生産制御管理システムとしてDCS((Distributed Control System=分散制御システム)を、現在まで継続して長期間使用している企業やプラントも多いのではないでしょうか。この20年間でDCSは、汎用の計装PLCなどを用いた新しいDCSへの置き換えが進んでいます。DCS自体が従来のような中央集中型で多様な機能をもつものから、他の計装機器と組み合わせる分散型へと変化しており、事例も増加しています。この記事では旧来のDCSと現在主流となりつつあるDSCとPLC、その他SCADAについて比較しながら、それぞれの違いや性能について解説します。
目次
DCSとは

初めに、DCSについて概要を解説します。
DCS(Distributed Control System)とは
DCSとは“Distributed Control System”の略称で、日本語では「分散制御システム」と訳され、工場を監視して制御するシステムを意味します。用途としては主に大規模工場や精製プラントにおいて、危険性の高い流体を扱うプロセス・オートメーション(PA)です。石油化学や発電から、製紙、食品までさまざまな業界で使用されています。
「分散」という名前の由来は、その構造にあります。一つのシステムの中に複数の機能があるのではなく、複数の製品や設備を連携するためそれぞれの区分(ユニット)ごとに制御機器が設置されています。このように制御ユニットを分けることで、万が一どこかのユニットに不具合が発生してもシステム全体が止まらない・トラブルが波及しないことから、長期継続運転が可能な仕様になります。リスクの分散だけでなく、設置場所や機能そのものの分散も含まれます。
特に従来型のDCS(後述)は、半導体やCPUの性能が今ほど高くなかったことから、全体の制御を調整するためにDLCメーカーが設置や設定まで行っています。現在では制御のラダープログラム(機械の動作を記述するプログラム)はPLCでは工場側でも書くことができますが、従来型ではメーカーで実施したものもありました。
DCSの定義の変遷
前述した名称の由来である「分散」は、近年のDCSではなく従来型のDCSがその意味をより具現化しています。これは時代によって、製品としての「DCS」が指している概念が変化しているからと考えられます。
DSCという言葉やシステムは、以前から使われてきたものです。伝統的な(従来型の)DCSは、プロセス・オートメーションを対象とするのは現在と同じであるものの、製造プラントの運用を支援する「統合的な」制御システムを指していました。複数の制御ユニットや表示装置、センサーなど、各種の「製品」を組み合わせて連携させ、一元的に管理するものです。各ユニットを繋ぐために、メーカー各社はそれぞれ独自の通信規格による産業用 Ethernet(RTE)を用いて通信し、安定的な可動性を確立しています。
