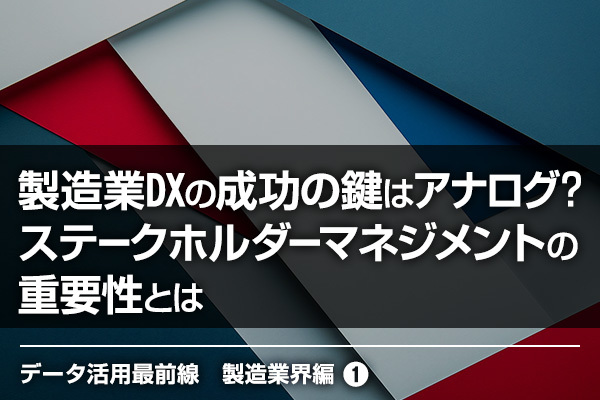
製造業DXの重要性が叫ばれて久しいですが、次々と新しく先進的なテクノロジーがIoT、AIも実践活用されてきており、日進月歩の様相を呈しています。しかし、そのようなテクノロジーの進歩と相反して、製造業DXの推進レベルは企業によって差が生まれており、まだまだ業界全体で浸透しているとは言いにくい状況です。
DX推進の成功についてはさまざまな情報が溢れていますが、「DX推進の成功の秘訣はアナログ」と答えるのは、数多くの製造業企業でDX推進を進めてきたウイングアーク1st株式会社の小林大悟氏と株式会社コアコンセプト・テクノロジーの石原雅崇氏。
企業のDX(デジタルトランスフォーメション)を支援する専門家のお二人に、製造業DX推進の解決策について伺いました。
Data Empowerment事業部 ビジネスディベロップメント部
2018年、ウイングアーク1stに入社。現在 BIダッシュボード MotionBoardの製品企画・戦略立案に従事。また、2010年からIoTの推進に注力しており、ベンチャー企業でのIoTプラットフォームの事業企画や、大手ドイツ自動車部品メーカでのインダストリー4.0やコネクテッドカー向けシステムを手掛けた経験から、IoTデータの活用を中心としたエバンジェリスト活動も行っている。
DX事業本部 副本部長
東京大学工学部で原子炉材料研究のかたわら、Webシステム開発会社を起業。2015年、製造業関連で先進的なアプリケーション開発に取り組むCCTに入社。クラウド基盤構築、ビッグデータ基盤構築、機械学習アプリケーション開発、3Dレンダリング開発などを担当。2020年に、スマートファクトリーを中心とした製造業DX支援事業の責任者に就任。
日本製造業のカイゼン文化がDXでは生かしきれていない
ーー製造業では以前からDXの重要性が叫ばれてきました。現状の製造業のDX推進について、率直にどのような印象をお持ちですか?
石原:大手メーカー様向けにMESやIoTの構築をさせていただくのが最初の経験でしたので、製造業界のDXは進んでいる印象を受けましたが、その後中堅企業のお客様などを担当していくうちに、多くの企業がデジタル化、DXの実現を検討されているけど、うまく進んでいない状態だと思っています。
小林:私はさまざまな企業規模のクライアントを担当してきましたが、一言で製造業といってもDX推進のレベルはまちまちの印象です。
デジタル化やデータをどう取得するのかで悩まれている方もまだ結構いらっしゃいますね。そのほか、データ取得はできるようになり、現状把握の見える化まで進んだものの、そのデータを改善にどう生かすかに課題を抱えている企業もあります。さらに、一部の部門で改善効果が出てきたものの、製造、購買、設計などそれぞれの部門と経営とがデータでつながって意思決定できている企業は多くない印象です。
ーー企業によって差が出始めているのですね。どのような原因で推進が上手くいかないケースがあるのでしょうか。
小林:私自身の体験談でもあるのですが、経営陣から「徹底的にコストダウンをしろ」「きっちりとしたものづくりしろ」などの指示が降りてきて、各現場が何をどれほど改善すれば会社の経営目標が達成できるのかが数字で見えていない。データに基づかず、最後は根性論みたいになっているケースはよく見受けられます。
これを解決するには様々なステップを踏む必要がありますが、まず「データ化ができてない」課題について説明すると、アナログでリアルな製造業の現場では、データはあっても、紙に書いてあったり、勘とかコツのように誰かの頭の中にあったりすることが多いです。それらをどうデジタルのデータにしていくかが、最初の壁となります。
石原:職人気質な方は工夫を積み重ねてきた現状の仕組みから変えたくないという思いが強く、デジタルに拒否感を示されることがあります。またこれまで構築してきた独自システムやExcel等も多々あり、心理的にこれまで培ってきたものを失くしたくない考えが根強いですね。
危機感はある一方で、DXのROI(投資対効果)が見えにくく路頭に迷ってしまうケースもあります。なんとなく必要そうな設備・システムの見積もりを取られたりはするんですが、総投資額も効果も計算しきれずに頓挫し、進まない企業は多いです。
小林:実は現場の方は、現状のやり方であまり困っていなかったりすることも多いですよね。DXは「カイゼンを回すための便利な道具」であると理解していただくことにまだまだ工夫の余地があると考えています。
ーーカイゼン文化がある日本製造業で、DX推進が上手くいかないのは興味深い視点です。ROI(費用対効果)が見えにくい課題は、やはり経営と現場がデータでつながっていないことが要因でしょうか?
