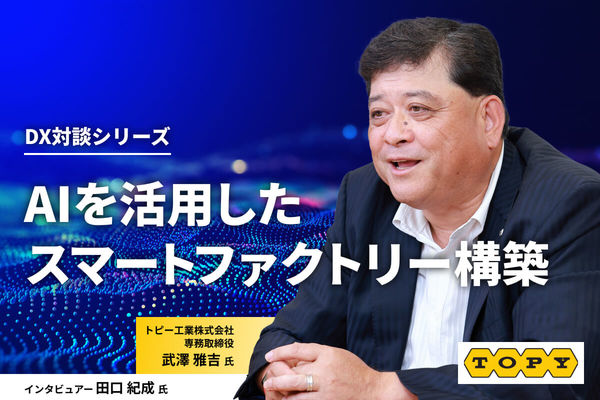
Koto Online編集長の田口紀成氏(コアコンセプト・テクノロジーCTO)が、DXの最前線を企業にインタビューする本シリーズ。今回は、中期経営計画における事業戦略の重点テーマにDX推進を掲げるトピー工業の取り組みをご紹介します。
トピー工業は、素材供給部門の鉄鋼事業、加工部門の自動車・産業機械部品事業が相互に関連し、廃棄物の集荷・処理から原料調達まで一貫した生産体制を持つ金属加工の総合メーカーです。DXの基礎をスマートファクトリー化によって築いた同社の取り組みと将来像について、同社専務取締役の武澤雅吉氏に伺いました。
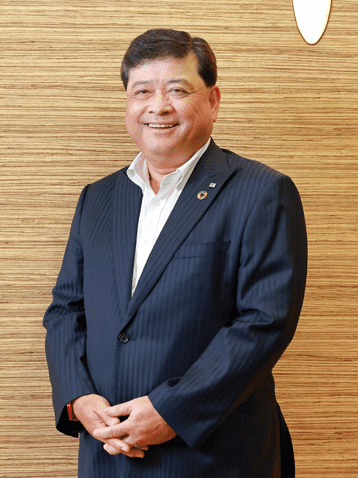
大学で経営工学を専攻し、1983年トピー工業株式会社入社。入社から25年間、豊橋製造所にて圧延技術スタッフ、管理職を務める。2008年に本社経営企画部に異動したのち、2011年豊橋製造所長に就任。2013年再び本社異動となり、業務改革推進部長、IoT推進部長、技術部長を歴任。システムのオープン化、ERP刷新、スマートファクトリー構築などのシステム改革を牽引し、執行役員、常務取締役を経て2022年4月より現職。
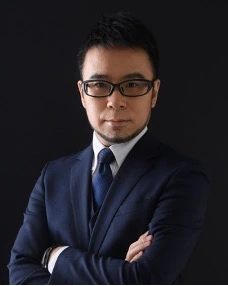
2002年、明治大学大学院理工学研究科修了後、株式会社インクス入社。自動車部品製造、金属加工業向けの3D CAD/CAMシステム、自律型エージェントシステムの開発などに従事。2009年にコアコンセプト・テクノロジーの設立メンバーとして参画し、3D CAD/CAM/CAEシステム開発、IoT/AIプラットフォーム「Orizuru(オリヅル)」の企画・開発などDXに関する幅広い開発業務を牽引。2014年より理化学研究所客員研究員を兼務し、有機ELデバイスの製造システムの開発及び金属加工のIoTを研究。2015年に取締役CTOに就任後はモノづくり系ITエンジニアとして先端システムの企画・開発に従事しながら、データでマーケティング&営業活動する組織・環境構築を推進。
目次
トピー工業が目指すインダストリー4.0の姿
田口氏(以下、敬称略) 御社がDX戦略に取り組むことになった背景について、ご説明をお願いします。
武澤氏(以下、敬称略) 当社は、2015年頃からIoT化推進やERP刷新、電力の「見せる化(*)」、インダストリー4.0への対応としてスマートファクトリー構築に着手していました。背景としては、情報通信技術の急速な成長をはじめ、法改正への対応を含むレガシーシステムの刷新、製造業の世界的な潮流、東日本大震災後の電力事情の悪化など、さまざまな外部環境の変化に対応するためです。
