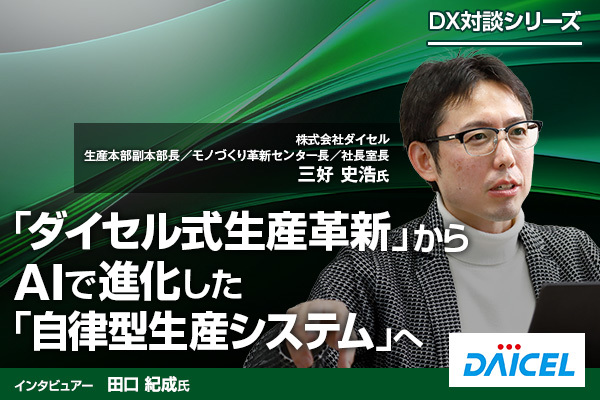
2000年に誕生し、モノづくり業界において生産手法を抜本的に変えた成功事例として知られる「ダイセル式生産革新」は、現在でも多くの企業が学ぶ、色褪せない優れた手法です。
DXの潮流のなか業種問わずさまざまな企業が業務プロセスの変革に挑む現在、「ダイセル式生産革新」は改めて高い注目を集めていますが、株式会社ダイセルは現在さらなる生産性向上を求めて「自律型生産システム」を実行しています。
「ものづくりDXのプロが聞く」は、Koto Online編集長の田口 紀成氏が、製造業DXの最前線を各企業にインタビューするシリーズです。今回は、株式会社ダイセルのモノづくり革新センター長であり、「自律型生産システム」を主導した三好 史浩氏にお話を伺いました。
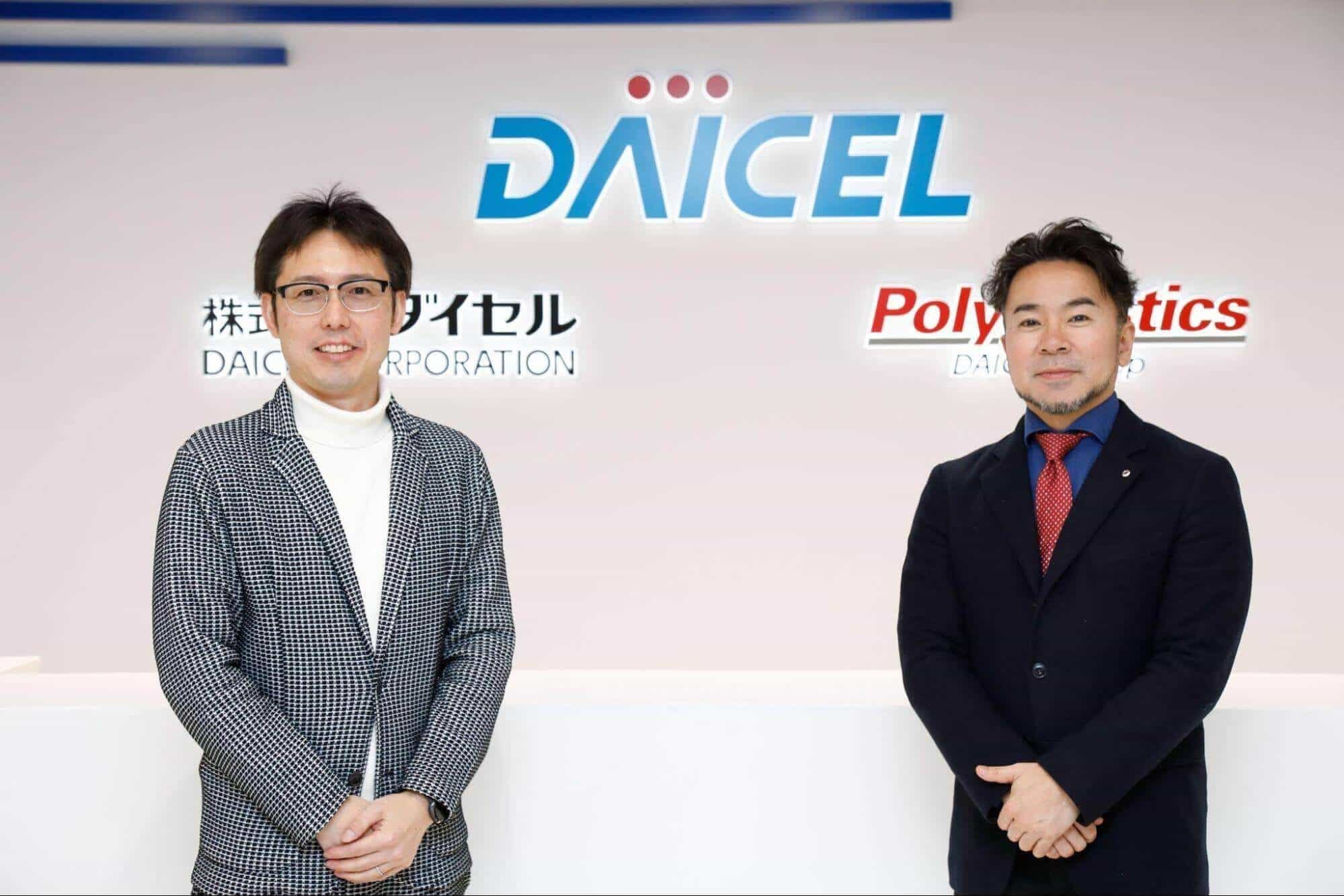
2007年に株式会社ダイセルに入社。入社後、播磨工場、新井工場など現場での生産革新に取り組む。2017年から次世代型生産システム構築プロジェクトリーダーに就任。3年でコンセプト、設計、開発、オフライン検証をおこない、2020年に同社網干工場でのオンライン実証テストを実施。2021年にモノづくり革新センターの設立に伴い、現職。
2002年、株式会社インクス入社。3D CAD/CAMシステム、自律型エージェントシステムの開発などに従事。
2009年に株式会社コアコンセプト・テクノロジー(CCT)の設立メンバーとして参画後、IoT/AIプラットフォーム「Orizuru」の企画・開発等、DXに関して幅広い開発業務を牽引。2014年より理化学研究所客員研究員に就任、有機ELデバイスの製造システムの開発及び金属加工のIoTについて研究を開始。2015年にCCT取締役CTOに就任。先端システムの企画・開発に従事しつつ、デジタルマーケティング組織の管掌を行う。
2023年にKoto Onlineを立ち上げ編集長に就任。現在は製造業界におけるスマートファクトリー化・エネルギー化を支援する一方で、モノづくりDXにおける日本の社会課題に対して情報価値の提供でアプローチすべくエバンジェリスト活動を開始している。
目次
ダイセル式生産革新は企業特有の「壁」を壊すことがスタート
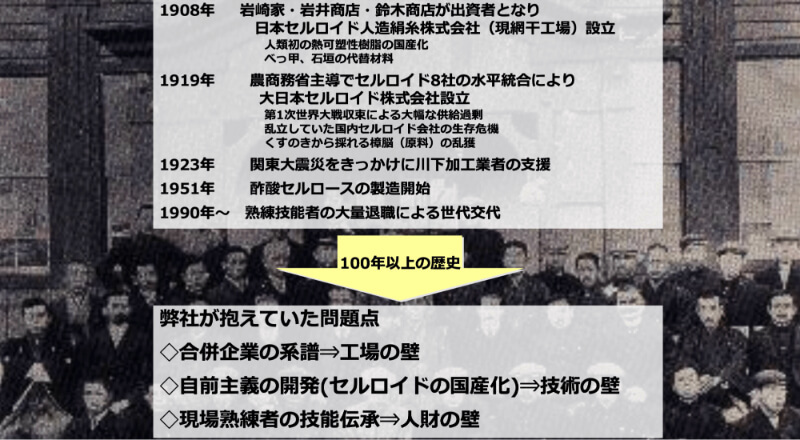
――まずは御社の事業の概要や企業風土などについてお聞かせください。
三好氏(以下、敬称略) 「ダイセル式生産革新」やDXの取り組みをお話しする前に、当社の成り立ちを話した方がご理解いただけると思います。株式会社ダイセルは、明治末期の1919年 に財閥系のセルロイド企業を中心に8社の企業合併でできた会社で、当時は大日本セルロイド株式会社という社名でした。
