近年では、ITシステムやロボット技術の発展により、倉庫内を自動化する企業が増えています。物流業界を中心に導入が進んでいますが、製造業にも物流業務をともなうため注目を集めています。倉庫の自動化は人材不足やコストなどの企業が抱える課題を解決する可能性がありますが、同時にデメリットや注意点もあります。
本コラムでは、製造業における倉庫作業の自動化について解説します。その方法やメリットについても触れるので、ぜひ参考にしてみてください。
目次
倉庫の自動化とは
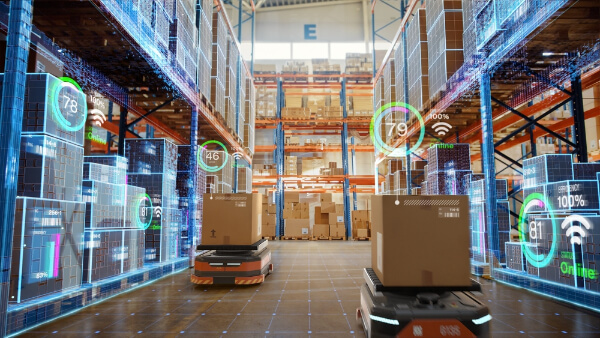
自動倉庫とはロボットなどの機械やITシステムを活用し、今まで人の手で行っていた倉庫内の作業を自動的に行えるようにしたものです。近年では、優れた倉庫管理システムや自動搬送装置が開発されており、物品の入庫・出庫までを機械化できるようになっています。
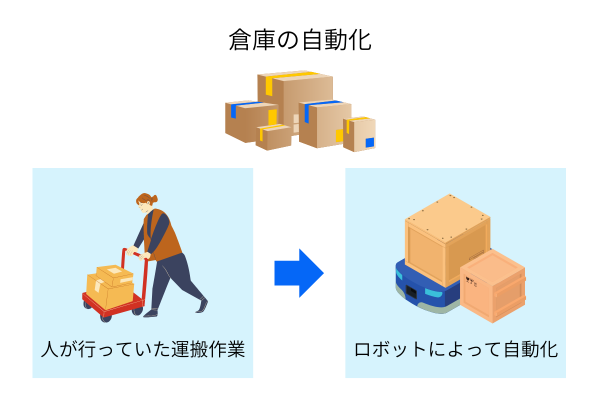
機械を導入することにより、物流業務の一部のプロセスを自動化するケースもあれば、全ての工程を自動化する場合もあります。自社に適した倉庫の自動化を実現することで、従来よりも作業効率が向上するでしょう。同時に、企業が抱える課題を解決できる可能性も十分にあり、物流業界だけでなく製造業でも注目されています。
製造業が倉庫を自動化するメリット
製造業が倉庫を自動化するメリットは多いです。ここでは、製造業の倉庫を自動化するメリットを具体的に紐解いてみましょう。
生産性の向上
今まで人が行っていた業務を機械・システムによって自動化することにより、作業効率は大幅に向上します。例えば、人が作業しなければならないとき、長時間の労働はできないため稼働時間に限界があり、業務量が多い場合はその分の人手を確保しなければなりません。
その点、機械やロボットを利用することにより、時間の制限なく稼働させることができます。そのため、作業員のシフト調整・休憩時間の確保といった作業も不要になります。また、人手を確保するための採用活動も必要ありません。
取り扱う商品の種類によっては冷蔵・冷凍倉庫があり、人では対応が難しい環境でもロボットであれば問題なく作業できます。
作業の品質の安定化
人が倉庫内の作業を行う場合、作業員の経験値やスキルによって業務の品質に差が生まれる可能性があります。例えば、新人とベテランの作業員を比較すると、同じ作業時間であっても作業量は変わってくるでしょう。これは作業の効率だけでなく、ミスが発生する割合にも違いがあります。
この対策には、徹底したルールの策定や研修などによる教育が必要であり、手間や時間がかかります。そこで倉庫内の作業を自動化させることにより、作業員による差が生まれにくくなります。
ヒューマンエラーを削減できる以外にも、人の出入り自体も減らせるため異物混入のリスクが減るメリットもあります。また、倉庫内の温度管理をしやすい点も作業の品質に影響するでしょう。
効率化・省力化・省人化によるコスト削減
倉庫内作業の自動化により、コストを大幅に削減できる可能性があります。コストは作業に対して発生する人件費だけでなく、人材確保のためにも費用がかかります。前述の通り、多くの製造業は人手不足を課題に挙げており、人材を募集しても確保するのが難しいのが現状です。
そこで、倉庫を自動化することにより、人の手による作業を機械に代替できるため、省人化を実現できます。人不足の課題を解決するだけでなく、人材確保や教育のコストなどの費用も大幅に削減できるでしょう。
自動倉庫を導入する際の注意点
製造業が倉庫の自動化を実現した場合、さまざまなメリットを得られますが、同時にデメリットもあります。導入を検討する際はメリットとデメリットのバランスを考える必要があるでしょう。ここでは、製造業が自動倉庫を導入する際の注意点を解説します。
初期導入コストが大きい
倉庫を自動化する方法にもよりますが、導入する際に大きなコストが発生します。導入の初期費用が高額であれば、企業にとって大きな負担になるでしょう。実際に汎用(はんよう)性の高いシステムであれば数千万円規模の投資が必要です。倉庫内の作業に大きな課題を抱えていても、企業の規模や経営状況によってはすぐに導入できない可能性があります。
