本記事は、木村哲也氏の著書『Small Factory 4.0 第四次「町工場」革命を目指せ! ― IoT の活用により、たった 3 年で「未来のファクトリー」となった 町工場の構想と実践のすべて』=株式会社翔泳社、2018年8月1日発行の中から一部を抜粋・編集しています。
トヨタ生産方式でもっとも嫌われるムダは「作りすぎのムダ」です。 売れない製品をたくさん作っても会社に損害を与えるだけだからです。売れるペースに合わせて製品を生産するのが基本なのです。
しかしながら、中小企業は自分たちで生産数を決定できるわけではありません。注文が来たらそれに応じなければならないのです。その注文 数も一定ではなく、多少の波があるのが普通です。注文が多い時には しっかりそれに応えなければなりません。かといって、注文の多い時期 に合わせて生産設備を導入してしまうと、注文が減った時には困ってし まいます。
この矛盾する2つの課題を解決するために、私たちは、「時間当たり出来高をアップする」ことを目標にしました。
このことによって得られる効果は 3つあります。
①労務費の削減
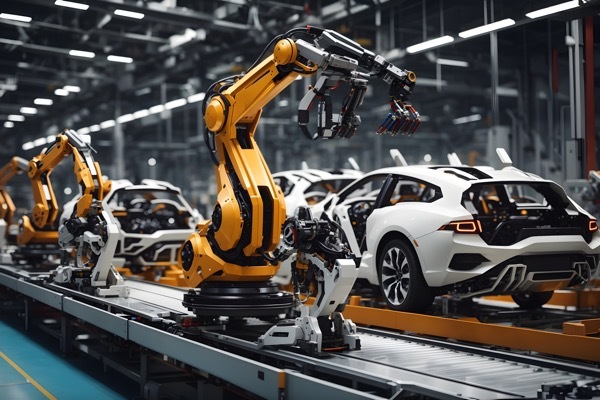
定時内に作ることができないほどの注文が来た場合は社員を残業させて応じなければなりません。しかし、時 間当たり出来高を向上させれば、ある程度まで定時内で対応できるはずです。そうなれば残業代(労務費)の削減につながります。
②設備投資の抑制
残業しても応じきれない注文に対しては通 常、設備の増設で対応します。そうすると設備投資はもちろん、 工場スペースも必要になります(③)。しかしながら、現有設備 でも時間当たり出来高を向上させれば、これらの投資が不要になります。
③工場スペースの節約
②であげた例だけでなく、既存の製造 ラインの時間当たり出来高を向上させることができれば、ライン 数の削減につながり、工場スペースの節約が可能になります。
当社ではこれまで「時間当たり出来高」へのこだわりが不十分だった ため、前述の3点においてムダなコストを費消することが何度もありま した。つまり、改善の余地が大いにあったというわけです。 そこで、製造ラインの問題点を発見し、対策を講じ、結果を確認して、 次のアクションにつなげるという「PDCA サイクル」を回し、「時間当 たり出来高のアップ」を達成することが新たな目標となりました。
カギとなったのは、やはり「IoT」の利用です。
(ⅰ) サイクルタイムがばらついている
前述したように、第一世代の「可動率モニター」で得られたデータを「ラインストップミー ティング」に活用することで、ムダな停止時間を大きく減らすことがで きました。しかし今度は「生産個数」が足りないという問題が発生しました。
「生産個数」は次の式で決まります。
生産個数=ラインが稼働した時間÷サイクルタイム
したがって、可動率モニターによって「ラインが稼働した時間」を管理するだけでは、生産個数を管理することはできません。そして調査をしてみるとやはり、この「サイクルタイムがばらついている」ことが、 生産個数が足りなくなる原因だと判明しました。
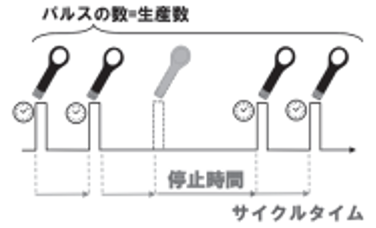
「IoT 化」の次なる目標は、「サイクルタイムをモニターできるシステ ム」の開発に決まりました。
(ⅱ) パルスを発信させカウントするシステム
システムの構想 はすぐにまとまりました。製品が 1 個できるごとにパルスを出し、デ ジタル・タイムスタンプ 15を捺すようにすればいいのです。パルスの 数が生産個数になり、通常の間隔でパルスが来ている時間はサイクルタイム、来るはずのパルスが来なければ停止とみなすことができます(図 1.4)。
(ⅲ) 費用を安価に抑える工夫とは
問題はパルスを発信する方 法です。生産技術出身の社員からは「PLCを購入して設備に取り付け パルスを出す」という提案がありました。
しかし、以下のような理由でこの提案を却下しました。
①約 15 万円と高価
②設備の改造が必要
③「昭和の機械」(=古い設備)には対応していない
そこで前回同様に、東京・秋葉原で適当なセンサーを購入し、試作をすることにしました。全 38種類のセンサーを購入しましたが、それでも大した金額にはなりませんでした。
余談ですが、こうした機会で、私たちが大事にしている基準のひとつは「面白いかどうか」です。結果として役に立たなくても構いません。「それ、面白い発想だな!」とほめることもあります。最近ではドローンを 購入して製造工程を撮影することにトライしていた社員がいました。実用化できる確率は高くないだろうと踏んでいましたが、「面白いから OKだ!」と励ましました。社員からすばらしい発想を引き出すには、一見、ムダに見える発想を大切にしてあげることが必要です。