セルロイドは世界初の人造プラスチック材料で、熱可塑性樹脂というプラスチックを国産化する最初のネタでしたので、国を挙げて産業の発展に寄与してきました。セルロイドは眼鏡のフレームやボールペンなど、 当時はさまざまな生活用品に使用され、欠かすことのできない素材でした。
しかし、セルロイドは燃えやすい性質があり、大きな課題でした。セルロイドに変わる不燃化プラスチックとして開発されたのが酢酸セルロースです。現在でも酢酸セルロースは、液晶ディスプレイの保護フィルムなどさまざまなものに使われています。
当時の大日本セルロイドの写真フィルムの部門が分社化したのが、富士写真フイルム株式会社(現在は富士フイルムホールディングス株式会社)です。
ダイセルは歴史のある会社ですが、そもそも合併企業です。現在、グループ企業が75社、工場が7つありますが、三井系、三菱系などそれぞれの系譜は異なります。つまり、同じ会社であっても壁があり、労働組合も工場毎に個別交渉しており、単一化までに60年ぐらい続いていました。
またセルロイドは、日本で初めて国産化したので、当時最先端の技術が集まっていました。当社は新たな素材の提供のみならず、川下の加工に関しても支援をおこなうことで日本のものづくりをおこなうサプライチェーン構築にも寄与したことが社史におさめられています。自分たちで立ち上げ、切り開いてきたからこそ、自前主義の考えや多くの技術者、熟練の技術者を抱えることになり、歴史的にもこうした問題に直面することになりました。
1990年代に入りまして、現在の社長の小河が当時30代で課長の時にモノづくりの現場にいたのですが、従来からずっと続くこれらの壁に問題意識を持っており、それが一つのきっかけとなって考案されたのが「ダイセル式生産革新」と聞いております。
その背景には、いわゆる効率化だけではなく、企業の成り立ちから存在する組織、技術、人財の壁をぶち壊す取り組みでもあったのです。
田口氏(以下、敬称略) 「ダイセルレポート」でも2000年頃に初めて「ダイセル式生産革新」という言葉が出てきます
三好 兵庫県姫路の網干工場に統合生産センターがつくられた2000年で、そこでは、東京ドーム20個分ぐらいの敷地に建設されたプラントをこの1か所で集中コントロールし、全てのプラントを20名の要員で運転しています。
生産革新以前の生産の運営はモノの形態に合わせた単位になっていましたが、当時の先輩方は本来のモノづくりの繋がりから運営形態をサプライチェーンで括り直しました。ただ、括り直してもプラントの位置を簡単に移動することはできないので、当時急速に進むデジタル技術を活用してあたかも隣に並んでいるかのように見せて実現してきたと理解しています。
