(本記事は、桑原晃弥氏の著書『トヨタ式5W1H思考 カイゼン、イノベーションを生む究極の課題解決法』KADOKAWA、2018年9月21日刊の中から一部を抜粋・編集しています)
なぜ「知っていてもできない」のか?
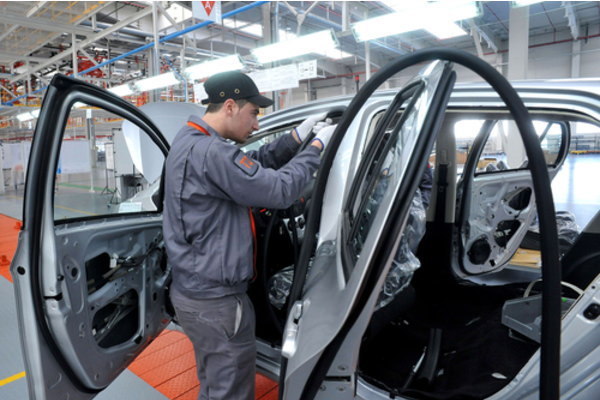
組織における上司と部下の関係は簡単ではありません。
上司には一定の権限や権力があり、部下に指示することはできますが、では部下全員がその通りに動いてくれるかというと必ずしもそうではありません。
かつてサッカーの日本代表チームを率いた外国人監督が「日本人の『わかった』を信用してはいけない」という趣旨の話をしていました。
日本人選手は外国人監督から戦術などを指示されて、「わかったか?」と聞けば、納得していなくてもその場を収めるために「わかった」と答える癖があるので、「わかった」という言葉でなく、選手1人ひとりの動きを見ることで「わかっているかどうか」を見極める必要があるというのが、その外国人監督が経験から得た日本人観です。
サッカー選手に限らず、上の人間のいっていることが理解できないのなら、「理解できません」と、納得がいかないのなら「納得できません」といってくれればいいのですが、波風を立たせないためなのかとりあえず口にする「わかりました」という返事ほど上司にとって厄介なものはありません。
トヨタ式に「『わかった』ということは実行することである」という言い方がありますが、現実には「わかった」がそのまま「実行する」につながるかというととても難しいものです。
そしてそれは日本人だけの課題ではないようです。
大手食品メーカーの海外担当役員を務めるAさんは元はトヨタグループでトヨタ式の普及定着に大きな役割を果たした人ですが、同社を退社後、食品メーカーに移り、日本国内の工場に同じくトヨタ式を普及定着させることに成功しました。
国内に目途がついたことで、次に取り組んだのが海外工場にトヨタ式を普及定着させることでした。
Aさんはトヨタグループの企業に勤務していた時も海外工場での経験が豊富であり、同じやり方をすれば食品メーカーの海外工場でもトヨタ式の実践は可能だろうと自信を持っていました。
トヨタグループ時代と同様、ほぼ毎月海外工場に出張して、「改善研究会」という名の改善活動を指導しました。
研究会には毎回、職種や役職関係なしにたくさんの社員が参加して熱心に勉強しました。活発に質問もします。
そして研究会の最後に感想を聞くと、「トヨタ式のことがとてもよくわかった」「勉強になった」という好意的な感想ばかりが返ってきました。
その様子を見てAさんは「これは日本人より熱心だなあ、これなら大丈夫だ」と自信を深めましたが、半年、1年と経つうちに奇妙なことに気づきました。
改善研究会には相変わらずみんな熱心に参加するのですが、Aさんが工場を見に行くと以前と同じつくり方、同じやり方をしており、改善の成果がまったく出ていませんでした。
「なぜ改善研究会では『わかった』『参考になった』という人がたくさんいるのに、現場の改善はまったく進まないのだろう?」という疑問を持ったAさんがいろんな人に話を聞くと、「組織風土」の違いがあることがわかりました。
トヨタ式で育ったトヨタの社員には「自己学習風土」がありますが、食品メーカーの海外工場にはそうした風土はありません。
さらに「仕事に対する意識の違い」も大きなものでした。
課長の1人がこんなことを教えてくれました。
「トヨタ式を勉強するのはとても面白いが、それを自分が実践するかどうかは別だ」
社員の多くはトヨタ式への興味と、上司の勧めもあって、改善研究会にはせっせと参加していますが、それはあくまでも「自分のための勉強」に過ぎません。
では、なぜ学んだことを現場で生かさないかというと、問題点を自ら探し出して、日々改善するのはラインを担当している自分の仕事ではなく、スタッフの仕事であるという考え方が根底にあることがわかりました。
改善を行えば不良率が下がり、コストも下がり、生産性も上がることは理解しています。
しかし、自分の仕事は所定の生産量を確保することであり、それ以上はやる必要もないし、会社も求めていない、というのが彼らの考え方でした。
これではたしかにいくら「わかった」「参考になった」といっても、「改善しよう」となるはずがありません。
そこで、Aさんはそれまでの座学中心の研修をやめ、実際に現場に出て、チームをつくり、自分たちでムダや問題を見つけて改善をするという実習を中心に行うことにしました。
「自分でやる」というのは、たとえ小さな改善であっても成果が見えるだけにとても嬉しいものです。
自分の気づきと知恵によってつくり方が変わり、「より良く、より早く、より安く」が実現できるのですからこれほどやりがいのあることはありません。
実習を通して多くの社員が「改善もいいものだな」と実感したといいます。
そして会社に対しても改善によって成果が出た場合はその成果を各人の評価に反映するように提案しました。
こうした積み重ねもあって同社の改善はようやく軌道に乗り始め、Aさんも「これで大丈夫」と確信するようになりました。
トヨタ式に「問題のホルダーになれ」といういい方があります。
どんなに良いことを学んだとしても、目の前にある問題を「自分の問題」と考えない限りは誰も改善のために行動を起こそうとはしないものです。
所詮はどんな問題も他人事です。これでは改善は進みません。
そんな時にはたとえば会社の置かれている状況やマーケット情報、原価などの情報を丁寧に説明します。
そのうえで「あなたが問題のホルダーだよ」という意識を持たせることができれば、人は率先して改善に取り組むようになるのです。
社員のモラルが低下した時や、改善活動が低調な時、「なぜ」と問いかけてみると思いがけない「真因」が潜んでいるものです。
真因を知ることは社員のやる気を引き出し、モチベーションを上げることにもつながるのです。
長時間残業の本当の理由
みなさんの周りに長時間残業が日常化している人はいないでしょうか?
