」は、構造解析ソリューションツールで、非線形弾性材料、超弾性材料、プラスチックなど、さまざまな材料モデルを異なる条件の下、正確にシミュレーションして開発速度・コスト・品質の成功条件をクリアします。
また、設計チームと製造チームが同時並行で作業できるため、設計を次段階に移すときのエラーを削減しやすく、製造上の潜在的な問題点を設計段階で早期に検出可能です。人目を引くビジュアル作成でステークホルダーを惹きつけることができます。
Ansys Mechanical
アンシス・ジャパン株式会社の「Ansys Mechanical」は、伝熱と構造解析、音響と構造解析といった複雑な連成解析が可能なソフトウェアです。
線形構造解析や接触解析、伝熱解析、疲労解析など、汎用的な解析機能を装備した「Ansys Mechanical Pro」を基本に、Mechanical Proの機能に加え、より高度な非線形応力解析や線形動解析などが利用できるPremium、フラッグシップ製品のEnterpriseで構成されており、初級から上級レベルまでステップアップしていくことができます。
Fusion 360
オートデスク株式会社が提供する「Fusion 360」は、設計、エンジニアリング、電子設計、製造などの機能を搭載したオールインワンソフトウェアです。3D CAD、CAM、CAE、PCBを統合したクラウドベースの単一ソフトウェアで、製品開発プロセスを一元管理することが可能です。
個人利用や非商用、一部の条件を満たしたスタートアップ企業は無料で利用でき、サブスクリプション契約は1カ月・1年間・3年間の中から選べます。
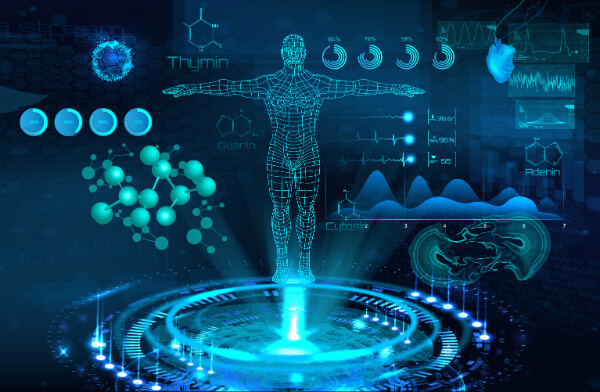
まとめ
CAEは、今後、5GやIoT、AIといった先端技術との融合でさらに活用範囲を広げていくことになるでしょう。実際に、CAEがAIに学習データを提供する役割を担ったり、CAEの解析モデルをAIによって高速化させたりといった試みが始まっています。こうした進化に伴い、CAE解析を専門に行うエンジニアはさらに重要な役割を担うようになるはずです。
CAE関連のエンジニアは数が足りない状態です。こうした専門のエンジニアは一人前になるためには、CAE解析ツールの操作技術だけでなく、工学や機械設計に関する専門知識、そしてAIなど複合的な知識、経験が必要になります。人材育成に時間がかかるハイレベルなエンジニアは常に不足状態で、製造業企業にとって頭の痛い問題です。
例えば設計者自らがCAEによる解析を行う『設計者CAE』の体制を整えたい企業が多いと考えられますが、一朝一夕にはそうした体制を敷くことは難しいでしょう。その理由として、設計者がこれまで培った経験だけではCAEを扱うことは難しく、新たに解析などの知識を習得するための体制を組織として持つ必要があります。またこうした課題には、解析の専門家に設計の知識・技能を習得してもらうというアプローチも考慮する必要があるでしょう。
いずれにせよ、CAEの技術を使いこなすことは、市場の変化に素早く対応できる組織となるうえで不可欠な条件となるはずで、ひいては競争力の強化につながります。
(提供:Koto Online)