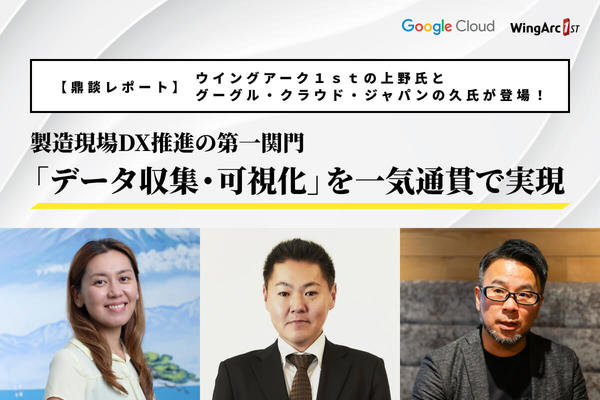
多くの企業でDX推進が叫ばれている今、鍵を握るのがBIツールを始めとしたソフトウエアです。しかし、何から取り組むべきか迷っている企業も多いのではないでしょうか。
そこで今回、「製造現場DX推進の第一関門『データ収集・可視化』を一気通貫で実現」というテーマで、2023年7月5日にウイングアーク1st主催のウェビナーが開催され、同社の上野智宏氏とグーグル・クラウド・ジャパンの久夏子氏、コアコンセプト・テクノロジー(CCT)CTOでKoto Online編集長の田口紀成氏が登壇しました。本記事では、そのウェビナーのダイジェストをお届けします。
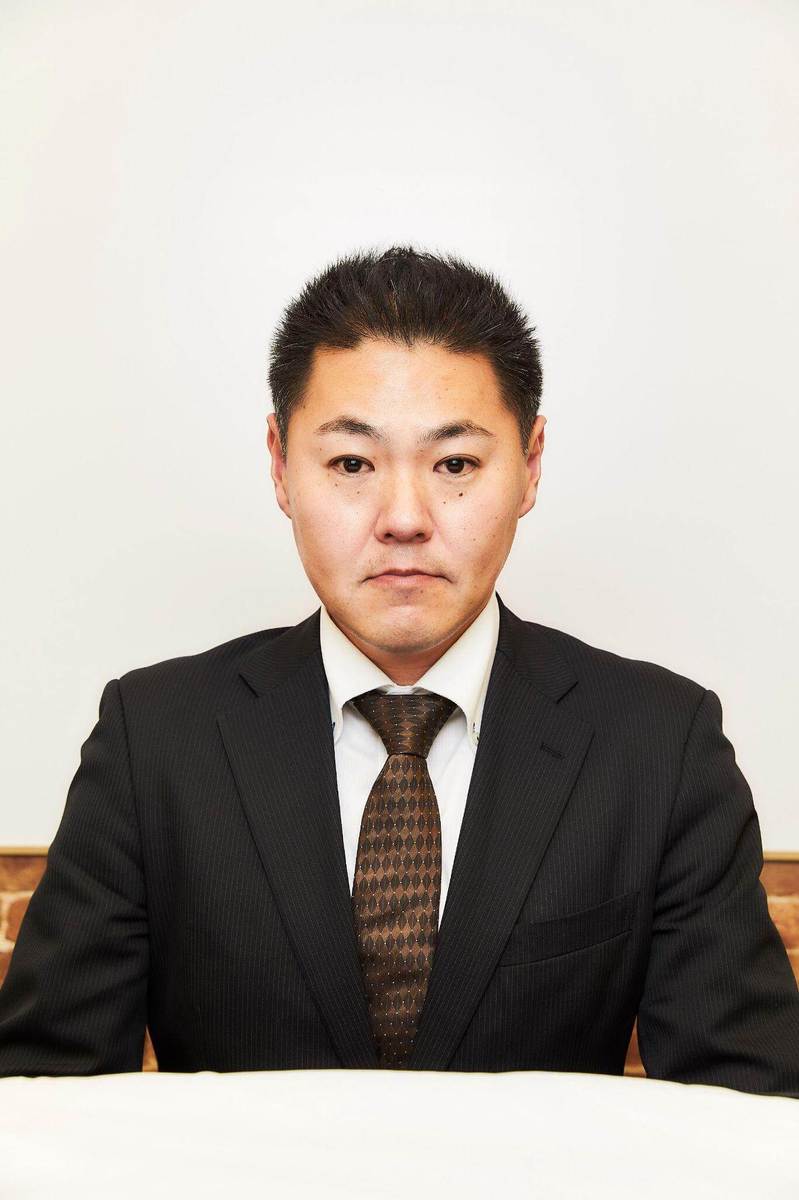
SIerで製造業向けのシステム開発、医療機器製造メーカーでの社内SE、エレクトロニクス商社で製造現場向けのプリセールスなど製造業に関連するキャリアを重ね2016年にウイングアークへ入社。現在は、テクノロジーとセールス双方の側面から製造業向けのソリューション企画やデータ活用提案の業務に従事。
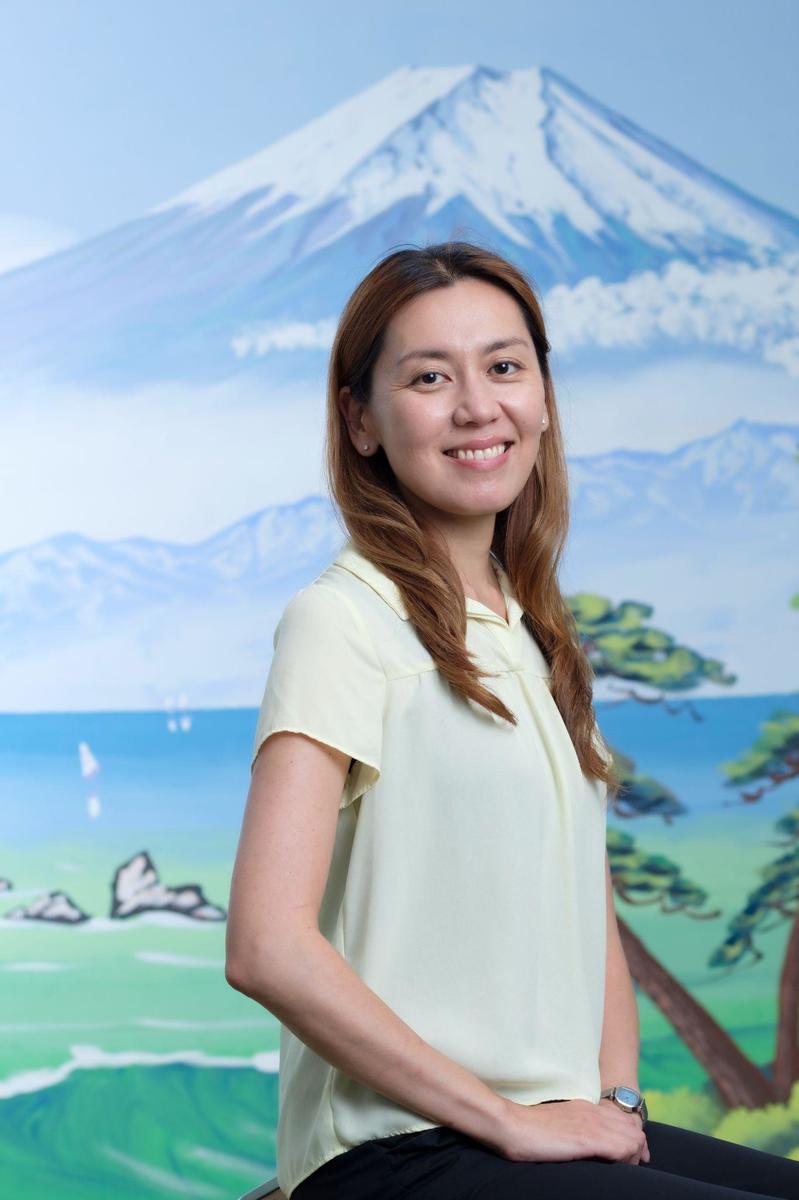
グローバル企業にて、パートナーとのアライアンス、共同戦略立案に従事。USにてMBA取得後、レッドハット株式会社を経て、2020年にグーグル・クラウド・ジャパンへ入社。Manufacturing, SupplyChain & Logistics を中心にクラウド、データを活用したIndustryソリューションをパートナー企業とともに推進。
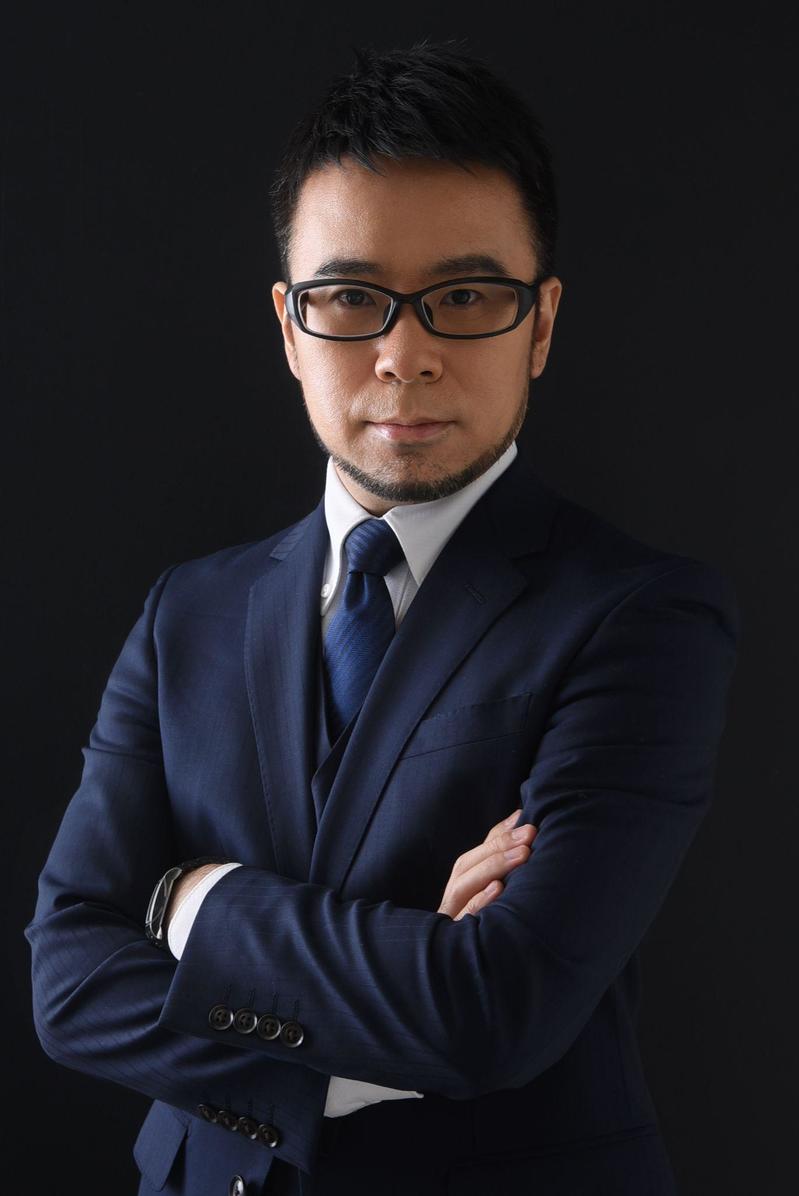
2002年、明治大学大学院 理工学研究科修了後、株式会社インクス入社。2009年にコアコンセプト・テクノロジーの設立メンバーとして参画し、3D CAD/CAM/CAEシステム開発、IoT/AIプラットフォーム「Orizuru」の企画・開発などDXに関する幅広い開発業務を牽引。2015年に取締役CTOに就任後は、ものづくり系ITエンジニアとして先端システムの企画/開発に従事しながら、データでマーケティング&営業活動する組織/環境構築を推進。
目次
製造現場のデータの可視化・分析に適した「MotionBoard」
上野氏(以下、敬称略) ウイングアーク1st株式会社の上野と申します。本日はよろしくお願いいたします。本セミナーでは、「現場データを可視化・分析する製造業に適したMotionBoard」と題しまして、弊社が開発しております、BIツールの「MotionBoard」についてご紹介いたします。
ウイングアーク1stは東京・六本木に本社を構え、ソフトウエアやクラウドサービスの開発・販売・保守を手掛ける、純国産のパッケージソフトウエアメーカーです。会社の会計情報などを記録する帳票とBIツールの2本柱で事業を展開しています。
「MotionBoard」は、さまざまなデータをリアルタイムに可視化する、データ活用ダッシュボードツールです。プログラミングが不要なので、ITの知識がない方でもスタイリッシュな画面を構築することができる、表現豊かなところが特徴です。製造業のお客様ですと、特にハードウェアを制御・運用するOT部門や生産技術部の方など、ITリテラシーがそれほど高くない方にも利用されています。