例えば、モノづくりの上流側は気体・液体形態が多く、下流に行くにつれ固体になります。つまり、上流と下流で別の組織運営がされていましたので、上流工程でトラブルが起こると、下流にも悪い影響が出るため、その結果、上下の工程間で仲が悪かったと聞いています。
仲が悪い弊害は、情報断絶を招き、信用がなくなると上下工程でトラブルがあっても影響を受けなくするために在庫を持つなどの力学が作用することです。モノづくりの過程で生じるこのような無駄をデジタルの活用によりバーチャルで統合運営をしているというようなことになります。
田口 2000年当時としては、かなり革新的な手法です。
三好 また、バーチャルファクトリーは、広島県の大竹市と兵庫県の姫路市の工場のデータを連結させてエネルギーの最適化計算をしています。各工場でエネルギーのボイラーやタービンの構成が異なるため、需要からどのような構成で運転したらいいかを選択しています。デジタル化と言えばそれまでですが、目的は縦割りから横割りへと運営を変えていくことで、そのためにデータ基盤を構築して連携しています。
ダイセル式生産革新は0段階の予備調査が重要
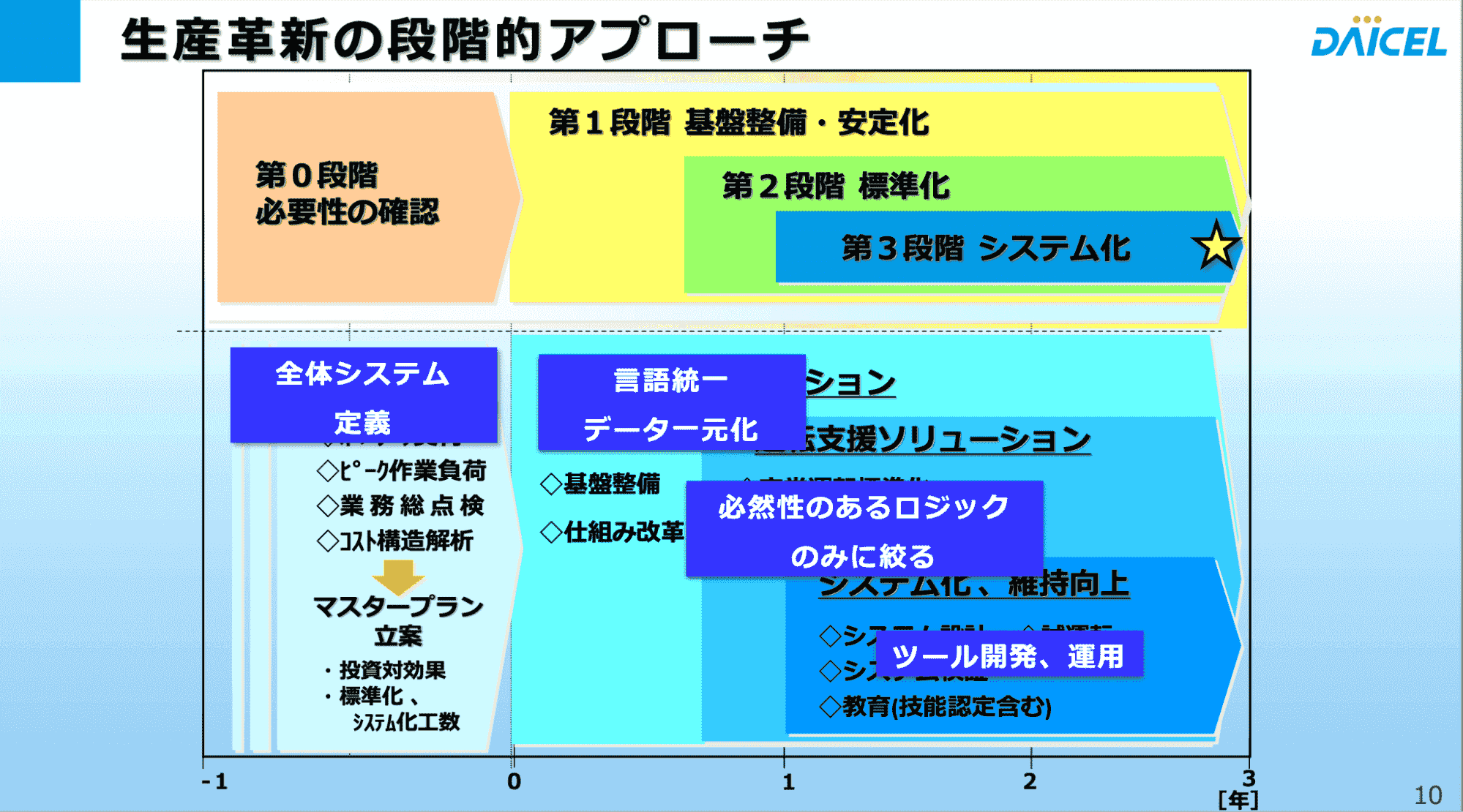
――ダイセル式生産革新は具体的にどのようなステップで進めていったのでしょうか。
三好 ダイセル式生産革新は現社長の小河が作り上げた手法で、予備調査→基盤整備・安定化→標準化→システム化の順で進めてこられました。2000年の網干工場(姫路市)を皮切りに、社内各工場、他社への展開を進められました。私は二世代下に入社しましたので、先輩が作り、実行してきたことを勉強し、それを進化させる形で推進する立場で関わってきました。最近のAIブームの流れで業務を標準化し、システム化する会社が多くみられますが、成功の鍵はむしろ、その前の予備調査と基盤整備・安定化にあると思います。
まず、改革に着手する前に予備調査の段階(第0段階)で勝てる戦いにする必要があったと聞いています。生産革新は既存の生産プロセス、設備を一旦肯定し、運転方法、運用の見直しなど現場改善で成果を出す手法です。改善に労力を費やしても競合に勝てないのであれば、大型投資により生産プロセスそのものを革新的に変える、あるいは事業の継続そのものを判断する必要があり、経営層の意思決定が必要であったからだといいます。そのため現状の実態や課題を現場作業の実態や製品のコスト構造など多角的な視点からどこにボトルネックがあるかを把握し、勝つためのマスタープランを作ることがこの段階です。例えばデジタル化でも、デジタルツールを入れるためにどういうワークフローにするかなどの議論はよくあると思います。我々は順番が逆で、予備調査の段階で最終的な働き方を全部設計し、あくまでも手段としてデジタルを活用して実現するという流れです。
――予備調査はどのように進めたのですか?