一方、DCSがこのような統合的な役割をもっていた数十年前と比較して、現在はCPUの処理能力が大きく向上しています。そのためプラントにおける大量のループ制御を、従来型の統合的なDCSではなく、代替する製品やシステムで担うことが可能になっています。
そのため、近年のDCSは従来型の「別々の機器やシステムをつなぎ、全体を統合的に監視制御する」タイプのDCSと比較して、意味が狭くなっており、「"監視用の表示ソフトウェア"と"制御装置"」を表すことが増えています、以下で従来型と近年のDCSの違いを解説します。
従来型のDCSと近年のDCSの具体的な違い
従来型のDCSと近年DCSとされる機器が含む具体的な機能の違いはおおむね以下のとおりです。従来型のDCSの機能を別の装置やソフトウェアで代替していることをわかりやすくするため、PLC、SCADA、表装置についても記載しています。
ただし、メーカーによってDCSは従来同様に統合制御装置として設置しているところもあるため、一例としてご覧ください。
表示面 | 制御面 | ||||
装置 | ソフトウェア | 装置 | ソフトウェア | ||
従来型のDCS | ○ | ○ | ○ | ○ | |
現在のDCS | ー | ○ | ○ | ○ | |
従来型DCSを代替する機器・装置 | PLC(制御装置) | ー | ー | ○ | ○ |
SCADA(監視用ソフトウェア) | ー | ○ | ー | ー | |
産業用PC | ○ | ー | ー | ー |
制御装置や表示装置の性能・設置設定は半導体によって決まるとされます。従来は半導体の性能が今よりも低かったため、装置の設置と制御は切り離せず、一体となったものを開発せざるを得なかったようです(従来型DCS)。しかしここ数年、半導体の進歩により「装置開発(による性能向上)」と「装置の設置設定(エンジニアリング)」は切り離せるようになり、汎用性の高い別の装置で代替できるようになりました。
そのためDCSを示す概念自体が縮小され、現在は制御装置と表示ソフトウェアの機能になっています。表のように、PLC・SCADA・産業用PCを組み合わせることで、従来型のDCSの機能をカバーできていることがわかります。
PLC(PLC計装)とは
現在のDCSの担う範囲が限定的になっている代わりに、従来のDCSが行っていた統合的な制御を行う機能が必要になります。これがPLC(PLC計装)です。ここではPLCとPLC計装について解説します。
PLCとは
まずPLC(Programmable Logic Controller/プログラマブルロジックコントローラ/プログラム可能な論理制御装置)とは、工場の生産現場に導入されている産業用制御システムで、様々な機械や装置、プロセスの制御に広く利用されます。工場を管理するコンピューターと、各装置の間に位置します。主に自動車など、組み立て系の自動化(ファクトリー・オートメーション:FA)の分野で使われています。
