
競争が激しい現代において、企業の生産性向上は重要な課題の一つになっています。そんな中、世界中の企業が注目しているのが「トヨタ生産方式」です。トヨタ生産方式とは「ムダ」を徹底的に排除し、生産効率を最大限に引き出すことを目指す生産システムのことです。
本記事では、トヨタ生産方式の核心となる考え方や導入のメリット、具体的な導入手法について詳しく解説します。
トヨタ生産方式(TPS)とは
トヨタ生産方式(TPS:Toyota Production System)は、トヨタ自動車による自動車製造においてムダな工程や在庫を極限まで削減し、顧客のニーズに迅速かつ柔軟に対応する生産システムです。「ジャスト・イン・タイム」や「自働化」といった手法を用いて、高品質な製品を低コストで生産することを目指しています。ここでは、トヨタ生産方式について概要を解説します。
トヨタ生産方式の定義
トヨタ生産方式は、高品質な製品を低コストで迅速に提供するためのトヨタ独自の効率的な生産システムです。ムダを徹底的に排除し、より効率化された生産の「よどみない流れ」を追求することで高い生産性と品質の安定化を実現しています。
具体的には「自働化」による不良品の早期発見や、「ジャスト・イン・タイム」による必要な部品の必要な数量の供給、その他のさまざまな手法を組み合わせることで高い品質と生産性を両立させています。
また「かんばん方式」など独自の考案ツールを用いていること、常に問題を見出し、継続的な改善活動を行うことも特徴です。全従業員が主体的に改善活動に参加し、PDCAサイクルを回すことで、生産性の向上と品質の安定化を実現するシステムです。
現在、トヨタ生産方式は自動車産業に限らずあらゆる業界で応用可能な汎用性の高い考え方であり、さまざまな業界や分野で導入され、活用されています。またトヨタ生産方式をベースに、さまざまなマネジメントシステムや生産方式も生み出されています。
トヨタ生産方式の始まり
トヨタ生産方式は、創業者である豊田佐吉の自動織機が持つ「ムダをなくす」という思想を継承し、豊田喜一郎が「ジャスト・イン・タイム」という概念を導入することで、生産のあらゆる工程においてムダを徹底的に排除するシステムへと進化しました。長年の試行錯誤と改善を重ねることで、今日のような形に至っています。
(参考)脱規模の経営を目指して 抄録 トヨタ生産方式,大野 耐一 著
トヨタ生産方式の各分野・各国への導入
トヨタ生産方式は自動車産業にとどまらず、製造業、サービス業など幅広い分野でその思想が応用され世界中で導入が進んでいます。
例えば自動車産業以外の製造業では、生産ラインの効率化、在庫削減、品質向上などの目的で導入されています。病院、銀行、レストランなどのサービス業でも、顧客満足度向上、業務効率化のためにトヨタ生産方式の考え方が応用されている例が多くあります。またソフトウェア開発やシステム運用など、IT業界でも開発効率の向上、品質の安定化のために、トヨタ生産方式の考え方が取り入れられている例もあります。
また欧米や中国をはじめとする東アジア・東南アジアへの影響も大きいです。欧米ではトヨタ生産方式は「リーン生産方式」の源流として知られ、多くの企業が導入しています。
アジア諸国でもトヨタ生産方式が導入され、新興国では、コスト競争力を高めるために注目されています。
【参考】トヨタ生産方式とリーン生産方式の違い
リーン生産方式は、トヨタ自動車の「トヨタ生産方式」「5S(「整理」「整頓」「清掃」「清潔」+「躾」)」「カイゼン」などについて実態研究を行い、収集したデータから体系化・モデル化された理論です。
リーン生産方式の基本的な概念は、トヨタ生産方式とほぼ同様であり、ムダをなくし(これが名称の「lean=贅肉をそぎ落とす」につながっています)、生産効率を高めるものです。欧米では、コンサルティングパッケージ化もされており、より使いやすく有名な手法となっています。
【関連記事】
リーン生産方式とは?トヨタ生産方式との違い・メリットをわかりやすく解説