「MotionBoard」は製造業専用のツールではなく、さまざまなシーンで活用できるBIツールです。例えば、売上高や営業利益などの経営指標の可視化やKPI管理といったマーケティング、営業、さらには人事にもご活用いただけますが、特に製造業のお客様が非常に多いのが特徴です。製造業のお客様が多い理由についていくつかご紹介します。
まず1つ目は、「リアルタイム連携機能」の搭載です。他社のBI製品はリアルタイムデータの可視化は難しいのですが、「MotionBoard」では設備側からデータベースにデータを蓄積すると、そのまま変更・登録されたタイミングでダッシュボードに反映されます。データの蓄積と同時に可視化ができるので、設備の稼働状況を監視するのに活用できます。また、スマートフォンのGPSデータを使い位置情報もリアルタイムに可視化できるので、工場内の動線分析にご活用いただくケースもあります。
2つ目は、製造業独自の表現がかなり豊富に搭載されている点です。例えば、QC7つ道具(製造現場の課題を見える化する手法)である管理図分析やBOMといった専門ツールの領域レベルのことも標準で備えています。これも製造現場で活用されている大きな理由です。
3つ目は、「3Dマップアイテム機能」が挙げられます。ノンプログラミングで簡単に構築することができ、動的にオブジェクトの配置やスタイル変更が可能ですので、デジタルツインのようにご活用いただくお客様もいらっしゃいます。
4つ目は、BIツールのダッシュボードから直接データを入力できるところです。BIツールは大量のデータを取得してグラフ化するものですが、「MotionBoard」なら入力画面も作ることができます。例えば、作業日報などを紙で運用されているお客様がタブレットで作業日報を入力し、そのデータを別のダッシュボードで可視化することで、現在の進捗状況をリアルタイムに把握することも可能です。
この他にレポート出力も「MotionBoard」の武器です。ダッシュボードで使用しているデータと作成したアイテムは、ExcelやPowerPointの帳票に出力することもできます。その際は単純に出力するのではなく、工場の稼働状況のデータであればライン別にExcelのシートを分ける、PowerPointのレポートを分けるなどを設定1つでできることが、製造業のお客様に高く評価していただいています。
このように、製造現場での活用用途はさまざまあります。設備の稼働状況のリアルタイム監視やマン・マシンチャート、トレーサビリティ、統計的品質管理、工場内動線分析など、いろんなところで活用できるのが「MotionBoard」の特徴です。
「MotionBoard」の活用事例
上野 引き続き、製造現場DX推進の実現に向けて、「MotionBoard」の活用事例をご紹介します。
一般的な企業が採用する方法では、計画データは上位システムや生産管理システム、品質系のデータは品質検索システム、設備データは収集ツールを使ったデータベースに格納しています。それに対して「MotionBoard」では、さまざまなデータを集めて1つの画面で仮想統合し、データ活用の幅を広げられるといった特徴があります。
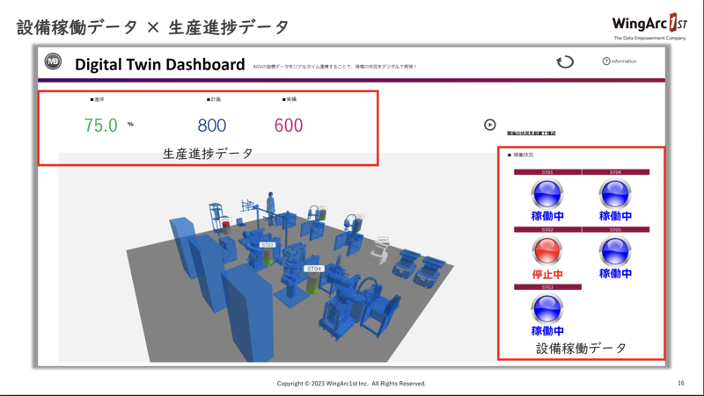