石原:まずDXの全体像や目的が明確になっていないため、投資額が正確に揃わないんです。情報が集まっていなかったり、現場のデータも可視化ができていないので、現実味がないざっくりとした試算になるケースがよくあります。
小林:実状にそぐわない挑戦をしてしまうケースも結構あります。DX文脈では、先進的でキラキラした事例が次々と世の中に発表されるので、どうしてもそこに目が行きがちですが、自社においてもそれが効果を生むとは限らない。
例えば、保全ではAIとIoTを活用した予知保全という分野があります。突発故障を予知して事前に防ぐシステムですが、すべての設備に対して投資対効果が出るわけではありません。物量が非常に多いラインなどであれば停止による経済的損失も大きいので効果が見込めますが、そうでないと十分な効果をだすことが難しいケースも多いです。十年に一回しか壊れないものもあるでしょうし、突発故障よりは経年劣化での停止が多い設備もあるでしょう。そもそも壊れないように設備改良するアプローチもあるかもしれません。そのため、予知保全、予防保全、事後保全など最適な保全方法を組み合わせないと投資対効果は出てこないのです。
経営と現場の指標が分断されることでDXの目的・効果が見えにくい
ーー現場の課題を経営指標につなげる際のポイントはありますか?
小林:本来はそもそもつながっているはずなんです。よくKPIツリーで表現されますが、例えば、経営サイドでROA(総資産利益率)の向上目指すとしましょう。ROA向上をブレイクダウンしていくと、現場の指標である在庫回転率向上になったり、部品コストの削減につながります。このように経営指標は現場の指標に落とし込みできるはずですが、データでこれらの指標がつながって戦略立案できている企業は少ないですね。なので「徹底的に」とか「きっちりと」みたいな話になってしまう。
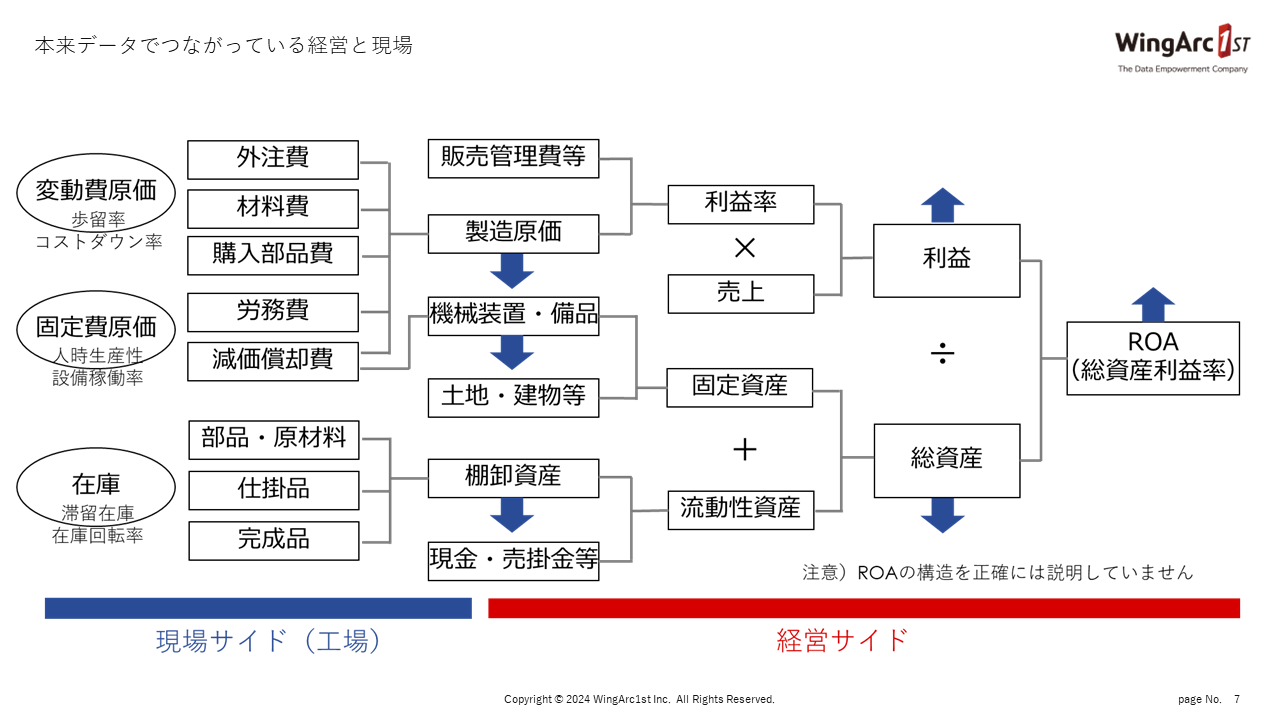
逆も然りです。現場から「不良率を20%削減しました」とか「稼働率を10%あげました」という改善が出てきますが、経営陣からするとどれだけ収益性に影響があったか見えにくい。例えば、一個10,000円の製品の不良率なのか、一個100円の製品の不良率なのかによって金額インパクトは違います。
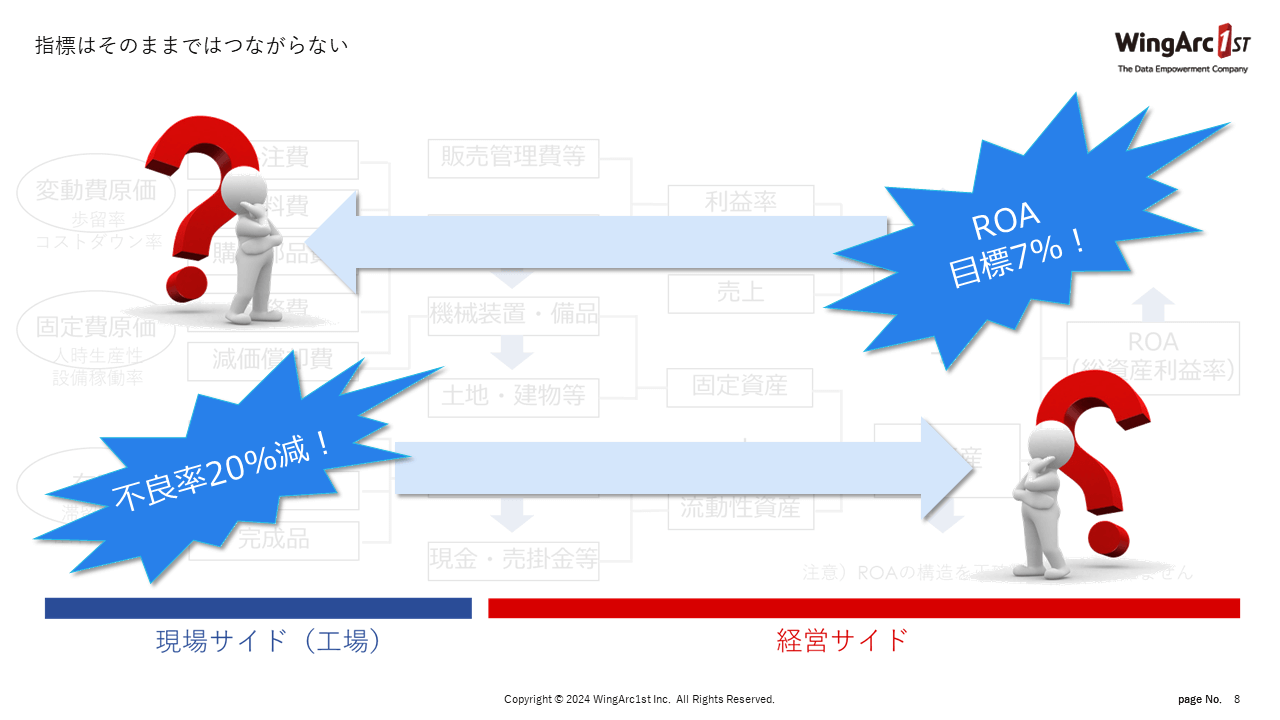
ーーでは現実的なDXの投資対効果にアプローチするにあたり、どのようにクライアントとコミュニケーションをとっていますか?