*エネルギー消費の推移を「いつでも・誰でも・簡単に」確認できる仕組みのこと。
この流れを汲み、今後目指していくのが、個別最適化から全体最適への変革です。社会ニーズや環境変化を柔軟に捉え、製品・サービスやプロセス、ビジネスモデルを変革し、生産性・競争力・収益力の向上につなげるのが狙いです。
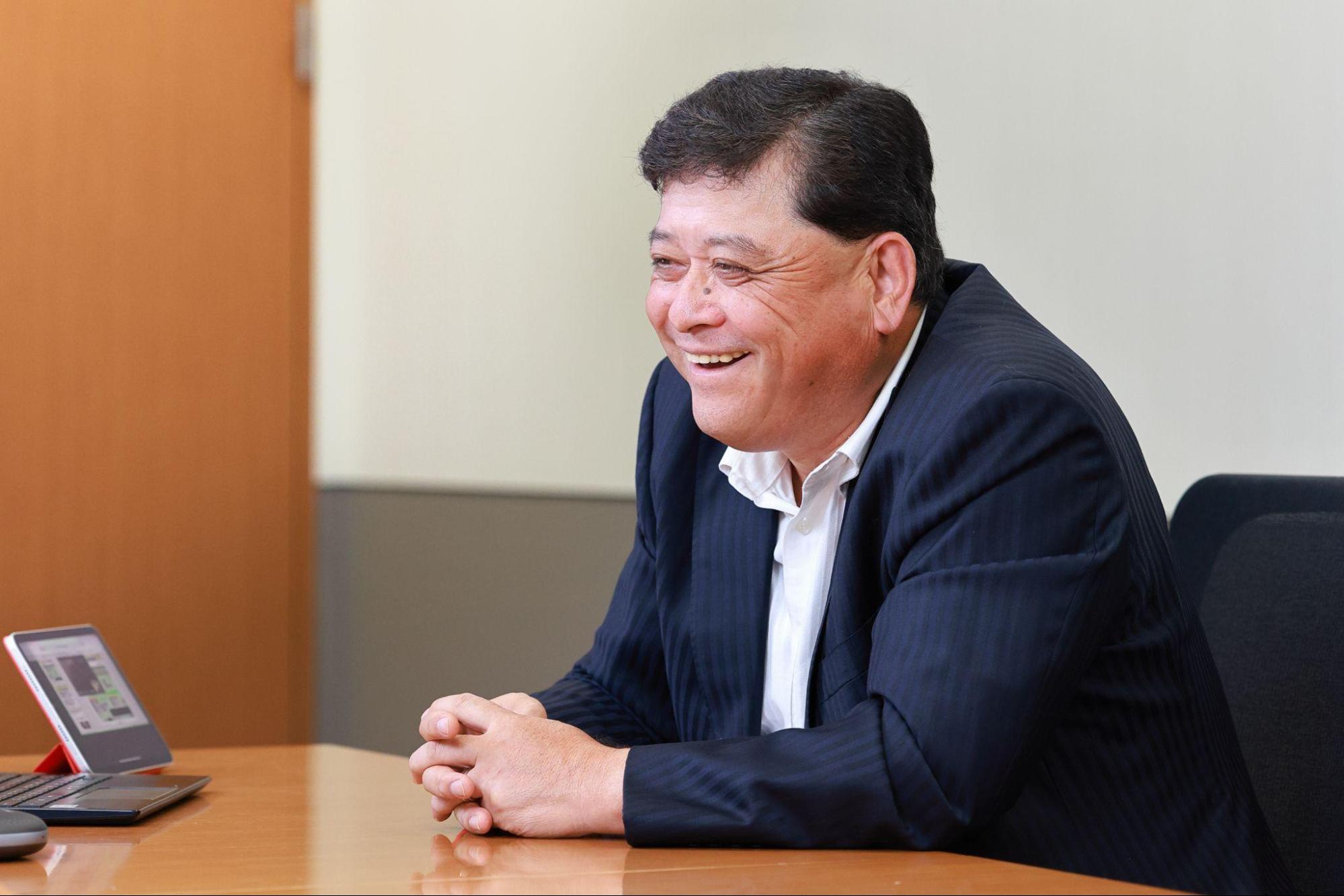
インダストリー4.0に対する取り組みによって情報収集と一元管理のDX基盤ができたので、今後は情報を「データドリブンプラットフォーム」に集約し、各種BIで経営に資するデータに変換する取り組みを始めようとしています。
田口 ひとくちにインダストリー4.0といってもその範囲は非常に広いですが、御社ではどのようなことを示しているのでしょうか。
武澤 当社にとってのインダストリー4.0は「生産改革」を指し、最終的にはデジタルツイン・CPS(サイバーフィジカルシステム)の構築を目標としています。工場をスマートファクトリー化して現場のあらゆる情報を収集し、人間では判断が難しい情報を分析させます。閾値管理やAIを活用した設備診断機器で異常を仮想空間で判断し、生産時のトラブル予防や影響を最小限に留めるために、現実空間にアラートを発信するというものです。インダストリー4.0の上にDXが入ってくるイメージですね。
田口 ありがとうございます。DX基盤の構築を完了されたとのことですが、これまでの取り組みについてご説明いただけますか。
武澤 はい。まずIoT推進のため、販売や生産、品質保証などの製造に関する情報・機器の接続を実行しました。具体的には社内ネットワーク環境の整備やコンピュータシステムの連携、製造所内のFA機器の仕様統一です。製造所のFAサーバに工場のPLC(プログラマブルロジックコントローラ)や生産実績、工程検査などのあらゆるデータが蓄積される仕組みを構築しました。
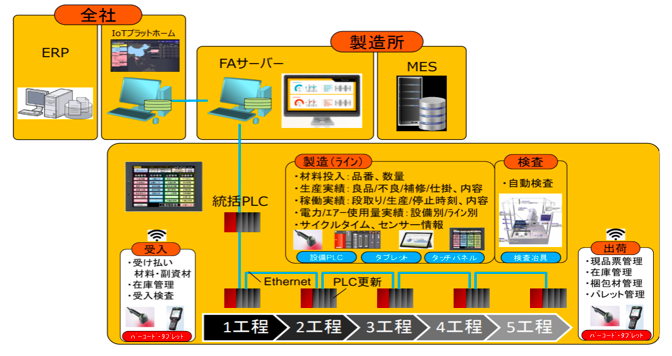
当社がスマートファクトリーと呼んでいるのは製造所の部分までになりますが、収集した生産実績や品質情報などさまざまなBIツールを活用して、能率管理などを分析・評価・見せる化し、課題の明確化による改善につなげており、最終的に全社側のIoTプラットフォームにデータを貯めていく流れを作っています。
このように製造所のデータを収集する基礎は完成しており、豊川製造所(愛知県)を皮切りに、2022年から各製造所への導入をスタートさせているところです。エネルギーの管理システムはすでに全社展開しています。このシステムを活用して得られた成果が、当社のスマートファクトリー化とDX戦略の大きな推進力になりました。
田口 なるほど、詳しくお聞かせください。