こちらのダッシュボードは、設備稼働と生産進捗のデータを組み合わせて、1つの画面で表示したものです。設備から稼働情報を収集してリアルタイムの様子を示し、信号機のようなもので停止状況も表現しています。例えば、タブレットからどの製品をいくつ作ったかなどの生産進捗を入力し、多くの方が共有できる形でダッシュボードに表示することで、意思決定の質・スピードが向上できるといった特徴があります。
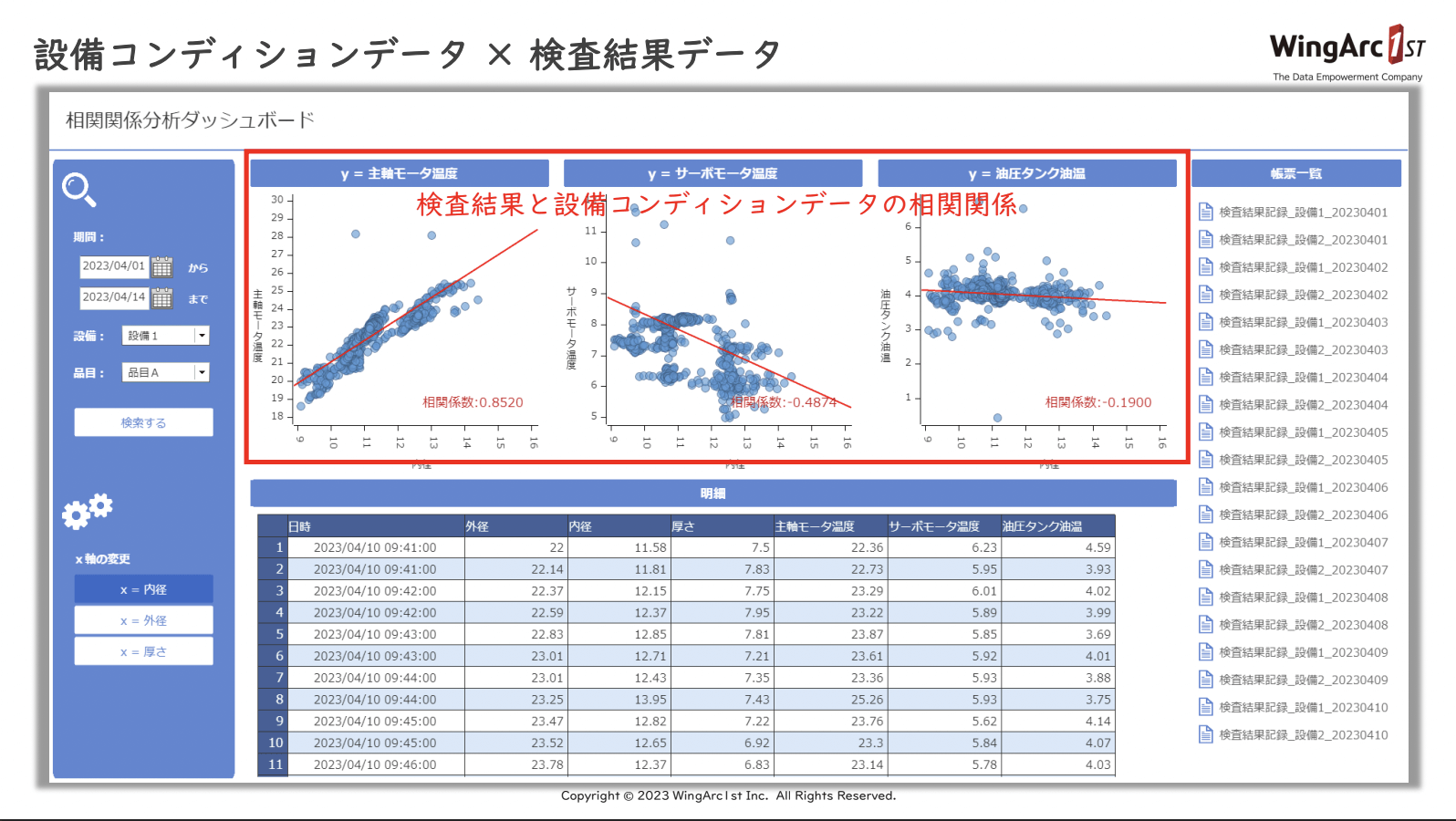
こちらのダッシュボードは、検査結果データと設備コンディションデータを組み合わせたものです。ここでは検査結果データと設備から収集したコンディションデータ、例えば主軸モータの温度とサーボモータと油圧タンクなどのデータと品質結果に相関関係があるかといったところを分析しています。
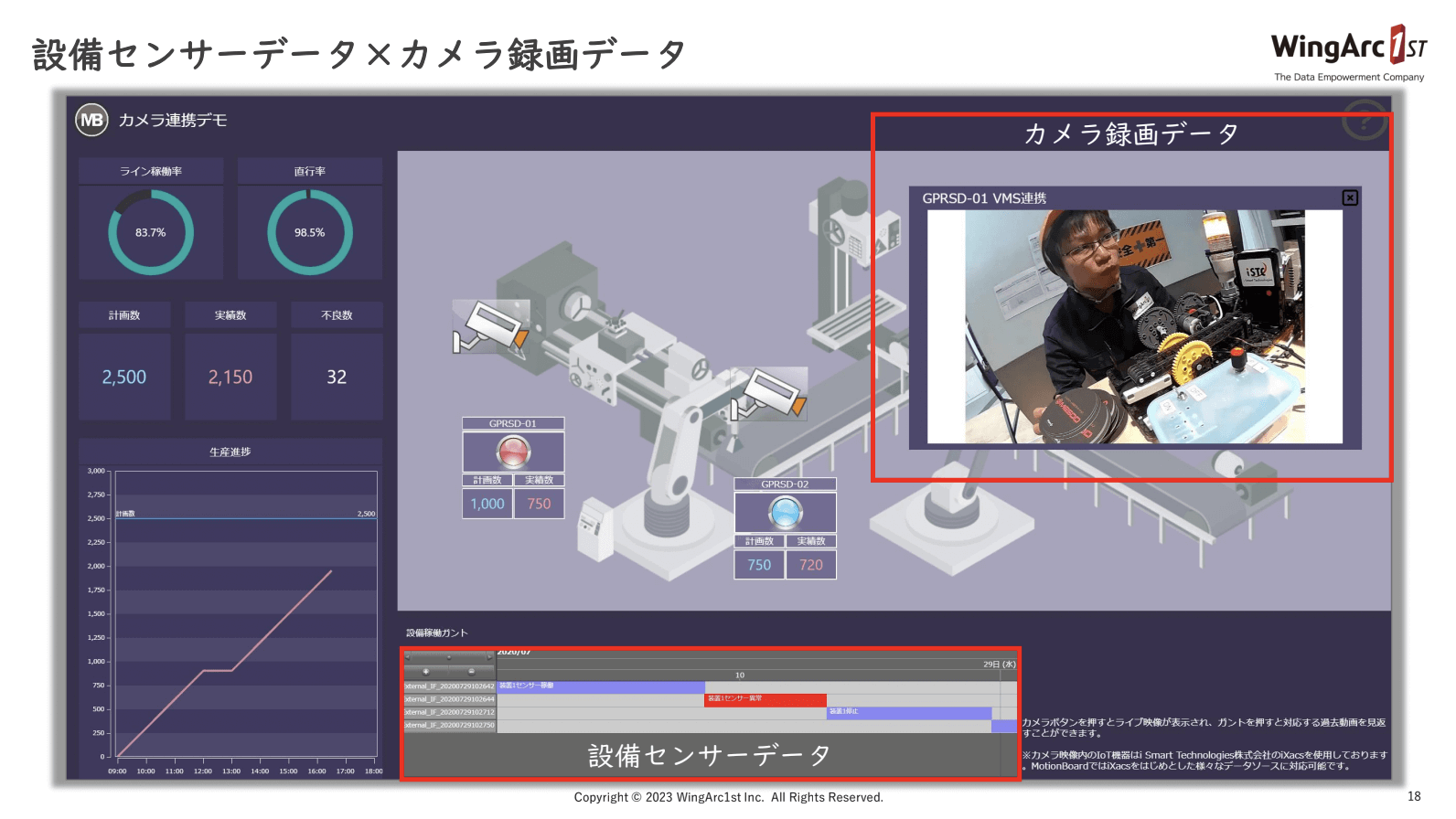
こちらのダッシュボードに関しては、設備生産データとカメラの録画データを組み合わせたものです。設備側に何らかのセンサーを設置した上で工場をリアルタイムに監視し、ダッシュボードに何か異常が表示されたところをクリックするとその時間帯の録画データが再生され、異常の原因を解明できる可能性があります。こういった機能も製造業のお客様に好評です。
本日は時間の都合上、少ない活用事例となりましたが、他にも製造業DXの実現に向けて情報を発信しています。何から手をつけるべきか分からないなど、お悩みの方は気軽にお問い合わせください。
クラウドで実現できる製造IoTデータ基盤とユースケース
久氏(以下、敬称略) グーグル・クラウド・ジャパン合同会社で、インダストリーソリューションを担当しているパートナーマネジャーの久と申します。本日は、Google Cloudで実現できる製造IoTデータの基盤「Manufacturing Data Engine」のユースケースをご紹介いたします。
最初に、グーグルはインダストリー(製造業)のトレンドについて、基本的にトランスフォーメーション(変革)が大きな軸になると考えています。トランスフォーメーションの中でも「業務プロセス改善」「AI利用への関心の高さ」「長期にわたるサプライチェーンの混乱」「従業員の不足/デジタル人材の不足」「気候変動/サステナビリティへの備え」の5つが軸になります。
インダストリー関連の課題を抱えている方がいる中で、どうビジネスを変革していくかが大切です。Google Cloudとしてはデータをどう活用して、どう分析するかというところに軸足を置き、ビジネスをどう加速させるか、AIをどう活用していくか模索しています。
今ある状態をデータで見えるようにするために、プロダクトのエンジニアリングから生産管理、製造、組み立て、品質管理、物流、配送、販売、お客様の体験、保守・運用まで一貫して行い、ここにデジタルツインやサプライチェーンツインなどを用いて、AIもしくはお客様のデータと組み合わせて「Intelligent Manufacturing」と呼ばれる製造プロセスの最適化を目指しています。
今後、さまざまなデータソースを活用してユースケース(システムの仕様)を作っていきますが、エッジ(ネットワークの端末)のソリューションやロボットとの連携、コネクティビティ、パートナー様のコンソリューション(コンサルティングとITソリューションの融合)が欠かせない形になっています。
