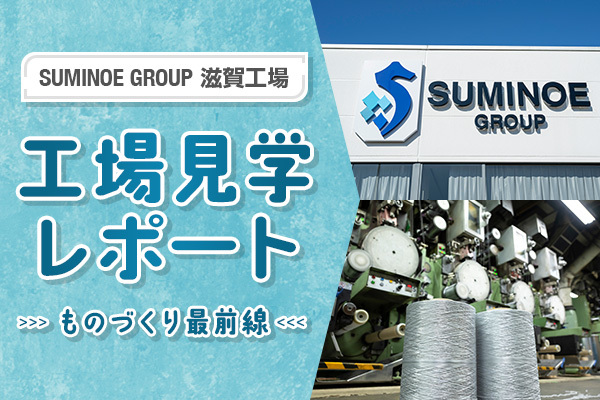
製造業の未来について発信していくYouTubeチャンネル「AMANO SCOPE」とコラボレーションし、時代に即した製造業の今の姿をより多角的にお伝えする本企画。今回ご紹介するのは、カーペットを中心としたインテリア事業や自動車・鉄道の内装事業などを手がける、SUMINOE GROUPです。AMANO SCOPEの天野眞也氏が滋賀県にある工場を訪れ、使用済みのペットボトルを再生して作った繊維「スミトロン®」の製造過程をレポートします。
また、新型車のシート表皮にスミトロン®を採用した、トヨタ自動車のモビリティ材料技術部 大下直紀氏をゲストに招き、スミノエ テイジン テクノの第三営業部部長 大杉忠司氏と天野氏の3名で対談を行いました。使用済みのペットボトルがどのように繊維に生まれ変わるのか、そして「世界のトヨタ」がどのように再生材料を生かしたクルマ作りを進めているのかについて迫ります。
本記事ではその様子を、YouTubeチャンネルの動画でもお届けします。
目次
使用済みペットボトルから生まれたスミトロン®、滋賀工場での製造過程に迫る
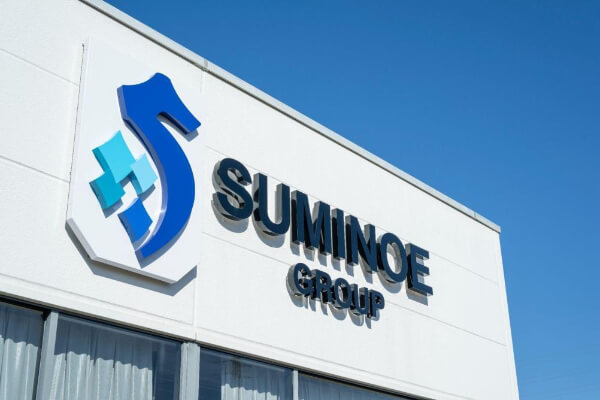
滋賀県にあるSUMINOE GROUPの工場では、使用済みのペットボトルから作られた樹脂を使い、カーペットや自動車のシートに使われる糸、スミトロン®を製造しています。使用済みのペットボトルがスミトロン®に生まれ変わる詳しい製造過程を、住江テクノ株式会社 製造部製糸課の藤田隆史課長にご案内いただきました。
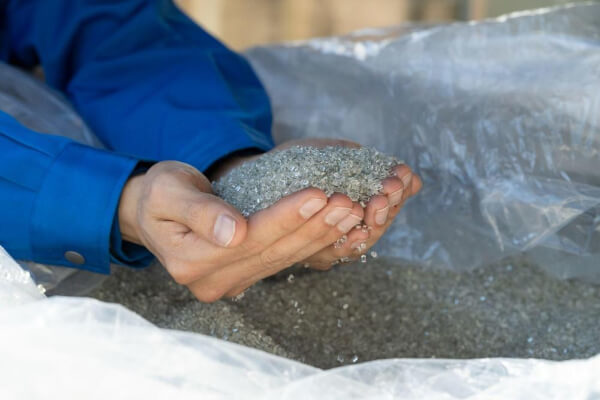
スミトロン®の製造には、使用済みのペットボトルからできた大量のペレット(粒子状の工業原料)が使用されます。ラベルや蓋を外し、回収されたペットボトルを選別、粉砕した後に洗浄して作ったものがペレットです。
藤田氏(以下、敬称略) ペレットは固体なので、熱で溶かして液体にする必要があります。ポリエステルの融点が約260度なので、それ以上の温度、大体280度ぐらいでペレットを溶かしています。
天野氏(以下、敬称略) ペットボトルからできたペレットには色がついていませんが、スミトロン®️の色はどうやって付けているのでしょうか。
藤田 例えば、透明や白いペレットと黒く着色されたペレットを同時に機械に投入することで、グレーの糸を作ることができるのです。黒いペレットを多く入れると濃いグレー、少なくすると薄いグレーというように、調合比率で色の濃淡も調節することが可能です。黒だけではなく、赤青黄いろいろな色があり、1つのラインに3台の糸を押し出す機械がついているので、3色が混ざった糸を作ることもできます。
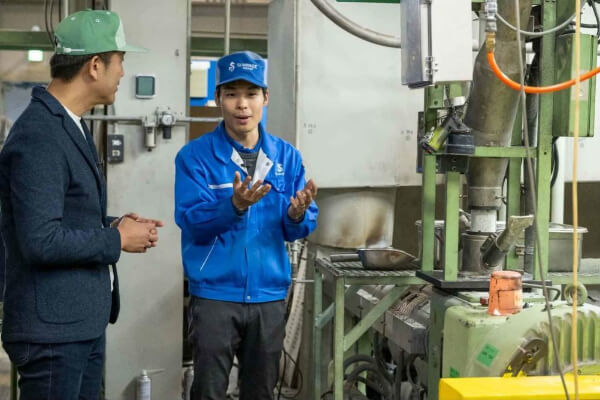
