現代において、品質は企業評価に直結する要素です。アメリカの航空機大手ボーイングは、品質問題などが原因で2022年に50億ドル超の赤字を計上しました。安全性が求められる時代だからこそ、近年ではFMEA(故障モード影響解析)が注目されています。
目次
FMEA(故障モード影響解析)とは?未然にトラブルを防ぐ生産管理手法
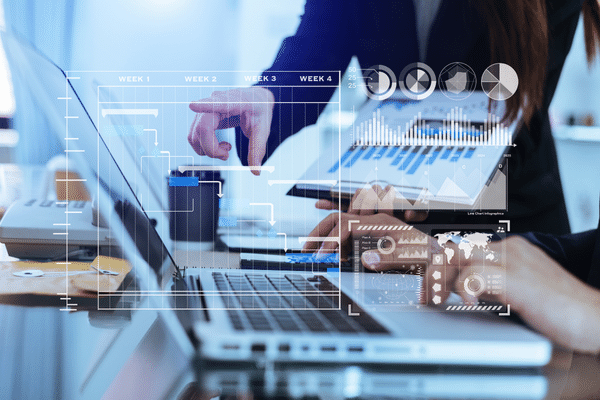
FMEA(Failure Mode and Effects Analysis)とは、 モノづくりの設計段階でリスクを予測し、製造プロセスや製品そのものに潜むリスクを事前に取り除く管理手法です。リスクの解析・評価が故障モードをもとに行われることから、日本語では「故障モード影響解析」と呼ばれています。
起源は諸説ありますが、1950年代にはすでにアメリカの海軍で導入されていました。その後、航空産業や宇宙産業における成果が評価され、現在ではさまざまな業界へと普及が広がっています。
故障モードとは、製品を構成する部品などにおける構造破壊を指します。例えば、システムに不具合が発生した際にはプログラムのバグ、通信の遮断、CPUの高負荷など様々な原因が考えられ、これらが故障モードに該当します。誤解されがちなのですが、故障モードは製品やシステムの故障自体を指すものではないことに注意しましょう。
故障モードとは?FMEAの一般的な流れ
もう少し具体的なイメージをつかむために、FMEAの一般的な流れを見ていきましょう。
1.リスク解析・評価の対象物を決める
2.各部品の故障モードを特定し、その原因を突き止める
3.故障モードが発生したときの損害を評価する
4.各故障モードの確率を予測する
5.評価した損害と発生確率から、総合的な危険優先度を算出する
6.危険優先度をもとに、具体的な改善策や企画を考える
上記の「故障モード」とは、深刻なトラブルを引き起こす原因のことです。以下の例で示すように、故障そのものを指す用語ではないため注意してください。
自動車を例にすると、故障モードに当てはまるもの・当てはまらないものは以下のように分類できます。
【故障モードに当てはまるもの】
タイヤのパンク、エンジンオイルの漏れ、ガソリン不足、ベルト類の劣化
【故障モードに当てはまらないもの】
車が走らない、エンジンがかからない、走行中に異音がする、ノッキングが起こる
仮に「車が走らない」を故障モードにすると、パンクやガソリン不足など多くの原因が考えられるので、損害や発生確率を正しく評価できません。そのため、故障モードは具体的な原因まで落とし込む必要があります。
FMEA(故障モード影響解析)とFTAの違い
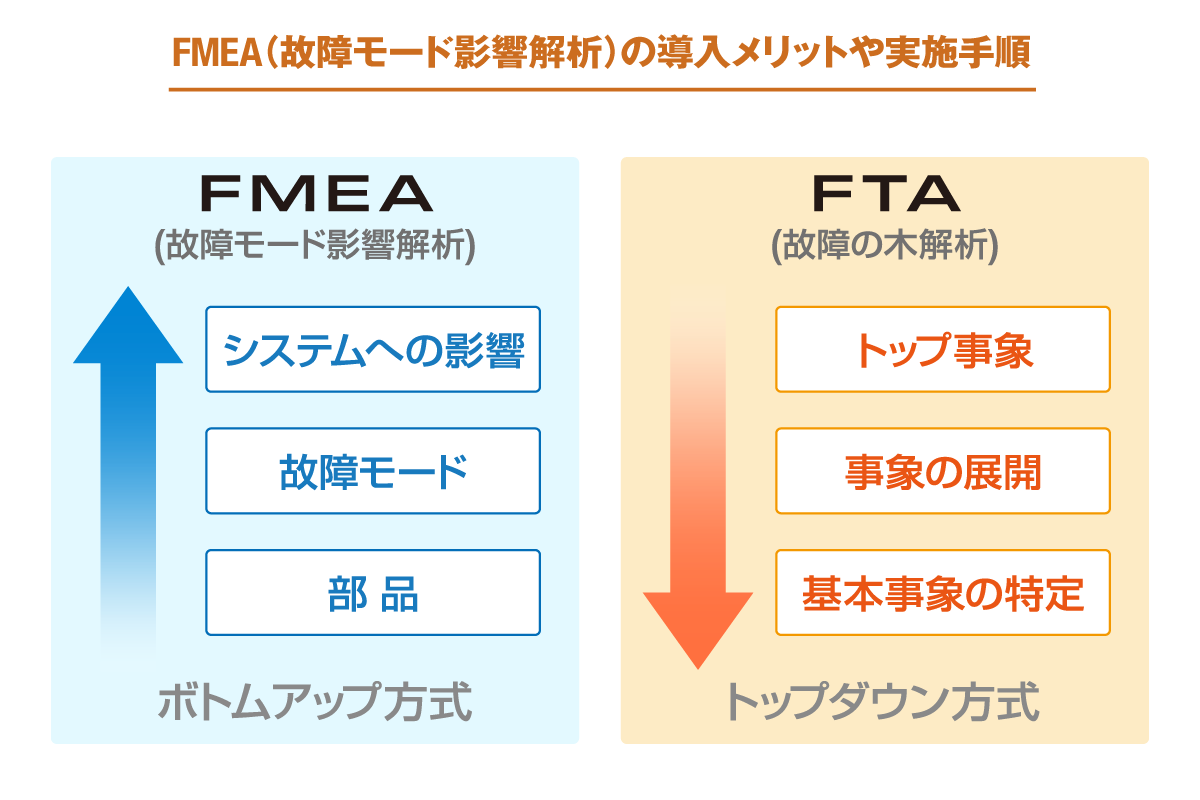
FMEAと混同されやすい用語に、「FTA(Fault Tree Analysis)」と呼ばれるものがあります。これは、 回避すべきトラブルを設定してからリスク要因を挙げていく手法であり、その特性から「故障の木解析」のように訳されます。
主な違い | FMEA | FTA |
日本語訳 | 故障モード影響解析 | 故障の木解析 |
リスクの解析手法 | ボトムアップ型 | トップダウン型 |
リスクの特定基準 | 故障モード | 回避すべきトラブル |
把握できること | ・想定外のトラブル ・優先的に解決すべきトラブル |
・トラブルの発生確率 ・トラブルとリスクの因果関係 ・部品や資材の特性 |
自動車製造での回避すべきトラブルを「タイヤのパンク」として、FTAの簡単な例を見てみましょう。
回避すべきトラブル | トラブルの原因 | リスク要因 |