Google Cloudが考えるミッションは、メーカーがクラウドとエッジでデータを分析し、AIを使用してビジネスの優先事項を達成できるようにすることです。最終的にどのようなビジネスを 考えていくか、何を優先すべきかを見据えてデータやAIを活用することを目的にしています。
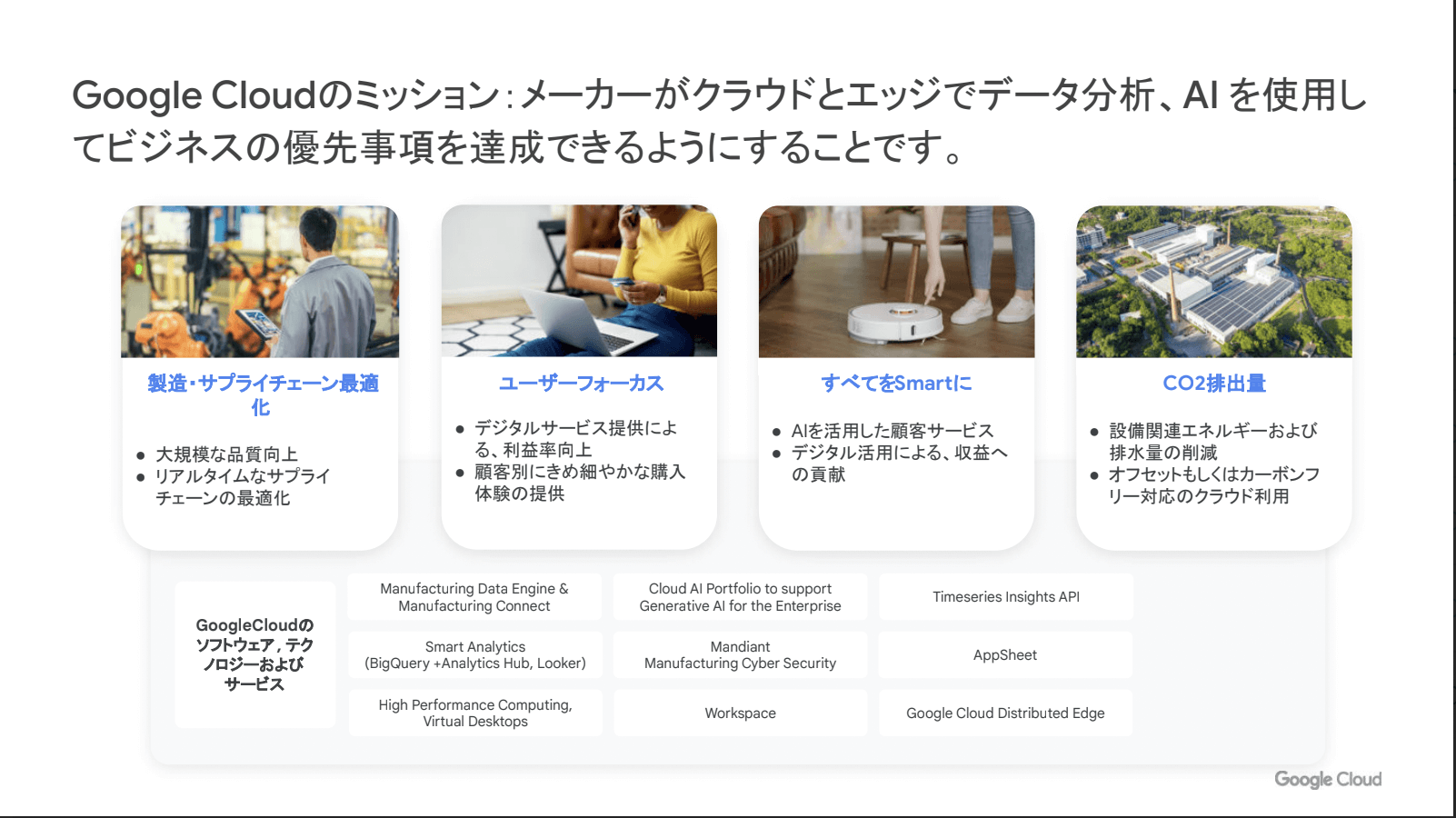
具体的なミッションとしては、「品質向上/リアルタイムなサプライチェーンの最適化」、「デジタルサービスによる利益率向上」「AIを活用した顧客サービス」「設備関連エネルギーおよび排出量の削減」などが挙げられます。
Google Cloudのミッションに付随するソフトウエアのテクノロジーやサービス関連のユースケースから見ていきます。このページ(以下画像)で説明しているのは、インダストリーに特化したテクノロジーです。
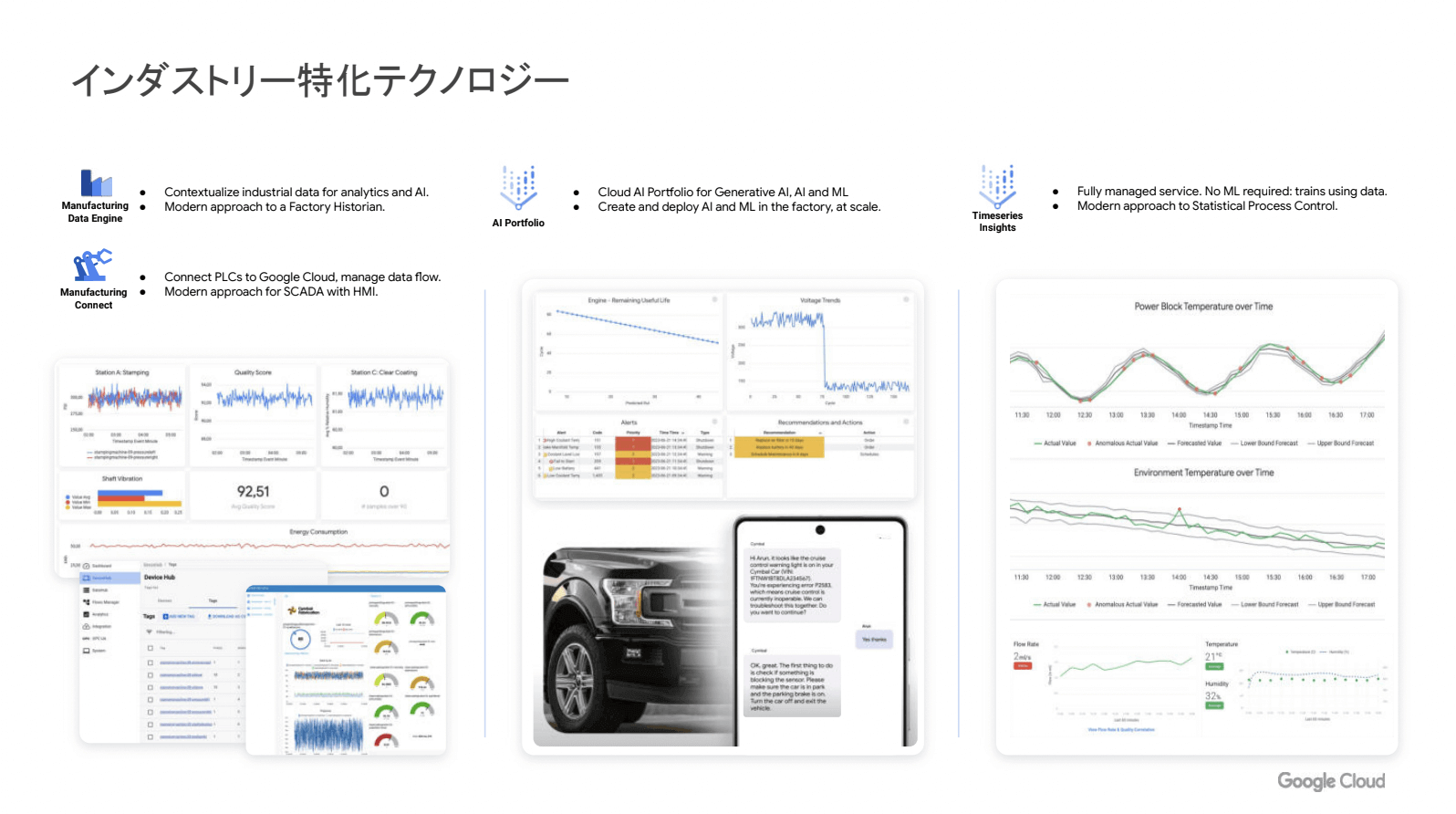
ここでいうインダストリーは製造業が対象で、一番左側の「Manufacturing Data Engine」と「Manufacturing Connect」が、今ある工場や生産設備のデータを格納・見える化している部分です。
次に真ん中のAI Portfolioは、今後AIを活用してGoogle Cloud がどのようなユースケースを出すのかを示しています。右側のTime Series Insightsは時系列データと、今あるデータだけではなく過去のデータをどう分析に生かすかについても、マネージドサービス(クラウドなどの保守・運用を外部委託)としてリリースする予定になっています。
Google Cloud利用のユースケース
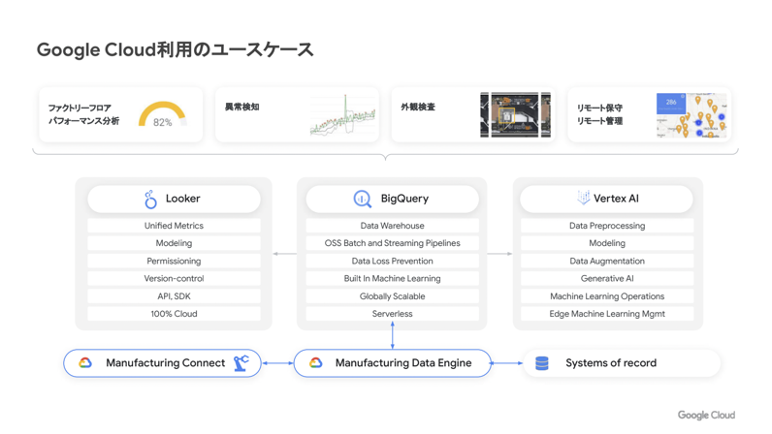
Google Cloudを利用する際の4つのユースケースと、システムの構成
久 ユースケースに関しては、大きく4つのテーマを掲げています。各テーマは「ファクトリーフロアのパフォーマンス分析」「異常検知」「外観検査」「リモート保守管理・リモート管理」の4つに分かれています。
重要なのは「Manufacturing Data Engine」です。どうやって「Manufacturing Data Engine」のBigQuery(データの管理と分析を支援するためのデータベース)にデータを入れるのか、どう保存するのかが課題となります。以下(下記画像)が「Manufacturing Data Engine」のアーキテクチャを表し、左側がデータソースになっています。
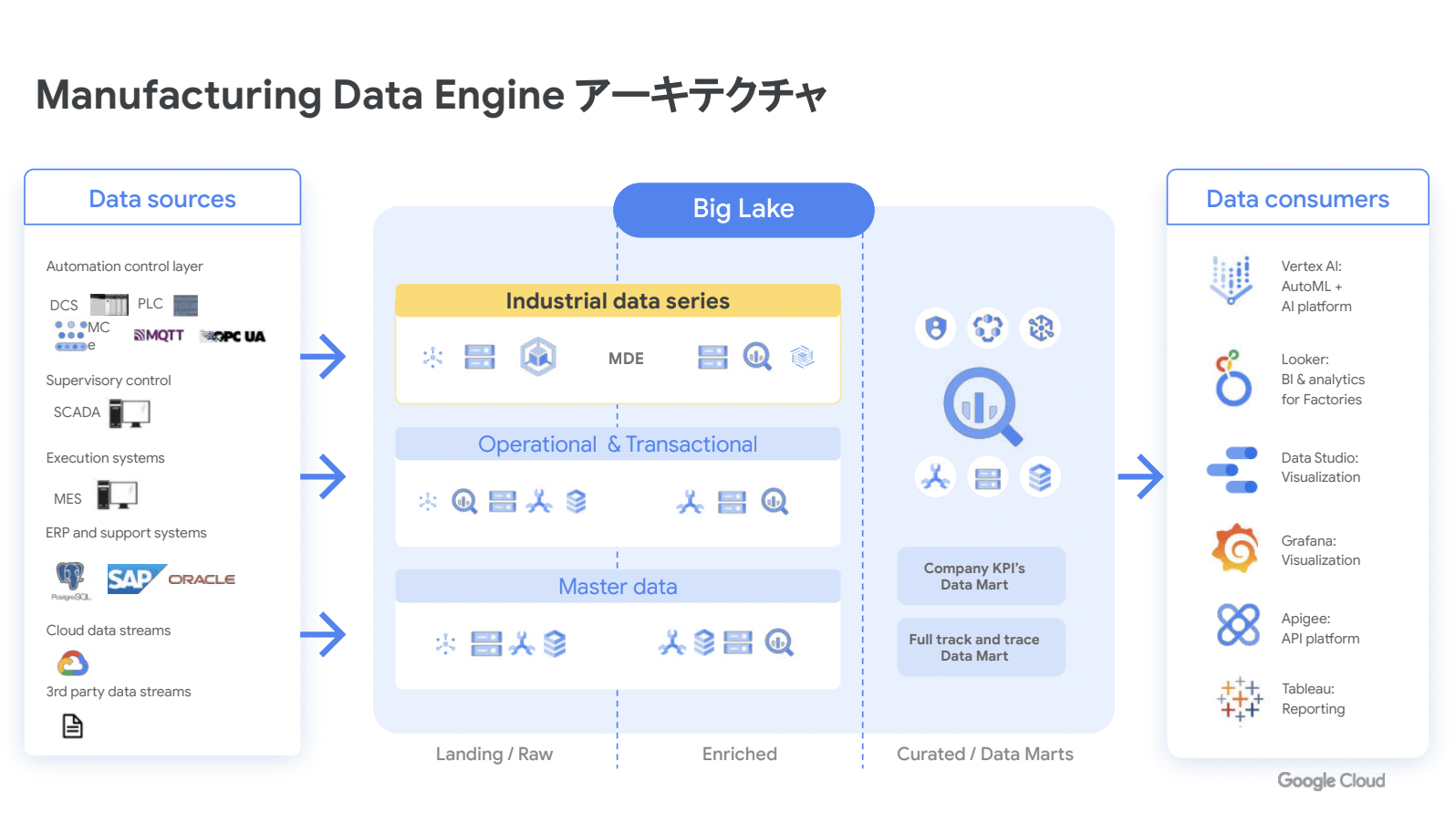
工場のファクトリーフロアやMES(製造実行システム)、SCADA(監視制御システム)、SAPなど、第三者のデータがデータソースになってくるのを、インダストリアルデータ(サプライチェーンを構成する企業間のデータ)として確保するというのが、「Manufacturing Data Engine」の大きな特徴になっています。これらのデータをData Consumers(消費者のデータ)でどう活用・可視化するのかまでが アーキテクチャになっています。
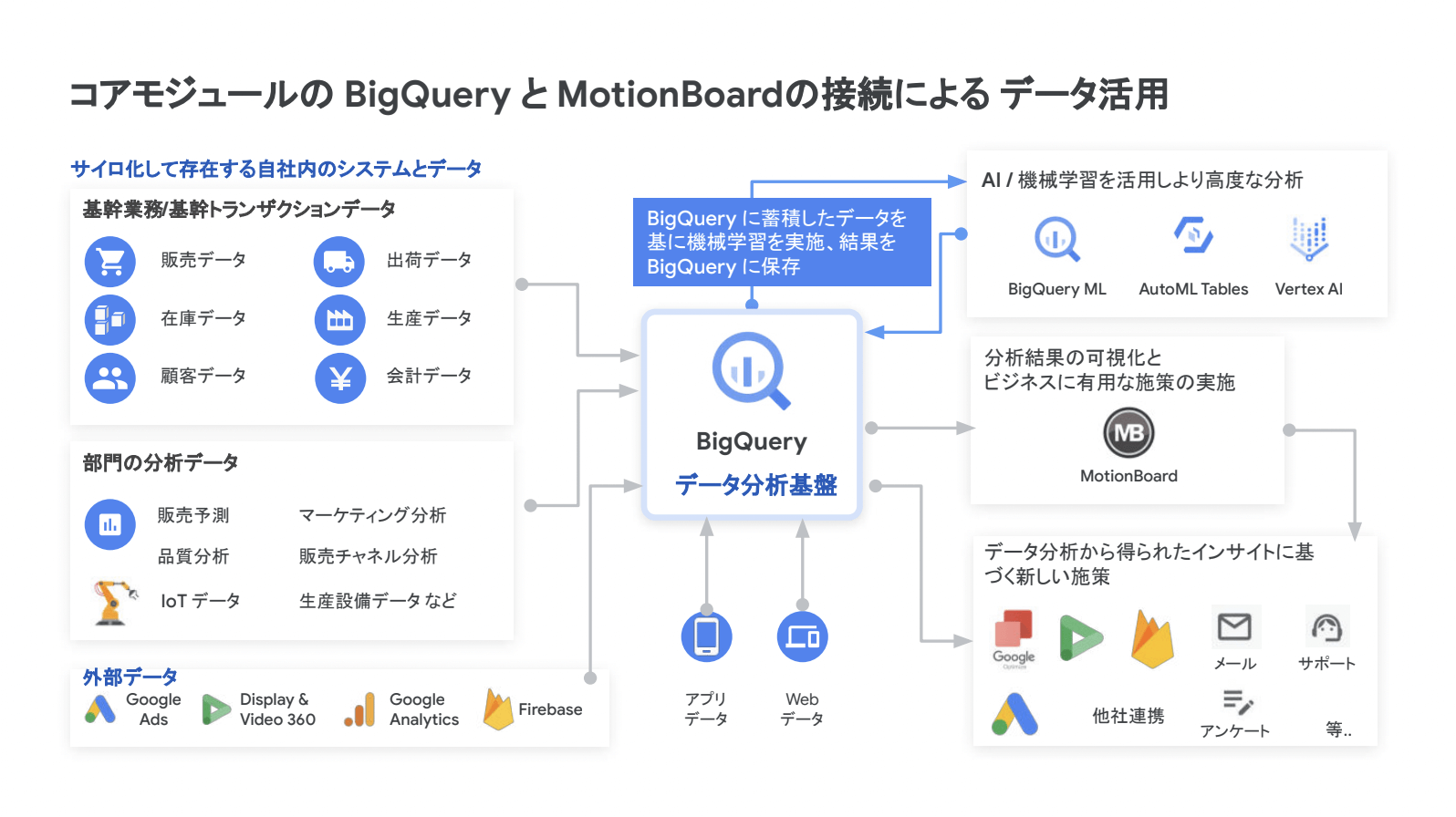