天野 いろいろな色を使って、より表現力豊かな糸を作ることができるのですね。
藤田 そうですね。そして次の工程では、液体になった樹脂を、小さな穴が開いた金属板に通して上から下に流し落とすことで、糸の形にしていきます。シャワーヘッドの穴から水を出すような、もしくはところてんを押し出して作るようなイメージですね。
そして、細い穴を通って上から落ちてきた液体の樹脂に、やわらかい冷たい風をあてています。溶けた樹脂は熱を持っているので、風をあてて冷却し、固めて糸にするのです。
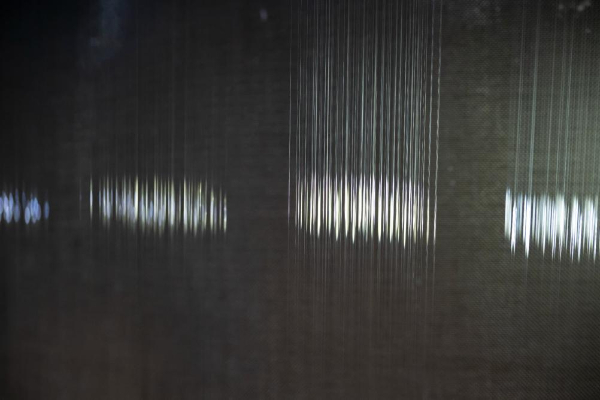
天野 まさにスミトロン®製造の心臓部ともいえる工程ですね。
藤田 はい。風が強すぎると1本1本がくっついてしまったり、金属板の穴が詰まってうまく樹脂が出なかったりすることがあるので、注意が必要です。
穴を通って上から下に降りていった糸を、今度は金属のローラーで巻きとります。そして、糸を引っ張って強度を持たせる「延伸」という工程に移ります。さらに、スミトロン®はカーペットなどで使用されることが多いので、捲縮(けんしゅく)加工といって、パーマをかけたように糸にボリューム感を持たせる加工をしています。
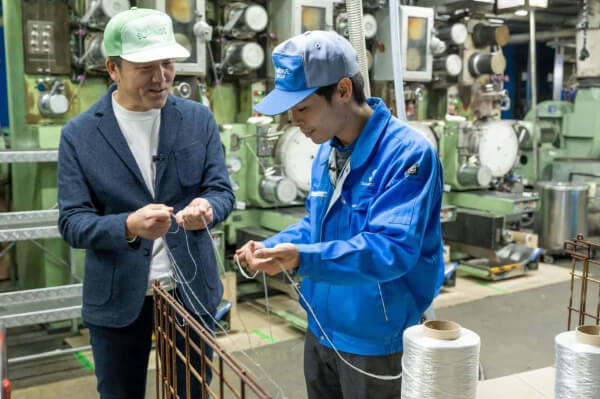
天野 ちなみに、SUMINOE GROUPさんではかなり前から再生ペットボトルを原料とした糸を製造されていると伺いました。
藤田 はい。当社では、約30年ほど前からスミトロン®を作っています。昨今、SDGsなどによって環境問題に対する意識が高まり、CO2削減に向けた取り組みが各方面で活発になっています。そうした影響もあり、お陰様で、昔から製造している再生原料を使ったスミトロン®にも注目していただけるようになったのかなと思います。
SUMINOE GROUPの工場見学動画
本記事では、工場見学の一部をご紹介しています。滋賀工場の中の様子や、使用済みのペットボトルからできたペレットが溶かされ、そしてスミトロン®として生まれ変わる詳しい製造過程の様子については、天野氏がナビゲートする以下の動画よりご覧ください。
https://www.youtube.com/c/AMANOSCOPE
スミトロン®は、カーペットやオフィスなどの入り口マット、洗浄ブラシなど、さまざまな用途に活用されています。そのうちの一つが、トヨタ自動車が昨年公開した、新しいクルマのシート表皮です。
トヨタ自動車でクルマの内装や表皮の開発に携わっている大下直紀氏と、SUMINOE GROUPの営業を担当しているスミノエ テイジン テクノの大杉忠司氏をお招きし、トヨタ自動車が表皮シートにスミトロン®を選んだ理由、トヨタ自動車とSUMINOE GROUPが共にすすめる、CO2削減に寄与する珍しい取り組みなどについて、お話いただきました。
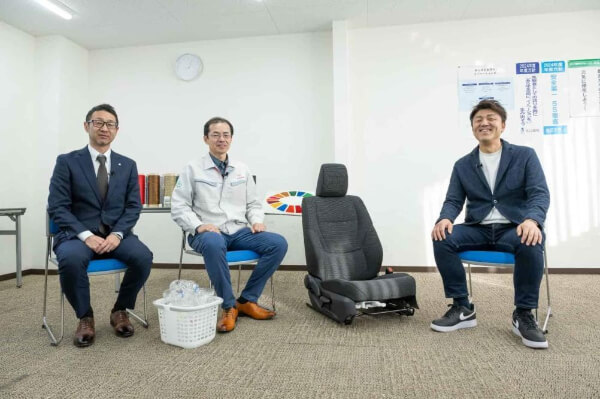