スマートファクトリー化に拍車をかけた成功体験
武澤 2011年の東日本大震災後の電力事情の悪化に対し、神奈川製造所で電力管理システム導入による省エネ活動を行いました。このシステムでは、生産工場と工場を抱える製造所全体の電気使用量が一括してリアルタイムで見えるようになりました。それをドリルダウン(*)していくと、各工程の時間ごとの電力消費量が見えてきます。契約電力は30分デマンド値をいかに下げるかで決まりますから、その状況を現場で確認し判断すれば、稼働タイミングをずらして使用電力のピークが抑えられるのです。この電力使用量の削減取り組みに対し、2017年に経済産業省「省エネ大賞」を受賞できました。現在、この省エネ活動を、電力に限らずエネルギー全体の管理システムとして全社展開しています。
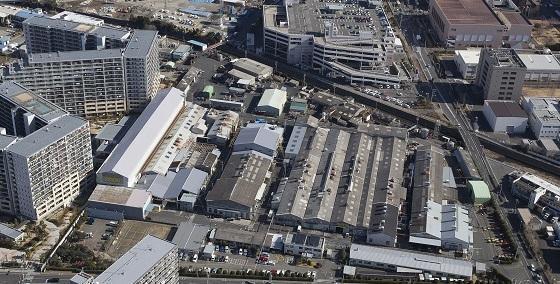
田口 非常に大きな成果ですね。しかし省電という目的で現場をまとめるのも大変かと思いますし、生産計画もある中でピークカットは簡単なことではないと思われます。何か秘訣があったのでしょうか。
武澤 この取り組みのポイントは、省エネに関して製造所長以上の権限を持つ「省エネマイスター制度」を設置したことにあります。省エネマイスター主導で電力管理システムを運用し、優先的に電力を使う工程を判断し、この稼働タイミングなどをずらすことでピーク電力をカットしました。この制度により、製造所が一体となり自らの判断で省エネを意識した稼働とすることで、電力消費量の大幅削減に成功しました。
当社は昭和58年(1983年)から省人化ならぬ「少人化」を推進しており、オペレーターの多能工化と作業の平準化に取り組んできました。1人のオペレーターが複数のスキルを持っていますから、製造工程や出勤をずらしても生産が滞らないのです。2014年からは「エネ活」という表彰制度をつくり、省エネに貢献した職場を毎年表彰しており、それも現場のモチベーションになっています。
今では全製造所に同じシステムが導入され、燃料エネルギーの使用状況もモニタリングできるようになりました。当社グループは2050年のカーボンニュートラル実現を目指し、2030年までにCO2排出量を46%カット(2013年度比)することを目標にしていますが、省エネ活動の継続は、その主力の取り組みとなっています。
田口 IoTやスマートファクトリーは予算がつくまでの道のりが遠いと聞きますが、こうした成功体験があると会社全体の理解が得られやすくなりますね。ここまでデータを駆使して省エネに取り組む企業は多くないように思うのですが、何がきっかけでこうした取り組みが始まったのでしょうか。
