現代の製造業において注目を集めているのが、「FMS(Flexible Manufacturing System)」です。現代の市場ニーズに合わせた改善手法には違いないのですが、それ以外にも効果があります。FMSとはいったいどのようなものなのでしょうか。
この記事では、FMSの特徴、背景、仕組み、導入事例、およびメリット・デメリットについて解説します。
フレキシブル生産システム(FMS)とは
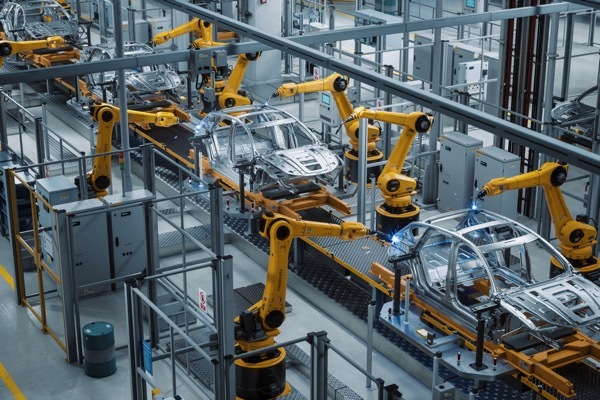
FMS(Flexible Manufacturing System)は、一つの生産ラインで異なる製品や種類を柔軟に製造できるシステムを指します。
これまでの生産ラインは、一つの製品に特化したラインを構築する手法が主流でした。しかし、FMSでは、産業用ロボットなどを活用してすべての工程を自動化することで、機械同士がデータを相互に利用できるようになります。これにより、生産プロセス全体が統一的に管理され、製造業者は市場の変化や需要の変動に対応できるという利点があります。
FMSの特徴
FMSの特徴は、産業用ロボットなどを活用した自動化にあります。加工、組立、検査、搬送といった生産工程をすべて自動化することで、製品や装置の状態をデータ化し、そのデータが工程間でやり取りされることが挙げられます。これにより、製品が変わっても迅速に対応できる環境が構築されます。
全工程が自動化されることで、人の習熟度や機械の変更、方法や材料の変更などに左右されることなく、フレキシブルに対応可能な生産環境が確立されます。
さらに、すべての機械が自動化されることで、リアルタイムでデータを収集し、工場内の状況を一元的に把握できます。これにより、生産プロセスが「見える化」され、効率的な管理が可能となります。
FMSが求められる背景
FMSが求められるようになった背景には、市場の多様化があります。生活様式の多様化、情報化社会の進展、グローバル化、ライフスタイルの変化などにより大量に生産される画一的なものには価値が見いだされなくなってきました。
現代はすでに大量生産による経済発展で成功をおさめ、次の「多品種少量生産」の時代に入っています。現代の消費者ニーズの多様化とプロダクトライフサイクルの短期化から「変種変量生産」が求められ、これまでの大量生産体制では対応できなくなったのです。
製造業には、「大量生産並みのコストで、オーダーメード製品を作る」というマスカスタマイゼーションの考え方がありますが、FMSはまさにこれに対応したものだともいえます。
FMSの仕組み
FMSは、加工、組立、検査、搬送という各生産工程をすべて自動化することで可能になります。それぞれの工程にはNCマシンやマシニングセンタなどの加工機械、無人搬送車、産業用ロボットが設置されています。各自動化機械はデータの相互通信ができるように設計されており、製品の情報が共有されています。これにより部品の組付け、加工から次の工程への搬送に至るまで一元管理を可能にします。
製造しようとする製品がA、B、Cの3種類あって、それぞれの製造用データを製造ラインにセットしたとします。製造ラインに製品Aを流し、次に製品Bを流しても、各工程では自動で判断をして製品に必要な部材や工具を切り替え、動きを変えて作業をします。
加工だけではなく、組立と検査、搬送も一元管理のもと、行えるようになります。相互のロボットはデータのやり取りを行っており、滞りなくラインが流れるように制御されます。すべてデータで制御されるので、工程全体は見える化され管理できる仕組みになっています。
現代では、電化製品や衣服など多種変量生産が要求される分野が数多くありますが、FMSはこの仕組みによって市場の要請に応えられるようになっています。
図1.FMSの仕組み
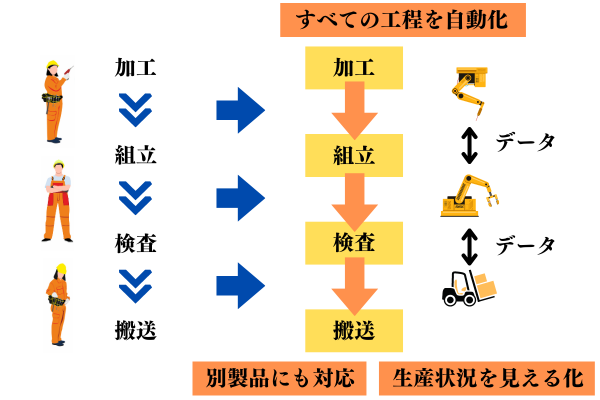
FMSの事例
実際のFMSはどのような要請に基づいて始まり、どのように構築されていったのでしょうか。ここでは自動車メーカーマツダの事例をご紹介します。
マツダ
自動車メーカーのマツダでは、「近年自動車業界を取り巻く環境は100年に1度の劇的な変化を迎えている」としています。