PLCはセンサーや計器からのデータを読み取り、構築されたプログラムに基づいて、各機器やプロセスを制御します。また、制御内容をプログラムで書き換えられる柔軟性・拡張性の高さももっています。例えば同じ製品であっても、制御内容の変更があった場合はプログラムを変更することができます。このため、必要に応じた多様な制御を実現でき、新しい条件に合わせて最適化できる特徴があります。異なるプロセスや機器にも簡単に適応できます。
また処理に対して高速性と正確性をもち、しかも比較的安価という点がメリットといえます。そのためFA(ファクトリー・オートメーション)分野での採用が近年は増えています。
PLCをつくるメーカーはFAメーカーだけでなくPLCを専業としていない大手企業も多く、各社のPLCには通称があったり、呼び名が異なったりします。例えば三菱電機はPLCを「シーケンサ」としており、名称は異なりますが機能はPLCにあたります。
PLC計装とは
「計装」とは、「計測器を装備する」を語源としています。「プラントなどの各工程で必要な様々な機械の状態を計測し、プロセスを監視して統合機器(コンピューター、DCSなど)を使って自動で制御(管理)できる状態で装備すること」を指します。
PLC計装とは「PLCを用いて多くの計測機器を管理すること」という意味になります。つまり、従来型のDCSが制御システムとして担っていた機能をPLC計装で再現できることになります。近年ではDCSより安価であること、拡張性が高いことから、特に中規模プラントで移行が進んでいます。またPLCは高い応答性を持ち、リアルタイムで様々なデバイスやセンサーからの情報を処理できます。
DCSの代替にするPLC設備の構成
PLCの多くは、制御ユニットとして二重化対応(特定の部分を二系統準備すること。障害が発生した際や機器が故障した場合にもシステムを停止させることなく、制御を続けるためのリスクヘッジ)して、DCSの「止まらない」性能、メリットを再現しています。
また指示や監視はSCADAと産業用コンピューターを組み合わせます。通信は精度の高い産業用Ethernetで接続され、制御はリアルタイムで行われます。
DCSとPLCの違い
上の表にもあるように、DCSもPLCも産業用の制御システムであり、機器や装置を制御する役割があることは共通です。一方、従来型・現在どちらのDCSともPLCが異なっている点は、以下のようになります。
表示機能・装置
PLCには表示装置が含まれません。よって、PLCだけでは人間が工場内の状況を確認できません。そのため監視用ソフトウェアであるSCADAとの組み合わせが必須となります。
設置される工場の規模・適用範囲
特に従来型のDCSは、広範囲で複雑なプロセスの制御に適しています。例えば、大規模な工場全体やプラントの生産プロセス全体を統合的に管理することができます。一台のコンピューターが集中的に制御するのではなく複数の機器それぞれに制御装置があり、各ユニットがネットワーク上で連携して一元的に管理されます。