こちらのスライドでは、「MotionBoard」と連携する際のイメージを描いています。Google Cloudを中心にBigQueryという大きなデータ分析の基盤を置き、そこにサイロ化(各部門のシステムが連携できていない状況)している自社内のシステムのデータや、各部門の分析データ・分析に必要な外部データを入れます。これらのデータと「MotionBoard」を連携させて、分析結果の可視化やビジネスへの活用をしていただくことになります。
Google Cloudの活用事例
久 ここからは、3社の活用事例をご紹介いたします。
1社目はフォードモーター社です。どうやって世界中の工場からデータを収集して活用するのかという課題がありましたが、「Manufacturing Data Engine」を使用し、BigQueryをデータファクトリー(データの一元化)として活用していただく形で結果を出されています。分析をするデータの一元化ができたことで、工場の最適化が実現しました。
2社目はドイツの老舗陶器メーカーとして知られる、ビレロイアンドボッホ社です。エネルギーコストを下げたい、陶器のクオリティを維持しつつプロダクション(生産)のスピードを上げたい、ビジネスプロセスを透明化したい、というニーズからBigQueryを利用しました。また、外観の検査のためVisual Inspection AIという外観検査のソリューションを使い、エネルギーコストの低減とプロダクトのクオリティ向上を実現しました。
3社目はドイツの老舗印刷機メーカー、ケーニッヒアンドバウアー社です。こちらの場合、「Manufacturing Data Engine」を通じて世界中にある自社の印刷機のデータを利用することで、今までは単発でしか確認できなかった機械の不具合と、どういう状況でパフォーマンスが低下するのかを分析しました。
最後に、「Manufacturing Data Engine」の主なベネフィットをまとめさせていただきます。まず、1つ目は直接的かつ実測可能な工場オペレーションが可能になるので、感覚ではなくデータに基づいた品質向上ができることです。
2つ目はコストパフォーマンスが高く、スケールアップ(性能を上げること)とスケールアウト(システムの処理能力を高めること)ができることです。導入が簡単なので、小さく始めて他 の工場に展開することも難しくありません。複数の工場で持っていた重複データの一元化も可能です。
3つ目は、「Manufacturing Data Engine」上に、パートナー様のさまざまなソリューションを載せることが可能になっています。これによりベンダーロックイン(特定のベンダーに依存して乗り換えできない状況)を防止し、みなさんの業務の課題に応じてGoogle Cloudとパートナー様のソリューションをお使いいただくことができます。以上になります。ありがとうございました。
製造現場のデータ一元管理のスタートライン
田口氏(以下、敬称略) コアコンセプト・テクノロジー(CCT)の田口です。本日は「製造現場のデータ一元管理のスタートライン」と題してお話しします。