同社はこれまでも「ニーズの多様化や市場環境の急激な変化に柔軟に対応するため」、多種変量生産ラインを開発、展開してきました。しかし、カーボンニュートラルなど新しい社会的要請が出現し、自動車そのものの概念が大きく変容してきた現代で、生き残りをかけた変化への対応が求められていました。
そこで、フレキシブルな生産への取り組みを進めるために、まず製造に対する考え方を次の3つの軸に定めました。
一括企画
コモンアーキテクチャー(CA)構想
フレキシブルライン構想
「一括企画」とは、5年から10年先の全商品を同時に企画するもので、商品の多様化へ対応するとともに生産効率を高めようというものです。マツダはこれまで車種ごとにバラバラに工程や設備を用意しており効率的とは言えませんでした。これに対する反省と対策ともいえるものです。
先に未来の全商品の企画を作っておけば、各車種間で開発と生産のコンセプトを共通化できます。これが「コモンアーキテクチャー(CA)構想」です。これは車格や排気量が違っても、各ユニットのコンセプトを共通化するため、製造設備も共通化できる点が多くなるところに利点があります。
「フレキシブルライン構想」は、汎用設備のみで生産ラインを構成することに取り組み、治具を極小化して、製品が進化したとしてもフレキシブルに対応できるようにしました。
マツダではこのように、単にロボットなどの設備の更新をするだけではなく、製造に対する考え方や取り組み方そのものを変革させた上でFMSを実現させています。
FMS導入のメリット
FMSを導入した時のメリットについて以下にまとめてみました。時代の要請に応えるためにできたFMSですが、企業にとっても多くのメリットがあり、経営の改善にもつながる効果が期待されます。
省人化
まず挙げられるのは、省人化です。FMSは単なる合理化、機械化ではなく考え方そのものの改革を含みます。従来型の生産体制を一度リセットすれば、ある工程で必要だと思われてきた人員も必要なくなるかもしれません。
それは、自社の生産性を向上させるということであり、誰もが避けたいと思うであろう、きつくて危険な仕事、夜勤などを不要なものとすることにもつながります。これからの人手不足時代、必ず対策をとらなければならなくなることから、省人化は必須といえるでしょう。
また、製品の製造原価で目標より人件費のウェイトが大きい場合はこれを削減しなければなりません。人件費というのは給与だけではなく、社会保険料や労働保険、すなわち法定福利費や賞与、退職金までも含みます。さらには目に見えないコストとして十分に習熟するまでの時間にかかった教育コストが加わるのです。
省人化によってそれにかかる人員が1人でも削減されれば、その効果はかなり大きなものになります。製品の製造原価が目に見えて低減化し、利益は大きくなります。固定費部分が変わらないのであれば営業利益率も上がります。
人件費が削減できるのと同時に生産性も上がり、人手不足への対策にもなるので、単なる省人化という以上のメリットがあります。
品質の安定
あらゆる工程が産業用ロボットによって自動化されていくと、品質のばらつきは小さくなっていきます。人間の手によって加工が行われている工程があれば、個人差が品質に反映されるのは避けられません。熟練工を必要とする工程においては製品の製造が属人的になり生産性向上の障壁となっている例もありました。
ところが、FMS導入をきっかけに工程が自動化されれば長年の経験や勘もデータ化され工程に反映されていきますので、同じレベルの品質のものを生産し続けられます。品質は安定し、人が行ってきたときのような品質のばらつきはなくなります。
「この人でなければできない」といわれた工程もデータ化して組織的に対応できるようになるのです。FMSは品質の安定に寄与します。
安全性の向上
省人化のところで、人がいなくても作業できるようになる工程が出てくることを述べましたが、これは作業環境を改善し危険性を排除することにもつながります。労働災害の多くはヒューマンエラーや危険予知不足から起こりますが、最初から人が介在しない作業工程ではその可能性がありません。
もちろん産業用ロボットは強い力で作動したり、素早い速度で作動したりするので人と協働する作業場で危険性が生じることもあります。そういう場合ですら、センシング技術を生かして人の動線を避けるようにプログラムされるなどしていますので、人による作業工程が多くを占めている作業場よりは確実に安全になるのです。
