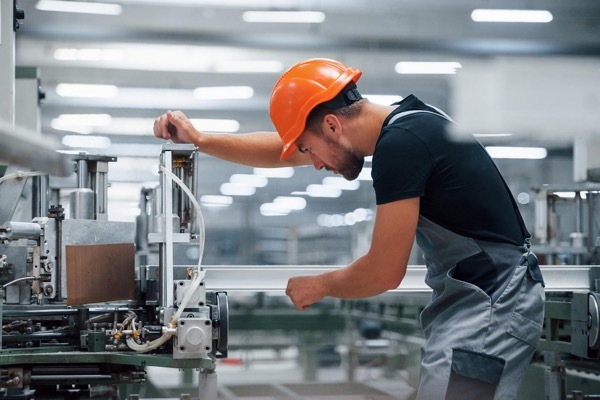
多様な製品を少量ずつ生産する多品種小ロット生産は、顧客のニーズや市場の変化に迅速に対応できるという大きなメリットがあります。しかし同時に、生産効率の低下やコスト増加といった課題も抱えています。
そこで活用したいのが「グループテクノロジー(GT)」です。グループテクノロジーは、共通部品の活用などを通じて、多品種小ロット生産における効率化を実現します。本記事では、グループテクノロジーの具体的な手法や導入によって得られる効果について詳しく解説します。
グループテクノロジー(GT)とは?
はじめに、グループテクノロジーの概要について解説します。
グループテクノロジーの定義
グループテクノロジー(Group Technology)とは、多品種少量(小ロット)生産の効率を向上、最適化するための生産方法です。
製品に関連するもの(原料となる資材・部品などのほか、設計情報、工具なども含む)を、形状や加工方法、管理方法など類似する特徴を持つグループに分類し、それぞれのグループに最適な生産設備や工程を配置することで生産効率を向上させる手法です。これらの情報を体系化・数値化することで、生産に関するコストや製造時のロスを抑制・削減することを目指します。
英語表記の頭文字から「GT」という略称が使われることもあります。日本語では、「類型加工法」「類似部品加工法」「グループ加工法」などとも訳されます。類型化されグループ分けされた材料や部品群は「グループ」と呼ばれますが、ほかに特に機械工業においてはグループ化された部品群を「部品ファミリー」と呼びます。
この場合グループやファミリーは、部品の形状、加工工程などの「類似性」に基づき、形成されます。
グループテクノロジーの歴史
グループテクノロジーの開発と発展については、第二次世界大戦後まもなくの旧ソ連がはじまりとされます(※)。1958年に旧ソ連のミトロファーノフ氏によって考案され、その後ドイツ、イギリスなど、EUを中心に欧州に広がり研究されていきます。1970年代以降には、アメリカ、そして日本に伝わって取り上げられ、さらに進展し取り上げられるようになったようです。
日本では、自動車生産の効率化の試行錯誤とともにこの考え方が組み込まれ、「より売れるものを、スピーディに」を目指し、トヨタ生産方式の二本柱の一つである「ジャストインタイム(JIT)」にも影響を与えました。ジャストインタイムは、多品種少量生産を目的として生まれた生産方式といえます。
(注※)一説では、1895年ごろから製品部品の共通化などの設計技術、マーケティングにそった製品づくりの基礎(連続同期化)が始まっていたとされます。
【関連記事】
7つのムダとは?トヨタの生産方式が指摘する「ムダ」と具体的な排除方法
グループテクノロジーの基本的な考え方と効果
グループテクノロジーは、類似した部品などをまとめて処理することで、設計や製造の効率化を図る生産方式です。
設計の段階では「形状が似ている部品は設計も似ている」という考え方のもと、新しい製品を設計する際は既存の部品を参考に、必要な部分だけ変更を加えることで、効率的に設計を進めることができます。
一方、製造の段階では同じような部品をまとめて加工することで、機械の段取り替えの回数や部品を運ぶ時間、工程間の待ち時間を減らすことができます。
グループ化のための手法
グループテクノロジーでは、部品をどのグループにまとめるか(部品ファミリーの構成をどうするか)、そしてそれぞれのグループの部品を加工する機械をどのように配置するか(機械グループの編成とレイアウトをどう関連付けるか)が非常に重要です。そのため、これらの部品ファミリーや機械グループを決定するための分類方法として、以下のようなさまざまな方法があります。
・目視調査法
専門家が部品や図面を直接見て、似ている部品をグループ分けする方法です。
・コーディングシステム
部品の寸法や形状などの特徴をコード化して、似た部品をグループ分けする方法です。(Opitzコードが代表的な例)
・分類アルゴリズム
数学的な手法を用いて、部品を自動的に分類する方法です。
・生産フロー分析
現実の生産データに基づいて、部品ファミリーと機械グループを決定する方法です。
