『デジタルツイン』という言葉が注目されています。デジタルツインは主に工場での活用が進んでおり、現場が大きく進化した事例が出てきました。デジタルツインは何を進化させたのでしょう。メタバースやシミュレーションとの違い、メリット、事例について紹介していきます。

目次
デジタルツインとは何か
デジタルツインとは、直訳すると「デジタルの双子」です。現実の設備をデータ化して、そっくりそのまま同じに見えるものを仮想空間上に再現する技術のことを言います。
現実の設備と同じものが仮想空間にあれば、IoT(Internet of Things)デバイスで収集したデータをもとにして、仮説を立てての実験ができます。現実の設備は1つしかなく、運転を止めての実験ができなくても、デジタルツインであれば仮説を試すことができるのです。例えば、ある一部分の動きが悪くなった場合、全体としてどのような影響が出るのか、機械の配置を換えた場合、効率はどのように変化するのか、など現実の世界で試すことができないことが実験できるようになるというわけです。
また、これまでIoTによって蓄積されたデータを使ってAIで分析し、近い将来起きるかもしれない障害を予測することも可能になってきますし、障害が起こった際にどのように対処するのが最も効率的か、なども試すことができるようになります。
このように現実に限りなく近い環境を仮想空間に作り出すことによって、何度でも試してやり直すことができるので、コストや時間を著しく削減できます。現場の生産性向上に寄与し、変化のスピードがこれまで以上に加速されるでしょう。
デジタルツインはなぜ注目されているのか
デジタルツインが注目され始めた背景には、VRなど3D映像の技術やIoT、AIの発達があります。精度の高い仮想空間を構築できるようになったため、現実の設備を仮想空間に再現することができるようになったことが大きい要因と言えます。
精度の高い仮想空間の出現に合わせて、これまで蓄積されていたIoTによるデータとAIによる分析を加えて、現実の世界でできないことを仮想空間で再現できるようになったのです。
航空宇宙局(NASA)は1960年代、アポロ計画の際に「ペアリング・テクノロジー」というものを編み出しました。これは宇宙を飛行中の機材と全く同じものを地上にも設置しておき、もしもの時に対処法を伝えるために考え出された方法です。現代のデジタルツインはNASAのペアリング・テクノロジーと同じことをコンピュータの中で再現できるようにする技術だといえます。
デジタルツインとメタバースの違い
仮想空間上に現実世界を再現するものとしてはメタバースがもてはやされています。メタバースとデジタルツインはどこがどのように違うのでしょうか。最も大きな違いは、使用目的による「再現するものの中身」にあるといえます。
メタバースは、必ずしも現実世界を忠実に再現するものではありません。あり得ない想像上の世界を構築することもあります。また、メタバースには、“アバター”という人間の分身が不可欠ですが、デジタルツインではアバターのような人間の分身は必須ではありません。メタバースは、仮想空間で他人とのコミュニケーションを楽しむことを主目的としています。
一方、デジタルツインは現実世界の設備や物を完璧に再現することを必要としています。現実世界ではできないシミュレーションを行うことを主目的とするデジタルツインでは、メタバースと似た技術を使っているとはいっても、このように中身が違ってきます。
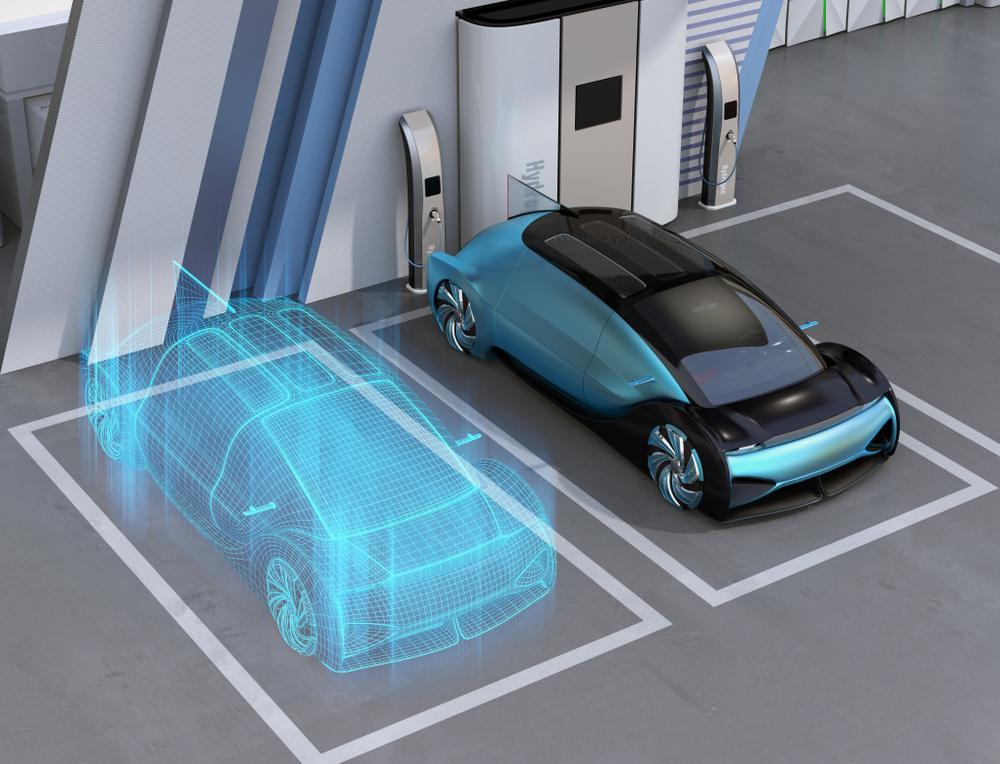
デジタルツインとシミュレーションの違い
