近年、製造業を取り巻く環境は消費者のニーズの多様化、製品ライフサイクルの短縮化など大きく変化しています。「少量の品種を大量生産」「多品種少量生産」そして「多品種大量生産」など、さまざまな顧客や市場のニーズに合わせつつ売上を高め、企業の発展を支える新しい生産方式を企業は必要としています。
トヨタ自動車の生産方式が起源とされるリーン生産方式は、「無駄」を徹底的に排除することで高品質な製品を短納期・低コストで生産することを可能にする生産管理手法です。この記事ではリーン生産方式の基本的な考え方と仕組み、トヨタ生産方式との違い、導入のメリットとデメリットについて、わかりやすく解説します。
リーン生産方式とは|概要
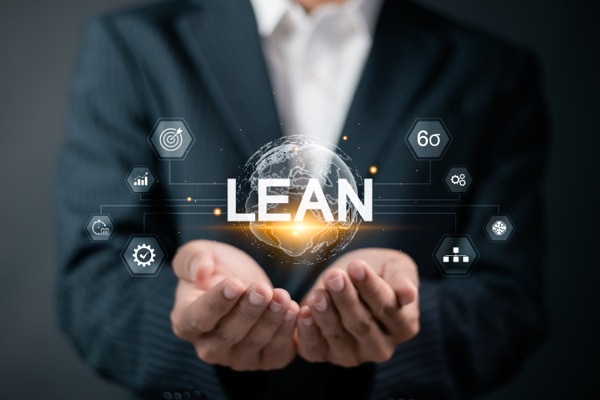
はじめに、リーン生産方式とは何か、その特徴や歴史を解説します。
リーン生産方式とは
リーン生産方式とは、日本のトヨタ自動車が発展させ、実践している生産方式を基に研究・整理・一般化された生産管理手法を指します。
「ジャスト・イン・タイム(必要な物を、必要なときに、必要なだけ生産する考え方)」や「カンバン方式(別名後工程引き取り生産。かんばんと呼ばれる伝票を用いて仕掛品を最小化して過剰生産を抑え、生産コストを管理、削減する手法)」を中心に、生産工程の「ムダ」を徹底的に排除することで、多品種大量生産、かつ短納期・高品質・低コストを効率的に実現する生産方式です。
「リーン(lean)」とは、英語で「体が引き締まった、ぜい肉のない」という意味の形容詞です。ここから転じて「無駄のない、効率的な」という意味でリーン生産方式と名づけられました。
リーン生産方式はこのように、もともとは製造業から発展した理論ですが、「普遍的な五つの原則を守り応用することで、生産だけでなく流通、医療、教育などさまざまな業界のマネジメントに適用可能である」と、最初の提唱者であるクラフチック(後述)は述べています。
現在はその言葉どおり、製造業だけでなくサービス業やソフトウエア開発なども含め、さまざまな分野で応用されています。
リーン生産方式の歴史
リーン生産方式は、日本の自動車メーカーであるトヨタ自動車が実践していた「トヨタ生産方式(TPS:Toyota Production System)」、同じくトヨタの「5S(「整理」「整頓」「清掃」「清潔」+「躾」)、「カイゼン」などについて実態研究を行い、収集されたデータを基にして体系化・モデル化された理論です。
この理論にある"lean"という言葉を最初に(1988年)論文("Triumph of the Lean Production System")で用いたのは、アメリカ、マサチューセッツ工科大学(MIT)スローン経営大学院に当時在籍していたジョン・クラフチック(John F. Krafcik)と考えられます。その後、同じMITスローン経営大学院の研究者ジェームズ・P・ウォマックらが研究を行い、1990年に「リーン生産方式」として発表したことから世界に広がっていきます。
TPSは日本式の生産方式として結果を出していましたが、リーン生産方式はそれを理論立てて整理し体系化、一般化したことに意義があります。現在、海外ではリーン生産方式専門のコンサルタントも存在し、パッケージ化されていることから、企業が業務改善を考える際に導入しやすくなっているといえます。
現在は、「リーンマネジメント」「リーンプロジェクト管理」などリーン生産方式を応用したさまざまなマネジメント手法が発展しています。
