近年は、製造業だけでなくサービス業やIT業界などさまざまな業種で品質管理の重要性が高まっています。そこで注目されているのがシックスシグマと呼ばれる経営・品質管理手法です。シックスシグマは、統計分析を体系的に用いることで企業におけるさまざまな活動プロセスの分析を行い、問題の原因と対策を発見して製品・サービスの品質向上を実現し、顧客満足度の向上を図る手法です。
本記事では、シックスシグマの概要や導入の際の注意点、成功させるためのポイントについて詳しく解説します。
目次
シックスシグマとは
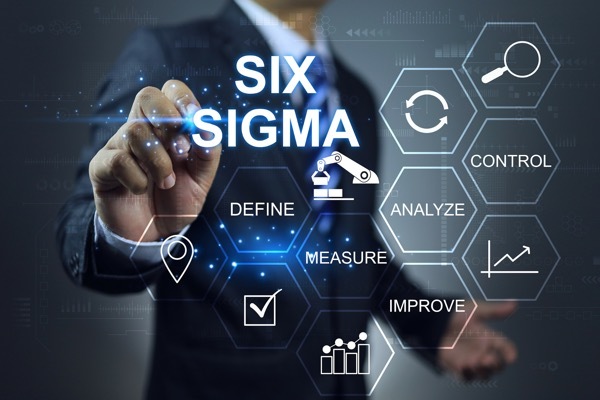
はじめにシックスシグマの名前の意味と由来、定義について解説します。
シックスシグマの定義
シックスシグマ(Six Sigma)とは、主に製造業におけるあらゆる部門の業務の品質改善と効率向上を目指す手法のことを指します。シグマ(σ)とは「標準偏差」という意味で、標準偏差(後述)は統計学の言葉です。シックスシグマでは「DMAIC(定義・測定・分析・改善・制御)(後述)」という5段階の手順を用いてプロセスの「ばらつき」を減少させます。
この結果、欠陥や不良の発生率を「6σ(シックスシグマ)=3.4ppm(100万個あたり3.4個)以下」にまで抑えることを目指します。
シックスシグマの命名の理由
この手法がシックスシグマと命名されたのは、「ロスの発生率を6σに抑える」ことが由来になっています。
統計学とシックスシグマ
【図】正規分布グラフにおける標準偏差とその分布割合
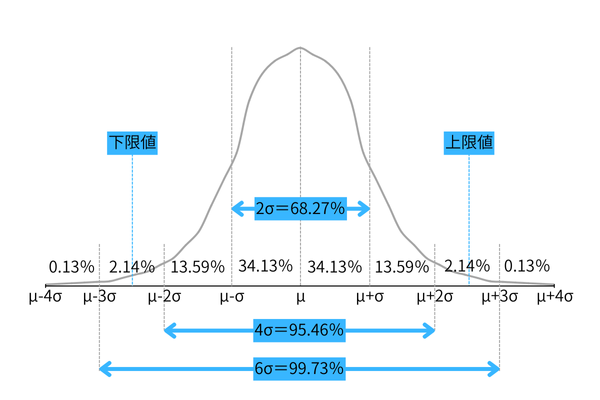
ここで統計学と標準偏差、正規分布について苦手な方もいるかもしれませんので、わかりやすく説明します。統計学における考え方は「いろいろな値が出現する世の中の事象の発生確率は正規分布する」という前提です。ランダムに事象が発生するとき平均値に最も数が多く集まり(つまり発生確率が最も高くなる)、平均値から離れるほど発生確率が低くなる分布になります。
標準偏差とは「どれくらいの範囲に散らばっているか(分布の偏り具合、散らばり具合、ばらつき具合などと表現される)」を表す単位です。それを「σ」という文字を使って表します。事象が正規分布しているとき、グラフは真ん中が最も高く、端にいくほど低くなり、左右対称の山型で表される形となります。
平均値(中心)からの左右それぞれのばらつきは「σ」、平均値の両側のばらつきは「±σ」と表記します。データが正規分布しているとき、±σ(±1σ)のなかに全体の68.26%、±2σのなかには全体の95.44%、±3σのなかには全体の99.73%のデータが収まるとされます。ただし数字については、資料によってもぶれがあります。
参考までに一般財団法人日本規格協会による工程能力指数は以下のとおりです。
【不良率(両側規格)】※両側規格とは、平均値の左右両側の範囲を指す
±σ =31.7%
±1σ=4.55%
±3σ=0.27%
±4σ=0.0063%
±5σ=0.000057%
(出典)『工程能力指数』(社)日本品質管理学会 監修,永田 靖・棟近 雅彦 共著,日本規格協会グループ
σ(1σ)から数字が大きくなるに従い、分布のばらつきは少なくなっていきます。100万回あたりの不良回数は、±σで31.7%(約31万7,000回)、±3σでは約2,700回だったものが、シックスシグマ(6σ)の場合、約3.4回です。
シックスシグマにおける「6σ」の数値と注意点
現実的には、±3σの数値でもかなりの好成績ですが、シックスシグマではほとんどミスがないことになり、実現不可能なレベルのように感じる人が多いのではないでしょうか。実際にTQMやTQC(全社的品質マネジメント、全社的品質管理)の実践における不良・異常の判定ラインは、一般的に3σが目安とされています(業種による)。