現実の設備を忠実に仮想空間に再現するデジタルツインはシミュレーションと何か違うのでしょうか。デジタルツインもシミュレーションの1つと言えそうですが、これまでのシミュレーションとは違う点があります。それは、現実の情報を仮想空間に連動できる点、リアルタイム性が高い点、発生する事象の予測ができる点の3つです。それぞれを掘り下げて見てみましょう。
現実の情報を仮想空間に連動できる点
シミュレーションには仮説が必要になります。想定した筋書きで仕様を決めて実験を行うという手順です。これらの実験は人の手で行わなくてはならないし、場合によっては設備も用意する必要が出てきます。デジタルツインは、現実と同じものが現実と同じ条件でリンクしているので、そのままシミュレーションできます。仮説ではなく現実に起こっていることをもとにしていますのでより現実的になるのです。仮想空間を現実世界に連動させることによる効果が出てきます。
リアルタイム性が高い点
シミュレーションは仮説に基づいて実験をやった結果を踏まえ、対策を講じていくという手順を踏まざるを得ません。対策を講じて結果が出るまでに時間がかかるために、後れを取ってしまうという欠点があります。デジタルツインでは現実のデータを元にするので、そのデータに基づいた予測の元、実験を行います。仮想空間でそのまま実験を行えば結果が出るまで待つ必要がありません。
発生する事象の予測ができる点
シミュレーションでは不可能なことですが、デジタルツインでは、想定される事態を実際に起こしてみることができます。また、今の状態のまま経過した場合、あとどれくらいでその事態になりうるのかなどの予測が可能になります。現実の空間にこれらの情報を共有すれば、「不測の事態」などと呼ばれてきた事象を減らすことができるようになります。
デジタルツインのメリット
これまで述べてきたように、デジタルツインは相乗効果としてメリットがたくさん出てきます。コスト削減、品質の向上、予知保全、遠隔管理ができるという4つに整理して、解説します。
コスト削減
工場では物を作る前に何回も試作を繰り返す必要があります。デジタルツインで試作を行えば、仮想空間上の3Dモデルで検討できます。現実の工場で行う試作や試験には時間上、空間上の制約がありますので限界がありますが、仮想空間で試作を繰り返せる範囲で行う分には、何回でもチャレンジできます。
この方法で、製品に欠陥が生じないかどうかの発見が可能になるのです。時間や材料費の節約になりコスト削減につながります。また、後述しますが、故障してラインが止まってしまうことを予知し、防止することによるコスト削減も挙げられます。
品質の向上
試作品を仮想空間で繰り返し作ることによって、それまで現実空間で製品開発をしていた際にはできなかったことができるようになります。人間では気付かないことに気づいたり、目に見えない箇所に手を入れたりすることができるようになる場合もあります。デジタルツインで、これまでのやり方では不可能、あるいは気が付かなかった加工法が生まれた結果、品質が向上することもあるのです。また、部品の耐久性の問題などについても、ビッグデータから解析して不具合を発見できるようになります。デジタルツインで試験をしながら製造した製品の信頼性は格段に上がるでしょう。
予知保全
デジタルツイン環境には、現実の工場に設置したIoTによる各種センサーのデータが蓄積されて分析できるようになっています。これらデータをAIで分析することによりこのままでいけば、どこがいつ故障するのか事前に知ることができるようになります。