トヨタ生産方式(TPS)における2本の柱
トヨタ生産方式(TPS)は「ムダのない生産」を追求し、高品質な製品を効率的に生産するためのシステムです。トヨタ生産方式を支える2本の柱が「ジャスト・イン・タイム」と「ニンベンのついた自働化」です。
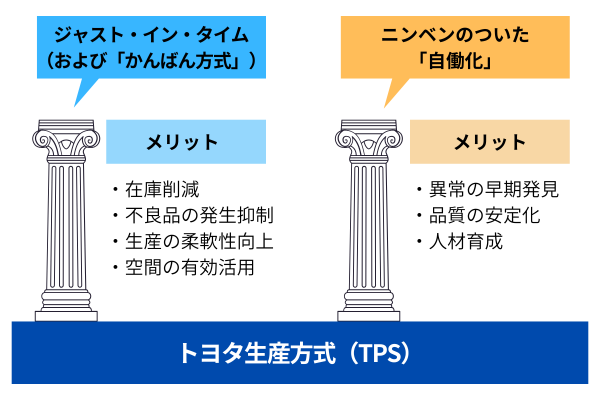
「ジャスト・イン・タイム」(および「かんばん方式」)
「ジャスト・イン・タイム」とは「必要なものを、必要な時に、必要なだけ生産する」という方式です。過剰な在庫を抱えることなく、生産と消費を一致させることで、以下のようなメリットがあります。
- 在庫削減(資金の効率的な運用が可能になる)
- 不良品の発生抑制(長期保管による品質劣化を防ぐ)
- 生産の柔軟性向上(需要の変化に迅速に対応できる)
- 空間の有効活用(倉庫などのスペースのムダを削減)
「かんばん方式」は、ジャスト・イン・タイムを実現するための具体的な方法の一つです。「かんばん」と呼ばれる「いつ・どこで・何が・どれだけ使われたか」が書いてあるカードなどを使い、前の工程から次の工程へ必要な部品や製品を必要な数量だけ引き渡す仕組みです。
かんばん方式によって、生産計画の見える化や生産の進捗状況の把握が容易になります。部品工場やサプライヤーは作りすぎの「ムダ」を削減でき、製造現場は不要な部品を置くスペースのムダを削減、余ったスペースを有効活用できます。
かつては、手書きのメモであった「かんばん」ですが、現在は電子化されたデータが活用されています。
ニンベンのついた「自働化」
もう一つの柱となる「自働化」は、単なる機械の自動化ではなく「異常が発生したら機械が直ちに停止して不良品をつくらない」という考え方です。この「ニンベンのついた自働化」には、以下の特徴があります。
- 異常の早期発見(機械の異常を早期に発見し、不良品の発生を防ぐことが可能になる)
- 品質の安定化(常に一定の品質の製品を生産することが可能になる)
- 人材育成(機械のトラブルシューティング能力を向上させることができる)
「ニンベンのついた自働化」と「ジャスト・イン・タイム」は、相互に補完し合う関係にあります。自働化によって品質が安定し、ジャスト・イン・タイムによる効率的な生産が可能になるというわけです。
トヨタ生産方式(TPS)を支える仕組みや考え方の用語
ここでは、トヨタ生産方式を理解するうえで重要なTPSを支えている仕組みや考え方を紹介します。ここにあるそれぞれのフレームワークがトヨタ生産方式を実現するために不可欠な要素といえます。
(1)7つのムダ
トヨタ生産方式における「7つのムダ」は、製造現場で発生する「付加価値を生み出さないあらゆる無駄」を「加工のムダ」「在庫のムダ」「作りすぎのムダ」「手持ちのムダ」「運搬の無駄」「不良・手直しの無駄」という7つの視点からカテゴリ分けしたものです。
トヨタ生産方式を掲げるトヨタグループでは従業員に対し「か・ざ・つ・て・と・う・ふ(飾って豆腐)」と、7つのムダの頭文字を並べて覚えやすくしています。これらのムダを徹底的に排除することで、生産コストの削減、納期の短縮、品質の向上を実現できます。
【関連記事】
7つのムダとは?トヨタの生産方式が指摘する「ムダ」と具体的な排除方法
(2)3M(ムリ・ムダ・ムラ)
3Mとは「ムリ」「ムダ」「ムラ」の3要素の頭文字をまとめたものです。それぞれ生産現場において業務効率を下げる要因となるものを指します。
「ムリ」
能力を超えたムリな仕事を強いられることです。例えば、短い納期で膨大な量の仕事をこなさなければならない状況などが挙げられます。多様な働き方やルーチンワークは、従業員に「ムリ」な負荷をかけ、業務効率を低下させる要因となりかねません。トヨタ式「カイゼン」は、こうした「ムリ」を解消し、働きやすい環境を実現します。
「ムダ」