武澤 実は、顧客である建機メーカーからの要請がきっかけです。同社の事例を参考に、神奈川製作所が取り組みを進めました。当社グループはJK(自主改善)活動が進んでおり、現場主導の改善活動を非常に得意としていますので、そうした過去からの取り組みも生きたのだと思います。
田口 長い時間をかけて築き上げた企業風土が、新たな取り組みでも力を発揮しているのですね。非常に素晴らしい事例だと感じました。
苦労したERP浸透、CPS構築は自社開発で推進
田口 ERPの刷新はどのように進められたのでしょうか。
武澤 2000年問題やその後の法改正への対応、データ収集・分析による経営判断の迅速化、海外拠点のリソース不足の解消など、さまざまな課題解決のためにERP刷新の検討を始めました。ERP導入には大きな投資を伴いますが、失敗に終わったという他社の事例も耳にしていました。そうした会社や海外の関連会社にヒアリングを重ねたところ、失敗原因の多くがアドオンによるものだと分かったのです。汎用システムに自分たちの業務を合わせたことが、ERP刷新を成功させた秘訣だと考えています
田口 しかし、その方法では現場から反発があったのではないかと推察します。
武澤 おっしゃる通りです。特に強い抵抗感を示したのは各業務のスペシャリストたちでした。業務の標準化・効率化によって自分のスキルが優位性を失うという危機感もありますし、業務処理を一から覚え直さなければならない面倒さもあります。さらに、システム導入はシステム担当がやるものであって、自分たちは関係ないという非協力的な社員がほとんどでした。
田口 どのように理解を得たのでしょうか。
武澤 刷新メンバーが製造現場に足繁く通い、手厚く支援しました。情報入力や結果証明のExcelづくりなど、定例業務がRPA化できることや、ビッグデータの活用が評価・改善のレベルアップにつなげられることなど、「ERPを使った方が業務は楽になる」と実感してもらったのです。最近は 社員の態度も協力的になりました。
社員への意識付けとして社内イントラを活用しており、役員メッセージや健康経営、サステナビリティなど、さまざまな情報を開示しています。情報に触れることに慣れ、その活用方法を理解してもらうためです。社内イントラはMicrosoftのSharePointで構成されているので、簡単にシステムに取り込めますし、各部門で公開したい情報も自由にアップロードできます。システム活用によって、自分たちのやりたいことを効率化できるという理解が浸透し、DX推進の機運の醸成に大きな役割を果たしています。
田口 情報だけでなく、ITを使いこなされている御社の姿も見えてきました。CPS構築の現在地についてもお聞かせください。
武澤 もちろんです。ERPやMES、FAの連携に取り組んでおり、基礎が完成しています。画面で事例をご紹介しましょう。
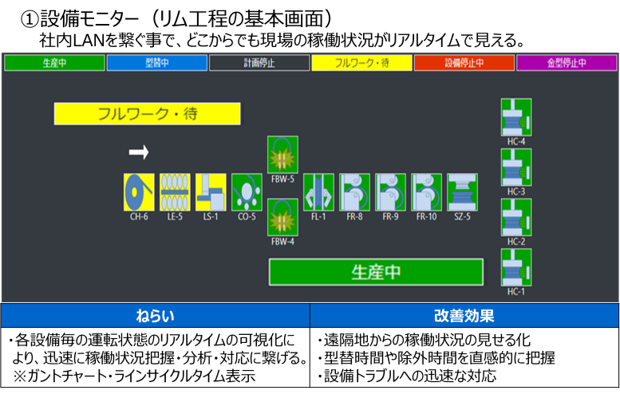