1996年、トヨタ自動車株式会社に入社。主に、インパネやシートなど自動車内装樹脂・表皮材料の開発を担当。ベルギーおよび中国・天津での駐在時には、地域ニーズにマッチした材料の開発を推進。天津のR&D駐在時、幾多の評価・解析により、車室内VOC(揮発性有機化合物)に関する世界初の知見を発見、論文を執筆し、技術雑誌「天津科技」に2度掲載。2021年5月より現職、カーボンニュートラル実現に向けたシート表皮の将来シナリオ策定、環境対応材料開発などに従事。
1998年、住江織物株式会社(現 SUMINOE GROUP)入社。トヨタ担当の営業部に配属後、自動車内装材の量産管理、生産準備を担当。その後、表皮開発を担当するようになり、日産・いすゞ向け、ホンダ・スバル向け等の各営業部長として、国内の様々な自動車メーカーとの内装材全ての開発経験を経て、古巣である、現職のトヨタ・ダイハツ向けの営業部長に着任。営業一筋25年。
株式会社カクシン CRO
株式会社FAプロダクツ/株式会社さくらFuture Vision 顧問
1992年、キーエンスに新卒入社。工場の自動化に関わるセンサやカメラの提案に従事し、グループ責任者、営業所長を経て社長直轄の海外営業・重点顧客プロジェクトの初代リーダーに抜擢。売上数百億円から二千億円の企業へと成長するまでの期間、営業として第一線でけん引する。キーエンスで築き上げた自動車・食品・半導体などのあらゆる業界の生産現場を見てきた経験と、顧客と共に海外を含む新工場プロジェクトを成功に導いてきた実績を基に、2010年に起業。
選ばれる企業になるためのファクトリーブランディング
天野 今回、新たにトヨタ自動車のシート表皮にスミトロン®が採用されたということですが、一体、どのクルマのシートに使われているのでしょうか。
大下氏(以下、敬称略) 昨年8月に新たに公開された、“ランドクルーザー250”のシート表皮に、スミトロン®を使っています。私たちは自動車メーカーとして、2050年のカーボンニュートラルに向け、CO2を削減するためのいろいろな取り組みを進めています。その1つとして、内装材料にリサイクル材料を採用することを推進しているのですが、そうした際に大杉さんから使用済みのペットボトルから作られたスミトロン®を紹介していただいたのが最初のきっかけです。
スミトロン®をシート表皮に使うことで、私たちが目標としているリサイクル率を上げ、さらに従来の表皮でクルマを製造したときと比べて、CO2を約10%削減することができるのです。
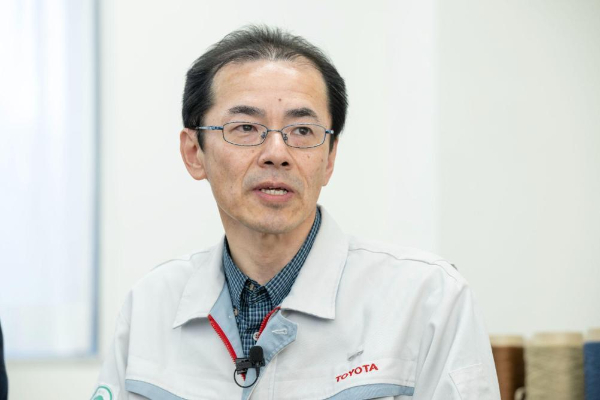
天野 10%の削減というのは大きいですね。環境面に配慮した素材であるということのほかに、スミトロン®を選んだ理由は何かあったのでしょうか。