リーン生産方式における5つの原則と具体的な改善の手順
クラフチックが発見し、それを体系化し発表したWomack and Jonesの著作には、「リーンの5つの原則」が示されています。
【リーンの5つの原則】
1 Specify Value:最終顧客の視点から価値を定義する
(出典)
2 Identify the Value Stream:価値の流れを定義する(価値をもたらさないステップ(ムダ)の全てをなくす)
3 Flow:流れ(フロー)を作り出す
4 Pull:顧客から上流工程へと価値の流れを動かす(プル方式)
5 Pursue Perfection:ムダのない完全な価値を作り出す完璧な状態になるまで続ける
原著:
"The Machine That Changed the World" by James (Jim) Womack, PhD, Dan Jones and Daniel Roos
日本語訳引用元:「リーン生産方式と学校における組織マネジメントを取り入れた改善活動について」宮久保雅行,奈良県教育研究所
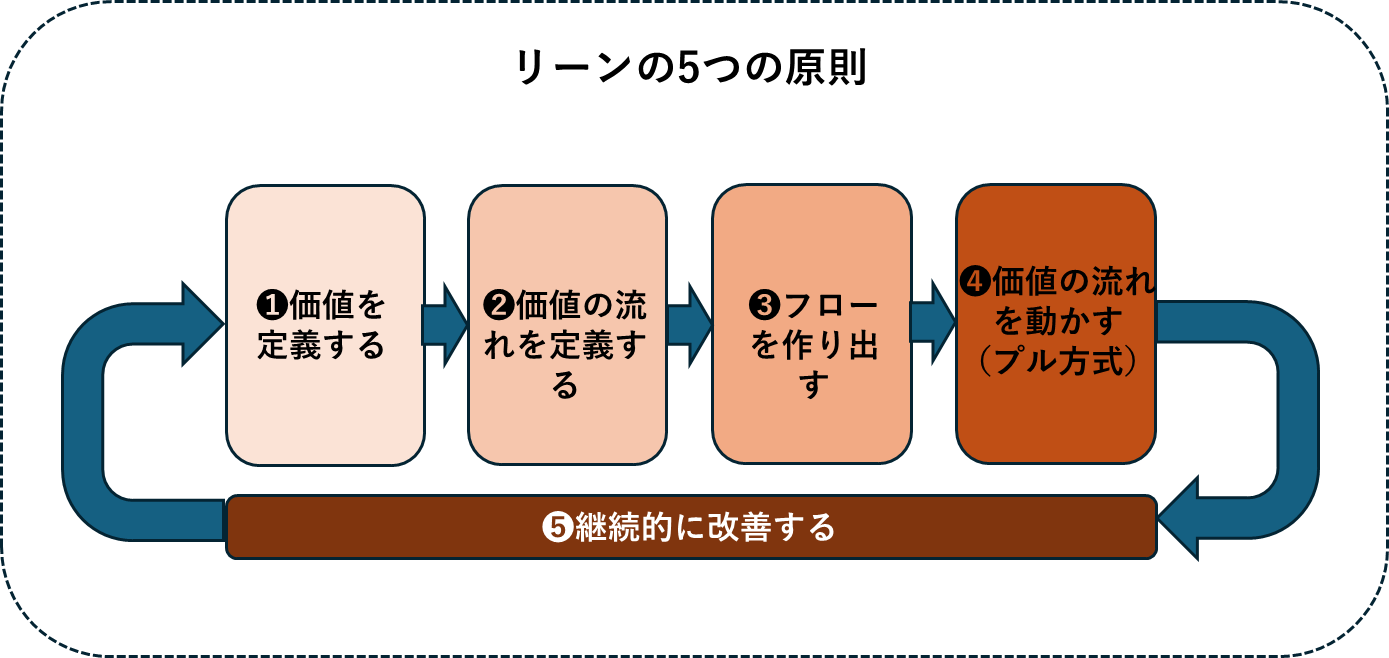
1.価値を定義する
リーン生産方式(あるいはリーンマネジメントやリーンプロジェクト管理)において、最初に製品の価値を特定させます。この場合の製品の価値とは、「顧客のニーズを満たすことができるものかどうか」です。
2.価値の流れを定義する
バリューストリームマッピング(VSM)と呼ばれます。これは、製造にかかわるあらゆる「無駄」をなくし、効率を最大化することを目指すものです。リーン生産方式の最も重要なポイントとなります。
3.フローを作り出す
前段階で見つかった無駄をなくし、最も効率的なフローを作成します。
4.価値の流れを動かす(プル方式)
「プル方式」とは、「ジャスト・イン・タイム」から発展した考え方、手法です。前段階から効率よく後の工程に仕事を引き継ぐ(引っ張る=pull)ための仕組みです。ワークフローを、止めることなく効率的に動かし続けます。
5.継続的に改善する
ここまでの流れを俯瞰し、問題点がないか、問題があった場合はどのように改善するかを考え、実行します。トヨタの原点でありリーンの目指すものである「改善を繰り返し、より完璧にする」ポイントにです。
1~5までを繰り返し、よりブラッシュアップしていきます。
リーン生産方式とトヨタ生産方式との類似点・違い
リーン生産方式は、トヨタ生産方式の理念や手法をベースにして開発されたため、基本的な部分の内容は同じといえます。
この方式の特徴は、「無駄」を徹底的に排除することにあります。無駄とは、生産過程における「価値を生まない」動きや時間、在庫などを指します。
リーン生産方式における「無駄」も、トヨタ生産方式と同じく以下の7つ(トヨタ生産方式では「飾って豆腐」と頭文字をとって呼ばれている)になります。
- 加工の無駄
- 在庫の無駄
- 作りすぎの無駄
- 手持ち無沙汰の無駄
- 動作の無駄
- 運搬の無駄
- 不良を作る無駄
また、生産プロセスを徹底して管理し効率化することによって、品質を維持しながら無駄をなくすために「かんばん方式」をとることも同様の特徴です。「かんばん」とは、部品ごとにつけられた部品情報+作業指示書を指します。
具体的には、後工程で部品箱を一つ取り出した際に、その部品箱についていた「かんばん」を外し、前工程(部品メーカーや在庫管理部署)に戻します。部品がなくなりました、というサインが部品を供給する箇所に「かんばん」の数だけ届くため、「かんばん」分の部品を新たに供給できるという仕組みです。