私自身はモノづくり系のITエンジニアとしてIoTの開発に関わってきた中で、IoTを導入できるお客様とそうでないお客様を見てきました。本日は、このような経験からIoTなどを導入する際に、何から始めるべきかについてお話させていただきます。また、当社は今年の3月にWebメディア「Koto Online」を立ち上げ、製造業における技術開発やESG、DXの進め方について情報を発信させていただいています。よろしければご覧ください。
【関連リンク】
Koto Online https://www.cct-inc.co.jp/koto-online/
本日のセミナーでお伝えしたいことは、「原価把握と最適化を目的として製造現場のデータを把握する」についてです。
現在はビジネス環境の変化が大きい時代で、最近ではサプライチェーンと為替の変化が際立ちました。これらを予測することはそもそも難しいので、企業はDXによってスピード感を持って変化に対応することが求められます。ただし、言葉で言うのは簡単ですが、製造の現場においてそのスタートラインに立つのは難しいです。そこで本セミナーでは、製造現場のデータ一元管理のスタートラインに立つために必要なポイントについてお話しします。
具体的には、「データ把握の背景」や「目的設定」、「製造現場のデータ把握に至るまでの流れ」、「上司の説得や予算の確保」、「どのような会話の流れで上司を説得したらいいのか」、「本セミナーでご紹介いただいた製品を組み合わせて、製造現場の見える化を達成するのか」について解説します。また、自社で実行するのが難しい場合、当社が全体のシステムインテグレーション(情報システムの構築)をお手伝いします。
課題解決のファーストステップは現状把握
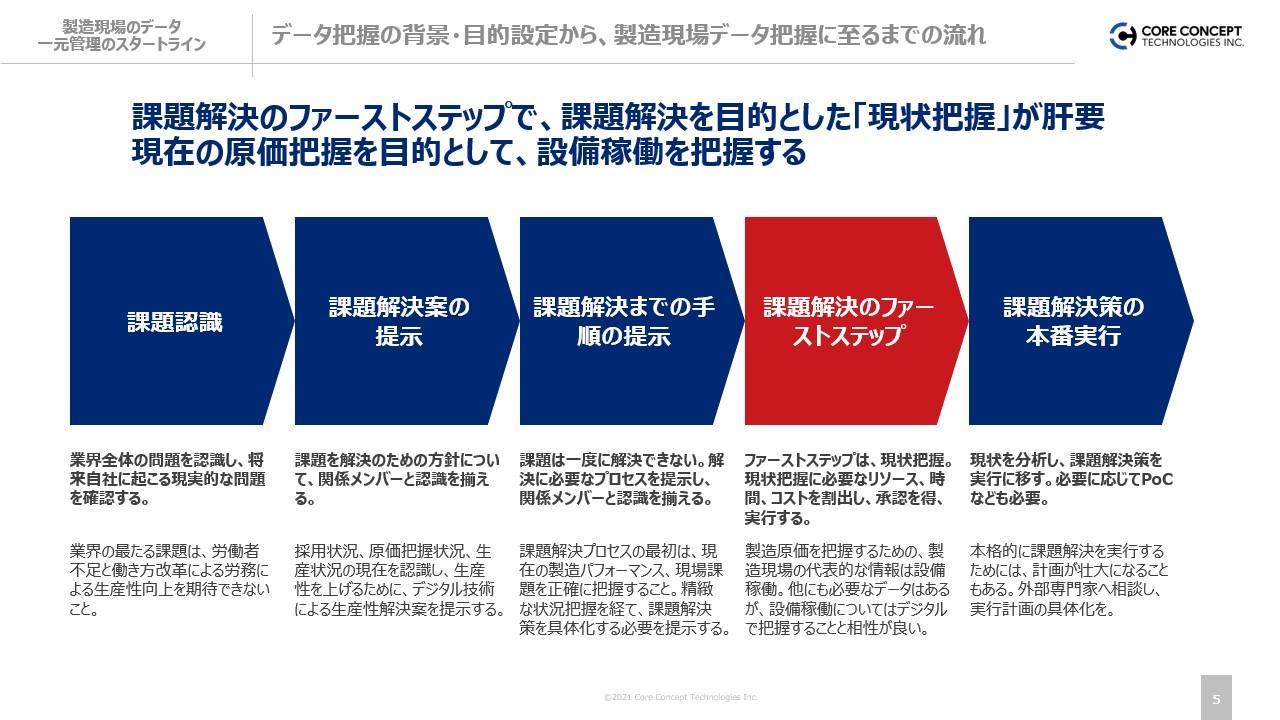
田口 まず、製造現場のデータ全体の中で、課題解決のファーストステップとして、「課題解決を目的とした「現状把握」が肝要です。現状把握が重要であるロジックとしては、今の設備稼働の状況を確認できないと何が課題なのかを正確に把握することができないという点が挙げられます。
そのロジックに至るまでの流れとして、最初に「課題認識」が必要です。例えば、業界全体の課題として、デジタル人材が不足しているなどの課題を認識することを指します。
次いで「課題解決案の方針と手順を提示」する必要があります。現状を見える化できないと対処すべき課題を知ることができません。この時に現場をデジタル技術によって見える化することが必要になり、その先に「課題解決の本番実行」として施策を決めて導入を進めていく流れとなります。
大きな課題認識としては、労働人口が減り続けているのと働き方改革によって、従業員と労働時間を増やして課題を解決する手段が取れない状況になっている点が挙げられます。そのため、従業員を採用してこれまでと同じ生産性を維持することはほぼ不可能です。デジタル化を実現し、生産性を高める必要があることを認識しなければいけません。
さらに「課題認識」は、数字で理解することが必要となります。具体的には、売上高と営業利益、従業員数の関係を把握し、会社の成長と従業員数の相関関係を明らかにすることが大切です。
生産性は結局のところ、売上高がどれだけの従業員数で生み出せているかということに尽きます。この数字を見たときに、どう推移しているかを把握できなければいけません。今は全社単位で話しましたが、自身が担当する領域のパフォーマンスを把握するために、事業や案件、製品開発など、それぞれでも見ておく必要があります。