設備モニターの画面では、黄色が停止している部分、緑が生産している部分を示しています。これによって、ラインのどの部分が停止しているかをひと目で把握できます。
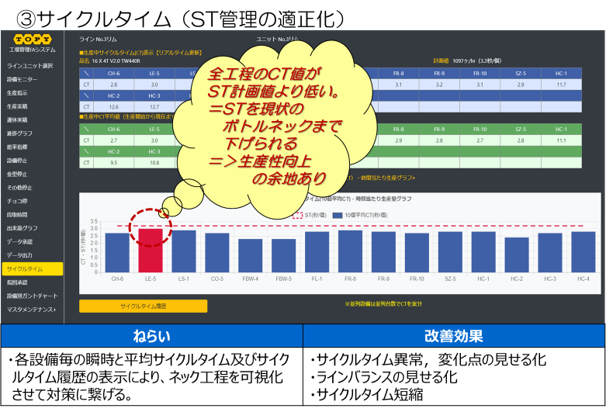
サイクルタイムの画面では、サイクルタイムのボトルネック工程を赤で示しており、ここを改善すると次のボトルネックが見えてきます。改善すべき点が一目瞭然ですから、現場にもスムーズに浸透しています。
田口 なるほど。現場がシステムでラインの状況を確認しながら、型替えやトラブルに迅速に対応できるということですね。このようなシステム構築にはどのような体制で臨み、ベンダーをどのように活用しているのですか。
武澤 基本的には私が指揮官となり、DX戦略部と技術部が実行部隊となっています。DX戦略部の中には、システム系と能率管理をするIE系の部隊があり、システム構築および改善手法の考案を担当しています。さらに、技術部に制御システムや機械システムを構築する設備戦略室もあります。スマートファクトリー推進は、先ほどご紹介した神奈川製造所の省エネの取り組みの省エネマイスターだったスペシャリストが主力となりシステム構築に取り組んでいます。制御系の人財なので、PLCと現行システムの相性も判断できます。
また、これまでのシステムは社外システムを利用していました。しかし、この方法では思い通りのシステムは構築できません。よって、今後のCPS構築は、自社開発とすることを命題にしています。これまでのシステムはベンダーに頼らざるを得なかったのですが、新しいデジタルツインの設備稼働監視は、すべて自社開発とする方針です。
田口 そうなのですか、そこまで自社で担われるとは驚きです。
武澤 お付き合いしていたベンダーは取引が長くなるほど費用が増し、頻繁に担当者が変わることがあったので、担当者が勉強してできることを増やし、依頼していたデータ変換なども自社で行うようにしました。さすがにERPのバージョンアップは自社で対応ができませんが、それ以外はベンダーに問い合わせ、改善のアドバイスを聞いてから自社で対応するようにしています。
田口 内製化にたどり着いているのですね。素晴らしい体制を構築されていると思います。企業のDX責任者の方は、内製化を進めたい現場とベンダーの板挟みになっているケースが多いのですが、御社はそうした状況に陥ることなくDXを推進されているようですね。
武澤 ERP刷新チームのメンバーが現場の抵抗にひるむことなく、強い意志を持ってスマートファクトリー化に取り組んでくれたおかげです。刷新チームにシステム系人財だけでなく、IEや技術系人財を組み入れたことも奏功したと思います。
人財育成に大きな課題 トピー流育成方法は?