・合成製品法
仮想的な製品を定義し、その形状を変えて、さまざまな部品を生成する方法です。
グループテクノロジーが必要とされる背景
現代の情報化社会では、あらゆる情報がリアルタイムに得られます。そのため、市場の流行や需要の動き、人々のニーズはますます多様化しており、それに合わせて製品の種類も増えてそのニーズに応えなければ製品を提供する企業は勝ち残れない時代です。
そのような理由から、製造業では少ない種類を大量に製造し市場に流すかつての大量生産制ではなく、さまざまな種類の製品を少量ずつ作る必要が出てきました(これを多品種少量生産、または多品種小ロット生産といいます)。
しかし、たくさんの種類の製品を作る場合は同じ種類の製品を大量に作る場合に比べて効率が悪くなってしまうという問題があります。この問題を解決するために生まれたのが、グループテクノロジーという考え方です。
グループテクノロジーの理念
グループテクノロジーでは、製品を作るために必要な部品や設計図などの情報を数値化して管理します。そして、似たような部品や設計図をグループ分けすることで、新しい製品を作る際にも過去のデータを活用して効率よく生産できるようになり、多様な製品を迅速に作り出すことができるようになります。
機械の切り替えにかかる時間や製品を運ぶ手間、ムダな材料やエネルギーを減らし、コストを削減し、ひいては生産性を向上させることができます。
この仕組みを効率よく動かし効果を高めるために、現在では製造業の現場のシステム化やIT化(DX)も必要になります。グループテクノロジーは、工場の情報システムを高度化することで「多品種少量生産」という難しい課題を解決するための技術なのです。高度化され情報を一元管理されたシステムの中で、グループテクノロジーはより効果を発揮できることが期待されます。
しかしシステムの高度化より、何よりも理念として意識すべきことがあります。特に製造業の工業生産品の場合、グループテクノロジーを効率よく行うためには「製品を設計する段階から」「共通して使える加工方法」を意識することが重要です。同時に、工場の機械や道具なども「複数の製品に対応できるように準備」しておく必要があります。
グループテクノロジーの各部門での活用と効果
各部門における具体的な活用方法としては、以下のとおりです。
・設計
製品設計の標準化
モジュール化による設計の効率化
CAD/CAMシステムとの連携
・製造
生産ラインのレイアウト設計
設備の選定
生産計画の策定
・管理
生産管理システムの導入
品質管理
コスト管理
グループテクノロジーに必要な基本的な準備
上で解説したグループテクノロジーの理念と必要な準備について、もう少し詳しく解説します。
(1)分類方法を決めて材料や部品をグループ化する
例えば工業の場合、グループテクノロジーに基づいた多品種少量生産を行うには、製品を構成する部品や組立品を形状や寸法、材料、加工方法などの共通点に基づいて分類しなければなりません。類似する部品や組立品を一つのグループにまとめることで、生産設備の共通化や段取り替えの削減が可能になります。
グループテクノロジーの分類の一つに「部品分類コード」を用いる方法があります。部品をグループ分けするために、それぞれの部品にコードを割り当てる方法です。このコードは、文字や数字の組み合わせで構成されて紐づけられており、部品の材質や形状、加工方法といった特徴を表すものになります。
何桁目の数字が何を表すかは、企業や製品、製造法によっても異なります。例えば、ある部品分類コードのN桁目の数字は「部品の大きさ」を、M桁目は「原材料の種類を表す」といった具合です。それ以外にもさまざまな要素が、割り当てられた数字や記号でわかるようになっています。
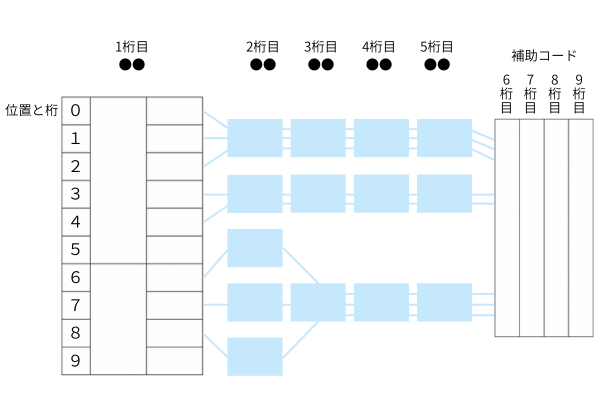
部品分類コードのほかには「加工経路分析」という方法があります。これは、部品そのものではなく加工方法に着目して抽出、「同じ加工経路のもの」同士をグルーピングしていくものです。表に加工工程と品種で当てはまる箇所に印をつけ、同じ工程ですむものをグループにしていきます。
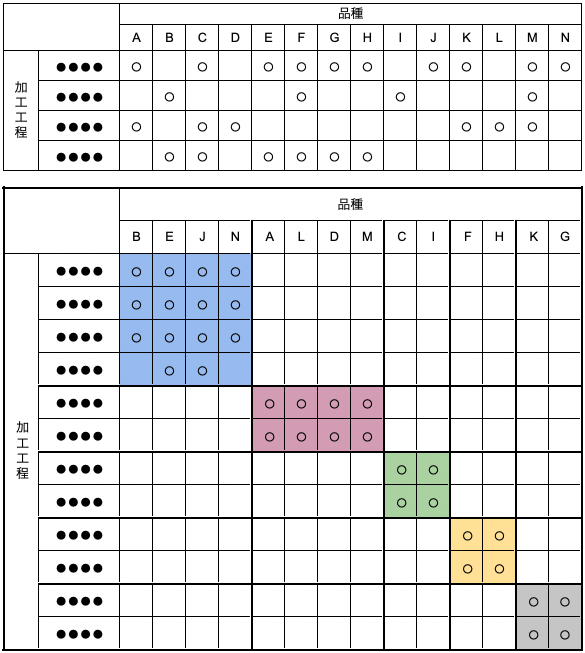