工場のラインがひとたび故障すれば、そのラインを停止して修理しなければならなくなりその分、生産効率が落ちてしまいます。いつ頃限界がきて故障するのかわかっているのならちょうどその事態が発生する前に交換するなどの措置を取ればよいことになります。こうした機械の故障による生産活動停止の事態を、あらかじめ知ることで保全することができるのです。
遠隔管理ができる
世界各地に工場がある場合でも、デジタルツインを本部に構築しておけば、現場の状況がデータとともにわかるので、遠隔地から監視をしたり、指示を出したり、といったことができるようになります。何か問題が生じるたびに、遠隔地まで出向くのはコストと時間がかかります。デジタルツインで監視しながら指示を出すことで済むのであれば、わざわざ出張する必要はなくなります。コスト削減にもつながりますが、働き方改革にもつながる効果です。
デジタルツインを実現する技術
デジタルツインはどのような技術で成り立っているのでしょうか。調べてみると、DXを構成するいくつかのキーワードが整理できます。順にみていきましょう。
VR
VRとは「Virtual Reality」を略した呼称です。直訳すると「仮想現実」ということになりますが、限りなく現実に近い仮想空間ということになります。一般的には狭い意味でとらえられて、HMD(Head Mount Display)をつけて仮想空間を自分の視点で映像をチェックするシステムのことを言いますが、VRを概念としてとらえたときに、デジタルツインはその一部だということができます。HMD使用の有無は別としてデジタルツインはVRとしての考え方がベースになっていることは間違いありません。
IoT
このコラムでも何回も取り上げていますが、この技術がなければDXそのものが発生しなかったという基礎的な技術です。インターネットに接続できる各種のセンサーが、それまで人間の手によって計測することができなかったさまざまなデータを大量に取得することができるようになりました。モノのインターネット(Internet of Things)があるからこそ膨大なデータを取得することができ、それをもとにデジタルツインが再現できるのです。
5G
5Gを略さずにいうと「第5世代移動通信システム」となります。5Gには次のような特徴があります。
―高速大容量
―高信頼・低遅延通信
―多数同時接続
日本では2020年春からサービスが開始されました。実はこの5GがDXに果たす役割は大きいと考えられています。われわれが利用してきた携帯電話などでは4Gが使われてきました。4Gが主流になって以来ゲームや動画などのコンテンツが普通に楽しめるようになってきた経緯があります。5Gは4Gと比較したときに、通信速度が20倍、遅延は10分の1、同時接続台数は10倍になるといわれており、これによるさまざまな進化が見込まれています。デジタルツインに関係の深い技術であるIoTにおいては、「多数同時接続」が可能な5Gによって、ますますデータ解析の精度は上がっていくでしょう。機械学習の飛躍的な進化も期待できます。
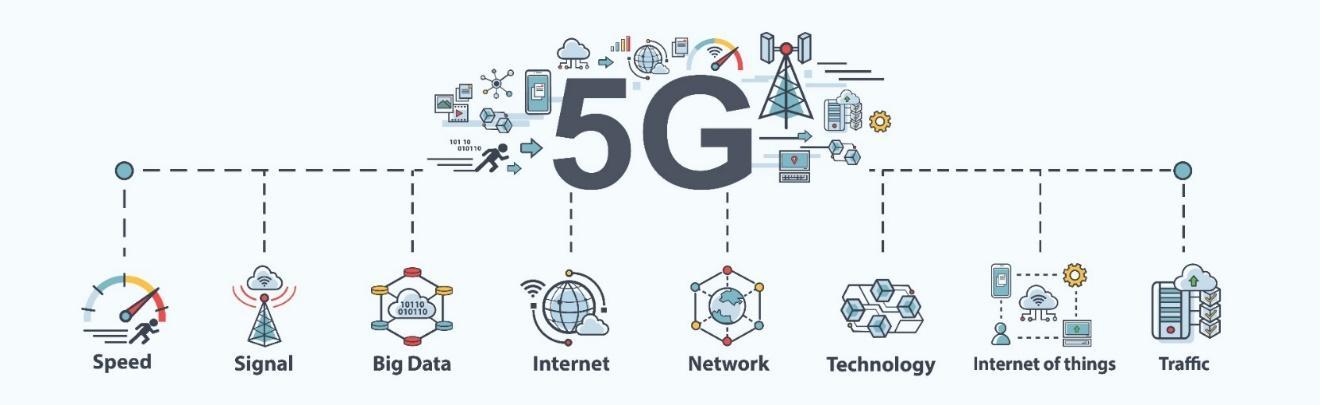
AI
デジタルツインでは、IoTで収集したデータをどのように生かすかが重要になります。単に物理的な設備の再現だけをするのではあまり意味がなく、IoTで収集したデータからAIが自立学習をすることに意味があります。故障の予知や、部品の耐久性など、長年の経験や長時間の試験などによってしか得られなかった情報が、デジタルツインとAIの力によって実現しているのです。
デジタルツイン工場での活用事例
実際の工場で活躍しているデジタルツインの事例をご紹介しましょう。
ダイキン工業