田口 先ほどインダストリー4.0対応で構築されたスマートファクトリーの上にDXがあるというお話がありましたが、この先の戦略をどのように描かれているのでしょうか。
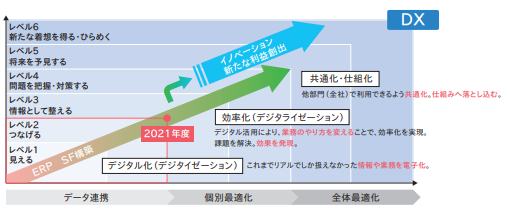
武澤 当社グループが目指すDX戦略のロードマップに対し、現在はレベル4の「問題を把握・対策する」というところまで来ています。これからは将来を予見し、新たな着想を得ていくというレベル5、6の取り組みに移っていきます。
前中期経営計画のDX戦略では、ERP刷新とスマートファクトリー構築を基本とした業務改革推進を掲げていました。2025年までの現中計では、情報を活用した経営の高度化に踏み込むべく、「データドリブンな日常の実現」に向け、個別に保管された情報のオープン化と、データに基づく意思決定・改革の推進に取り組んでいます。次期中計では「サイバーフィジカルな日常の実現」のため、冒頭でお話ししたCPS構築の完成を目指します。
田口 そのために、今後乗り越えていくべき課題は何でしょうか。
武澤 1つ目の課題は、CPS構築に向け、稼働状況の変化点を捉えたシステムが、自律的に適正条件を見出し、フィジカル空間に戻すことです。例えば、生産設備に振動計などを付け、その情報をAIに分析させ、まずは正常状態を認識させます。この正常状態に対する変化点をサイバー空間でAIに自律的に監視させ、変化を捉え異常を検知した場合、フィジカル空間に予知アラートを発信し、故障する前に点検・修復することで、設備原因による運休を防ぎます。現在、このモデルシステムを研究開発中で、予知予防保全につながる稼働監視画面の自社開発を2023年4月から始めており、近々その基本画面が完成する予定です。
2つ目は、さまざまな高ストレス作業の自動化推進です。重筋作業の自動化は引き続き取り組みつつ、生産計画や検査作業など、個人のスキルで判断していた作業の自動化にも着手します。すでに鉄スクラップ解析AIシステムを開発する株式会社EVERSTEELと、鉄スクラップの等級やダスト量を判定するAIシステムを共同開発しています。従来は検収員が目視で行っていた作業ですが、下の方に溜まっているダストの判定までできるようになれば、製鋼の生産性向上にもつながります。
また、4人がかりで行っている塗装後のホイールの表面検査作業もその対象です。目を凝らし細部までチェックする大変な作業ですが、画像処理情報をAI判定により過検出したものだけをチェックできれば、検査数を大幅に削減でき、少人化も可能となります。このシステムはすでに現場に試験機を入れ、実機検証をしているところです。
さらに、生成AIを活用した業務効率化にも取り組んでいます。海外グループの現地との打合せに有効な翻訳や議事録作成などに積極的に活用し、より高度な業務に着手できるようになればと考えています。しかし、そのためにはやはりX(トランスフォーメーション)人財の育成が大きな課題です。
自分や部門の状況を把握して改善のためにどのようなデータを取得するのか、自分が獲得したスキルを捨ていかに新しい改革へと向かうのかについてが、とても大きな課題だと思っています。