また、設備を整えるためには時間がかかり、内容によっては既存の体制を一部縮小しなければならないケースもあるでしょう。直接的な費用だけでなく既存の生産体制に与える影響や、初期費用を回収するまでの期間も十分に考慮する必要があります。
メンテナンスなどランニングコストがかかる
自動倉庫を導入する際には、初期費用だけでなくメンテナンスなどの費用がかかります。ロボットや機械、システムを安定的に稼働させるためにはメンテナンスが必要であり、それを担当する人材を確保する必要があるケースも少なくありません。
そのため、作業員を減らすことはできても、新たにシステムの担当者が必要となるため、発生する人件費と削減できるコストを比較することも重要です。
システム障害が発生するリスク
倉庫の自動化を実現したときヒューマンエラーを減らしやすくなりますが、システムの場合も障害が発生するリスクがあります。軽微なエラーであれば業務に与える影響は小さいものの、大規模なシステム障害が発生した場合、生産全体がストップする可能性があるでしょう。
業務が停止した場合の損害は大きくなることが考えられ、適切な対応が必要です。また、システム障害以外にもロボットなどの機械にトラブルが発生する可能性もあります。このような事態にも適切に対応できるよう、マニュアルの作成やルールの共有などの作業も必要です。
従業員への研修の実施
倉庫関連の新しいシステムを導入する際、アプリケーションや機械の使い方・業務フローを作業員に共有する必要があります。そのため、従業員向けの研修の実施やマニュアルの作成などの手間がかかります。
また、新しい仕組みの場合、慣れるまでに時間がかかることもあるでしょう。このようなマニュアルやルールは、導入後に決めるのではなく、システムの選定段階から検討することが重要です。
新しい体制の構築要
倉庫を自動化した場合、今までの業務フローが大幅に変わります。そのため、新しい業務フローを作成し、人員の再配置を行う必要があるでしょう。場合によっては、組織の体制自体を見直す必要があります。
その一方で、大規模な組織の変革や業務フローの見直しは、通常の業務に大きな影響を与える可能性があるでしょう。そのため、通常の業務に支障が出ないように計画を立てて導入する必要があります。
製造業の倉庫を自動化するシステム
製造業の倉庫を自動化する手法はいくつかあります。それぞれ特徴が異なるため、導入においてはそのポイントを理解しておくとよいでしょう。ここでは、倉庫を自動化する手法について紹介します。
自動倉庫システム
自動倉庫システムとは、前出の通り倉庫作業の自動化に特化したシステムであり、コンピュータの制御によって入庫・保管・出庫という一連の流れを管理します。入庫・出庫の情報を一元管理できるだけでなく、さまざまな制御装置・ロボットと連携させることによって、移送プロセスも自動化します。
また、自動倉庫システムにはさまざまな種類があり、ラック・パレットを活用するものから、商品を保管している棚自体を動かせるものなどがあります。企業の倉庫の規模や扱う商品のサイズや種類によって適したシステムは変わってくるでしょう。
WMS(倉庫管理システム)
WMS(Warehouse Management System)は、倉庫管理システムのことです。入庫・出庫や在庫管理まで倉庫内業務の運用をシステム側で管理し、効率化を図ります。倉庫管理システムの中には、帳票やラベル作成・発行の機能も搭載されているものもあるため、物品の保管・管理以外にも、事務的な作業の効率化も図れます。
また、販売管理システムなどと連携することにより、リアルタイムに在庫の個数を把握したり、返品などが発生した場合でも対応しやすくなったりします。従来のアナログな管理と比較すると、より精度の高い管理体制を構築できます。前出の自動倉庫システムとは異なり、自動化よりも効率化に重点を置いているため、作業プロセスの一部が自動化します。
関連記事:WMS(倉庫管理システム)の導入メリット・デメリットとは?