3Mでの「ムダ」は、価値を生み出さないムダな作業を主に指しています。例えば、同じ作業を何度も繰り返したり、探し物をするために時間を費やしたりすることが挙げられます。業務における「ムダ」は、生産性を低下させる大きな要因です。トヨタ式カイゼンでは、ムダを徹底的に排除し、企業全体の効率化を図っています。
ムダを排除することで生産性が向上するだけでなく、コスト削減や納期短縮、品質向上など、多岐にわたる効果が期待できます。
「ムラ」
仕事の進め方が人によってバラバラであったり、製造された製品の品質がバラバラで安定していなかったりする状態を指します。仕事の「ムラ」は、品質の低下や顧客満足度の低下につながりかねません。また「ムリ・ムダ・ムラ」を放置しておくと、仕事効率の低下、従業員のモチベーション低下、ひいては企業全体の競争力低下につながります。
そこで重要となるのが「カイゼン活動」です(後述)。トヨタ式カイゼンは、標準化を進め、ムラのない安定した品質を目指し、実現するものです。
(3)カイゼン
トヨタ生産方式が掲げる「カイゼン」は、単なる問題解決ではなく、継続的な改善を意味するものです。一般的にいうところの「改善」は「一度問題を解決すればそれで終わり」というニュアンスがあります。しかし「カイゼン」には「現状に満足せず常により良くしていく」との積極的な姿勢を表しています。
またトヨタでは「カイゼン」を通じて従業員一人ひとりが主体的に、日々の業務の中で改善を積み重ねることを重視しています。「カイゼン」は、トヨタ生産方式を通じて世界に広まり、今や製造業にとどまらず、さまざまな業種で導入され取り組まれています。
【関連記事】
鈴木万治氏が語る次世代自動車における価値づくりのあり方 カイゼンとDXの違いに見る、真に目指すべきDXとは?
(4)なぜなぜ分析
なぜなぜ分析は、問題の表面的な原因だけでなく、その背景にある根本的な原因を「なぜ?」を5回繰り返すことで明らかにする手法です。
例えば、製品の不良品が発生した場合、「なぜ不良品ができたのか?→工程でミスが起きたからだ」「なぜその工程でミスが起こったのか?→機械の不調を放置していたからだ」「なぜ機械の不調を放置していたのか?→保守点検の報告が漏れていたからだ」「なぜ……」と、原因を深掘りしていくことで、人材不足や設備の老朽化といった根本的な原因(=真因)を特定することができます。
この手法を用いて問題の根本原因を特定し対策を講じることで、再発防止につながり組織全体の品質向上に貢献するとしています。
(5)5S活動
5Sとは「整理・整頓」に「清掃・清潔・躾」を加えた5つの活動を指します。5S活動により、以下のような現場の状態が保たれるとしたものです。トヨタ式のカイゼン活動の第一歩は、5Sの実践から始まります。なぜなら整理整頓された職場は、生産性の向上だけでなく安全な作業環境の確保にもつながるからです。
例えば、整理整頓されていない職場で何らかのものを探している従業員がいた場合、それをトヨタ式では「ただのムダ」と考えます。探す間、探す人は本来の業務ができません。巡り巡ってその積み重ねが生産性や効率性を低下させてしまいます。このようなムダをなくすため、整理整頓などの5Sを積極的に進めようとするものです。
5Sを意識して職場の環境を改善することで作業効率が上がるだけでなく、従業員のモチベーションや職場の安全性も高まります。結果、生産効率自体が上がる効果が期待できます。5Sについては、厚生労働省もリーフレットなどで啓発しています。
①作業のムダがなくなり、効率がよくなる
(出典)厚生労働省:生産性&効率アップ必勝マニュアル>「参考 5Sについて」
・必要な道具がすぐに取り出せ、探す手間がなくなる。
・要らないものが片付いて、移動や運搬がスムーズになる。
②店舗環境がよくなり、品質向上・CS向上につながる
・ゴミやチリが減り、商品への混入が減る。
・きれいな店舗は顧客満足度が高まる。
③機械の故障が減り、稼動率が上がる
④職場が安全になる
・設備を清潔に保つことで、故障を引き起こす原因が減る。