タイヤのパンク |
タイヤの摩耗 | 空気圧の不足 |
素材(ゴム)の耐久性 | ||
金属部品の劣化 | 酸化によるサビ | |
素材(金属)の耐久性 | ||
異常回転 | 電源やエンジンの故障 | |
制御装置の故障 |
上記のように、FTAではトップダウン型でリスク要因を分析するため、想定外のトラブルは見つけられません。FMEAとFTAの役割は異なるので、製品や現場に合わせて使い分けることが重要です。
工程FMEAとは
FMEAの考え方を工程管理に適用したのが工程FMEAです。主に製造の現場において製造工程で起こりうるトラブルの予防を目的としています。工程FMEAでは、工程を構成する「設備」「作業者」「材料」「方法」「計測」の要素それぞれで故障モードを抽出してトラブルや自己のリスクを評価します。
製造現場では、小さな予兆や欠陥であったとしても見逃しがあると人命に関わる大事故となりかねません。そのため、事故やトラブルが発生する前に予兆を検知し、防止する必要があります。また、工程管理においても正常時だけを基準とせず、トラブル発生時の対応も視野に入れた形で実施することが重要です。工程FMEAを正しく実施すれば、リスクの低減に加えて生産効率の向上や品質向上にもつながるでしょう。
設計FMEAとは
設計FMEAは、FMEAを製品設計に適用したものです。設計FMEAでは、設計段階での潜在的なバグや品質リスクなどを発見し修正につなげることを目的とします。設計FMEAの故障モードは欠陥が顕在化した際に生じる影響、発生確率、欠陥の検出率などから点数がつけられ、対処すべきリスクの評価を行います。従来、故障モードのリスク評価は相対評価で行われていましたが、全ての故障モードの点数付けが必要であることから近年は絶対評価で行われる傾向にあります。
また、設計FMEAは工程FMEAと併せて実施されることがあります。設計は開発工程の一部であることが多く、工程全体の初期で潜在的なリスクを発見するために設計FMEAが活用されているのです。
機能FMEAとは
機能FMEAは、特定の製品やシステムを構成要素となる機能に焦点を当ててリスク評価を行う手法です。製品であれば製品を構成する部品、システムであればシステムを構成する機能やプログラムが機能FMEAの対象となります。機能にはそれぞれが果たすべき役割や正常な動作が機能要件として定義されており、機能FMEAではこの機能要件をもとに故障モードを抽出して潜在的な不具合の把握や評価を行います。
複雑な構造の製品やシステムで工程FMEAや設計FMEAを行う場合、FMEAの対象となる箇所が多すぎるため、より対処箇所を細分化するために機能FMEAが実施されることがあります。機能FMEAは工程FMAEAや設計FMEAの一部といえるでしょう。
DRBFMとは
DRBFMは、日本を代表する自動車メーカーであるトヨタ自動車で生み出された製品開発の工程です。DRBFMは設計FMEAに近い考え方であり、設計工程での故障モードを特定しその対策を練ることを目的としています。
一方、DRBFMでは設計者が工程や設計の変更に焦点を当て、有識者のレビューを受けることが大きな特徴です。DRBFMにはフォーマットが存在し、「変更に関わる心配点」「心配点はどんな場合に生じるか」「お客様への影響」などの記載項目があります。このフォーマットで定義された「心配点」の抽出には各工程や部品の有識者の意見が必要であり、DRBFMの過程では各関係者の活発な議論が行われます。
FMEA(故障モード影響解析)を導入するメリット
FMEAを導入すると、製造プロセスや製品に潜むトラブルを未然に防止できるため、企業にはさまざまなメリットが生じます。ここからは、導入時点で意識したい4つのメリットを解説します。