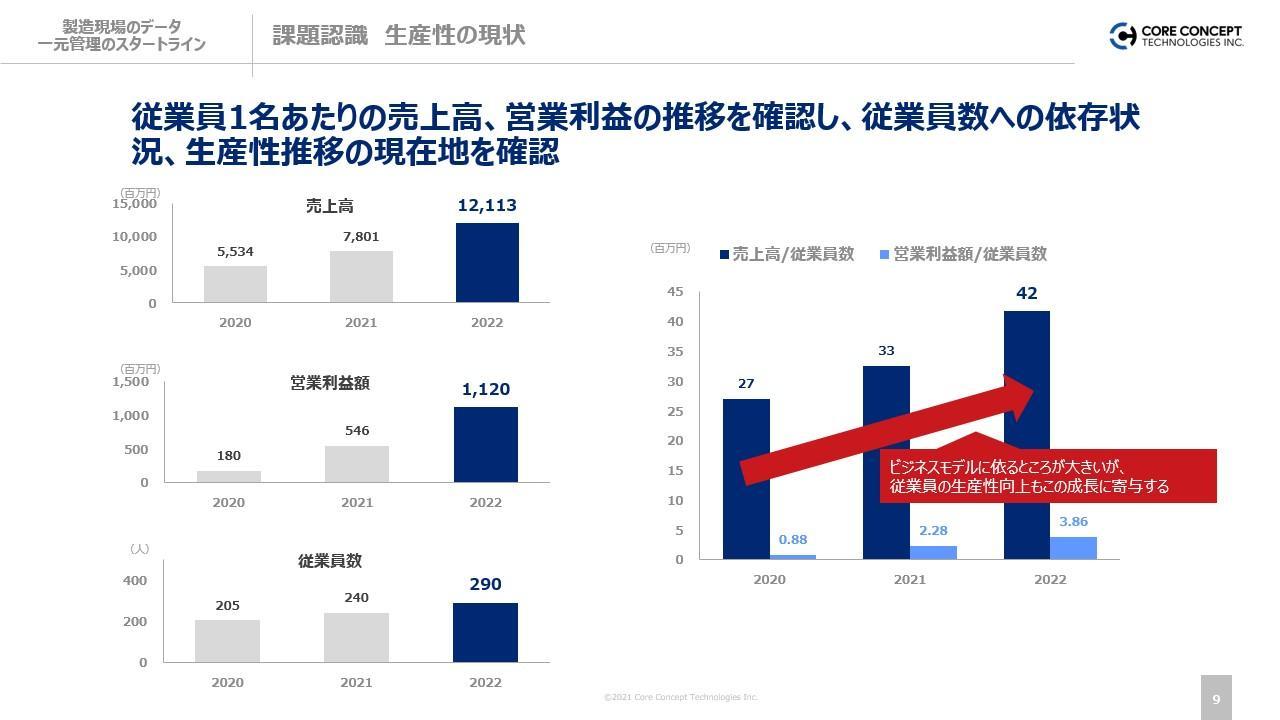
生産性が可視化できると、従業員1人あたりの売上高や営業利益、生産性の推移などが見えてきます。こちらの数字(上記画像)は当社のものですが、我々もこういった数字を重視していて、実態がどうなっているかを確認して、何をすべきか、どうすれば生産性が上がっていくかを常に考えながらビジネスを行っています。
実際に生産性を上げるための施策は、製造業では大きく4つに絞られます。1つ目は単価アップ、2つ目は販売数量のアップ、3つ目は原価のダウン、4つ目は固定費のダウンです。それぞれ 効果はありますが、優先順位が異なります。優先順位が高い効果的な施策としては単価アップ、次点で原価のダウンが挙げられます。この2つが利益を出すには最も効果が高いと考えられます。
ただし、お客様があってこそですから簡単に単価を上げるわけにはいかないので、原価を下げる方法を工夫することになります。工場で使う電気や部材などの調達コストを最適化することに集中するのは、そういったロジックがあるからです。ここまでのロジックを整理すると、次のような流れ(下記画像)になります。
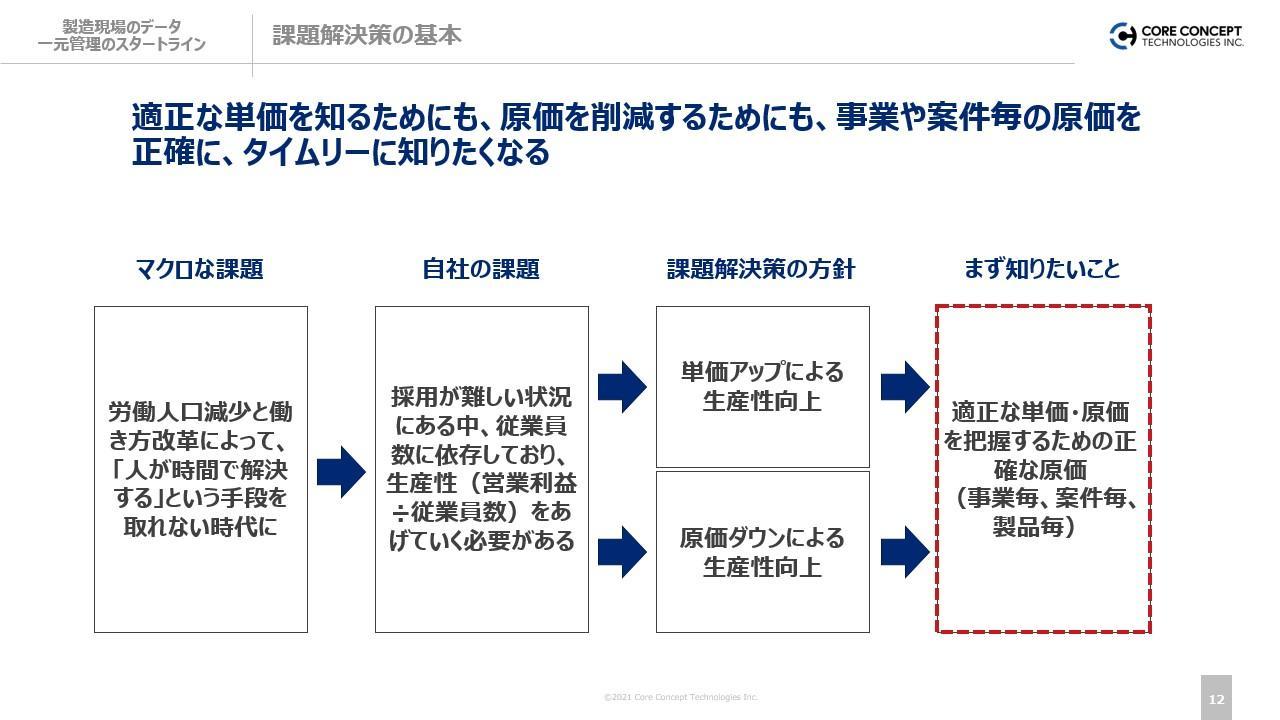
効果的な課題解決の施策には、前述のとおり単価アップと原価ダウンがあります。両方の施策を進める準備として、適正な単価を確認するために正確な原価をタイムリーに把握する必要があります。
実際に課題の解決を始めるには、現状の生産性の把握から始まり、原価・採算の把握、施策の設定・実行という流れになります。まずは生産性を把握し、次に原価・採算を把握することになります。原価には部材の調達コストや労務コスト、設備コストがあり、これらのコストを確認することで事業・案件・製品ごとに採算が良いものと悪いものが浮き彫りになります。
課題解決のファーストステップは、現状の状況を認識するために生産性を把握して、次に原価・採算を把握することが最も重要です。現状を正確に認識できないと課題解決のための施策を決めることはできません。そのため、状況を正確に把握する活動の優先順位が高いのです。
製造現場の中でも、データを収集して見える化が生かせるところは、設備コストの部分です。設備がどれだけ、どの製品のために動いたか、これを把握しましょうというのが、本セミナーのテーマとなります。
ノーコードで簡単にデータを収集・見える化
工場にある稼働設備のデータは、電流値(電気の流れる量)を用いて計測します。これらのデータは、Google Cloudの「Manufacturing Data Engine」であれば、ノーコードで簡単に集められる環境になっています。さらに「MotionBoard」で設備の稼働状況を見たいときに、コードを書かずに設備の稼働状況を把握するためのシステムを作ることができます。
実は、電流値を取るのに都合の良いアプリケーションが世の中にはありまして、最もおすすめなのが三菱電機さんの「iQ Monozukuri工作機械工具摩耗診断」です。設備の稼働状況を把握するためのデータを集めるのに便利で、電流値を簡単に取得することができます。