・きれいに整備された設備は、トラブルの元となる原因を発見しやすくなる。
・材料、道具の置き場を決め、従業員が安全に通れる通路を確保する。
・ケガの要因を除去する。
⑤職場のやる気と意識を引き出す
・きれいな職場で働くと、仕事へのやる気が高まる。
【関連記事】
業務効率化への一歩を踏み出すアイデア「5S」を解説
トヨタ生産方式(TPS)のメリットと課題
トヨタ生産方式(TPS)は、自動車産業を中心に世界中で導入され、その効果を実証してきた生産システムです。しかし導入にあたっては、メリットだけでなく課題も理解しておく必要があります。
メリット
(1)生産性の向上
ムダの排除を徹底することで生産効率が大幅に向上します。
(2)品質の向上
「自働化」によって不良品を未然に防ぐことが可能になり、高い品質の製品を安定的に供給できます。
(3)コストの削減
過剰な在庫を削減し、生産に必要な資源を最小限にすることでコストを削減できます。
(4)納期の短縮
ジャスト・イン・タイムによる生産は、顧客の要求に迅速に対応できリードタイムの短縮や早期の納品が可能になります。
(5)従業員のモチベーション向上
「カイゼン」が浸透することで業務や現場の改善活動への参加を促し、従業員の主体性を高めます。
(6)柔軟性の向上
需要の変化に迅速に対応できる生産体制を構築できます。
トヨタ生産方式導入の課題
(1)企業文化や既存システム、国民性に合わないケースがある
トヨタ生産方式は、それぞれの企業文化や既存のシステムと合わなかったり、大きく異なったりしている場合、整合性を図るのに時間がかかる可能性があります。また日本で生まれたトヨタ生産方式は、日本人であれば理解できることであっても海外で導入しようとするとうまくいかないケースもあるため、注意が必要です。国民性や習慣の違いもあります。
そのほか大企業と比較して中小企業は、資源や人材が限られているため、十分な改善ができず導入が成功しない場合もあるでしょう。
(2)短期的な視点での評価には向いていない
トヨタ生産方式は、根本的な改善を行い生産工程の全体を効率化するものです。またこれには、従業員への周知や教育なども含まれます。そのため短期的な利益を求める場合は、長期的な視点での改善ができず効果が期待できない場合があります。
(3)サプライチェーンとの連携が必須
トヨタ生産方式の「流れをつくる」方法には、サプライヤーとの連携が不可欠です。そのためサプライチェーン全体の最適化が求められます。トヨタ生産方式を導入し成功させるためには、経営層の理解と従業員のモチベーション維持のための環境づくり、PDCAサイクルの徹底と改善の継続が必要です。
また、これらの変化を柔軟に受け入れ、環境の変化に対応できるような企業風土を育成することも求められています。
まとめ
本記事では、トヨタ生産方式(TPS)について解説しました。トヨタ生産方式は、自動車産業を中心に世界中で導入されてきた生産システムです。ムダを徹底的に排除し、高品質な製品を効率的に生産するための仕組みは「ジャスト・イン・タイム」と「自働化」という2つの柱によって支えられています。
トヨタ生産方式の導入により、多くのメリットが期待できます。企業の規模や業種を問わず、導入することでさまざまなメリットが期待できますが、成功させるためには自社の状況に合わせて適切なカスタマイズを行い、長期的な視点で取り組むことが重要です。
(参考資料)
■公式サイト
トヨタ自動車工業:トヨタ生産方式
よくわかる「トヨタ生産方式」
トヨタ自動車75年史:1.トヨタ生産方式とは
■国によるリーフレット・啓発資料
厚生労働省:
生産性&効率アップ必勝マニュアル>「参考 5Sについて」
5S活動に取り組みましょう
■論文
「中国企業におけるトヨタ生産方式導入事例研究――ジャスト・イン・タイムとカイゼンを中心に―」羅樹凌,名城論叢(2008年9月)
富士通:「サービスプロセスへのトヨタ生産方式の適用」
(提供:Koto Online)