石原:しっかりと現状把握した上で新しい仕組みを入れたらどうなるのか? 「AsIs/ToBe」(「AsIs=現状」と「ToBe=理想の姿」)を定めることを重視しています。理想に至るまでに既存の設備・システム、手順を活用しながら、ガラッと変えるのではなく段階的にステップを踏みながら、現実的に運用可能にしていくように提案しています。
スモールスタートの段階で頓挫しては元も子もないので、投資対効果が各段階で見えるようにKPIを策定します。ソリューションは大規模なものを導入するのではなく、必要に応じてサブパッケージレベルで導入していくことを意識して、既存のシステムも適宜うまく活用しています。
小林:DXという言葉が世に出てから、特に全体最適というテーマが重要視されていると感じています。全体最適は、生産現場だけじゃなく購買や品質保証、設計、経営など部署横断で進める必要があります。そのため現場の業務が楽になるデジタルツールを導入しつつ、そこから得られたデータを戦略的な意思決定につなげて全体最適化を図っていく、その両輪が必要です。
その実現においてはシステムやデータの課題もありますが、人・組織、経営者への巻き込み、場合によっては現場の反対を乗り越えないといけません。お客様の人間模様や組織体制も含めてステークホルダーの方々を把握した上で進めないといけません。
現場とIT双方の立場が理解できるキーマンを推進者に
ーーステークホルダーマネジメントが重要になる上で、キーマンはどなたになるでしょう?
小林:キーマンは、経営者の場合もあるし、DX推進の方のケースもあって様々です。組織の中で、この人がヒーローになるとプロジェクトが進むという推進者を見つけるのがポイントですね。
成功する推進者の特性はさまざまですので、唯一の成功パターンはないのですが、ITや現場を理解してビジネス成果につなげる必要があるため、一般的には広範囲な理解が必要となります。でも知識面が不足していたとしても、「あの人に頼まれたら断れない」という特性を持っている方がDX推進者になると、周りの人を上手く巻き込んで成功したりもします。技術やプロセスももちろん重要なのですが、推進者の方の立ち回り、ステークホルダーマネジメントが鍵だったりします。成功の秘訣って結構アナログだったりします(笑)。
逆に失敗パターンは定型のものがいくつか存在し、例えばITに詳しくてシステムをつくることにフォーカスしてしまい、現場に行かないような推進者は失敗する可能性が高いです。
石原:やはり重要な役割となるのはDX推進者なので、小林さんが仰ったような方が推進者となるのが理想ですね。推進者の頭の中だけで考えて導入するのではなく、実際に業務で使用する方々にも業務変革の意識や変革後のイメージを浸透させていかなくてはいけない。そのため、DX推進する際には多くのステークホルダーとコミュニケーションを取る必要があります。
ーーウイングアーク社では、そのような課題を解決するためのソリューションとして、MotionBoardなどの製品を提供されていますが、特徴を教えて頂けますか
石原:これまで話した通り、最初はスモールスタートで段階的にソリューションを導入するケースが多いので、サブパッケージで導入できることが非常に大きいです。
製造業でもお客様によって課題はさまざまですが、カスタマイズの負荷も小さいですし、その他のBIツールと比較しても我々が実現したいことが大抵できてしまい、フィット率が非常に高いです。
小林:ありがとうございます。MotionBoardは一応BIツールというカテゴリーには属しますが、一般的なBIツールにはない機能がいくつかあります。生産現場の中で特に生きてくるのがリアルタイムに可視化ができる点です。
例えば、設備が壊れたというアラートが、15分遅れとか1時間遅れで来ても困りますよね。ですが、リアルタイムで秒単位にアラート通知できるBIツールは意外と少ないので、その点は当社の強みです。
また、入力機能も特徴的な機能です。例えば、現場で設備停止が起きたときに担当者がその理由を付加したくなることがよくあります。例えば、手動で設備を止めた場合は、真の停止理由は設備からは取れませんが、MotionBoardなら作業員が入力することもできます。それらのユニークな機能が製造業で支持されている理由かなと思います。
本記事のポイント
・日本の製造業のカイゼン文化がDXでは生かされていない
・現場と経営指標のデータによるつなぎこみが製造業DXの鍵となる
・壁を作らずにステークホルダーマネジメントが可能な推進者が成功を収めている事例が多い
(提供:Koto Online)