三好 予備調査のひとつの業務総点検を紹介します。縦軸に人、横軸にモノづくりの工程、斜め軸に機能を設定して、原料が工場に入荷してから出荷までの業務を洗い出します。そして誰がどんな意思決定をして業務が回っているのかを可視化します。
具体的にはワークショップの形式で聞き役、聞かれ役を決めてヒアリングしていきます。例えば、現場の方に具体的トラブルを想定してどのように発見しますか、といったことを聞きます。そこから何を判断して誰に連絡するのかと質問をして矢印で繋げていくんですね。そうすると、縦軸に課長、部長、工場長などが登場します。
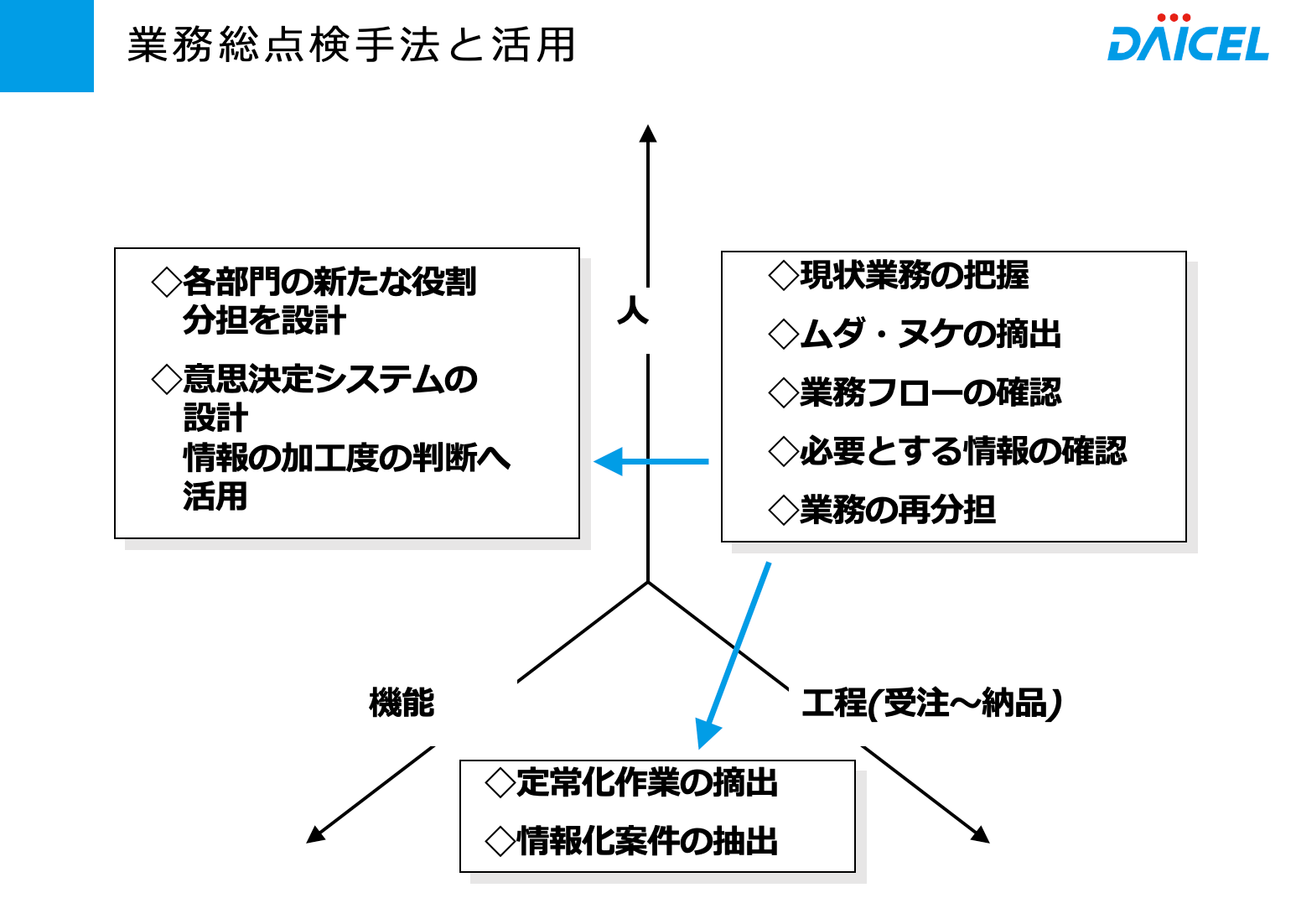
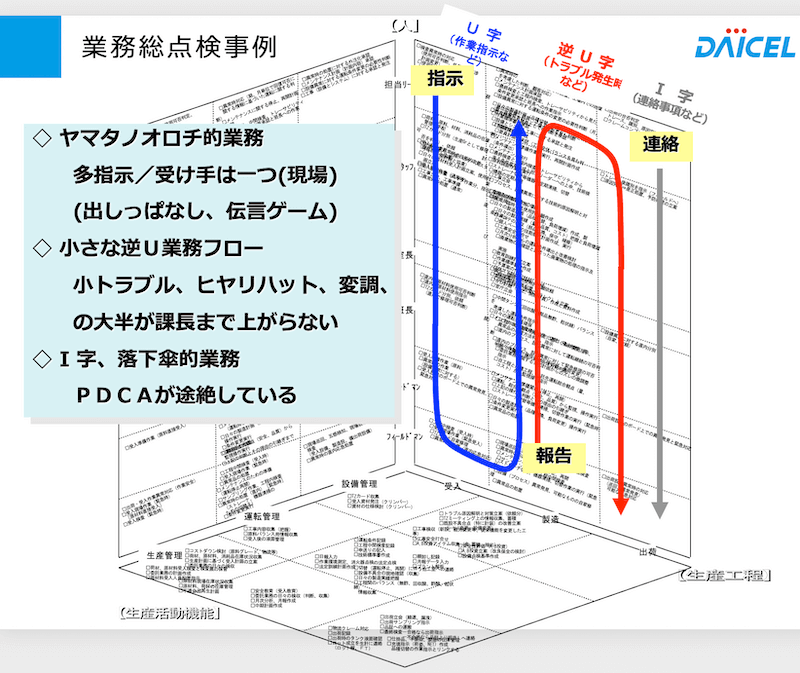
ヒアリングでこのU字、逆字、I字フローが見えてきて、さまざまな無駄が見えてきます。
このヒアリングの中で、当たり前と思ってしていることが、情報を収集している行為、あるいは保管、加工、判断、調整、実行などと各階層で何をしているのかを明らかにし、どこまで人がやり、どこから機械に任せるのかを決めます。その後、機械に任せる業務は、工程と機能の象限に書き出し、情報化投資案件として整理します。
田口 手法は非常に納得度が高いですが、プロのコンサルタントが入って進めたような印象ですね。
三好 実際に2000年以降、現在に至るまで他社さんからの見学も継続的にあり、小河は他社へもコンサルタントとして指導してまいりました。我々はコンサルタントを生業にしたいわけではないのですが、大きな規模の利益につながっています。
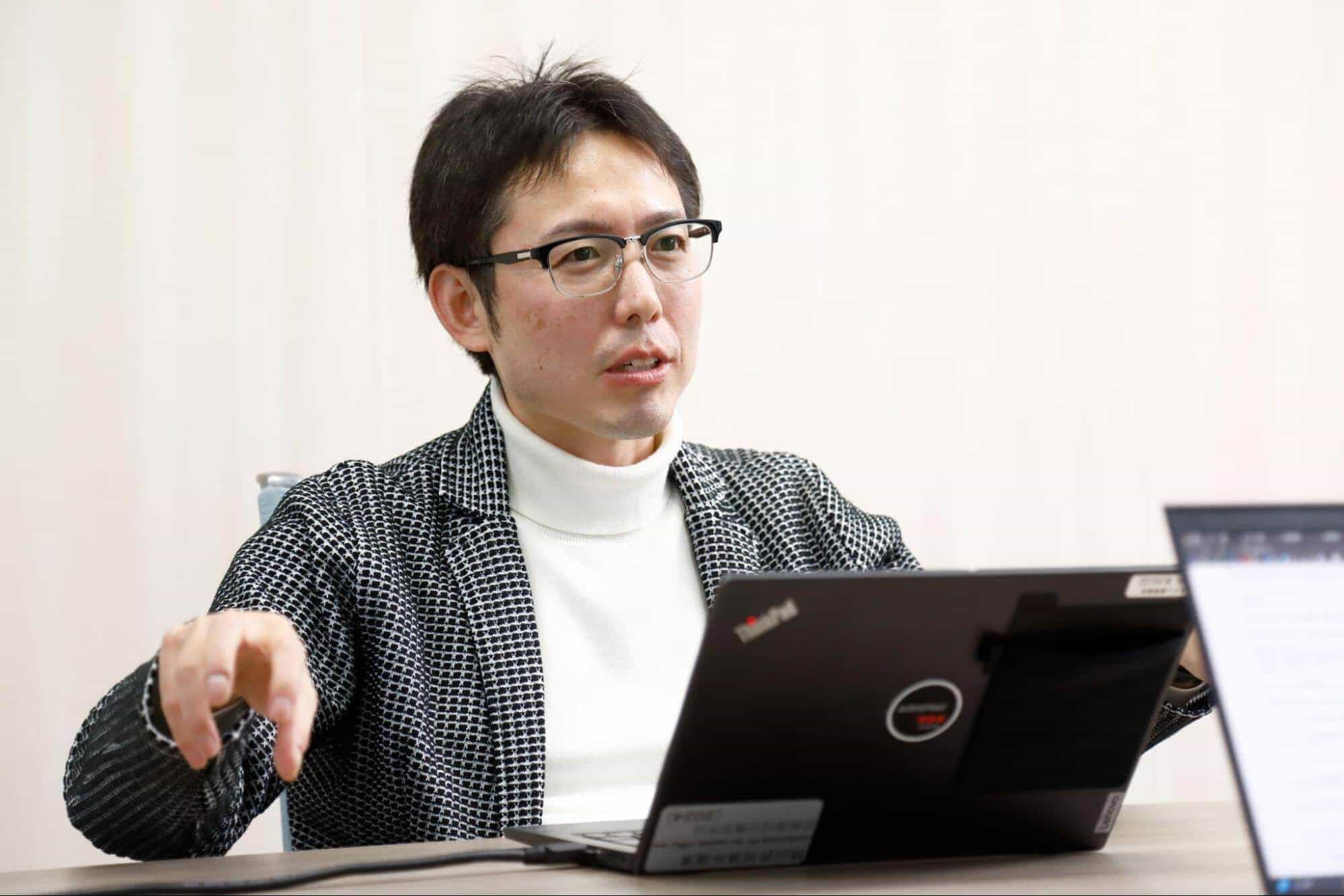
暗黙知を形式知にして標準化を目指し、さらにその先へ
――予備調査後は、どのように進めていくのでしょうか。
三好 0段階での予備調査を行った後、第1段階の「基盤整備・安定化」を行います。安定化をするためにトラブルを徹底的になくしていく。そのためには言語の統一が非常に重要となります。工場で使用される言葉は、工場ごと、さらには部門ごとにバラバラなことが多いです。同じ機器を指していても、呼び方がまったく異なります。よってここでは図面に記載する機器ナンバー(タグナンバー)をユニークにし、固有の呼び方ではなくのタグナンバーで呼ぶことに統一します。この段階で3S活動を推進するとともに、一定レベルにプラントが安定化するまでトラブル低減をおこないます。