メリット1.量産体制をつくる前にリスク対策ができる
FMEAでは、優先的に解決すべきトラブルのほか、想定外のトラブルまで特定できます。事前にさまざまなリスク要因を排除できるため、量産体制をつくってから新たな問題が生じることを防げます。
ロスのない製造プロセスを構築することで、 生産ラインの修正リスクを抑えるだけではなく、生産性アップの効果も期待できるでしょう。
メリット2.顧客満足度や企業評価がアップする
製品に潜むトラブルを未然に防ぐと、商品・サービスの質や安全性が向上するため、FMEAには顧客満足度を引き上げる効果もあります。それをきっかけに良い評判が広まれば、 ステークホルダー全体からの企業評価も高まるでしょう。
一方で、欠陥品が市場流出することによるダメージは少なくありません。その製品の売上が下がるだけではなく、企業イメージやブランドの喪失にもつながってしまいます。
メリット3.従業員満足度やモチベーションがアップする
FMEAの導入は、社内にも良い影響をもたらします。高品質な製品がつくれるようになると、良いモノづくりへの意識が社内に広がるため、従業員満足度やモチベーションもアップすることが考えられます。
また、 設計段階から想定外のトラブルを解析させることで、従業員の思考力や想像力、技術力を鍛える効果も期待できます。
メリット4.人的リソースやコストを最適化できる
FMEAの導入には、人的リソースやコストを最適化する効果もあります。
仮に想定外のトラブルが発生すると、その対応に多くの人的リソースやコストが費やされます。最優先で対処すべき課題となってしまうため、通常の製造プロセスにも悪影響が生じるでしょう。
FMEAはこのような事態を防いでくれるので、 導入すると経営資源を適材適所に振り分けられるようになります。
FMEA(故障モード影響解析)を実施する手順
FMEAの効果を最大化するには、正しい手順で各プロセスを進める必要があります。順序が前後するとリスク解析の結果が変わるため、有効な改善策を講じられません。
全体のプロセスは前述でも触れましたが、以下ではさらに細かいプロセスや流れを解説します。
手順1. FMEAフォーマットを作成する
まずは対象物を決めるために、検査項目をまとめた「FMEAフォーマット」を作成します。一般的には表計算ソフトを用いますが、特に決められた形式はありません。
以下の例を参考にしながら、チェックしやすい表を作成してみてください。
・作業名目
・具体的作業
・故障の検出手段
・検出度
・RPN(危険優先度)
全体の製造プロセスを踏まえて、もし作業名目や具体的作業に分ける必要がないと判断した場合は、FMEAフォーマットから除外しても構いません。
手順2.想定できるミスから故障モードを決める
FMEAフォーマットを作成したら、「想定できるミス」と「故障モード」の欄を埋めます。ミスと故障モードは混同しやすい部分なので、分かりやすい例を紹介しましょう。
想定できるミス | 故障モード |
配線に足を引っ掛ける | 断線 |
ネジの回し方が不十分 | 対象部分の強度不足 |
保管方法の間違い | 金属部の酸化 |
上記のように、トラブルの原因となる現象が「想定できるミス」、その結果として生じたトラブルが「故障モード」になります。なお、 故障モードの対象はあくまで製造プロセスのみであり、部品の形状が合わないなどの設計ミスはFMEAフォーマットに入力しません。
手順3.故障の影響・原因まで落とし込む