通常は、それ以上厳しく管理をすると設備に管理コストがかかり、かえって運用コストが高くなってしまう可能性があることには注意が必要です。そのため検品や検査で不良品を確実に弾くことで、出荷する製品の不良率を6σにするほうが現実的な場合もあります。なおシックスシグマでは、3.4ppmが実現されるといわれていますが、本来の統計学における6σの値は0.002ppmです。
この差は、マイケル・ハリー(モトローラがシックスシグマを開発した際のオリジナルメンバー。シックスシグマのワールドクラスのコンサルタント)によれば「ベルカーブの中心部(平均値)を右へずらすことにより,本来なら4.5σ(3.4ppm)であるものを,「6σ」に到達できる(平均値を1.5σ分だけ右にずらす)」ことからきています。
そのためシックスシグマという経営理論では、6σ=3.4ppmとされていることに注意が必要です。一見、非現実的な数字を挙げていることから、シックスシグマは実現不可能な「スローガン」のようなものと思う人もいるかもしれません。しかしシックスシグマは、単なる生産工程の数字改善だけを目的にしているものではありません。
例えば管理部門などの業務効率化など、企業活動全般を視野に入れた品質向上のためのアプローチといえます。
*(出典)「シックスシグマの意義と課題」岐阜聖徳学園大学 伊藤賢次,日本生産管理学会論文誌,Vol.8, No.2, 2002. 3
【関連記事】
TQMとは?全社的品質マネジメントにおける意味とTQCとの違い
シックスシグマの歴史とQCサークル活動との関連
シックスシグマは、1980年代に米国のモトローラ社で開発された品質管理手法です。モトローラ社は、1970年代後半ごろから自社製品の品質に不満を持っていたため、そのころから全社的に製品の品質改善運動をスタートします。1980年代に日本のポケベル市場に参入しようとしたモトローラ社は、日本メーカーの製品と自社製品の品質の差に驚きます。
日本製品の品質は、モトローラ社のものをはるかに上回るものでした。この差を埋めるべくモトローラは、日本的経営スタイルを研究し、その結果生まれたのがシックスシグマといわれています。特にモトローラが参考にしたのが、日本の製造業をはじめとしたさまざまな業種で現在も行われている「QCサークル活動」でした。
QCサークル活動とは、小集団改善活動とも呼ばれ、一般的に10人程度の小規模の集団で行われる製品やサービスの品質管理(Quality Control=QC)を向上させるための改善活動を指します。もともとQCサークル活動は、米国の統計学者W・エドワーズ・デミングによって1950年に提唱されたものです。しかし日本に伝わると日本の事情に合わせて独自の発展を始めます。
1962年に日本型のQCサークルが生まれ、2000年代にはQCサークル活動が多くの組織で行われるようになりました。QCサークル活動の特徴は、現場の従業員などがお互いにアイデアを出し合って業務改善や品質向上を目指すことです。特に日本型のQCサークル活動は、自主的な活動に近くボトムアップ型手法で経過よりも、どのような結果・実績を出せたかを重視します。
一方、シックスシグマはQCサークル活動をベースにトップダウン型の手法として考案されたものです。また結果はもちろん、プロセスそのものも重要です。このようにモトローラ社は、日本式をそのまま取り入れたのではなく米国式に合わせてより効率的になり効果が出るよう改良したことがわかります。やがてGE(ゼネラル・エレクトリック社)がシックスシグマを導入し「クオリティ2000計画」を実施。