大下 1つは耐久性ですね。シート表皮には、“ランドクルーザー250”のコンセプトに合った、タフで力強い表皮が求められます。また、シートは必ずお客様の目に触れて、お客様が座る場所になるため、高いデザイン性や意匠性も必要です。そうした点も含めて、スミトロン®を使うことで、私たちが求めているシート表皮を実現できると判断しました。
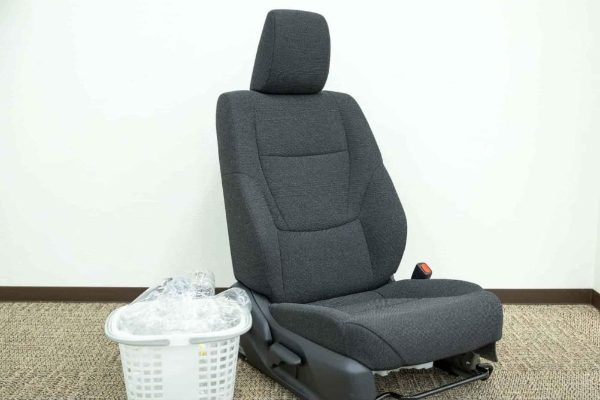
大杉氏(以下、敬称略) 今回、実際にスミトロン®を使った“ランドクルーザー250”のシートを大下さんが持ってきてくださいました。こちらはブラック色になりますが、よく見ていただくと、糸の中で黒っぽい色、グレーっぽい色、白っぽい色の3色を使って色を表現しているのです。タフな印象を与えつつも、いわゆる高級感を持たせるよう、糸の色味にも工夫をしています。
トヨタ自動車全従業員が回収に協力、ひと月6トンのペットボトルが工場へ
天野 トヨタ自動車のシート表皮に使う糸を作るとなると、かなりたくさんの使用済みペットボトルが必要になると思うのですが、どのように調達しているのですか。
大杉 そうですね。環境問題に対して社会の意識が高まるにつれて、ぺットボトルがいろいろなところで再利用されるケースが増えてきました。スミトロン®以外に使用済みペットボトルを使った製品もたくさん出てきて、実は、スミトロン®を製造する上でペットボトルの数量の確保には、少し不安があったのです。もしかしたら供給が不安定になってしまうかもしれない、という旨を、当初、大下さんに率直にご相談しました。
大下 大杉さんからお話を聞いて、なるほどと思うと同時に、何とか協力できないかと考えました。そこで、小さなことかもしれませんが、私が所属している材料技術部の従業員で、飲み終わったペットボトルを集めてお渡しすることにしたのです。
最初は私たちの部署だけで始めた活動だったのですが、社内で説明などをしながら認知度を上げ、少しずつ参加者が増えていきました。現在では、当社の全従業員が使った、これまで捨てていたペットボトルを全て回収し、こちらのスミトロン®の原材料として使っていただける規模にまで、取り組みが大きくなっています。
大杉 以前、トヨタ自動車さんを訪問した際に見つけたのですが、ペットボトルを再利用してシート表皮ができるという、今回の取り組みをお知らせするポスターがいたるところに貼ってありました。
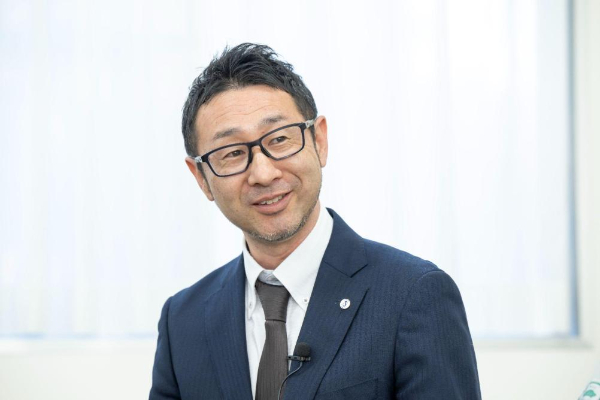
天野 トヨタ自動車さんの全従業員というとかなりの数だと思いますが、大体どのくらいの量のペットボトルがトヨタ自動車さんから集められているのでしょうか。
大下 当社の従業員は7万人以上いるのですが、その全従業員が捨てるペットボトルは毎日1万本以上、ひと月におよそ6トンあります。これまで捨てられていたそのペットボトルをリサイクル業者さんに渡して加工してもらい、それをSUMINOE GROUPさんに送ってスミトロン®を作っていただいています。私たちトヨタ自動車の従業員から集めたペットボトルが、まさに“ランドクルーザー250”のシート表皮になっているのです。