そのため全体を止めることなく動かし続けられるメリットがあり、大規模な工場などに多く使われます。プロセス制御および製造プラント全体の管理が必要な、例えば、化学プラント、発電所、製油所などで使用されます。
PLCは、制御装置の機能はDLSと同様ですが、主に小規模・中規模の工場などで使われることが多く、FA分野である製造ライン、自動車産業などで使われます。
その拡張性や汎用性からDCSからの置き換えも進んでいます。今後の半導体やCPU、PLC自体の機能の進化によってはさらに大規模な工場で使われることが増えるかもしれません。
柔軟性と拡張性
従来型DCSの拡張性は低く、機能追加などに対しては多大なコストがかかります。PLCは比較的コストを抑えられます(メーカーによる)。
設置にかかるコスト
DCSと比較すると、PLC+監視装置SCADA+PCで代替した場合の方がコストを低く抑えられるようです(メーカー、プログラム内容などにより異なる)。
これらの違いに基づいて、企業はプロセスの性質や規模に応じてDCSまたはPLCを選択しているようです。最近のDCSとPLCを組み合わせて使用することもあります。
DCSとSCADAの違い
SCADA(Supervisory Control and Data Acquisition)とは、PCで工場内の監視制御とデータ収集を行うためのシステムです。施設を監視・制御し、操作者にリアルタイムな情報を提供します。
SCADAはPLCと同様、拡張性が高いことが特徴です。同じ製品であっても、条件に合わせてプログラムを変更することができます。
すでに紹介したように、DCSは監視装置も付随している制御装置です。SCADAは主にデータ監視や可視化に焦点を当て、大規模で分散したシステムを管理します。主に遠隔地からの監視や報告が求められる場面で利用されます。
DCSとPLCの使い分け
従来型のDCSは特に、設置から設定までメーカーへの依存度が高く、また初期費用や維持費用(保守点検)、リプレイスに高いコストがかかります。また特に長く使われているDCSは近年のシステムとの互換性が低いものもあり、レガシーシステムとしての置き換え問題があります。そのため、近年は従来型のDCSがもっていた機能をPLC・SCADA・コンピューターで代替するところも増えています。
メーカーの方でもDCS、PLCともに製造現場の自動化・省力化に対応できるよう、省エネ化・コスト削減・効率向上が叶う製品を開発しています。またスマートフォン・タブレットなどの汎用性の高いデバイスによる遠隔監視が可能なものも出ています。
このように見ていくと、PLCとSCADAなどの組み合わせで十分ではないかという見方もできます。しかし一方、大規模な石油化学工場や発電所などでは24時間・365日の連続使用が求められます。万が一にも止まることが社会の重要インフラとして許されない現場、止まることで社会的・経済的影響が多大な現場、危険が多くても安全性を担保すべき現場には、連続稼働に信頼性の高い制御システムとメーカー独自の災害等リスクに対する技術、そしてメーカーと製品に対する高い信頼が必要となってきます。そのような現場にはDCSの導入が不可欠といえるかもしれません。