次は、故障モードを分析・評価する前準備として、「故障の影響」と「故障の原因」の欄を埋めます。 故障の影響は、後述する影響度の分析で必要になるため、具体的な弊害まで落とし込みましょう。
故障の原因についても、発生度や検出度を評価する際に用います。具体的なシーンをイメージしながら、それぞれの欄を埋めてください。
手順4.故障の影響度を分析する
故障の影響度は、「故障の影響」をもとに10段階で評価します。製造プロセスによって基準は変わりますが、以下では一般的な目安をまとめました。
影響度 | 影響の度合い(例) |
10 | 命に関わる、全く機能しない |
9 | 特定条件下で全く機能しない |
8 | 機能しないリスクがある |
7 | 特定条件下で機能が低下する |
6 | 機能低下のリスクがある |
5 | 機能はするものの要改善 |
4 | 軽微な影響、機能はするものの改善が望ましい |
3 | 影響がほぼ無いと判断できる |
2 | 影響を無視できる |
1 | 影響なし |
目に見えるトラブルが見つかった場合は、影響度は少なくとも4以上になります。また、影響度6以上では深刻なリスクを抱えている恐れがあるので、ほかの数値が高くなくても製造プロセスや製品を見直しましょう。
手順5.故障モードの発生度を分析する
故障の発生度は、「故障の原因」から発生頻度を判断します。以下は目安となりますが、評価する対象(製造プロセスや製品)によって発生頻度によるリスクは変わるため、独自の判断で基準を設定しましょう。
発生度 | 故障の頻度(例) |
10 | 1週間に1回以上 |
9 | 数週間に1回以上 |
8 | 1ヵ月に1回以上 |
7 | 数ヵ月に1回以上 |
6 | 1年に1回以上 |
5 | 数年に1回以上 |
4 | 5年に1回以上 |
3 | 数年に1回以下 |
2 | 5年に1回以下 |
1 | 発生しない |
故障が発生しやすい製品などは、「1日に1回以上」を発生度10にすることもあります。
手順6.故障モードの検出度を分析する
検出度は、目視や管理システムなどで故障を発見できる確率を表したものです。発見できる確率が低いものほどハイリスクになるため、検出度も高くなる特徴があります。
あくまで目安ですが、検出度についても例を見ていきましょう。
検出度 | 故障の発見確率(例) |
10 | 発見できない |
9 | 製造段階で10% |
8 | 製造段階で20% |
7 | 製造段階で30% |
6 | 製造段階で50% |
5 | 製造段階で70% |
4 | 製造段階の前で100% |
3 | 作業の次の工程で100% |
2 | 作業途中で1~99% |
1 | 作業途中で100% |
検出度1や検出度3~4は「100%」となっていますが、これらに該当するのは機械での検出のみです。 目視での確認は、ヒューマンエラーによる見落としがあるため、発見確率は100%にならないものとして判断します。
手順7.RPN(危険優先度)を計算する
RPN(危険優先度)とは、製造プロセスや製品に潜むリスクのうち、優先的に対処すべき故障モードを数値化したものです。専門用語の一つですが、計算自体はそれほど難しくありません。
RPN(危険優先度)=影響度×発生度×検出度
仮にある工程の影響度を5、発生度を3、検出度を2とすると、RPNは30(5×3×2)になります。すべてのRPNを計算したら、手順1で作成したFMEAフォーマットに数値を書き込みましょう。
手順8.改善計画を立てて実施する
ここまで進んだら、RPNが高いものから改善計画を立てます。
改善計画の方向性としては、RPNを下げることを目標にすれば問題ありません。例としては、 加工設備を導入して発生度を下げたり、AIによる自動検出システムによって検出度を抑えたりする方法があります。