この仕組みは、トヨタ生産方式・リーン生産方式を支える「ジャスト・イン・タイム」、つまり「必要なものを、必要なときに、必要な分だけ」の生産が可能になる手助けとなります。
またTPSの2本の柱のもう一つである「にんべんのついた自働化」(故障があれば機械が自動で止まり、不良品が生産されなくなる仕組み)も含まれます。
その他、「3M(ムダ・ムラ・ムリ)」「なぜなぜ分析」「カイゼン」などの業務効率化のための手法も体系化されて取り入れられています。
ただし、かんばん方式については、不良品が出ないことを前提にしていることから、全ての生産工程やマネジメント、管理手法に適しているというわけではありません。
(参考)
トヨタ生産方式
"トヨタ生産方式" 豊田章男の解釈
【関連記事】
7つのムダとは?トヨタの生産方式が指摘する「ムダ」と具体的な排除方法
リーン生産方式を導入するメリットとデメリット(注意点)
リーン生産方式のメリットは、前述してきたとおり生産工程における徹底した無駄の排除と効率化にあります。それに加え、こちらも前述したように、リーン生産方式はパッケージ化されているため企業への導入がしやすくなっています。コンサルティング業にも商品として用意されていたり、大学の学部の単位にもなっていたりと、海外ではトヨタ生産方式よりも一般的です。現在はさまざまな業種に応用されており、研究もさらに進んでいます。
一方でリーン生産方式は、「ジャスト・イン・タイム(JIT)」をその中心に置いていることが、メリットでありつつもデメリットになることがあります。たとえば生産ラインがなんらかの問題で止まってしまうと、そこでフローが止まってしまい、かんばん方式もつながらなくなります。結果的に製品や部品の欠品が発生することになってしまいます。これは、トヨタの「にんべんのついた自働化」が高精度で稼働していることが前提になっているためで、問題が起こりやすい現場では理論通りの結果が出せないことになります。
これらのデメリットを解決するには、現場作業員への教育によって、リーン生産方式の理念への理解度を深めてもらうことが重要になってきます。またトラブルが起きた際、そこで手待ち時間になっても何もしないで待つのではなく、自ら考えて問題解決に動けるような意識改善も重要です。
まとめ
この記事ではリーン生産方式について解説しました。
リーン生産方式は、トヨタ生産方式をベースに体系化・一般化された管理手法で、無駄を徹底的に排除することで短納期・高品質・低コストを実現する生産方式です。顧客満足度の向上、コスト削減、リードタイムの短縮など、さまざまなメリットを得ることができます。
またパッケージ化されているため導入がしやすく、コンサルティングを依頼した場合は企業の特性に合わせてカスタマイズして提供することも可能になっています。そのため海外では、TPSよりもよく知られており、活用されています。リーン生産方式は現在、製造業だけでなく、さまざまな業種で導入されています。業務効率の改善方法の一つとして、参考にしてみてはいかがでしょうか。
(参考資料)
「リーン生産方式の比較分析に関する試論的ノート ―自動車ボディ・バッファー管理の事例―」,藤本 隆宏, 東京大学大学院経済学研究科,赤門マネジメント・レビュー 1巻9号(2002年12月)
TOYOTA:「トヨタ生産方式」
鳥取県:「なぜ、今、トヨタ方式か?」
(提供:Koto Online)