(2)セル生産システムの形成を行う
各グループに最適な設備を配置し、一つの流れ作業ライン(セル)を形成します。これがセル生産システムです。セル生産システムでは、製品の流れがシンプルになり、作業者の負担が軽減され、品質の安定化が期待できます。
セル生産方式が特に注目されるようになったのは、1980年代ごろからです。この時代から製品の種類が増え、一つ一つの製品を作る数量が少なくなる傾向が増えてきたことが背景にあります。
しかし当時の工場では、さまざまな種類の材料を扱わなければならないことと、少ない数量の製品を作ることを両立するためには、作るものが変わるたび何度も機械の設定を変えなければなりませんでした。そのため、生産の準備に多くの時間がかかってしまい、生産効率が悪化する結果になっていました。セル生産システムは、この課題を解決するための方法といえます。
(3)部品などの標準化と設計の再利用化を進める
部品や組立品の標準化を進めることで、設計の効率化を図り、新しい製品の開発期間を短縮することが可能です。また、過去の設計データを再利用することで、設計ミスを減らし、製品の品質向上に貢献します。
グループテクノロジーのメリット
グループテクノロジーの導入でどのようなメリットが得られるのか、あらためて解説します。
生産効率の向上が可能になる
同じ素材、同じ加工ルートを整理することで、安定性が高まって生産効率が向上します。
- 段取り替え時間の削減
- 設備の稼働率向上
- 作業者の移動距離の短縮
- 加工ルートの整流化
コスト削減につながる
- 設備投資の効率化
- 人件費の削減
ムダな時間、機械の非稼働時間、従業員の待機時間などを削減できるため、コスト削減が可能になります。
在庫管理の適正化がかなう
同じ素材をグルーピングすることで在庫の管理も効率化・最適化されます。ここから、以下の効果が期待できます。
- 需要予測の精度向上
- 過剰在庫の削減
- 在庫管理の適正化
製品の品質向上と顧客満足度の向上が得られる
多品種少量生産を最適化するためのグループテクノロジー導入により、以下の効果が得られ、品質と顧客満足度が向上します。
- 品質の安定化
- 納期短縮
- 顧客ニーズへの迅速な対応
グループテクノロジーを導入する際の注意点
グループテクノロジーを実際に導入する場合に注意しておきたいポイントについて解説します。
導入前の徹底的な現状分析が必要
現状の生産システムを分析し、問題点を洗い出します。そのうえで、製品を分類し、グループを形成して各グループに最適なセルレイアウトを設計しましょう。課題の見えていない状態では「どの工程に問題があってグループテクノロジーを導入したいのか」という目的も薄れ、実際に導入してからもうまくいかないおそれがあります。
設備投資やレイアウト変更を行う
セルレイアウトを構築するための設備投資が必要になる場合があります。新しい設備を導入しなくても、部品や素材、加工工程のグループ分けに伴い、工場、現場のレイアウトそのものの変更や人員配置の修正が必要です。
全員の意識改革が不可欠
従業員への教育・訓練を実施して意識改革を継続的に行います。これまでの動きや、方法に慣れていると従業員の中には抵抗を感じるケースもあるかもしれません。その場合も「なぜグループテクノロジーを導入したのか」「なぜ新しいやり方を行う必要があるのか」を伝え、一人ひとりに企業の成長のための意識づけを行う必要があります。
柔軟な対応と継続的な改善が必要
すぐに効果があらわれなくても、試行錯誤しながら改善を継続する必要があります。トヨタ生産方式は「カイゼン」を継続することでグループテクノロジーである「ジャストインタイム」に成功した例です。現在もトヨタグループでは、日々の改善を継続することで成長を続けています。
(参考)トヨタイムズ:総理が見た"混流生産ライン" 4つのクルマを流す現場の秘密とは?
まとめ
この記事では、グループテクノロジーについて解説しました。グループテクノロジーは、多品種少量生産に対応するための有効な手段です。適切に導入することで、生産効率の向上、コスト削減、品質向上など、さまざまなメリットが期待できます。ただし導入にあたっては、事前の計画と準備が重要であり、継続的な改善も必要です。
(提供:Koto Online)