田口 DX人財の育成は確立されたプログラムもなく、非常に難しいところですね。御社ではどのように進めているのでしょうか。
武澤 当社では、IEやQCといった観点から解析の基礎技術を身につけることが大切だと考え、新入社員には基礎教育をしっかりと行っています。「変化は歓迎すべきこと」という価値観や、慣習を健全に疑う視点を養うことも重要視しています。
近年は人材不足が叫ばれていますが、これは私の持論なのですが、実は人の数は足りていると思うのです。不足しているのは社員一人ひとりの能力をフルに生かし、パフォーマンスを管理できる「指導者」なのではないかと感じます。そうした課題に対しても、先ほどの社内イントラを活用してコミュニケーションボード(所属長宛てに、業務に関する意見を無記名で提示できるボード)を整備するなど、システムを用いて取り組んでいます。
目的の共有と自己変革の意識がDX実現のカギ
田口 中期経営計画の進捗状況についてもお話を伺えますか。
武澤 はい。まず財務目標については、売上高営業利益率とEBITDA、ROEの全指標においてほぼ計画通りに進捗しています。非財務目標についても2030年に達成すべき数値目標に向け、CO2排出量の削減や女性管理職比率の増加は順調に推移しており、コンプライアンス違反件数は0件を維持しています、一方、労働災害件数は、数値目標が年間0件と非常に高いため、まだ達成には至っていません。特にカーボンニュートラルに関しては、再エネ利用や燃料転換、既存プロセスの見直しにより、2030年までの目標達成の目途は立ちつつあります。
人財確保・離職防止の観点からも、フレックス制や育児休業制度、不妊治療のための休職制度などを拡充してきました。一度他社へ転職した人財がジョブリターン制度を利用して復職するケースも出てきており、社員に優しい働きやすい会社になってきたと思います。
田口 ありがとうございます。最後に、今後DX戦略を推進していくにあたっての意気込みをお聞かせください。
武澤 DX戦略で最も大切なのは「X」、トランスフォーメーションです。どんなに優秀な社員でも、自らを変える意識がなければDX戦略にはついてこられません。当社グループには「考動」という言葉があります。自ら学び、考え、行動に移し挑戦していける人財が、戦略をリードしていくでしょう。
そのためには、我々が改革の目的・目標を明確かつ定量的に示さなければいけません。ステップの条件を設定し、スモールテーマで業務改革の効果を実感してもらい、その達成感や期待感から自己改革に取り組む気持ちを持ってもらいます。私自身も初心を忘れず、自ら新しいことを学び、社員と同じ目線に立ちながらDXというテーマに挑戦していく所存です。
田口 本日は貴重なお話をお聞かせいただき、ありがとうございました。
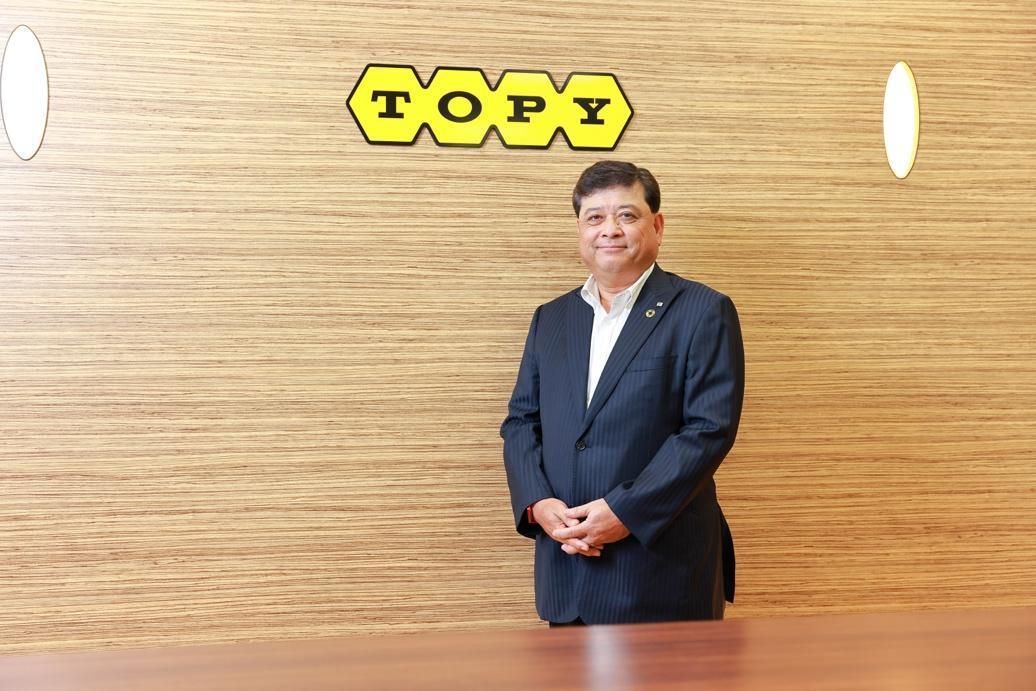
【関連リンク】
トピー工業株式会社 https://www.topy.co.jp/
株式会社コアコンセプト・テクノロジー https://www.cct-inc.co.jp/