大幅なコスト削減と品質改善など優れた業績を上げたことから、シックスシグマは米国に知られるようになります。GEは、製造業だけでなく自社の展開する業種すべてでシックスシグマを導入しました。そしてすべてにおいて品質向上、顧客満足度の向上という成果を上げ、企業価値を高めることに成功しました。
日本では、1997年にソニーが世界規模でシックスシグマを導入。東芝などの大手電機メーカーをはじめとする大手企業もこれに続き注目を集め、日本企業にも広がり始めました。現代では、さらにトヨタ生産方式から生まれたリーン生産方式と組み合わせた「リーンシックスシグマ」が導入されるようになっています(後述)。
シックスシグマにおける5つの原則とベルト制度
ここでは、シックスシグマの5つの原則とシックスシグマの資格取得者へ与えられる「ベルト」制度について解説します。
シックスシグマの5つの原則
シックスシグマの原則(目的のために行う心構え)は、以下の5つです。
- 顧客へのフォーカスを行う
- データ活用によりばらつきを発見する
- 継続的なプロセス改善を行う
- 全員で取り組む
- 柔軟性の高いサステナブルなエコシステムを作る
シックスシグマのレベルを示す「ベルト」制度
シックスシグマの現場では、教育研修を受けた「改革認定者」に認定ベルトを付与しています。
- イエローベルト:シックスシグマの基本トレーニングを受けた人、サポート役を務めます。
- グリーンベルト:部分的なプロジェクトリーダーを務めます。データ分析などを担当します。
- ブラックベルト:改善計画全体に携わるプロジェクトリーダーです。
- マスターブラックベルト:全社的導入プロジェクトを担当し戦略的にシックスシグマの取り組みを監督する、ブラックベルトの上位資格です。ブラックベルト、グリーンベルトへの教育も行います。
なお「ブラックベルト」という名称は、日本語の「黒帯」からきています。
シックスシグマの評価ポイント
シックスシグマは、企業が製品やサービスの品質を向上させ、コストを削減し、顧客満足度を高めるための効果的な手法です。シックスシグマは、株主を含め顧客と考え、徹底した顧客満足度の工場をトップダウンで追求します。製品といった成果物の質の向上だけでなく経営プロセスの質の向上をより重視し、さらに利益に対する貢献度を評価ポイントとしています。
シックスシグマでは、有限の経営資源を改善すべきどのプロセスや活動に先に充てるか、優先順位を決定しなければなりません。シックスシグマでは「業務がどれくらい改善されたか」という効果をはかるツールとして「不良品質コスト(Cost of Poor Quality:COPQ)」というスケールが用いられています。
どの活動が最も利益が出るか見極め、資金をどのプロセスに充てるかを知るためにプロジェクト完了後の実績とともに、品質改善などの活動がどの程度利益に直結し効果を出したか調査します。不良品質コスト(COPQ)は、コストがどの程度かかったのか、ロスがどれくらいあったかをダイレクトに表示するため、シックスシグマにとっては理想的なスケールといえます。
シックスシグマの他の業種への応用と注意点
シックスシグマは、本来製造業における品質向上を目的に作られたものですが、現代ではさまざまな業界で利用されるようになりました(前述のとおり、GEが自社展開する別業種に応用させた実績も影響していると思われます)。ただし業種によっては、実装方法が難しいケースやせっかく導入しても効果がうまく出ないケースもあります。
シックスシグマは、時間と費用がある程度かかります。効果的に機能させるためには、その計画とプロセスに関わる関係者全員がモチベーションを維持し協力できる体制でなければなりません。また従業員へのシックスシグマを運用するための継続的な教育も求められます。その点を考慮して導入の検討が必要です。