自動ピッキングシステム
倉庫管理では一般的にピッキング作業が発生しますが、その作業を効率化・自動化するものが自動ピッキングシステムです。倉庫管理システムのような仕組みとロボット・機械を組み合わせることにより、人が行うピッキング業務を代替します。
現在では、一般的なピッキングシステムを使うケースが多く、ハンディターミナルなどのデジタル機器・デバイスを使ってバーコードを読み取り、自動的に個数を集計しリアルタイムに情報を管理できます。システムを使っていない場合は、紙などを使ったアナログな作業になるでしょう。
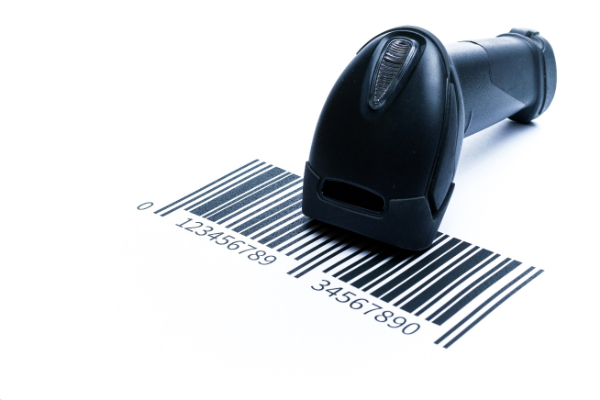
人がピッキングする際には、ハンディターミナルなどのリーダーを活用し、個数や状態を確認しながら商品をピックアップします。自動ピッキングシステムを活用し、自動倉庫システムや倉庫管理システムなどと連携させることで、ケース・パレット単位でピッキングできます。
このシステムを構築できると、人の代わりに機械がピッキングするため工数や人件費の削減が可能です。さらに、ピッキング作業の処理速度も上がるため、リードタイムの短縮にもつながるでしょう。精度が高いシステムであればヒューマンエラーなどのミスも防止できます。
デジタルアソートシステム(DAS)
DASとは、商品の仕分けを効率化するシステムです。種まきのように、単一の商品を複数の箱に入れていくため、DASの仕分けは「種まき式」と呼ばれています。
商品を読み取ると、投入すべき箱と個数をデジタル表示で教えてくれます。DASを活用すれば、入れ間違えなどの人的ミスの確率を大きく削減できます。また、投入すべき箱が一目でわかるようになり、作業効率が向上するでしょう。
ミスをリカバリーする回数が減るうえ、通常作業の効率が上がるため、結果的に作業時間を大幅に短縮できます。また、商品の読み取りや投入する箱の指示はDASが全て行うため、作業員は商品の情報を覚える必要がありません。そのため、作業員の能力にかかわらず、高品質な仕分けが可能です。
関連記事:デジタルアソートシステム(DAS)とは~物流を効率化~
デジタルピッキングシステム(DPS)
DPSは、作業員が集品箱を持ち、在庫から商品をピッキングするシステムです。作物を摘み取るように、異なる商品を集品箱にいれるため、DPSの仕分けは「摘み取り式」と呼ばれます。
仕入れ先を指定すると摘み取る商品のゲートが開き、商品の摘み取り個数を教えてくれます。DASと同様に、商品に対する知識がなくてもピッキングできるため、慣れていない作業員でも正しくピッキング可能です。また、ピッキングリストを用意する必要がなくなるため、ペーパーレス化を進めることができるうえ、リストを確認する手間を減らせるのです。
製造業の倉庫を自動化するロボット
製造業の倉庫を自動化するには、システムのほかにロボットも活用できます。ここでは、倉庫で活用されている2つのロボットを紹介します。
自動搬送ロボット(AGV・AMR・GTP)
自動搬送ロボットを活用することにより、倉庫内作業の一部を自動化できます。自動搬送ロボットは、原材料・仕掛品・商品の搬送をロボットが行うことにより、搬送作業を自動化する仕組みです。倉庫内の作業員に代わってロボットがピッキングを行うものもあり、大幅な工数の削減につながります。