「働き方改革」が叫ばれる中、「何とか残業を減らさなければ」とは思ってみても、案外できることは限られているものです。
結果、隠れ残業をしたり、家に仕事を持ち帰るという本来の改善策とは違うやり方をとる人も多いと思いますが、そんな時には「なぜこれだけの残業が必要なのか?」という理由を書き出して、その1つひとつについて「原因」と「対策」を考えてみることです。
首都圏にいくつもの保育所を持つA社で保育士さんたちの長時間残業が問題になっていました。
本社も深刻に問題を捉えており、残業を減らそうと通達を出したり、所定の時間になったら部屋の灯りを消すといった対策をとったものの、思うように残業は減らないばかりか、仕事を家に持ち帰るという、結果として労働強化につながってしまいました。
「なぜ残業が減らないのか?」と疑問に思ったA社トップはトヨタ式のコンサルタントに依頼して保育所での保育士さんたちの仕事の進め方を詳細に分析してもらうことにしました。
ポイントは「現地現物」と、「フィルターなしで白紙になってものを見る」です。
本社もこれまで改革案を考え提案してきましたが、いずれも現場での効果は薄いものばかりでした。
理由は現場に行き、現実の仕事を見て改革案を考えるのではなく、「こうすればきっとうまくいく」という机上のアイデアが多かったからです。
問題について考える時は現場に行けばいい、というのがトヨタ式の考え方です。
さらに大切なのは「白紙でものを見る」ことです。
トップが現れて「なぜ残業が減らないのか?」と聞けば、保育士さんたちの仕事のやり方は普段とは違うものになるはずです。
それでは正しく問題を把握することはできませんし、原因を知ることもできません。
大切なのは、問題の起きた現場で先入観なしに白紙でものを見ることです。
それで初めて「何が問題か」「原因は何か」という正しい「5W1H」が可能になるのです。
コンサルタントは保育士さんたちの仕事の進め方を見ていてあることに気づきました。
本来は子どもたちを見ていなければならないのに、しばしば事務室に入ってパソコン作業をしているのです。
理由を聞くと、本社への報告書や保護者への連絡事項などパソコンでつくるものがたくさんあるにもかかわらず、パソコンが2台しかなく、しかたなしにみんなが交代で事務室で作業をしているというのです。
それでもパソコン作業が時間内に終わることはなく、結局は残業したり、自宅に持ち帰って仕事をするほかないというのが保育士さんたちの悩みでした。
つまり、保育士さんたちの残業の原因は、(1)本社が要求する膨大な書類の作成(2)パソコンの台数不足であり、「残業を減らせ」と指示する本社自身が残業の原因を生み出していたことになるのです。
報告を聞いたA社のトップは驚きました。
急いで保育士さんたちがどれだけの報告書を作成しなければならないのかを調べると大変な数でした。
保護者向けの文書もたくさんありましたが、それ以上に本社がそれぞれの保育所に求める報告書の数が膨大で、しかも「何時までに」というものもたくさん含まれていました。
これでは保育士さんたちの子どもを見る時間も奪われますし、残業をしない限り仕事が終わるはずがないということがわかりました。
A社はこれまでこうした実態を知らずに保育士さんたちに一方的に「残業をもっと減らしなさい」「もっと仕事を効率よくしなさい」と指示してきたのです。
間違った原因に対して対策を打ったとしても問題が解決するはずがありません。
A社トップはすぐに次のような改善策を実行しました。
・多すぎる報告書の数を減らし、必要最小限のものだけを残す。
・保育士さんの人数などに応じてパソコンの数を増やす。
・保育所の忙しさに応じて「何時までに報告」を柔軟に対応する。
こうした改善策を実行した結果、保育士さんたちの残業時間は減り、子どもたちのための時間も増えることになりました。
トヨタ式の生産改革などを行う場合、現場で作業をしている人たちの後ろに立ってじっとその動きを見ながら、「なぜあのような動きをしているのだろう?」「あの動きにはどんな意味があるのだろう?」と問いかけていると、ムダや改善点が見えてきます。
何か問題があれば現場に行き、何かひらめいたなら現場に行けばいい。
そうすれば何が正しいかもわかるし、新しいアイデアも思いつくというのがトヨタ式の考え方です。
長時間残業を改善する答えもやはり現場にあるのです。