そして、第2段階では「標準化」を行います。熟練者の頭の中にあるノウハウを顕在化し誰もが実行できるようにする段階です。顕在化はヒアリングをベースにして手法化しており、総合オペラビリティスタディと呼んでいます。ノウハウを正確にかつ効率的に引き出すにはスキルが必要となりますので、トレーニングを積んで社内で認定を取得した人のみが実施できるようにしています。化学プラントは設計に余裕を持たせていたり、リサイクルなど工程が相互に複雑に繋がり影響し合ったりしています。そのためオペレーターの裁量で品質の作りこみ度合いが変わることもあり、現場ではさまざまな工程を意識しながらプラントをコントロールするための膨大なノウハウが溜まっています。大切なノウハウは意識していない当たり前なことが多く、そこを引き出して形式知化することが重要になってきます。この総合オペラビリティススタディはシステム化する際の設計資料としても活用していきます。
これらの取り組みは現在でも当たり前に行われています。このシステムは2000年にできて、私が入社したのが2007年です。完成度の高いシステムが完成し、その仕組みができあがった後に入社した我々にとっては仕組みやルールを正確にこなすことが成果になっていました。私も生産革新で構築したシステムの維持メンテナンスの担当をしていましたが、本来目指していた目的は何だったのか?時間とともに手段が目的化しているのではと問題意識をもっておりました。
最新のテクノロジーを活用し、今の時代においてもっと最適化したいと考えても、完成度の高い仕組みであればあるほど、その設計を崩すことができないんです。私も優れた完璧な仕組みだと思っていますが、それ故に完成された瞬間から手段の目的化という形骸化が始まっているんだと考えました。
田口 イノベーションのジレンマそのものですね。
三好 完成されたシステムとなると維持することにパワーを割くようになり、本来やるべきことにパワーが割けなくなる。標準化したが故に、本当の目的に対する思考力が弱まるのではと危惧していました。
そのような状況の中、2017年に社長の小河による指示で、社内でプロジェクトを立ち上げました。突然呼ばれて、なんでもいいから君の好きなことをやれ、と。まずは小河さんの知人である東京大学の松尾豊先生(人工知能や深層学習などAI研究における第一人者)に会ってこいと言われました。
