本記事は、八子 知礼の著書『DX CX SX ―― 挑戦するすべての企業に爆発的な成長をもたらす経営の思考法』(クロスメディア・パブリッシング)の中から一部を抜粋・編集しています
DXに欠かせないデジタルなPDCAの仕組み「デジタルツイン」
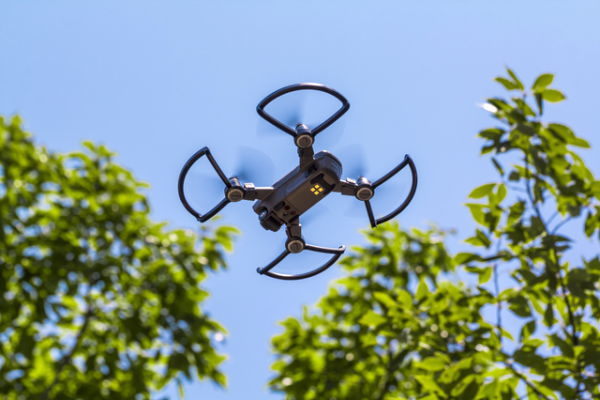
DX推進の重要なキーフレーズに「デジタルツイン」という考え方があります。これは「ビジネスの現場など、現実空間の様々な事象、状態、環境をデータで捉え、デジタル空間上に、同一条件の環境を構築する」というものです。
たとえば、デジタル空間上に、実際の製造現場の環境をデータで捉えた「仮想の製造現場」が存在したらどうでしょうか。トラブルへの対応、新たな取り組み、業務プロセスの変更、緊急時の対策など、現実空間にあっては試行や予測、検証が難しいことはたくさんあります。しかし、データを分析することでシミュレーションが可能になり、変化への対応、業務の改善、トラブルへの対応策などが検証できます。
こうして検証したデジタル空間でのシミュレーション結果の中から、最も適切だと予測できる結果を現実の製造現場にフィードバックし、実際の業務に生かす。この仕組みこそが「デジタルツイン」と呼ばれるもので、DXを推進するための強力な武器となります。
つまり、デジタルツインとは、データ取得→分析・シミュレーション→現実空間へのフィードバック→データ取得……というデジタルなPDCAサイクルを構築するための方法論なのです。
全体最適と部分最適
「全体最適」と「部分最適」の見極めは経営における重要な観点
実は、DXにおける「デジタルツイン」と、経営における「全体最適」は、密接不可分の関係にあります。そこで「全体最適」と「部分最適」に触れておきたいと思います。
たとえば、一連の生産ラインが、複数の工程から構成されている工場があったとします。各製造ラインの最適化を実施して生産能力を上げようとした場合、仮にその中に生産性を上げることができない工程が1つでもあったらどうなるでしょうか。結論からお伝えすると、その影響は次に述べるように、スムーズに流れていた前後の工程にまで及んでしまいます。
各製造ラインは工程がつながっているので、スピードが落ちた工程の設備に加工スピードを合わせざるを得ず、結果として工程全体のスループット、すなわち単位時間あたりの生産スピードが落ちることになるのです。つまり、各工程で最適化を実施しても、どこかにボトルネックがあれば、工程全体のスループットの低下を招いてしまうというわけです。これはつまり、最終的には工場そのもののスループットの低下、端的に言えば経営コストの損失増加につながります。
製造業において、全体最適がいかに大切であるかがご理解いただけると思います。
「目に見える効率化」の落とし穴
全体最適は、生産設備の話だけにとどまりません。ホワイトカラーのオフィスにおいても同じ考え方が成立します。DXブームにともない、日本の企業ではRPA(Robotic Process Automation)導入の動きが活発化しています。RPAはオフィスで日々行なわれているパソコン上の事務作業を自動化するシステムです。たとえば、Excelやスプレッドシートに記載された数字を基幹システムのデータベースにコピー&ペーストする、といった単純作業などにRPAが導入されています。
このような作業もRPAを導入することで、それまで毎日1時間の作業時間が必要だったものが数十秒〜数分で完了する、といった事務作業の効率化が可能になります。このように、「年間◯◯時間の作業の削減が可能」といった「目に見える効率化」が可能なことから、日本企業の間での人気に火がついたのかもしれません。
しかし、そんなRPAにも部分最適の落とし穴があります。たとえば、一連の業務プロセスの中にRPAを導入したとしても、そのプロセスの中に、「帳票をプリントアウトして上長の決裁印をもらう」という人間の判断を必要とするプロセスが挟まっていたらどうなるでしょうか。その部分だけは、紙と印鑑というアナログなプロセスが残っているために、人間がボトルネックになり、End to Endの全体最適を阻むことになります。
優れた部分最適の方法
先述の工場の事例や、RPAにしてもそうですが、あらゆる業務のすべてをいきなり全体最適化することは難しい場合もあるかと思います。その際は、最終的な全体最適を意識した部分最適を実施することが大切です。