大体1台の“ランドクルーザー250”のシート表皮を作るのに、ペットボトル21本が必要になります。自分たちが集めたものが再利用されてクルマの一部になっているということで、従業員もペットボトルの回収に協力するモチベーションになっていると思います。
天野 毎日1万本、ひと月に6トンというのはかなりの数ですね。しかも自分たちの会社で集めた再生材料を使って、自分たちの会社のクルマを製造するというのは、本当に驚きです。こうした事例は他にもあるのですか。
大杉 自動車業界で、自社製品に使う再生材料を自社で集めているというのは、少なくとも私は聞いたことがないですね。かなり珍しい取り組みだと言えるのではないでしょうか。
再生材料を使って、製造過程においても環境にやさしいクルマを
天野 これからの自動車は、製造過程においても地球環境に配慮しているかどうかが問われてくると思います。CO2削減などのさまざまな取り組みが進むなかで、今回の活動は従業員の方たち一人ひとりが自分ごととして参加できる、本当に良い事例だなと感じました。
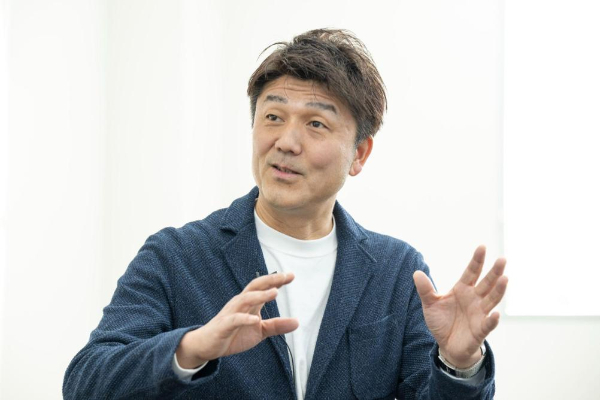
天野 今後、再生材料の活用は各方面でどんどん増えていくと思いますが、お二方の今後の展望について、改めてお聞かせいただけますか。
大杉 今日、実際にスミトロン®からできたシートをこうして見せていただいて、メーカーとして改めてありがたく思うとともに、非常にやりがいを感じました。品質はもちろん、環境への影響についてもしっかりと考慮した素材を作りご提供していくのが、私たちの会社に与えられている使命だと思っています。これからもお客様のニーズにあったご提案をしていけるよう、努力をしていきたいと思いますので、ぜひ今後ともどうぞよろしくお願いいたします。
大下 私たちは自動車メーカー、モビリティカンパニーとして、お客様により良い商品、より良いクルマを常に提供していきたいと考えています。特にカーボンニュートラル貢献に向けては、環境に配慮した取り組みを今後も続けることが必要です。材料に関する技術者として、素材の面からクルマの未来を変えていきたい、それが今後の目標ですね。
天野 大下さん、大杉さん、本日はありがとうございました。

トヨタ自動車・スミノエ テイジン テクノの対談動画
https://www.youtube.com/c/AMANOSCOPE
【関連リンク】
トヨタ自動車株式会社 https://global.toyota/jp/
住江織物株式会社 https://suminoe.co.jp/
AMANO SCOPE(YouTubeチャンネル) https://www.youtube.com/@AMANOSCOPE
(提供:Koto Online)