田口 大変ですね(笑)。
三好 3年の期間は何のアウトプットも求めない。好きなことだけやれと(笑)。実際そのとき、自分たちを軽んじているように感じ、それが悔しく、絶対にアウトプットを出す前提で話を進めていこうと腹をくくっていました。最低1か月に1度は社長に直接進捗報告とアドバイスをもらいにいきました。そして社内で同世代のメンバーを集め、1年かけてコンセプトを考え、2年目にロジック設計、3年目に実証テストまで検討をもっていきました。そこで生まれたのが「自律型生産システム」です。
これまでの生産革新の取り組みで安全、安定生産は達成してきていましたが、品質を良くするとコストアップになるなど、品質とコストの判断はトレードオフになることが多く、その最適解の計算は演算負荷が高く現場の人の判断に依存させてきた背景がありました。
そこでピンときたのが形式化したノウハウを活用し、AIで計算しようと。我々は2000年からデジタル化しているので、20年分のデータがあることも大きな強みとなりますから。
社長からは3年間はアウトプットを出すな、と言われていましたが「3年後に実装する」と宣言をしていました。早速、工場で実装テストをしました。実装テストの結果、面白いことがわかってきました。何かというと、研究により精度は96%に達していましたが、予測が外れ現場から文句が出ました(笑)。
田口 現場からの反発は、あるあるですよね。
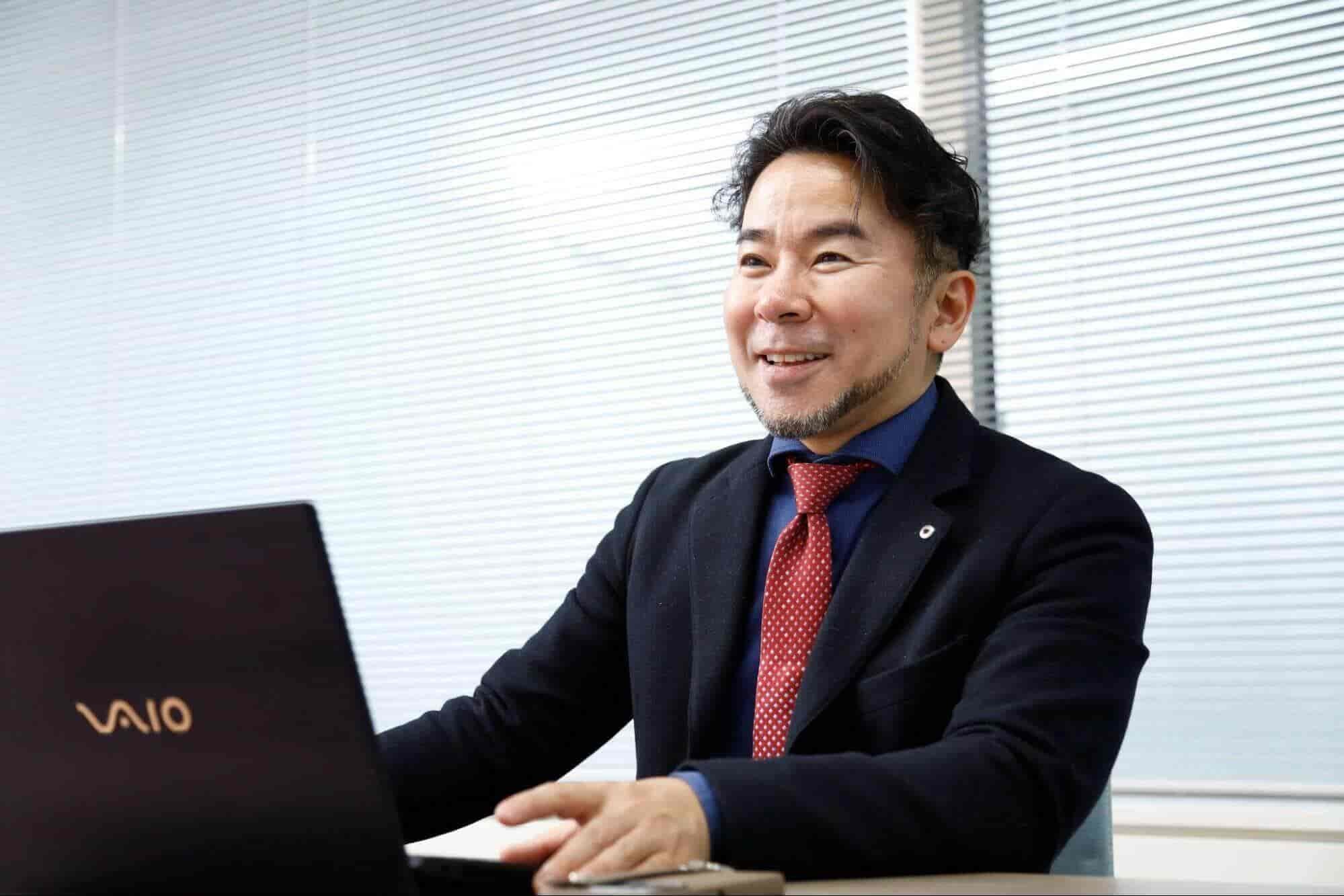
AIで進化した「自律型生産システム」は人とシステムの成長が軸
三好 我々が作ったシステムは、現場のベテランオペレーターから抽出した840万ものノウハウのロジックをツリー状に可視化し、AIで予測しているんですよね。成果が出ない、と言われると、むしろあなたたちの考えていることが間違っていたんじゃないですか、ってことになってしまう(笑)。
さらにデータと照合していくと、これまでは限界と思い込んでいたけどさらに最適化できる部分が見えてきました。このAIシステムは、もともとAIについて素人の私たちが勉強して、すべて自前でつくって運用していて、今は全工場にそのメンバーを配置しているんですよ。