各現場、各担当が生産性向上を目指して業務の最適化を実施することはとても大切ですが、横の連携がないまま好き勝手に部分最適を進めてしまうと、どこかでボトルネックが発生する形になり、全体のスループットを上げることは難しいでしょう。
コマツのLANDLOGはデジタルツインの成功例
デジタル空間で、建築現場をリアルタイムに仮想化する
DXを推進する上で、重要な要素となるデジタルツインですが、現時点で、本格的なデジタルツインを実現している事例は、世界的に見ても決して多くはありません。
そのなかで、建設機械メーカーのコマツのデータビジネスプラットフォームである「LANDLOG(ランドログ)」は、建設現場でのデジタルツインを実現しており、実際には次のようなことが行なわれています。
建設現場において、建設機器の位置情報を元にした走行データ、建機に搭載されたステレオカメラ、ドローンを飛ばして撮影した映像から、3Dの点群データを作成することができます。3Dの点群データというのは、点の集合体で空間を立体的に計測したデータのことで、ここでは土木建設現場の土地の傾斜や掘り込みの状態を点で表示することを示します。
このようなデータを毎日取得することで、地形の変化や建築の進捗といった作業状況が、すべてデータによりリアルタイムに把握できます。これを、デジタル空間上で計画図や設計図と対比させると、工事の進み具合を正確に捕捉できるようになっており、その進捗状態を現場にフィードバックする仕組みです。この時点で、建築現場のデジタルツインが実現しているのです。つまり、IoT機器から取得したデータを使い、デジタル空間上で建築現場をリアルタイムに仮想化している、という構造です。
ビジネスの課題をデジタルで解決する方法としてのデジタルツイン
従来であれば、人の手による測量作業を経なければ、現場の様子を正確に把握することができませんでした。たとえば、広大な現場であれば、測量には何日も要します。そうなると、何日か前の測量結果を確認しながら工事を進めることになり、リアルタイム性が損なわれてしまいます。
何日も前のデータを使って進捗管理をする、ということは、建設施工管理を行なっている人からすれば、それだけで大きなリスクとなります。たとえば、天候などの不可抗力で工事が1日止まったとします。その1日のずれを挽回するためには、場合によっては再度の測量作業などのために1日の遅延では済まない場合が多々あります。そうなると当然、計画に大きな狂いが生じます。
しかし、デジタルツインを実現していれば、工事現場の現況がリアルタイムで確認できるため、あらゆる可能性をシミュレーションできます。たとえば、ある現場に建機を1台、オペレーターを1名追加で配置すれば、1日の遅れは簡単に挽回可能といったことがシミュレーションできるようになるでしょう。
このように、様々なシミュレーションを実施することで、最適解を導き出し、それを現場に投入していくのです。デジタルツインで言うところの、「現実空間へのフィードバック」ということになります。
このようにして、コマツでは、建機そのものにカメラやセンサーを搭載するだけでなく、ドローン測量から得たデータをもとにデジタルツインを実現しています。
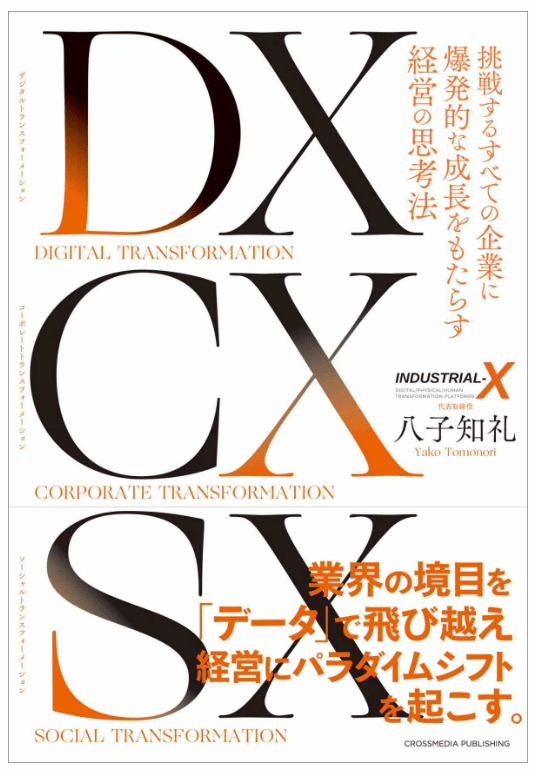
その後、後にベリングポイントとなるアーサーアンダーセンにシニアコンサルタントとして入社。2007年デロイトトーマツ コンサルティングに入社後、2010年に執行役員パートナーに就任、2014年シスコシステムズに移籍、ビジネスコンサルティング部門のシニアパートナーとして同部門の立ち上げに貢献。一貫して通信/メディア/ハイテク業界中心のビジネスコンサルタントとして新規事業戦略立案、バリューチェーン再編等を多数経験。2016年4月よりウフルIoTイノベーションセンター所長として様々なエコシステム形成に貢献。
2019年4月にINDUSTRIAL-Xを起業、代表取締役に就任。2020年10月より広島大学AI・データイノベーション教育研究センターの特任教授就任。
著書に『図解クラウド早わかり』、『モバイルクラウド』(以上、中経出版)、『IoTの基本・仕組み・重要事項が全部わかる教科書』(監修・共著、SBクリエイティブ)、『現場の活用事例でわかる IoTシステム開発テクニック』(監修・共著、日経BP社)がある。
※画像をクリックするとAmazonに飛びます