自動搬送ロボットにはいくつか種類があり、倉庫の床面に誘導体を設置することによりロボットが移動できるAGV(Automatic Guided Vehicle)や、誘導体がなくてもロボットが走行し搬送できるAMR(Autonomous Mobile Robot)などがあります。また、棚ごとに商品を搬送できるGTP(Goods To Person)もあり、それぞれ特徴が異なります。
現在は、物流業界を中心に急速に導入され始めており、無人で商品を搬送できます。このことから、倉庫の一部を無人化することも可能です。高度なシステム・仕組みであればAIを活用して制御することにより、高い精度を実現できるでしょう。
関連記事:AGV(無人搬送車)はどこまで進化した?基礎知識や導入メリット、最新機能
パレタイジングロボット
パレタイジングロボットとは、アームで商品の積み上げや積み下ろしをするロボットです。倉庫の作業を無人で行うには、システム間の運搬も自動化しなくてはなりません。パレタイジングロボットは、段ボールや商品を整理してパレットに積み上げ、次の工程に運搬できるようにします。
パレタイジングロボットの中には数百キロもの重量に対応している機種もあるため、そもそも人手での積み上げや積み下ろしが困難な商品も取り扱えます。自動化が実現するだけでなく、作業員の負担軽減や労働環境の改善にも役立つでしょう。
製造業での物流業務とは
製造業では、調達した原材料や資材を保管し仕掛品を移動させ、全ての工程が終えた完成品も出荷まで保管しなければなりません。そのため、原材料や商品を含む物品の搬送・保管・仕分け・ピッキング・積み込み・荷下ろしといった物流業務が発生します。
とくに製造業は、これらの作業が単体で発生するわけではなく、生産プロセスに組み合わさった状態で発生します。
また、製造業にとって商品を生産するプロセスは企業にとって利益になるものの、物流業務はコストとして扱われる側面が強いのも実情です。そのため、物流業務は機械化・自動化・省力化を実現することでメリットを感じる企業は多いでしょう。
他にも、物流に関わる作業コストや手間、時間を削減することにより、企業として商品の品質や付加価値を生み出す業務に注力できます。近年では、ロボットの活用など効率化を図るための技術が発展しており、以前よりも実現しやすくなっているでしょう。
製造業が倉庫を自動化する必要性
製造業では倉庫の自動化が進んでいますが、それは製造業がさまざまな課題を抱えているためです。ここでは、製造業が抱える課題とともに倉庫を自動化する必要性について解説します。
労働力の減少・人材不足
現在、日本国内は深刻な少子高齢化により人口が減少傾向にあります。その影響は製造業にもあり、多くの企業にとって人材不足が課題となっています。経済産業省の資料である『デジタル技術の進展とものづくり人材育成の方向性』によると、人手不足を経営課題に挙げている大企業は41.9%、中小企業では42.2%に上っています。
実際に、製造業では品質が良い商品を生産できる設備をそろえていても、生産ラインをひとつなぎにしなければ業務は滞ってしまいます。各プロセスとプロセスの間、設備と設備の間での原材料・仕掛品の受け渡しといった作業が発生しますが、人手が不足していることから課題が大きくなっているでしょう。
他にも、生産量を増やすために新しい設備やラインの増強を行いたくても、人手不足により頓挫するケースもあります。
人手不足の解決には代替する技術の導入が求められています。少ない人手で適切に業務を回せるように、省力化・省人化を図る必要があるでしょう。製造業における物流業務は自動化を実現しやすいことから、必要性を感じる企業が増えています。