故障モードの影響度は、製造プロセスや製品自体を変えない限り、企業努力で下げることはできません。仮に製造プロセスそのものを変更するとなると、「FMEAでリスクを防ぐ」という目的から逸(そ)れるため、ここまでの工程が意味をもたなくなってしまいます。
そのため、ここでは発生度・検出度を下げる計画を立てて、一つずつ実施していきましょう。
FMEA(故障モード影響解析)を実施するときの注意点
FMEAの有用性は多方面で認められていますが、期待した効果を得られない場合もあります。特に故障モードの抽出や、影響度・発生度・検出度の設定は、多くの人がつまずくポイントでしょう。
FMEAで最適な改善計画を打ち出すには、以下の点に注意することが必要です。
一人で判断すると主観的な評価になりやすい
FMEAの実施にあたって、一人体制は望ましくありません。いくら現場に詳しい担当者でも、一人では思いつく故障モードに限界があり、さらに影響度・発生度・検出度の分析も偏るためです。
主観的になりやすい管理手法だからこそ、基本的には複数人でチームを組みましょう。特に異なる作業の担当者でチームを組むと、 さまざまな角度からアイディアが飛び交うため、客観性の高いデータを得やすくなります。
「故障・不良・故障モード」を混同しない
FMEAにおいて、「故障・不良・故障モード」はいずれも異なる意味をもつ言葉です。これらを混同すると、本来は故障モードとして扱うものが別項目に含まれてしまうため、正しい分析結果を得られません。
故障モード:深刻なトラブルを引き起こす原因となるもの。
故障 :故障モードが原因で発生する、製造プロセスや製品の不具合。
不良 :設計プロセスや指示内容の不備による機能不全。
例えば、部品の欠け(故障モード)による動作不具合は故障、部品のサイズ違いによる組み立てミスは不良にあたります。 特に故障モードと故障は混同しやすいので、注意しながら抽出作業を進めてください。
10段階の検出度が望ましくないプロセス・製品もある
前述では検出度を10段階で紹介しましたが、実は3段階や5段階で評価するケースもあります。なぜこのような違いがあるのか、分かりやすい例を紹介します。
影響度 | 発生度 | 検出度 | RPN | |
製品A | 2 | 5 | 5 | 50 |
製品B | 10 | 5 | 1 | 50 |
上記の製品Aと製品Bは、いずれもRPNが同じ値です。つまり、同等の危険優先度であることを意味しますが、製品としてはそれぞれ以下の特徴をもっています。
製品A:故障リスクはほぼ無視できるが、製造段階で30%はリスクを見落とす。
製品B:命に関わる故障リスクがあるものの、そのリスクを100%発見できる。
このように比べると、各製品の危険優先度に差があると感じる方もいるはずです。その要因は10段階で評価している検出度にあり、実際に「検出度を強調しすぎている」と指摘する声もあります。
つまり、 対象のプロセス・製品によっては、3段階や5段階での評価が望ましいこともあるので、RPNを計算して違和感をもったら検出度を調整してみましょう。
FMEA(故障モード影響解析)を導入して経営を安定させよう
FMEAは想定外のトラブルを洗い出し、優先的に対処すべき故障モードを把握できる管理手法です。適切な改善計画を実施すると、これまで見落としていたリスクを排除できる上に、従業員を含めたステークホルダーからの評価も高まります。
ただし、主観的な判断が含まれやすい手法なので、導入時には異なる部門でチームを組むといった工夫を考えましょう。
(提供:Koto Online)