ですので、この現場からのフィードバックがあればすぐにバージョンアップできます。だから、常に進化していきますし、意見が反映されて改善に直結するので改善提案をした人は嬉しいですよね。ノウハウの修正の過程では、現場の若手がこうした方がもっと精度上がるんじゃないですか、とベテランに意見が言えるようになってきた。このサイクルがあるので若手が活性化しています。
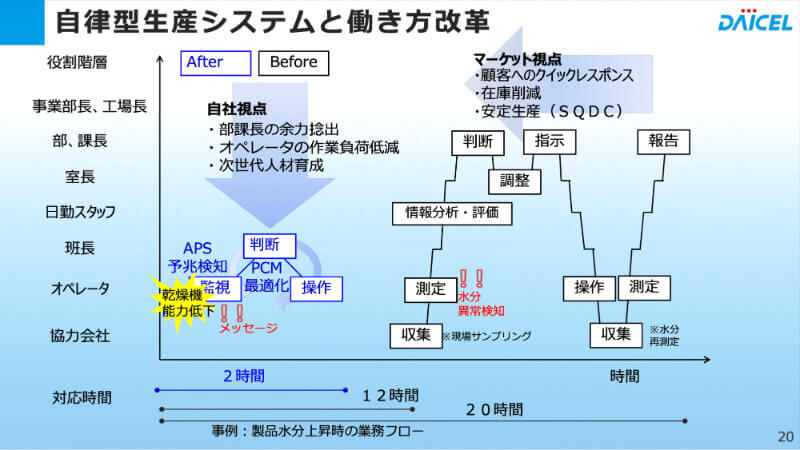
黒色が仕組みを入れる前のワークフローです。縦軸の階層は上の方が上位階層ですね。品質分析や巡回点検など自動化が進んでも人がやる作業は残っています。
例えば、ある製品には水分の品質規格があります。現場で測定するサンプルを採取して、実験室で分析にかけます。水分値が規格を上回っていることがわかると原因を追究していく。すると日勤のスタッフや技術者が検討に入り、それだけで時間を要します。この事例では乾燥機に原因があると生産そのものを止めないといけないリスクも発生し、部課長の承認や生産計画、営業など他の部門との話し合いが必要になっていきます。
「自律型生産システム」では、例えば、水分上昇を連続的に監視しており、それが発生したタイミングで、その原因が乾燥機の能力低下だと教えてくれます。化学プラントの場合は設備をすぐに止めて修理することが困難な場合が多く、リカバリーするために設定温度を上げるなど判断が必要になるため、設定温度を何度にしたらよいかのレコメンド支援をします。これにより青色の働き方に変わります。これは人が作業を機械に置き換えたのではなく、従来にない早期のタイミングで検知することで、事後から予防業務にシフトしていることになります。
我々が作るシステムはただのITツールではなく、人と機械が連関し合う繋がりを作り、人が機会を成長させ、その機会を使う人がさらに成長する仕組みを設計しています。「自律型生産システム」という名称は、 人もシステムも自律的に成長していくシステム、という意味を込めています。
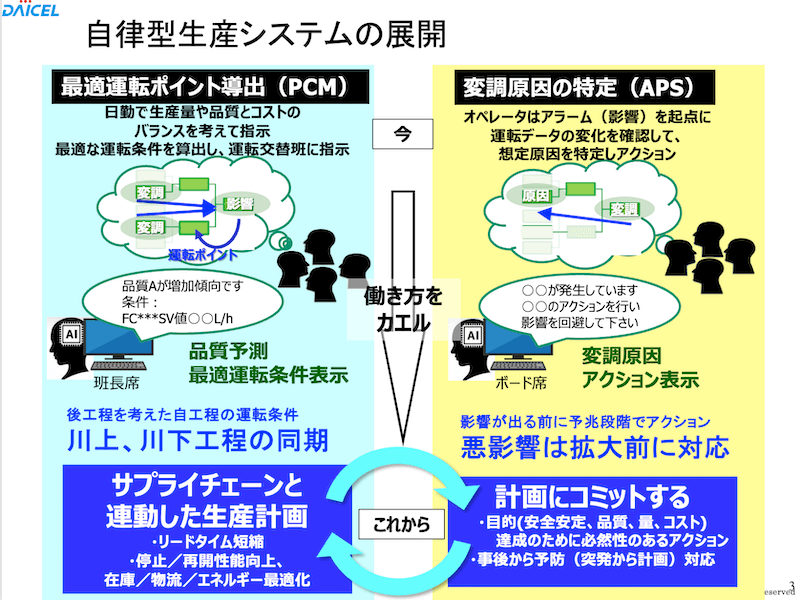
田口 結局、DXは人間。何かきっかけ、仕掛けがないと進まないはずなんですよ。業務をガラッと変えるわけですからリスクにもなります。組織がそれを認めているかどうかは非常に重要なポイントですね。ダイセルさんがなぜこのような改革を推進できたのか、ようやくその秘密がわかった気がします。