原材料や人件費などのコストの高騰
近年では、製造業全体で原材料や人件費などが高騰していることから、業務の効率化によるコスト削減を実現する必要があります。とくに、物流業務は肉体的な負担が大きいことから、人件費は高くなりやすい傾向です。
そこで、物流業務を自動化・効率化することにより、人手不足を解消しつつコストを抑えられるため多くの製造業で注目されています。
世界的な競争の激化
現代では、輸送技術の発展とコストの低下により、市場に国外の商品が多く流通するようになっています。先ほどの国内の人口減少に伴い、海外に進出する製造業が増えていることから、競争相手が世界規模に広がっています。
その中で、国内の製造業の競争力を高めるためには、コストの削減や効率化に伴う迅速な供給体制の構築が求められています。
製造業の倉庫を自動化するためのポイント
多くの場合、システムやロボットを導入して倉庫を自動化しますが、抱えている課題や目的によって最適なシステムや取るべき施策は異なります。倉庫の作業を効果的に自動化するために、以下の4つのポイントを押さえましょう。
- 自社の課題と導入目的を明確にする
- デジタルリテラシーの高い人材を配置する
- 機器のサポート体制を確認・整備する
- 課題や効果を検証する
自社の課題と導入目的を明確にする
まず、自社に最適なシステムを選ぶために、自社の課題と導入の目的を明確にしましょう。課題と目的から逆算して要件を定義すれば、選ぶべきシステムやロボットは自ずと明確になります。逆に、自社の課題や目的が明確にならなければ、システムを選ぶ基準があいまいになり、課題の解決に至らない事態に陥るでしょう。
また、徐々に自動化を進める場合には現場の声を聞くことも重要です。経営陣が自動化や省力化に役立つと考えているシステムの導入は、現場からするとかえって負担の増える仕組みを作り出してしまうかもしれません。社内全体の課題と目的を明確にすることで、倉庫の自動化が効率的に進みます。
デジタルリテラシーの高い人材を配置する
自動化を進めるにはデジタル化が欠かせないことから、システムを十分に使いこなせるデジタルリテラシーの高い人材が必要です。そうした人材がいない場合、システムを十分に活かしきれず、自動化が進まない場合があります。
まずは、研修を実施したり専門家のアドバイスを受けたりして、システムを有効活用できる体制を整えましょう。
機器のサポート体制を確認・整備する
システムやロボットを正しく利用していても、予期せぬ不良が起きることがあります。損失を可能な限り抑えるためにも、機器のサポート体制を事前に確認し、トラブル発生時の動きをあらかじめ明確にしておきましょう。
システムを長期間使い続ける場合は、サポート期間が過ぎた後に取る対応も明確にしなければなりません。トラブルに対応できる作業員が社内にいない場合、相談する企業や窓口をあらかじめピックアップしておくとよいでしょう。
課題や効果を検証する
自動化の効果を高めるためには、システム導入後の効果測定をする必要があります。事前に定めた目的や課題を達成・解決できているかを検証することで、より効果的な自動化の施策を見つけられるかもしれません。
今後の施策に活かせるよう、システムの導入で満足するのではなく、課題や効果の検証を忘れずに行うようにしましょう。
製造業における倉庫の自動化
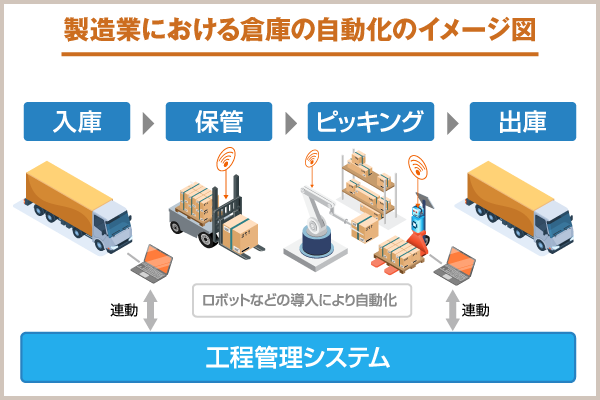