製造時間の短縮
FMSによってすべての工程がロボット化すれば、製造時間は短くなります。熟練工の中には早く作業できるすごい人もいないわけではありません。しかし生身の人間である以上一定時間働けば休憩しなければなりませんし、休日も取得しなければなりません。
ロボットなら24時間休みなく作動させられますので、一定日数で生産できる数は人間より多くなります。工具の交換や治具の交換などの時間も短縮されますので結果的に単位時間当たりの生産スピードは人間が行うより確実に早くなります。
教育コストの削減
人が作業する場合、作業員に教育を行い、十分習熟するまで訓練を行う必要があります。一人前に作業できるようになるまでどれくらいのコストをかけたらよいのかの計算も、その成果も個人差があって難しいものがあります。
FMSによるロボットの導入で、その時間や心配は不要なものとなります。教育にかけるコストは目に見えない部分が大きく、気づかないうちに大きな負担になっていると考えられます。ロボットの場合はプログラムとデータによって制御されますので一度セットすれば同じ精度で作業を続けられますし、教育コストも個人差もありません。教育コストが大幅に削減できるのは数字になって見えてきませんが、大きなメリットの1つです。
FMS導入のデメリット
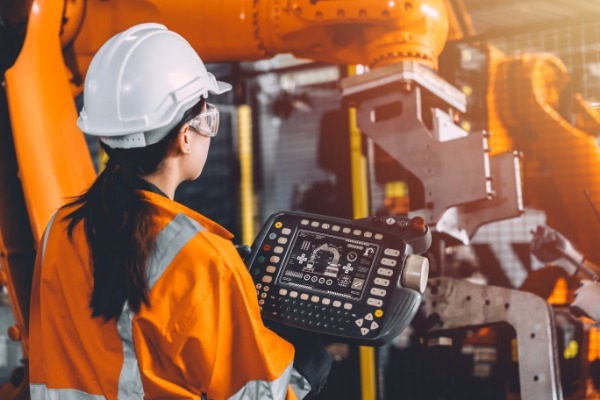
これまで述べてきたように、FMSには多くのメリットがありますが、導入して効果を出すためにはいくつかの障壁を乗り越える必要もあります。ここではFMS導入にあたってデメリットに数えられてしまうような導入にあたっての障壁をいくつかご紹介しておきましょう。
生産計画の複雑化
多品種変量生産に対応した工場運営は、生産計画を立てるのが容易ではなくなります。
FMSにおいてはすべての工程に汎用設備を用いるようなことも多いため、自由度は高まります。一方で、生産する品種ごとに工具の取替やサイクルタイムなどの生産条件が異なってくるので、製品ごとに製造する手順や方法の組み合わせが膨大な数になります。
需給変動や、機械がストップした時の対応などもでてくるので熟練技術者でも生産計画立案が困難になってくる場合があります。
導入コスト
FMSのメリットの段でコスト削減につながる点も述べましたが、一方でFMSの導入にはかなりの初期投資が必要となります。FMSは、全工程を産業用ロボットで自動化しますが、産業用ロボットは安いものではありません。
機械本体の価格だけではなく、ロボットSIerに支払う料金や、設置工事費、保守料も含めるとその投資額はかなりの額になります。導入計画を考える際は、投資対効果を考えて計画を綿密に立てる必要があるでしょう。代わりに人件費が削減できるのと生産効率が上がることでどれくらいの時間があれば回収できるのかの判断がカギとなります。
ロボット選定、ティーチング
FMS導入に際してどのロボットを選べばよいのかという点については専門知識が必要になってきます。ロボットを選んだとしても、これにティーチングをしなければなりません。ティーチングには専門的な知識が必要になりますし、指定された講習の受講も必要になってきます。誰でもできるわけではなく可能な人材が限られてきます。だからといってこれが滞るとラインが立ち上がらず、生産が遅れるということになります。
このようなデメリットを克服するためにロボットSIerの存在があります。産業用ロボットについてほとんど知識のない人がFMSを導入するにはロボットSIerの力を借りずにはできないでしょう。
図2.ロボットティーチング
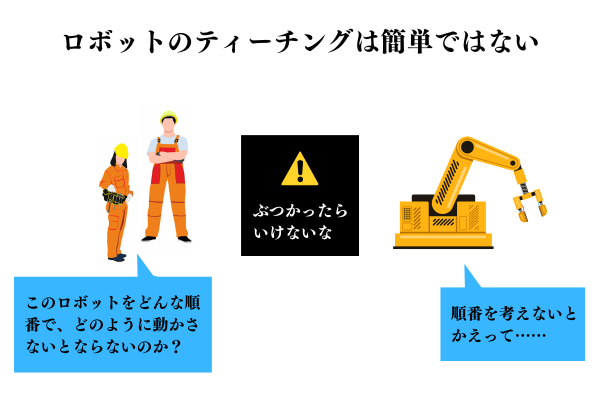
まとめ
FMSは多品種変量生産という時代の要請に応えるためのシステムです。フレキシブルに多品種を作り分けられる生産ラインがあれば、どのような要請があっても応えられるので市場では有利になるに違いありません。
ただそれをするには、これまでのものづくりに対する考え方の変革や、初期投資もそれなりに必要になってきます。導入する側としても勉強しなければならないことが多くあるでしょう。現代は生き残りをかけて変革をする、まさに製造業がデジタルトランスフォーメーションをする時が来たのではないでしょうか。
(提供:Koto Online)