「Manufacturing Data Engine」から見た設備の稼働状況を把握する仕組みは、データの連携自体は非常に簡単でシンプルになっています。データをクラウドに上げる方法には、PLC(プログラム可能な論理回路の制御装置)と直接連携する方法と、OPCサーバ(工場にある複数の設備を相互接続するためのアプリケーション)を現場に置く方法があります。
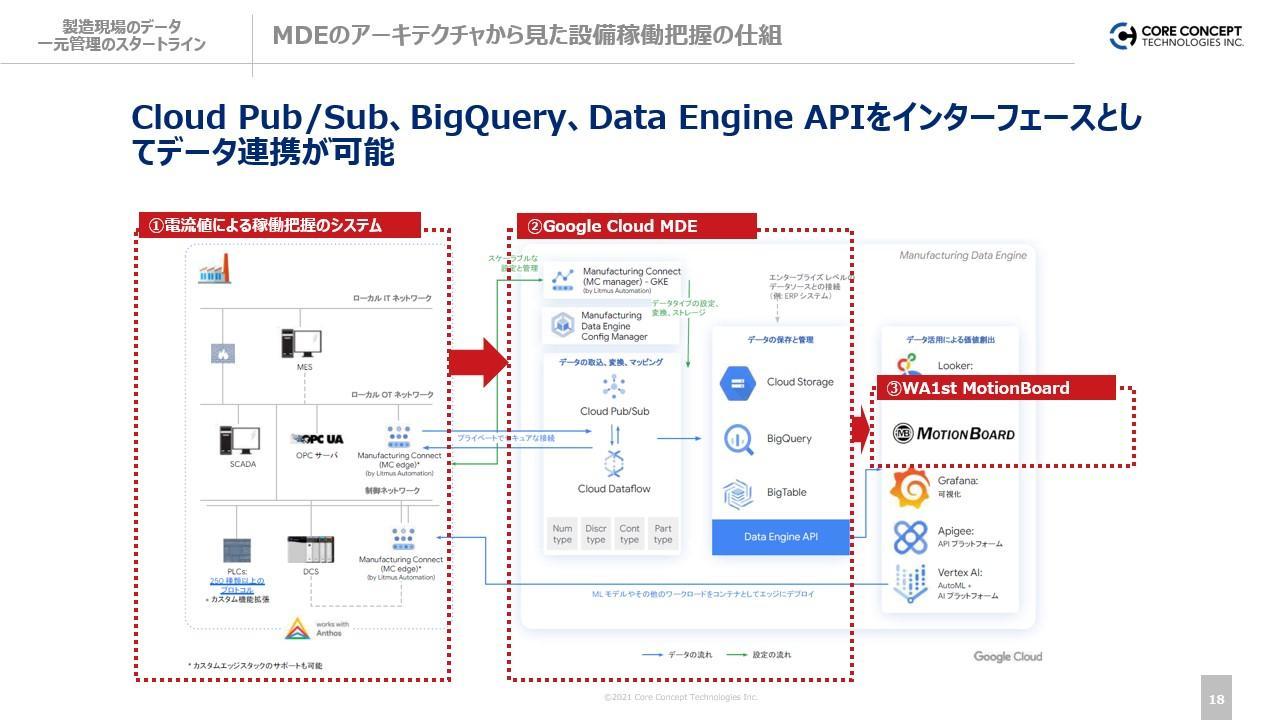
「Manufacturing Data Engine」はCloud Pub/Sub(データを効率的に送受信できるサービス)の真ん中にインターフェイスになる機構があり、ここにデータを上げることで実現できます。実際に「MotionBoard」と「Manufacturing Data Engine」を連携するためには、BigQueryとData Engine API(外部サービスを通じてシステムを拡張する仕組み)を用いて連携する方法があります。そういった形で連携すると、ノーコードでデータを収集する環境を作ることができます。
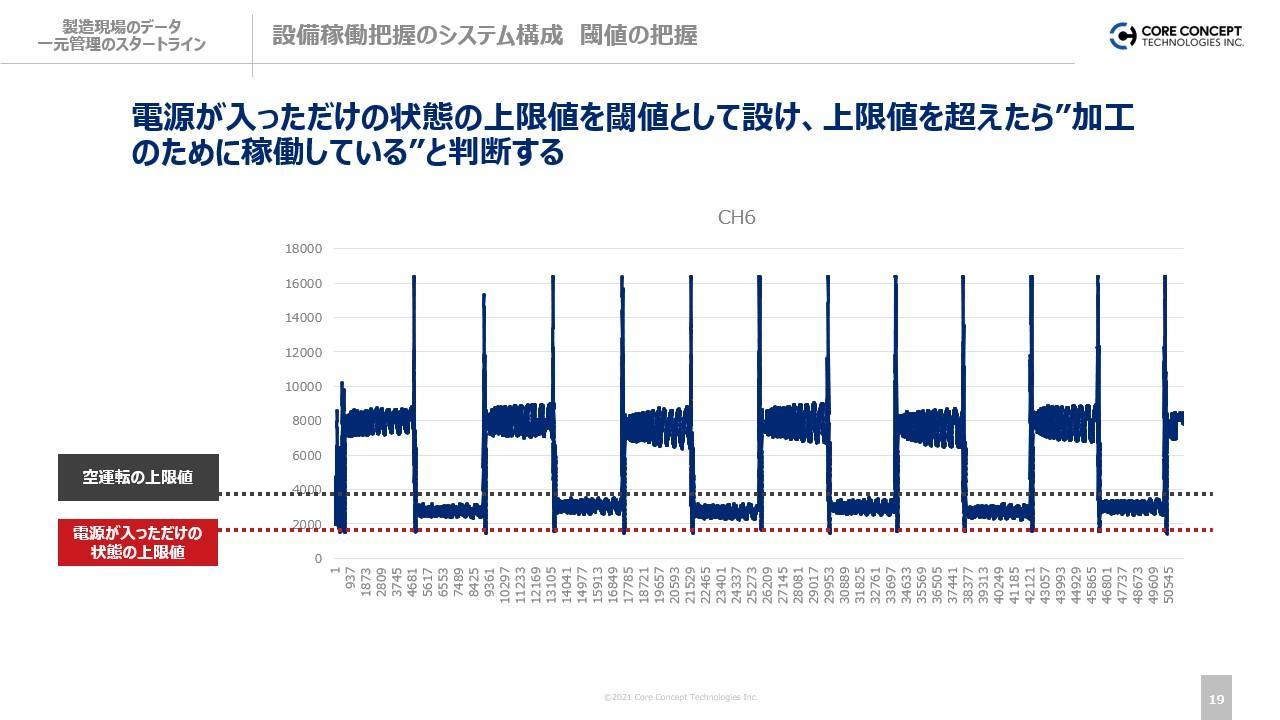
設備の電流値を取るとこのようなデータ(上記画像)になります。実際に設備の稼働状況を確認するときには、閾値(データ判定の境界となる値)を設ける必要があります。設備の電源が入っただけの状態で上限値に閾値を設ける場合は、電流値が少ないところで推移するはずなので、そこが上限値(閾値)となります。一方、設備の空運転を判断する場合は、グラフ(上記画像)でいうとギザギザの部分に閾値を設けるのがポイントです。
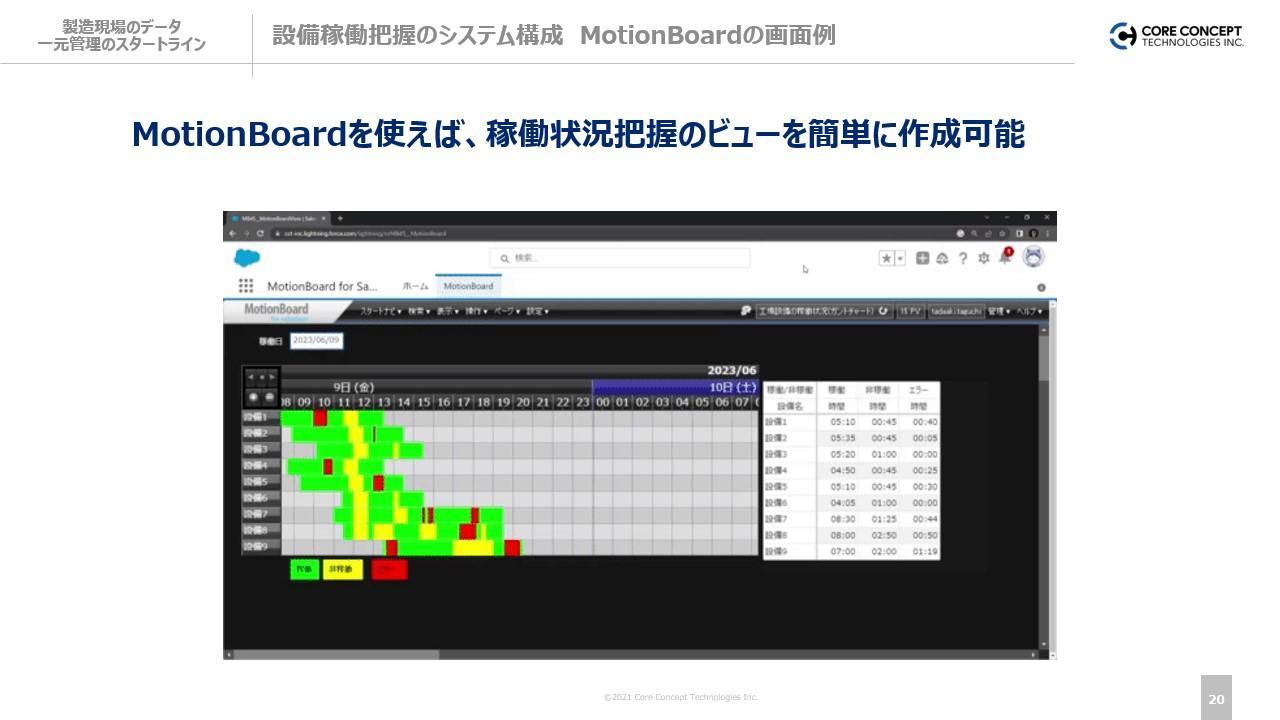
電流値などのデータを用いて、「MotionBoard」でチャートを作ることができます。例えば、上記の画像にある 緑色が正常、黄色が非稼働、赤色が何らかのトラブル状態を示すチャートを構築できます。このようなチャートの他にも稼働状況の把握を3Dで表現することも可能です。
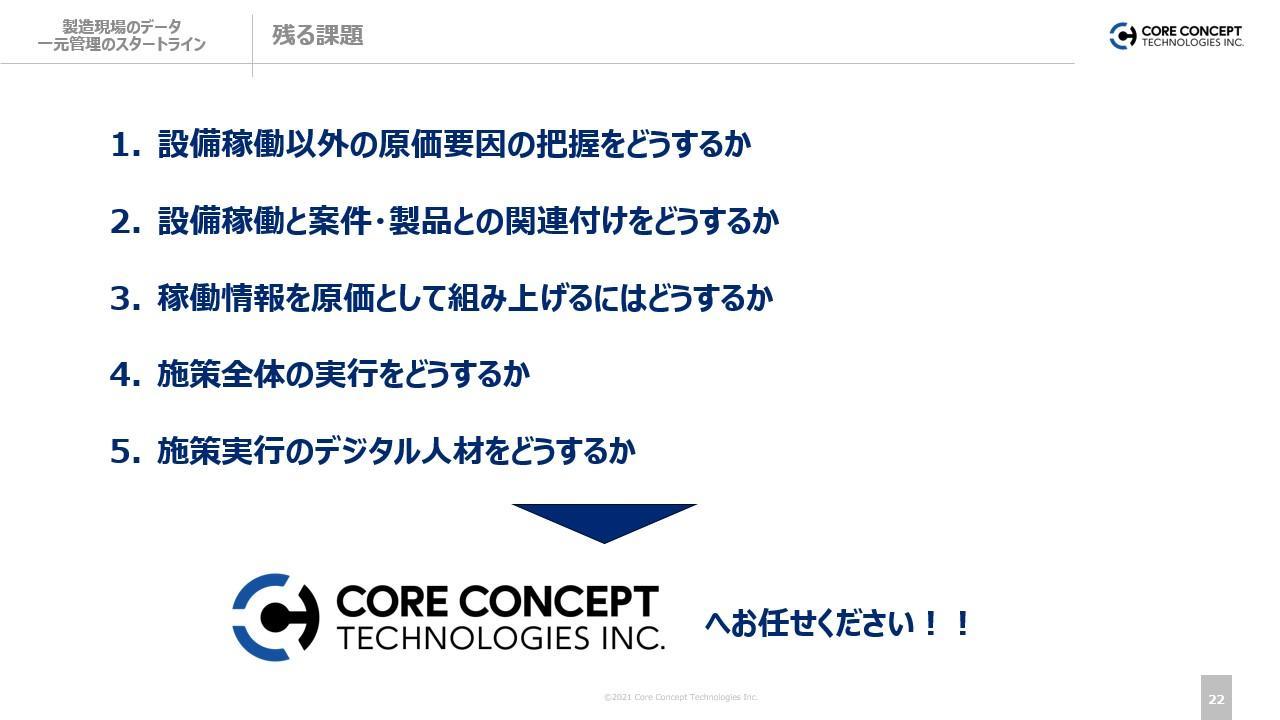
ここまでの話で、データをクラウドに上げて見える化をするまではできることが分かりました。
しかし、「設備稼働以外の原価要因の把握をどうするか」「設備稼働と案件・製品との関連付けをどうするか」「稼働状況を原価としてくみ上げるにはどうするか」「施策全体の実行をどうするか」「施策実行のデジタル人材をどうするか」といった課題は残っています。これらの課題をまとめて解決したいときは、当社にお任せください。
今後のハイパーコンペティション(競争の激化)は予測できないので、ビジネス環境の変化にすぐ対応できる仕組みをつくるために、デジタル化やDXが必要です。本セミナーでは、データの把握から目的設定に至るまでの流れと、各工程のポイントをお話ししました。当社のできることは、先ほど述べた課題として残っている部分、製造現場のDXやシステムインテグレーションですので、任せたいということであれば、ぜひご相談ください。ありがとうございました。
【関連リンク】
ウイングアーク1st株式会社 https://www.wingarc.com/
Google Cloud https://cloud.google.com/
株式会社コアコンセプト・テクノロジー https://www.cct-inc.co.jp/