製造業では商品を安定的に供給するための仕組み・体制を整える必要があります。そこで自動倉庫システムを導入することにより、プロセスを自動化することで現場の作業員の稼働時間や、生産のリードタイムの短縮につながります。その結果として、タイムリーで安定した商品の供給を実現できるでしょう。
他にも、倉庫内作業の自動化を実現するシステムと、現場の端末・工程管理システムなどと連動することにより、生産プロセスの進捗管理も効率化できます。さらに、製造業の中には工場内の作業を完全自動化するフルオートメーションを実現している企業もあります。
この生産設備では、無人で製造できる環境であり、24時間態勢でロボットなどの機械が稼働し生産を続けます。このように完全自動化を実現する製造業の事例はまだ少ないものの、自動搬送ロボットを導入することによって省人化・効率化を実現している企業は増えています。
倉庫自動化の事例
ここからは、実際に倉庫の自動化を図った4社の事例を紹介します。自社の倉庫に活かせる点がないかを確認してみてください。
1.Amazon
倉庫の自動化を実現した代表的な事例は、Amazonの物流倉庫です。Amazonはロボットメーカーを買収しており、自社用に倉庫内作業を行うロボットを開発しています。この自動搬送ロボットは、作業スタッフが目的の商品を選択すると、該当する商品をスタッフに搬送してくれるというものです。
この体制では、人が倉庫内を移動する必要がなくなるため、最小限の移動スペースの確保で済み倉庫を広く利用できます。さらに、作業スタッフは移動することがないため、業務の負担が大幅に削減し、ヒューマンエラーの低減にもつながっています。
2.アスクル
アスクルは、多種多様な組み合わせの商品を当日・翌日配送する通信販売事業を営む企業です。同社は、多くの製品を迅速に配送するため、倉庫のデジタル化を推進しています。
例えば、AIを搭載したデパレタイジングロボットやAGVを活用して、倉庫の高度な自動化を実現しています。移動には1,000キロまで対応可能なAGVを活用し、作業員の負担を軽減しながら作業効率を向上しています。
3.IKEA
IKEAは、スウェーデン発祥の家具販売会社です。同社は、店舗でもある「IKEA Tokyo-Bay倉庫」を自動化し、配送のピックアップ作業を効率化しました。その結果、作業員がピックアップする従来の方式と比べて、作業効率が8倍に向上しました。
これにより、作業員の倉庫内作業が減少し、従業員の体への負担が軽減しています。また、倉庫での作業時間が減少したため、顧客へのサポートに充てられる時間が長くなっていると言います。
4. 佐川グローバルロジスティクス
佐川グローバルロジスティクスは、日本全国に拠点を置く物流会社です。同社は、RFIDと仕分けシステムを活用することにより、倉庫内作業の生産性を向上しました。
例えば、RFIDを用いることにより、瞬時に検品できるような仕組みにしました。また、仕分けシステムを導入して、頻繁な移動が必要だった仕分け作業を、ロボットを活用して自動化したのです。
業務フローの見直しが必要になることも
倉庫の自動化を実現すると、製造業や物流業で発生している課題を解決できる可能性があり、業務効率を大幅に高められるでしょう。ただし、倉庫の自動化を実現する方法は複数あり、それぞれ特徴や発生するコストも異なります。そのため、導入する際は自社に適したものを選ぶ必要があるでしょう。
他にも、業務フローの見直しが必要になるなどの注意点があるため、メリットとデメリットのバランスを考え、導入を決めることが大切です。
(提供:Koto Online)