シックスシグマの5つの段階による手順
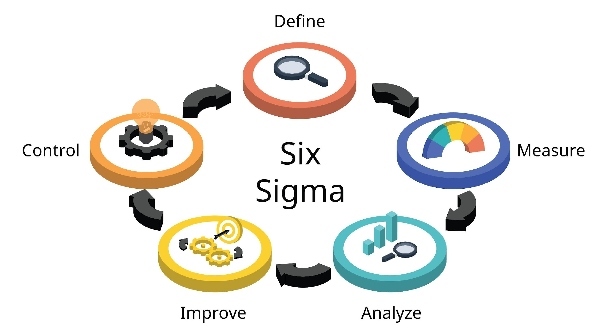
通常、シックスシグマは「DMAIC(定義、測定、分析、改善、管理)」の5つの段階にそって進められます。
定義:Define
改善すべき問題となっているプロセスや製品、その他の課題を明らかにして定義します。シックスシグマは、顧客満足度を高めることも目的となるため、顧客の声に耳を傾けプロジェクトの目標を決定します。
測定:Measure
プロセスパフォーマンスの現状測定を行い、データを収集します。
分析:Analyze
収集したデータを分析して問題となっていることを特定、さらに原因を特定します。またプロセスのばらつきの原因を調査します。
改善:Improve
改善策を実施し、プロセスを最適化、プロセスと成果物の品質向上を目指します。
管理:Control
改善結果を測定し、標準化された継続的なパフォーマンスの持続のための管理を行います。
【参考】シックスシグマとリーンシックスシグマの比較
シックスシグマとリーン生産活動の融合したものがリーンシックスシグマです。トヨタ生産方式を研究しパッケージ化されるほど洗練されている「リーン生産方式」と、製品だけでなくすべてのプロセスのばらつきを抑え品質向上を目指す手法「シックスシグマ」の優れたところをかけ合わせています。
リーンシックスシグマは、単なる課題解決ではありません。財務効果を出すことを目指すのは、シックスシグマと同じです。さらにリーンシックスシグマでは、業務改善効果を上げること、利益を出すことと並行し「リーダー人材を育成する」ことも目的とされる点が特徴です。
【関連記事】
リーン生産方式とは?トヨタ生産方式との違い・メリットをわかりやすく解説
7つのムダとは?トヨタの生産方式が指摘する「ムダ」と具体的な排除方法
シックスシグマでワークフローを改善するときの注意点
シックスシグマは、データを重視し“6σ”という目標値になるような品質のばらつきを低減させる手法です。理論だけでなくワークフレームとしての具体的な手順があり、何を評価するかなどの指標も決まっています。また多くの企業がシックスシグマで実績を上げたことも事実です。しかしどのような業種および企業でもシックスシグマが適合するわけではありません。
また6σという目標値を絶対に守らなければいけないわけでもありません。シックスシグマの最終目標かつ最大の目的は、顧客満足度の向上によって企業価値を向上させて成長し利益を上げることです。画一的にシックスシグマの枠組みに自社を合わせることが目的ではありません。自社に合った使い方をして本来の目標を達成させることが重要です。
まとめ
本記事では、シックスシグマにおける6σからの名前の由来と意味、5つの原則、歴史、改善のための具体的なステップ、導入の際の注意点などについて解説しました。もともとシックスシグマは、製品の品質向上を目指す小集団活動QCサークル活動から生まれたものです。現代では、成果物だけでなく企業活動、およびそのプロセスそのものの改善を目指す経営改善手法となっています。
製造業だけでなくさまざまな業種にも応用されているシックスシグマは、他の優れたマネジメント手法と結びつくなど、今後もさらに発展していくことが期待されます。
(参考資料)
研究論文「シックスシグマの意義と課題」伊藤賢次,日本生産管理学会論文誌 Vol.8, No.2, 2002. 3
日経クロステック:シックスシグマ手法を全社展開、計55プロジェクトで48億円の財務効果
(提供:Koto Online)