エアコンでよく知られているダイキン工業は、2018年に新設した堺製作所臨海工場でデジタルツインを導入しました。工場内には、「工場IoTプロジェクトセンター」が設置され、各工程の検査結果や加工条件の情報を集約しトレーサビリティを取っています。これは、製造ライン上に設置したIoT機器により収集された生体、制御、温度・CO2濃度データ等をリアルタイムにデジタルツイン上に再現し、AIで異常値を発見して重大な事故を防ぐ取り組みです。
この取り組みで、工場の生産ラインの停止、従業員の労働安全衛生、品質の保証をより高度に行うことができます。これによって、工場で起こった何らかの停止を防ぎ、前年度比で3割強のロスを削減する見込みだといいます。
旭化成
旭化成は福島県に建設した水素製造プラントに2021年デジタルツインを導入しました。化学製品を製造するプラントには、プラントごとに専門化したベテラン技術者がいて、現場で異常時などの対応をしています。ところがこのベテラン技術者の人数は限られており、出張や休みの時などに不在になってしまうことがありました。そこで差し迫った問題を解決するためにベテラン技術者が不在であっても遠隔地から指示できるようなシステムを考えたのです。
化学プラントの設備に何らかの異常が起きた時の対応は、マニュアル化することが難しくベテラン技術者の存在は不可欠です。そこでデジタルツインでプラントを丸ごと仮想空間に再現して、異常が起きた箇所を遠隔地からでも確認できるようにしました。同社では、海外のプラントでも日本国内から支援できるような体制も視野に入れているといいます。
サントリー食品インターナショナル
清涼飲料メーカーのサントリー食品インターナショナルは、天然水の工場にデジタルツインを導入しました。デジタルツインを導入したのは2021年5月に稼働した「サントリー天然水 北アルプス信濃の森工場」です。このデジタルツインは、主に製品のトレーサビリティを厳密に行う役割を持っています。これはペットボトル1本に対して、どの設備、どの部品によって製造されたのかをトレースするものです。万が一設備に異常が起こり、不良品が混じった可能性が発生しても、その製品がどの段ボールに梱包されて、今どこにあるのかがわかるようになっています。
このほかにも、IoTでデータを収集してリアルタイムに監視しているため、異常が発生しそうな場合はすぐにわかる体制なのだといいます。デジタルツインが品質の向上に寄与しており、食の安全のために貢献しているといえる事例です。
デジタルツインの発展性
デジタルツインの工場への導入は、2023年現在でもまだ始まったばかりだといえます。まだまだ伸びしろのある分野で応用範囲も広がってくるでしょう。
グローバルインフォメーション(GII)が提供するKBV Researchの市場調査レポート「デジタルツインの世界市場:タイプ・用途・業界・地域別の市場展望、産業分析、市場予測(2021年~2027年)」によると、世界のデジタルツインの市場規模は、2027年までに635億米ドルに達すると予測されています。デジタル仮想空間の中でトライアンドエラーを繰り返すことのできるデジタルツインは、新しい発見や発明を加速させることのできるアイテムだとも言えます。
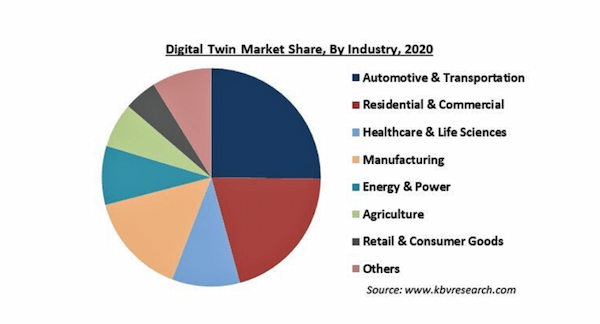
また、遠隔地から監視をしたり、ベテラン技術者をサポートしたりするなど働き方改革に寄与することもわかってきました。これまでご紹介してきた利用法以外にも、想定できないような使い方が生まれてくる可能性があります。デジタルツインは、これまで不可能とされていたことを次々と可能にしてきています。デジタルツインが世界中の製造業が飛躍的に効率を高め、日本国内におけるDXを進展させるための重要な要素になる可能性を持っています。