(参考)横河電機「Yokogawa DCS 製品のハードウェアにおけるSDGs 達成に向けた取り組み」,大脇,横河技報 Vol.63 No.2 (2020)
DCS・PLC・SCADA比較まとめ
isa-95の階層図とSCADA、DCS、PLCの階層をまとめました。
※図1 DCS・PLC・SACDAの改装図
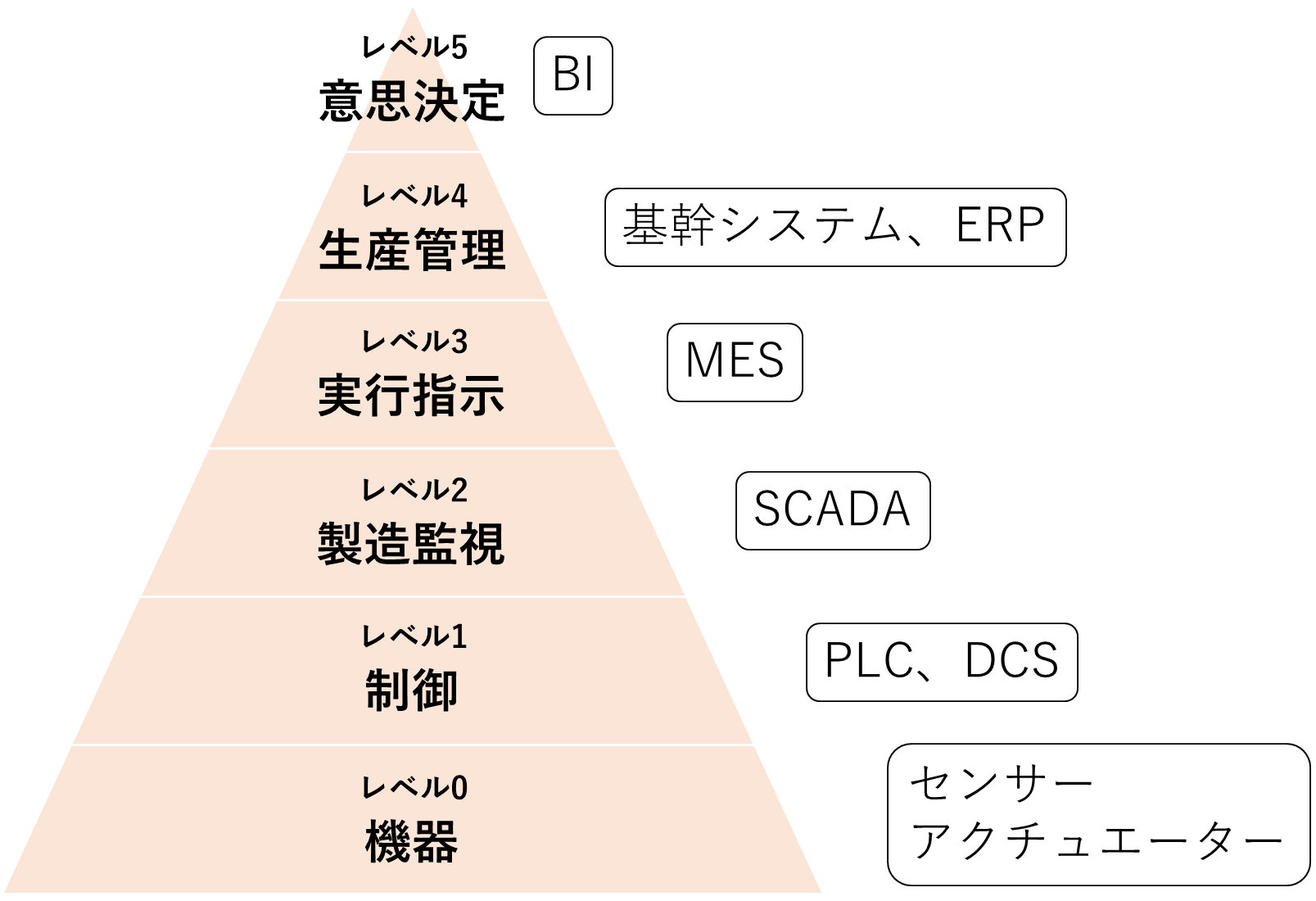
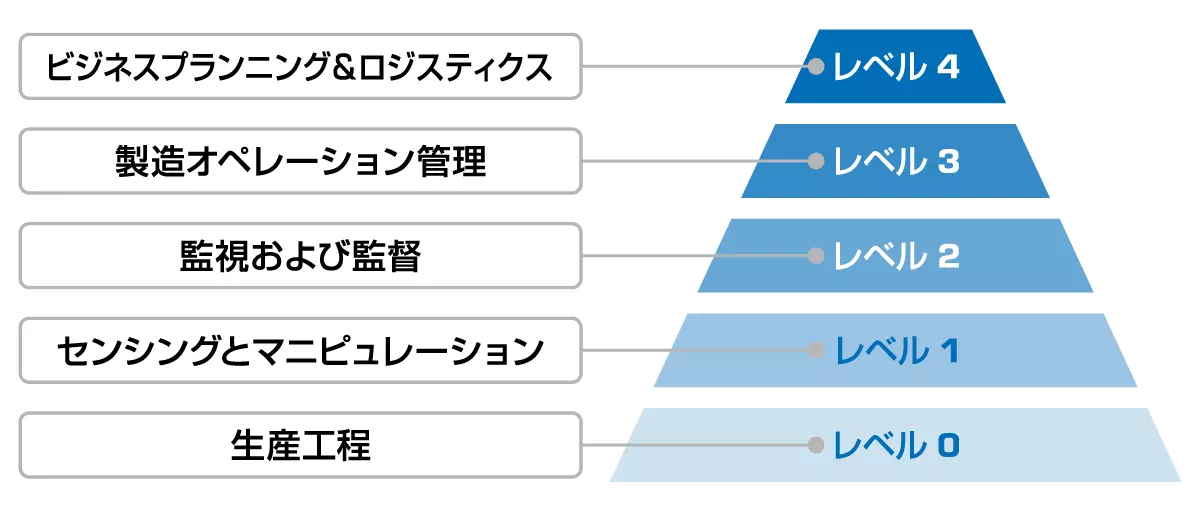
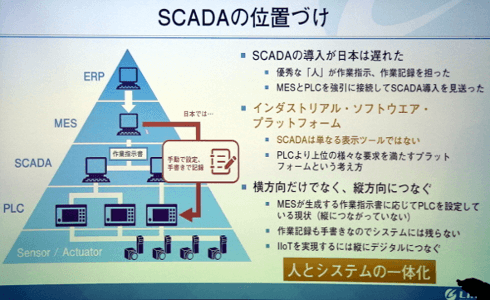
代表的なメーカー
DCS、SCADA、PLCなどの代表的なメーカーと製品を紹介します。(詳細は各メーカーへお問合せください)
製品種類 | 代表的なメーカー/サプライヤーなど | メーカー等の製品名 |
DCS | 横河電機、アズビル(旧・山武)、三菱電機、東芝、日本電機研究所 ほか | CENTUM/YEWMAC/ASTMAC/STARDOM(横河電機) |
PLC | 三菱電機、キーエンス、オムロン、富士電機、パナソニック、日本電機研究所 ほか | MELSEC Series(三菱電機) KV-8000シリーズなど(キーエンス) CP2Eシリーズなど(オムロン) |
SCADA | キヤノン、東京ガス、三菱電機、日本電機研究所 ほか | AVEVA InTouch HMI(キヤノン) JoyWatcherSuite(東京ガス) SCADA GENESIS64(三菱電機) |
まとめ
この記事では、DCSとPLCについて、その成り立ちや違いなどを解説しました。
DCSは工場などの統合監視制御システムです。PLCは制御のみを担うシステムです。近年の半導体やCPUの進歩により、数十年前から使われてきたDCSの概念や仕組みは変化しており、近年ではその言葉が表す概念は狭くなっています。また、コストと維持費がかかり汎用性の低い従来から使われてきたDCSは、新しいDCSや、PLC・SCADA・産業用コンピューターの組み合わせに置き換えられることが増えています。現在のDCSはPLCに表示装置がついたものになってきています。
今後は汎用性が高くコストが抑えられるPLCに置き換わっていく可能性が続くかもしれません。しかし大規模工場など安全性や信頼性、社会的な役割の大きい、万が一にも止まることが許されない現場においては、より信頼性の高い監視制御システムは必要です。コストと汎用性の高さはもちろん、さまざまな要因を加味したうえで自社の向上に最適な製品を選ぶ必要があります。
(提供:Koto Online)