三好 この手の話では、ITシステムがなにかしてくれるという幻想を抱いている風潮がありますが、本質的にはそうじゃない。ツールはツールでしかないので、結局使う側の問題です。利用する側の考え方・思想・リテラシーがベースになるのですが、これがなかなか伝わらない。ツールが先行する風潮があるので、そこは私なりの課題かと捉えています。
私と一緒にプロジェクトを推進した30名は、私の思想を理解して、現場でリーダーシップを発揮するメンバーになります。現場ではさらにメンバーに落としていき、全員ができるようにしていく必要があります。ただ注意が必要なのは、その過程で思想はどこかに置いてけぼりになり、システムを作ることが目的化しないこと。
目指したいのは、これを使って、こんな風にもあんな風に使えるって無限に想像できるし、新しい改善のポテンシャルを無限に見出していくことですね。それを現場で考えて実行する面白さがあるじゃないですか。当初考えた使い方やメリットはありますが、そこからはみ出して現場のメンバーが自律的に改善できるような仕組みは非常に重視していますね。
田口 現場の若手からしたら、はみ出ることのリスクをきっと感じているんですよね、はみ出てもいいよってやっぱり教えてあげることは大切ですね。
三好 本当に大事なんです。人は易きに流れる、じゃないですけど考えることをやめようとします。だから、このシステムを通じてそういうことを考えたり、議論のネタにしたりしてほしい。やはり“目的”は学ぶ必要があります。そして、“手段”は勇気を持って変えていくことも重要です。
――では、最後に今後の展望について教えてください。
三好 私が嫌いな言葉は、「前はこうだったから」です。前例を理由に変えない、やらないのは非常に良くない。自動化を進めたいとは、まったく思っていなくて、人もシステムも生き物のように成長していく形骸化しないサイクルを作りたい。
デジタル化・DXはすべての必須条件であり、当たり前のことだと思っています。 この分野に特化、もしくは関わっている皆さんは、刀を持った侍のようなものです。この刀をどう使うかって、自分たち次第だと思うんですよね。
この領域を本当に面白いと感じ、一生懸命向き合っている人には、業種問わず、一緒にやっていきたいので連絡ください(笑)。本当に本当です。
【関連リンク】
株式会社ダイセル https://www.daicel.com/
株式会社コアコンセプト・テクノロジー https://www.cct-inc.co.jp/
(提供:Koto Online)